La feria JEC sirvió para presentar el estado actual de las tecnologías
Las tecnologías aditivas con composites llegan al mercado
Luis Palenzuela. Área de Procesos de Fabricación y Materiales. División de Industria y Movilidad – Tecnalia
16/05/2023Hace aproximadamente 10 años comenzó a pensarse en la fabricación aditiva como algo más que una serie de tecnologías para obtener prototipos. El 3D Printing podía ser un proceso o parte de un proceso para conseguir piezas funcionales y comercializables que hasta ahora se fabrican con otros materiales y procesos. Los resultados ya están llegando al mercado, también al de los composites. Este artículo resume la presencia de las tecnologías aditivas en la principal feria europea dedicada a estos materiales, la feria JEC, que tuvo lugar en París entre los días 25 y 27 de abril, permitiéndonos detectar su estado de madurez y los primeros campos de aplicación en los que van a ser claramente competitivas.
La presencia del 3D Printing en los stands de empresas manufactureras transmite lo que está siendo o va a ser una realidad en el corto plazo (1 o 2 años). Los demostradores conceptuales de las Universidades, Centros Tecnológicos y startups orientan sobre las futuras tecnologías y sus potenciales campos de aplicación. Independientemente del estado de madurez de los procesos y sus casos de uso, las empresas deben de estar muy atentas a esta nueva generación de procesos productivos claramente disruptivos respecto a los actuales. Debe de pensarse en impresión 3D no solamente como una forma de reducir costes y plazos sino también como una oportunidad para generar más valor incorporando prestaciones que son imposibles con las técnicas convencionales.
El proceso aditivo estrella de la feria ha sido la extrusión directa de pellet de composites (CEAD, CMS, Breton, Belotti o Airtech) y su campo de aplicación más destacado es la fabricación de moldes de grandes dimensiones. Con esta temática, la feria muestra propuestas y orientaciones diversas:
- Sector y proceso de moldeo al que se dirige el molde
- Uso de granza procedente de materiales reciclados
- Materiales de altas prestaciones térmicas
- Granza reforzada con fibras naturales
- Configuraciones del extrusor mejoradas
- Equipos de fabricación que integran impresión y mecanizado
- Materiales auxiliares para el acabado superficial.
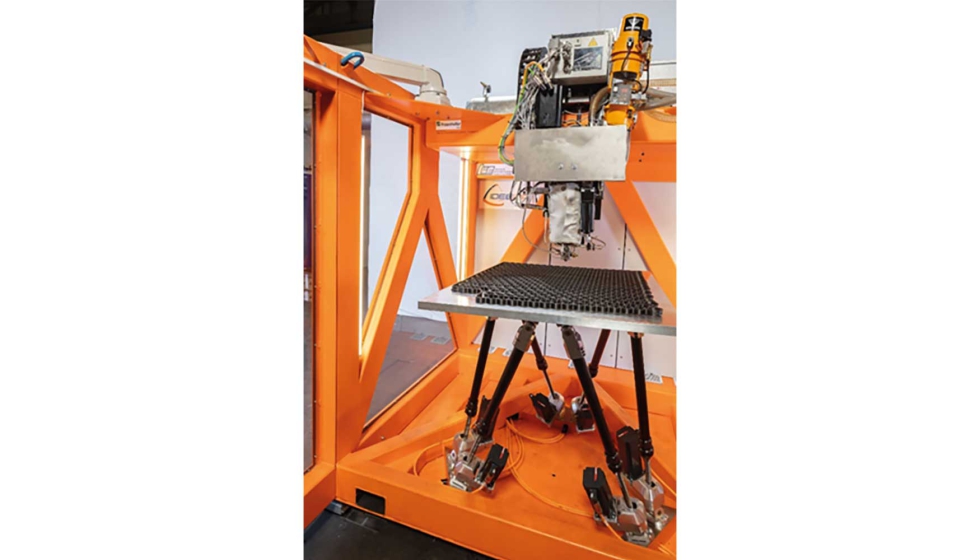
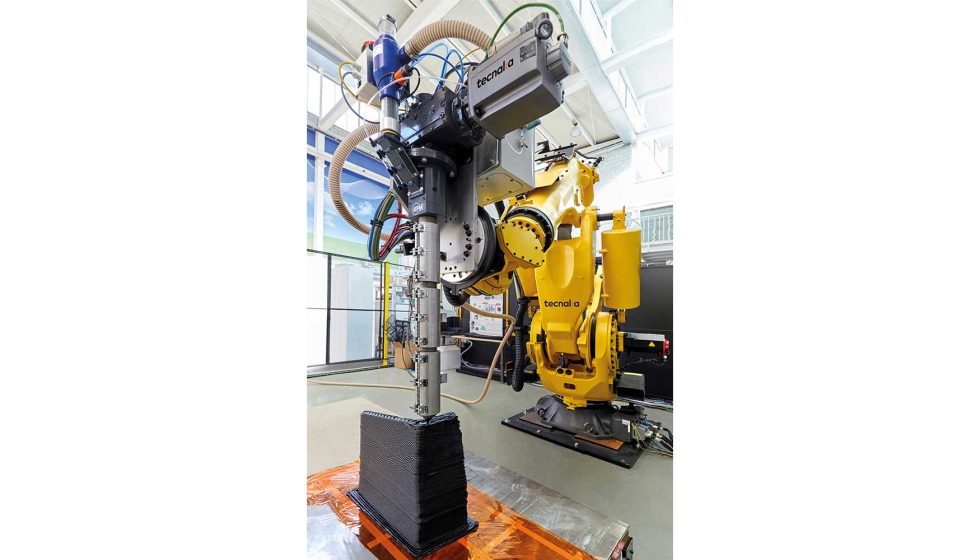
Equipo con capacidad de impresión de hasta 22 kg/h.
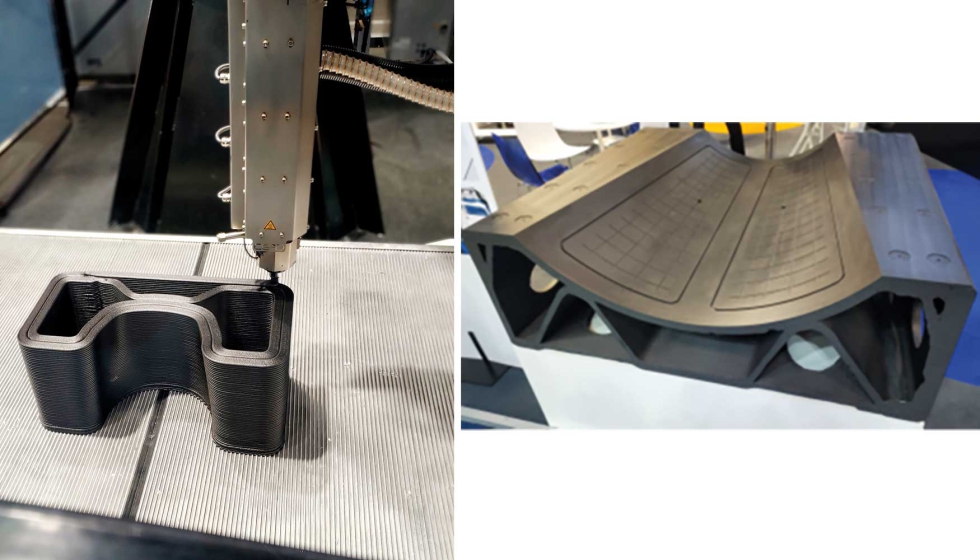
La impresión mediante extrusión directa de pellet requiere de un mecanizado final. A pesar de ello, los ahorros de coste y plazos pueden ser muy significativos. Los fabricantes de equipos indican que para moldes grandes del Sector Naval el plazo de fabricación, en los casos más favorables puede reducirse de 2 meses a 2 semanas y el coste bajar 4 veces (de 85.000 € para un molde de referencia fabricado por un proceso de mecanizado convencional a 20.000 € impreso por extrusión directa).
En casi todos los casos, los materiales utilizados están reforzados principalmente con fibras que además ayudan a reducir los alaveos y deformaciones propias de este proceso.
Sin duda, la extrusión directa requiere de una fase de aprendizaje que permita:
• Minimizar el tiempo de puesta a punto de la impresión
• Maximizar la velocidad de impresión
• Optimizar la calidad de la pieza
• Minimizar el Consumo y coste de los materiales utilizados
• Adecuar cada una de las configuraciones posibles de impresora a la geometría de la pieza.
El dominio de estos aspectos depende tanto de la experiencia de los usuarios como de los avances en el desarrollo de materiales, equipos, software y postprocesos. Las oportunidades de generar ventaja competitiva aumentan cuando las tecnologías en juego no son maduras, por ello, estamos en un buen momento para los procesos aditivos.
3D Printing reactivo
Los procesos reactivos llevan varios años desarrollándose y ya se han aplicado principalmente a siliconas y materiales espumados. En los procesos reactivos el cabezal de impresión es un mezclador dosificador al que llegan las materias primas (líquidas o pastas) impulsadas por bombas (generalmente de engranajes). Este año la empresa Polynt propone un proceso reactivo bi-componente para imprimir moldes que posteriormente requerirá un mecanizado final. Las ventajas de esta tecnología respecto a la extrusión directa de pellet pueden ser interesantes:
- Reducción de consumo eléctrico
- Resistencia a la temperatura
- Resistencia interlaminar y propiedades mecánicas en el eje Z
- Menor anisotropía
- Velocidad de impresión
- Reparabilidad más fiable.
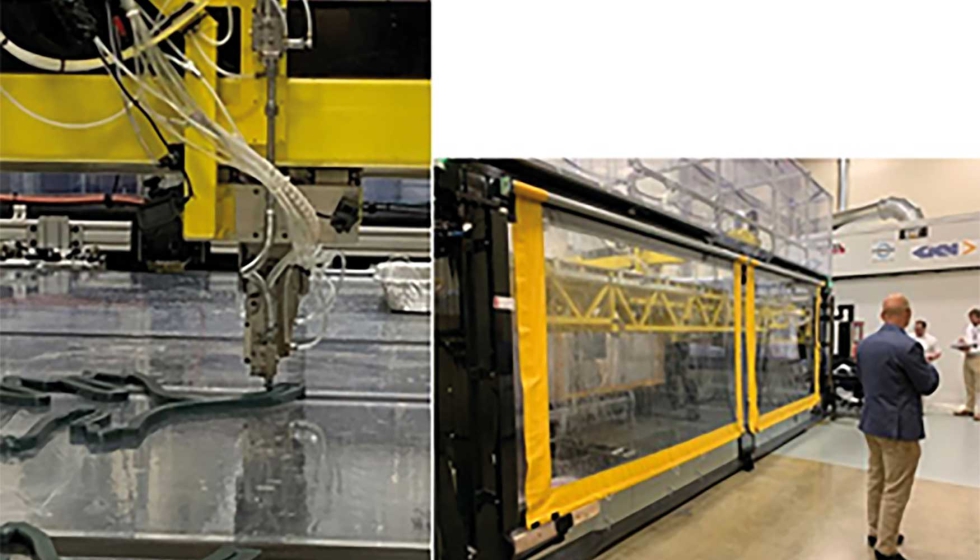
Equipo de Fabricación Aditiva Reactiva (RAM) de MVP. Material de impresión: Polynt Reactive Deposition PRD-1520. Fuente: CW.
Los sistemas mono o bicomponente reactivos pueden, como presenta Polynt, imprimir piezas de un material único. Otras posibilidades son su aplicación como post-proceso simultáneo o secuencial de tecnologías aditivas:
• FDM
• Extrusión directa de pellet
• SLS o fotocurado.
En estos casos, la resina incorporada durante o tras la impresión, complementa los requerimientos técnicos que no pueden ser cumplidos solamente con el material impreso.
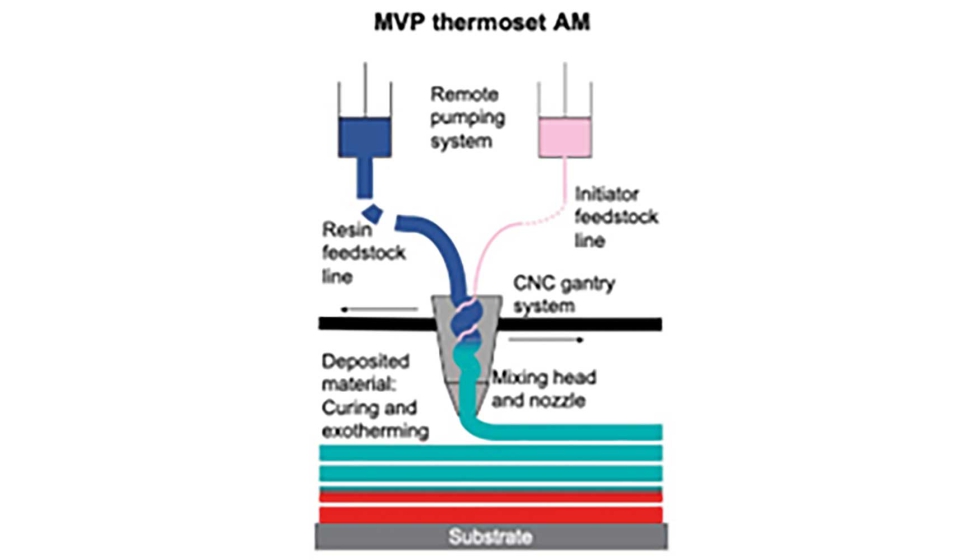
Esquema del proceso de Impresión Reactiva. Fuente: Oak Ridge National Laboratory.
Impresión de composites reforzados con fibra continua
La capacidad de dar formas complejas a fibras de refuerzo continuas (carbono, vidrio, aramida, basalto, etc.) posibilitará un gran salto en el aligeramiento de componentes con muy altas prestaciones mecánicas. Organizaciones como Orbital, 9TLabs, Fraunhofer - ICT, Tecnalia o IMT - Institut Mines Télécom presentan desarrollos en diferentes niveles de madurez orientados a la fabricación aditiva de piezas finales o intermedias como:
- Preformas complejas para su impregnación posterior mediante inyección o infusión de resinas termoestables
- Preformas termoplásticas para su consolidación mediante presión y temperatura
- Preformas para composites carbono-carbono
- Bulk (3D) preforms
- Parches de reparaciones
- Liners
- Tirantes reforzantes
- Refuerzos localizados y nervaduras para sobre-moldeo
- Isogrids.
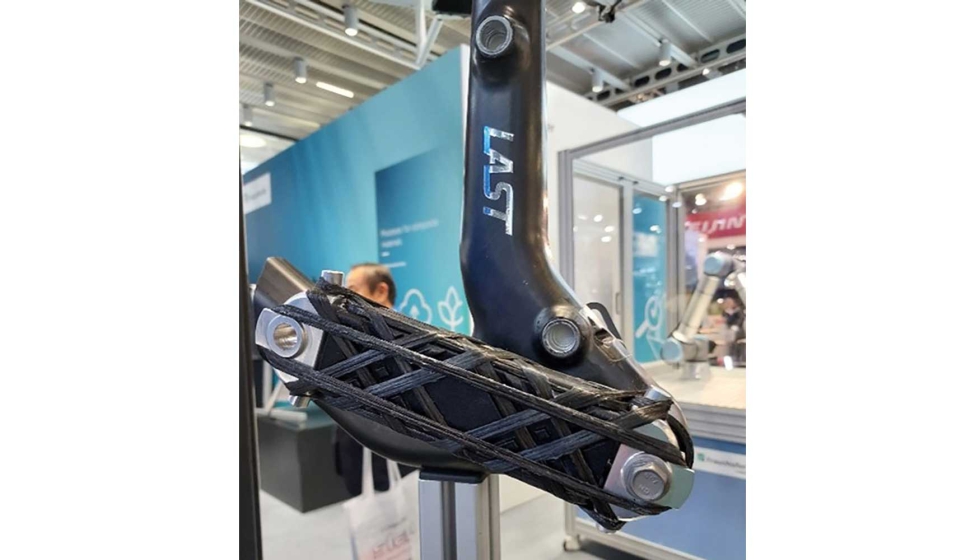
Biela de pedal de bicicleta reforzado con la tecnología de bobinado de armazón. Fraunhofer - ICT.
El proceso de preformado de tejidos de refuerzo es la fase más costosa y limitante del moldeo de composites. La contribución al coste final de este preproceso limita la extensión en el uso de los composites. Por ello, la automatización es una tendencia permanente en este sector. El preformado aditivo integra automatización y digitalización en un único proceso. Adicionalmente, alguna de las tecnologías aditivas en desarrollo, posibilita maximizar la optimización topológica y la complejidad geométricas de las piezas. Todo ello genera un gran potencial de mejora competitiva procedente tanto desde los costes y del valor aportado (nuevas y mejores prestaciones) como de los posibles nuevos modelos de negocio (personalización, fabricación in situ, etc.).
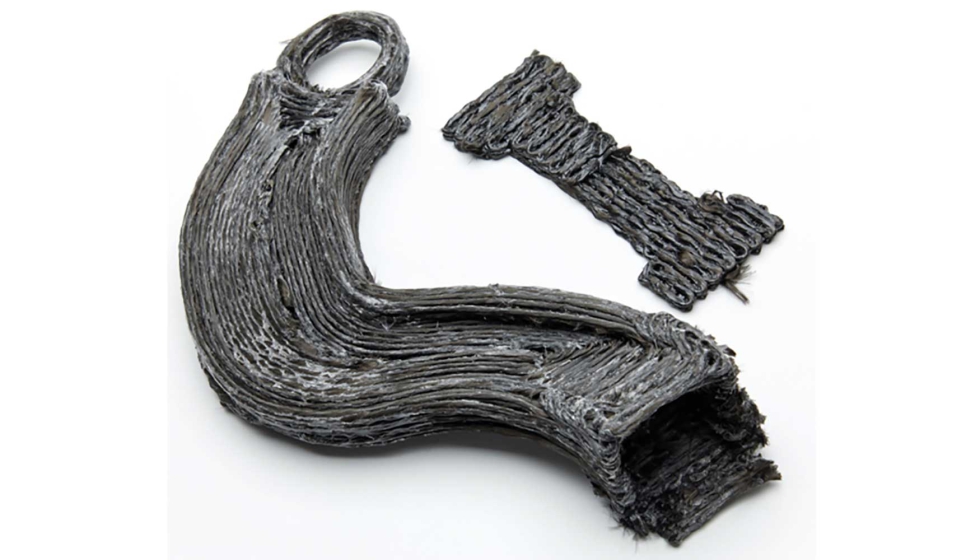
Preforma compleja impresa mediante fabricación aditiva de fibra continua. (Tecnalia).
El preformado aditivo posibilita fabricar componentes de composites termoplásticos de fibra continua sin limitaciones en la profundidad de conformado. Estos materiales no aportan solamente la ventaja de favorecer la reciclabilidad, sino la también la posibilidad aplicar sobre ellos la soldadura como tecnología de unión. Por otra parte, las preformas aditivas para su impregnación con resinas líquidas mediante infusión o RTM, permiten obtener composites finales con muy baja porosidad y prestaciones mecánicas próximas a los composites moldeados con procesos convencionales.
Probablemente, para la fabricación aditiva de piezas de composites, la impresión y sobreimpresión de fibra continua es uno de los procesos más disruptivos. Sus potenciales campos de aplicación demandan alta ligereza obtenida mediante nervaduras en la cara no vista de la pieza. Los refuerzos localizados de alta complejidad geométrica podrán sustituir a elementos metálicos sobremoldeados con termoplásticos.
Tecnologías aditivas híbridas
Se denominan tecnologías híbridas a las que combinan diversos materiales para obtener las prestaciones requeridas cuando éstas no pueden ser proporcionadas por un solo material y proceso. La empresa Massivit muestra un equipo de tamaño grande que imprime una pieza hueca que va rellenándose mediante casting con una resina bicomponente. En este caso es necesario un primer post-proceso que elimina por disolución el material de las paredes impresas. El mecanizado posterior finaliza la pieza. La pieza obtenida (también molde) será completamente isotrópica y el mecanizado de acabado muy rápido.

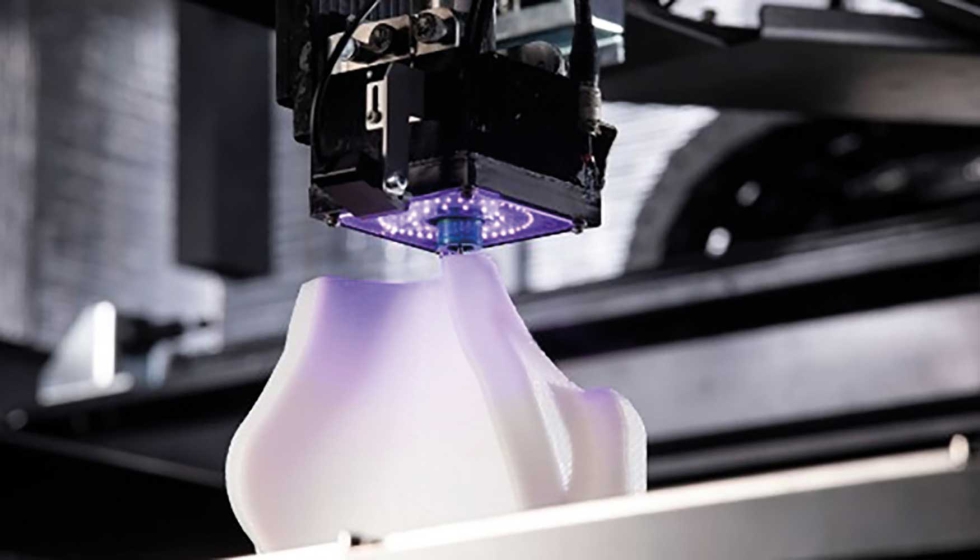
Detalle del cabezal de impresión Massivit. Fuente: Massivit.
Con otras tecnologías hibridas, se recubre, impregna, infusiona o rellena una pieza impresa con diferentes resinas para complementar los requerimientos técnicos que, por si solo, no puede cumplir el material imprimible.
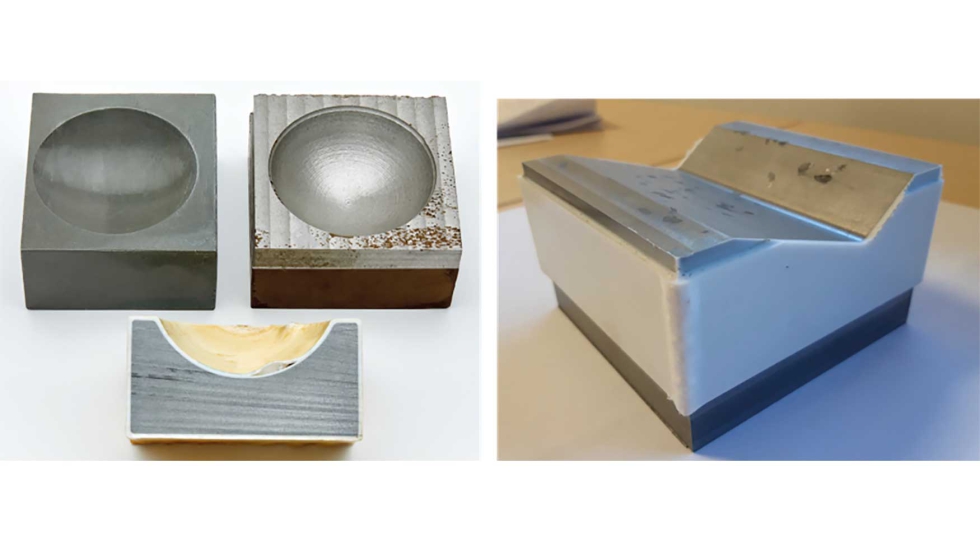
Demostradores de moldes obtenidos mediante procesos híbridos (Tecnalia).
Impresión funcional (‘pick and place’ de materiales y componentes)
Tanto Fraunhofer-IWU como Tecnalia presentan desarrollos en los que se embeben funciones eléctricas, electrónicas y mecánicas para conseguir prestaciones imposibles o muy complejas mediante otros procesos. Los equipos multicabezal permiten fabricar sistemas multifuncionales intercalando la deposición de plásticos, tintas, conductoras, hilo de cobre, resinas de encapsulado y componentes electrónicos.
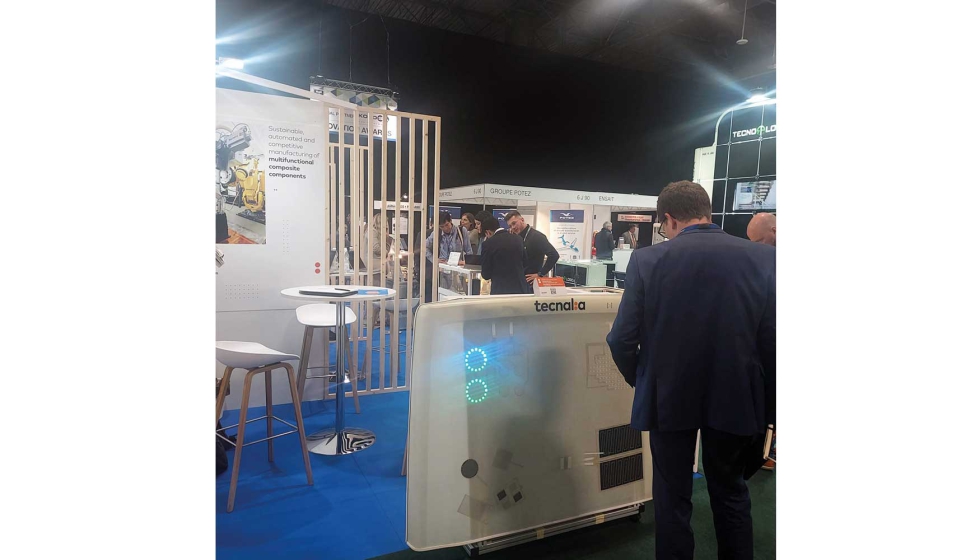
Panel de composites con funciones electrónicas embebidas.
Deposición de cable de cobre mediante FDM adaptado (Tecnalia)
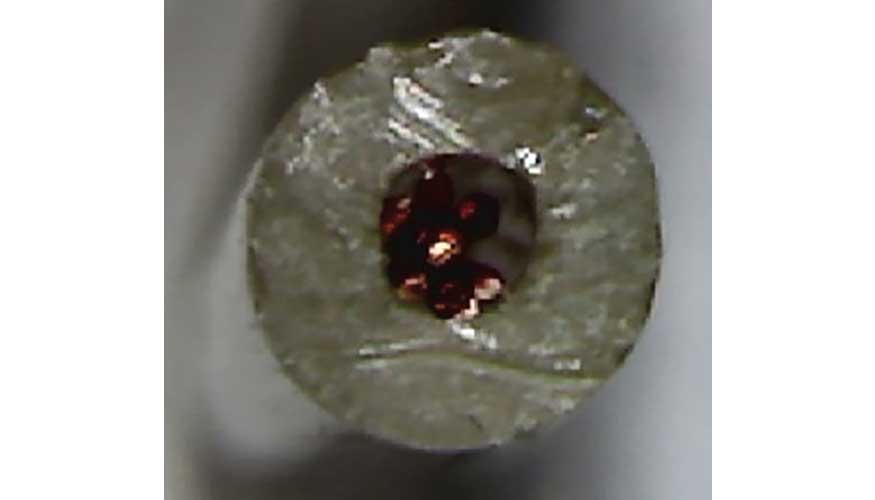
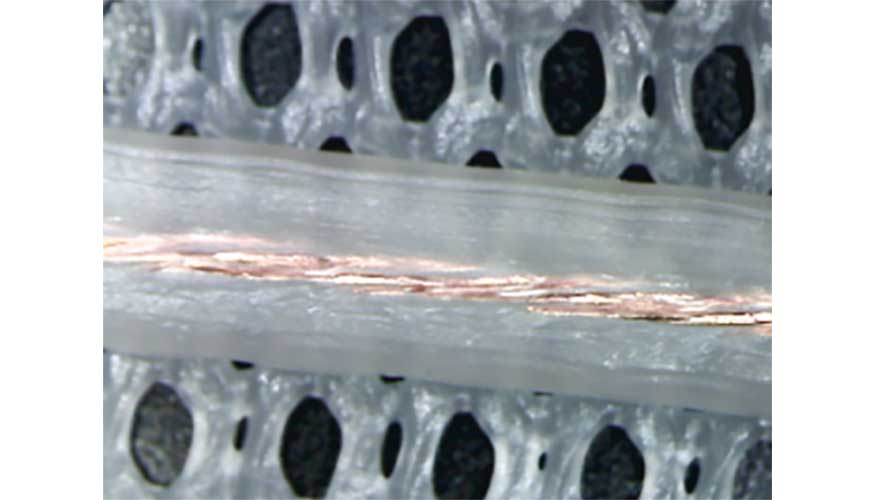
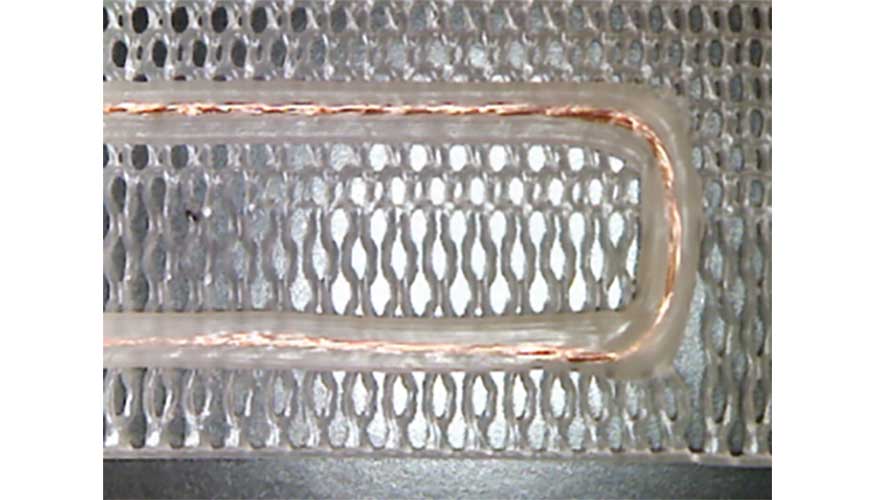
En definitiva y como conclusión, se percibe un elevado dinamismo tecnológico del 3D Printing de composites. Se buscan y se encuentran campos de aplicación que se adaptan a las ventajas y limitaciones que ofrece el estado del arte actual. Se mantienen las expectativas en los cambios disruptivos que aportarán en numerosos sectores de actividad y que promoverán un incremento del uso de los materiales compuestos. La Fabricación Aditiva se transformará no solo un proceso para fabricar piezas sino un “pick and place” de materiales y componentes que sofisticará la funcionalidad de los sistemas, pero simplificará su fabricación y el montaje.