Granallado eficiente de piezas de trenes de aterrizaje
Los trenes de aterrizaje de aviones se componen de una multitud de diferentes piezas expuestas a cargas extremas. Para prolongar su vida útil y prevenir la fatiga del material se considera el granallado como procedimiento indispensable sobre todo en el ámbito ‘MRO’ (Maintenance, Repair, Overhaul). Una prestigiosa compañía aérea ya se está beneficiando del sistema de granallado ALS 2000 GH1 R de Rösler para el tratamiento de los trenes de aterrizaje.
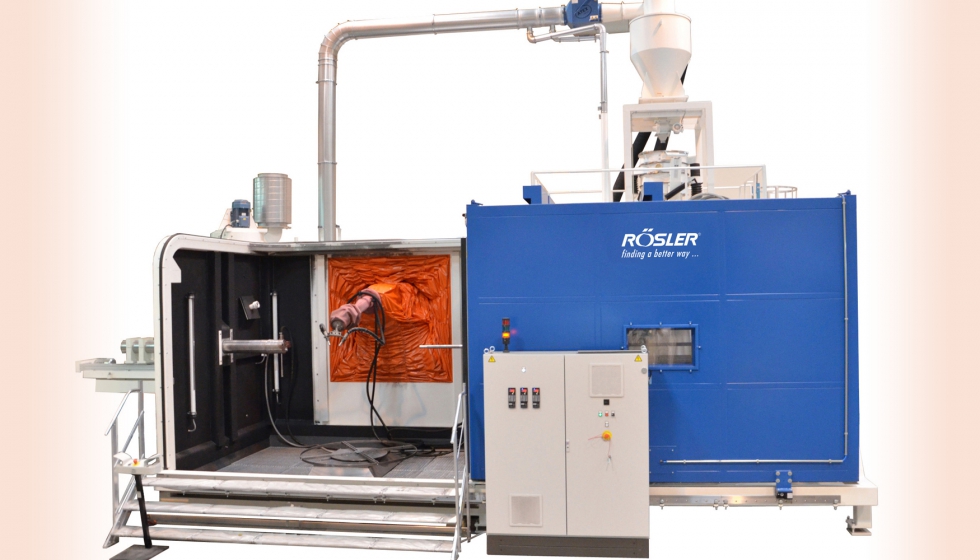
El granallado ha sido diseñado según las necesidades específicas de los clientes y cumple con las estrictas especificaciones técnicas de la aeronáutica AMS 2430 y AMS 2432. Asimismo podrá ser certificado conforme Nadcap. La ALS 2000 GH1 R está diseñada para el granallado de trenes de aterrizaje de una longitud de hasta 2.000 mm. La carga/alimentación se efectúa a través de una puerta/apertura en forma de L que además deja al aire libre grandes aberturas en el techo. De este modo piezas grandes y pesadas se pueden introducir desde arriba mediante una grúa.
Esto permite, al contrario de los carros de carga tradicionales, no sólo una construcción compacta, sino también una carga más rápida y segura para el operario. Las piezas se colocan en la mesa giratoria en función de su dimensión, verticalmente o horizontalmente y a continuación se fijan. De esta forma se garantiza un uso flexible para cada uno de los componentes de los trenes de aterrizaje. El cierre de la puerta con juntas neumáticas perimetrales reduce el nivel sonoro durante el proceso de granallado a menos de 75 dB y evita un escape de abrasivo/granalla. Un robot equipado con dos boquillas fijas o una boquilla giratoria realiza el granallado en las zonas exteriores de las piezas de los trenes de aterrizaje o en agujeros pequeños. En caso de demanda se puede chorrear al mismo tiempo el interior de la pieza con una lanza. Tanto la cantidad de abrasivo/granallado como la presión del chorreado se controlan por separado. Un sistema de doble calderín mantiene la presión uniforme y sin interrupciones. Una sonda en la parte inferior del calderín controla el descenso del nivel mínimo de llenado y da una señal de abertura a la válvula del calderín de presión superior y automáticamente fluye la granalla al calderín inferior. La granalla es recuperada a través de un sistema de aspiración neumático y es reciclada mediante un ciclón.
Control y registros a través de un sistema supervisor
El control de los procesos de la instalación se realiza a través de un sistema supervisado desarrollado por Rösler que permite la visualización de los procesos y sus registros. Todos los componentes específicos, tanto de información y programas, como de parámetros de procesos, se almacenan y supervisan constantemente en este sistema. Esto incluye también la creación de las curvas Almen, necesarias para el control de los procesos.
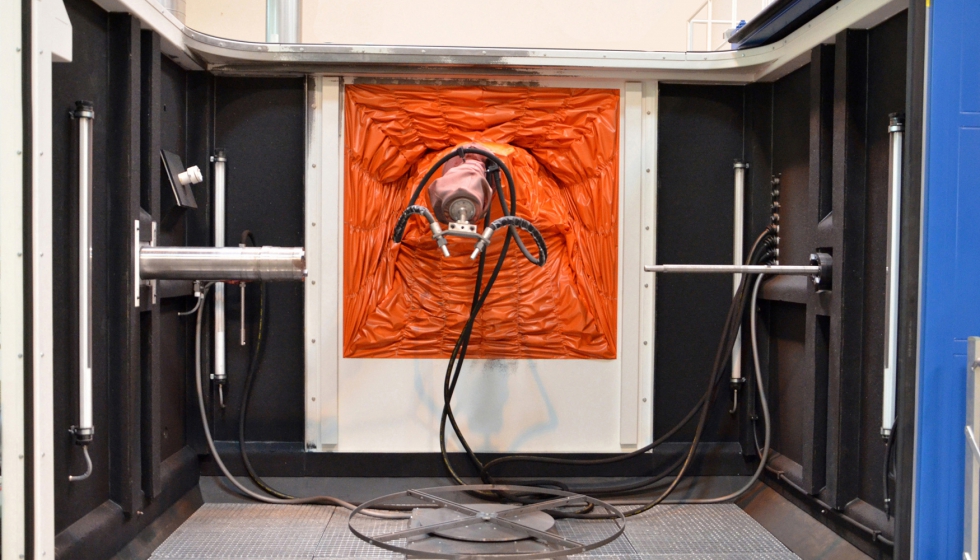