Aplicación de la metodología de inspección basada en el riesgo en instalaciones de proceso
Técnicos del Departamento de Seguridad Industrial de Inerco01/08/2006
El mantenimiento puede definirse como el conjunto de actividades que se realizan sobre un sistema, equipo o componente, al objeto de garantizar su correcto funcionamiento. En este sentido, las operaciones de mantenimiento deben planificarse con el objetivo de preservar la función del equipo y de optimizar el rendimiento del proceso, procurando la inversión optima de los recursos que sean necesarios.
Evolución de las técnicas de mantenimiento
En este sentido, se pueden distinguir las siguientes fases en cuanto a la evolución que ha sufrido el concepto de mantenimiento de equipos:
- En su origen, las instalaciones industriales disponían de pocos equipos, simples, fáciles de reparar y normalmente sobredimensionados. Los volúmenes de producción eran bajos, por lo que los tiempos de parada no eran importantes. Esto hacía que las técnicas de mantenimiento se centrasen casi exclusivamente al mantenimiento correctivo (reparación tras producirse el fallo del equipo).
- Posteriormente, la incorporación de equipos más complejos, y la preocupación por reducir los tiempos de parada, que repercutían en cuantiosos costes por pérdida de producción, dio paso a la necesidad de prevenir el fallo de los equipos, surgiendo de esta forma el conocido como mantenimiento preventivo.
- Finalmente, como consecuencia del avance tecnológico y de las nuevas investigaciones tiene lugar un aumento de la mecanización y de la automatización en la industria, operándose con volúmenes de producción cada vez más altos, y dándose especial importancia a los tiempos de parada debido a los importantes costes derivados de las pérdidas de producción. En esta etapa se produce la consolidación del mantenimiento preventivo y surge el llamado mantenimiento predictivo, que permite predecir el comportamiento futuro del equipo, así como los posibles mecanismos de fallo que pueden suceder.
En la actualidad, las principales preocupaciones se centran en la necesidad de aumentar la seguridad y fiabilidad de las instalaciones y reducir los costes asociados al fallo de los equipos, tanto los costes directos asociados a su reparación, como los indirectos, originados como consecuencia de la pérdida de producción durante la parada de la instalación.
Ante estas exigencias, el personal responsable del mantenimiento de las instalaciones está demandando la implantación de sistemas y técnicas que les faciliten la toma de decisiones y les permita definir, de forma objetiva, un programa eficaz de inspección y mantenimiento de las instalaciones que gestionan.
Para cubrir esta necesidad, surgen diversas metodologías. La más avanzada y novedosa, y al mismo tiempo, la más demandada en la actualidad, es la conocida como RBI (Risk Based Inspection). Esta metodología permite la evaluación y desarrollo de planes de inspección y mantenimiento de instalaciones, en base a los resultados obtenidos de un estudio exhaustivo de los riesgos asociados a cada uno de sus equipos.
Metodología RBI
Los buenos resultados obtenidos en las experiencias realizadas están haciendo que muchos sectores de la industria, en particular los sectores del refino o de la petroquímica, se estén sumando a la implantación de esta técnica.
La aplicación de la metodología RBI en instalaciones de proceso se fundamenta en el desarrollo de las siguientes etapas:
Análisis de riesgo
Consiste en evaluar el riesgo de cada uno de los equipos que forman parte de la instalación, orientando sus resultados a la gestión del mantenimiento de los mismos. Se compone a su vez de:
- Evaluación de consecuencias: mediante estimación de costes asociados a daños al medio ambiente, sobre la salud de las personas (tanto de trabajadores como de poblaciones cercanas), a equipos, socioeconómicos y pérdida de producción (lucro cesante).
- Evaluación de la probabilidad de fallo (veces/año): identificando los posibles mecanismos de fallo (corrosión, fatiga mecánica, fragilización, daños externos, etc.), determinando la probabilidad genérica de fallo y aplicando factores de corrección que tengan en cuenta las particularidades de la instalación (características del proceso, sistemas de control disponibles, sistemas de gestión implantados, factores externos, etc.).
- Evaluación del riesgo: mediante matriz de riesgos.
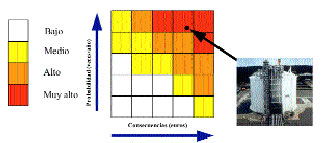
Revisión del plan de mantenimiento/inspección.
Asimismo la evaluación de la relación entre la reducción del riesgo conseguida y los costes asociados a las medidas adoptadas ayudará al gestor de mantenimiento a la selección de la opción más óptima.
- Reevaluación periódica del riesgo con nueva situación
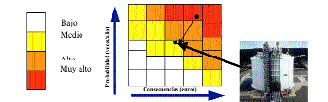
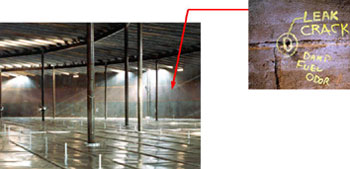
Beneficios en la aplicación de la metodología a instalaciones de proceso
Facilitar la planificación del mantenimiento:
La planificación de las actividades de mantenimiento de los equipos e instalaciones se fundamenta en la aplicación de una metodología sistemática, basada en la utilización de criterios objetivos.
Esta metodología permite identificar los componentes que más influyen en el riesgo de la instalación, sobre los cuales habrá que focalizar los esfuerzos de inspección, y definir, para cada caso, el alcance, la periodicidad y los métodos óptimos para su mantenimiento.
Aumentar la seguridad de la instalación:
La aplicación de la metodología RBI permite aumentar la seguridad de las instalaciones, garantizando un alto nivel de integridad mecánica de los equipos y una reducción de los mecanismos de fallo posibles. Esto se consigue tras la identificación de los equipos que poseen un mayor riesgo, a cuyo mantenimiento se destinan mayores esfuerzos y recursos.
Adicionalmente, la RBI permite conseguir una reducción del riesgo sobre el personal de la instalación o las contratas que realicen la inspección, si tras su aplicación se identifica la posibilidad de ampliar el periodo de inspección en aquellos lugares que pueden resultar más peligrosos o en lugares de difícil acceso.
Uno de los mayores atractivos que presenta la metodología RBI es que permite aumentar la seguridad de las instalaciones reduciendo los costes, tanto directos como indirectos, asociados al fallo de equipos, y que se pueden resumir en los siguientes:
- Costes asociados a la pérdida de producción por parada de la instalación. En este sentido, la aplicación de la metodología RBI permite adecuar el número de paradas de la instalación a las necesidades reales de inspección, y reducir el número de paradas no programadas que tienen su origen en fallos inesperados de sistemas o componentes.
- Costes de mantenimiento e inspección. La metodología RBI permite optimizar los recursos necesarios de mantenimiento e inspección, destinando los mayores esfuerzos a aquellos equipos que presentan un mayor nivel de riesgo.
- Costes derivados de accidentes. El conseguir mayores cotas de seguridad en la instalación permite reducir los costes asociados a reparar los daños que un posible accidente puede originar sobre las personas, los bienes y el medio ambiente.
- Costes de seguros. Existe gran aceptación por parte de las aseguradoras de la utilización de este tipo de técnica, lo cual puede redundar en la obtención de importantes beneficios económicos para la instalación