Tratamiento innovador del blisk con un nuevo proceso shot peening
Rolls Royce Alemania ha patentado un nuevo proceso de shot peening para la inducción de tensión residual de compresión en la superficie de los blisk ensamblados utilizados en los motores aéreos. El equipo de Rolls Royce junto con el equipo de shot peening de Rösler han desarrollado un sistema de shot peening que permite la medición completamente automática y precisa de los componentes y la calibración de las boquillas de chorreado. Un software de calibración especial garantiza la total estabilidad del proceso de shot peening.
En los elementos compresores convencionales para las turbinas, el disco de turbina y los álabes son componentes separados, mientras que en el caso de los blisks, los álabes y el disco de la turbina son mecanizados desde una única pieza (álabes integrados en el disco) de titanio o aleación de níquel y acero. Además de ahorrar costes mediante la eliminación del montaje de los álabes en el disco, la utilización de los blisks también reduce considerablemente el peso. Sin embargo, el shot peening de estos componentes plantea unos nuevos retos tecnológicos. Por esta razón, Rolls Royce Alemania desarrolló un nuevo proceso de shot peening cuyas principales características son que la succión y presión lateral de cada álabe individual son simultáneamente chorreados con boquillas de forma especial. La distancia entre las boquillas de chorreado y los álabes es de sólo unos milímetros. Esta pequeña distancia y el alto número de álabes del blisk, requieren un movimiento preciso de las boquillas con una desviación máxima de 1/10 mm (alrededor 0,004 – 0,010 pulgadas).La precisión requerida hace que la calibración y medición manual sea muy difícil y lleve tiempo, especialmente para el proceso de los blisk ensamblados, componentes que a menudo consisten en múltiples blisks.
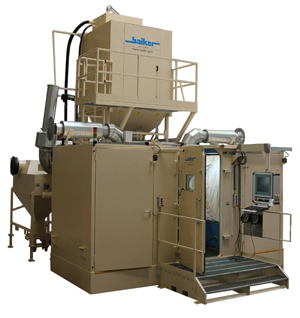
Precisión absoluta con un software de medición hecho a medida
Tras un cuidadoso análisis de todos los de equipos de la competencia, el cliente eligió el sistema de granallado totalmente automático KU 40 de Rösler. Un factor clave para la decisión del cliente era que los especialistas de Rösler podían ofrecer un sistema que permitiese una medición y calibración de las boquillas de chorro prácticamente automática. El software necesario se ha desarrollado en colaboración con una empresa de automatización, y, al mismo tiempo, el software de control para los robots ha sido optimizado para esta sofisticada aplicación de peening.
Los componentes a chorrear consisten en diferentes tipos de conjuntos de blisks con cantidades variables de álabes de la turbina y en posiciones diferentes. Después de haber colocado el conjunto de blisks en un soporte especial, el operario alinea el montaje y los bloquea. Entonces el operario monta los sistemas de medición sobre los dos robots y se inicia el ciclo de trabajo. A fin de lograr una precisión absoluta y evitar colisiones, los robots no solo deben tomar las lecturas de la distancia del soporte de la pieza de trabajo y el componente real, sino que también debe alinearse. Para este propósito, se montaron unos sensores especiales en la parte inferior de la mesa giratoria. Una vez que las tres medidas de la posición del componente se han definido exactamente, el operario retira los instrumentos de medición de los robots.
Los álabes son chorreados con las boquillas haciendo movimientos especiales, programados individualmente. Para este proceso de chorreado especial, la presión de chorreado depende de los contornos de las palas y, por lo tanto, se deben ajustar individualmente. Además de la medición en línea de la velocidad de chorreado, la supervisión continua y el ajuste de todos los parámetros pertinentes del proceso, aseguran que el valor especificado de tolerancia Almen no se supere. Además, para cada componente tratado, se genera automáticamente un registro de proceso en el que todos los parámetros del proceso están documentados. El chorreado adicional de la base de blisk se lleva a cabo mientras que el componente está en rotación continua.
La limpieza de la granalla y el sistema de reciclaje fueron diseñados y construidos de acuerdo con los estándares aeroespaciales existentes y está equipado con un separador en espiral y un sistema de tamizaje vibrante para separar la granalla inutilizable. El suministro continuo de la granalla a las boquillas de chorro está garantizado por un sistema granallado de doble presión.
Programación OFF LINE de los nuevos programas de granallado
Actualmente se almacenan dos programas de granallado en el PLC del panel de control del sistema. Para el tratamiento de componentes adicionales, los pasos y parámetros de proceso pueden ser fácilmente definidos en un entorno de programación en línea con la ayuda de un modelo 3D completo del sistema granallado. Los nuevos programas se pueden cargar directamente en el PLC. La selección de los programas de granallado, la medición y las operaciones de calibración, se realizan desde el panel táctil de fácil manejo.
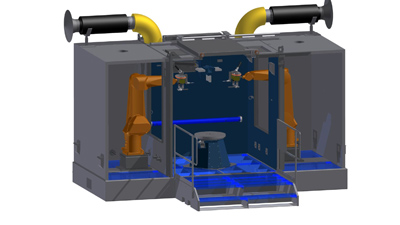
Mayor efectividad en costes y un mayor rendimiento de las piezas
La medición automática de este tipo de componentes y la calibración de las boquillas de chorreado se ha traducido en una reducción significativa de los tiempos de ajuste. Al mismo tiempo, el nuevo sistema de granallado produce un rendimiento considerablemente mayor de los componentes. Otra ventaja es que el sistema de granallado KU 40 también se puede utilizar para el reacondicionamiento y reparación de los componentes utilizados.
Como proveedor en todos los aspectos, Rösler Gmbh es pionero en el mercado internacional en la producción de acabado de superficies, granalladoras, sistemas de pintado y líneas de conservación, así como en tecnología de procesos para el acabado superficial (desbarbado, decapado, desincrustado, pulido, abrillantado…) de metales y otros componentes. Además de las plantas alemanas de Untermerzbach y Bad Staffelstein, el Grupo Rösler tiene sucursales en Gran Bretaña, Francia, Italia, Países Bajos, Bélgica, Austria, Suiza, España, Rumania, Rusia, China, India, Brasil, Sudáfrica y EE.UU.