La robótica aumenta la productividad en alimentación, envase y embalaje
30 de noviembre de 2009
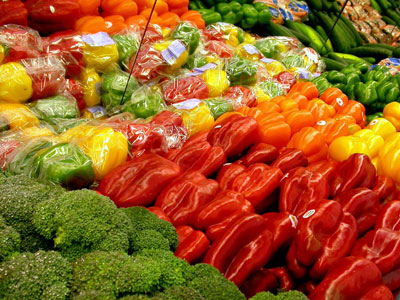
En producción de alimentos, toda aquella persona que piensa en panaderos, carniceros y cocineros solo vislumbra una pequeña parte del mercado. Ya se trate de conservas o de alimentos congelados, de productos de panificación o de dulces, pastas, salsas o bebidas, todo proceso de fabricación de alimentos se lleva a cabo a través de soluciones industriales. En definitiva, la producción en masa es la que hace asequibles a muchos bienes.
No obstante, los alimentos son productos sensibles que requieren el máximo nivel higiénico de las instalaciones de producción, así como un procesamiento rápido y preciso. De esta manera, todos los medios de producción empleados deben cumplir requerimientos específicos. Su diseño se debe ajustar a unas determinadas pautas como facilidad de limpieza y ausencia de esquinas y aristas. Los materiales han de resistir detergentes que contengan ácidos, alcoholes o disolventes, por lo que en muchos casos solo se pueden utilizar aceros inoxidables y plásticos especiales. Asimismo, sólo se pueden aplicar grasas especiales para lubricar las articulaciones. Resistencia al frío y al calor es otro criterio que deben cumplir todos los componentes de automatización; también los robots. En consecuencia, factores económicos así como requerimientos de higiene defienden el uso de los robots, aunque deben cumplir ciertas exigencias. Algo que corrobora el director de la división de Robotics de ABB Schweiz, Frank-Peter Kirguiz: “La puesta en práctica de los estándares de higiene de la industria de alimentación se pone de manifiesto en el ejemplo de ABB FlexPicker. Aquí sólo se utilizan materiales admitidos en el sector de la alimentación. Igualmente, las articulaciones ya no precisan de lubricantes, lo que excluye los correspondientes riesgos en la aplicación”.
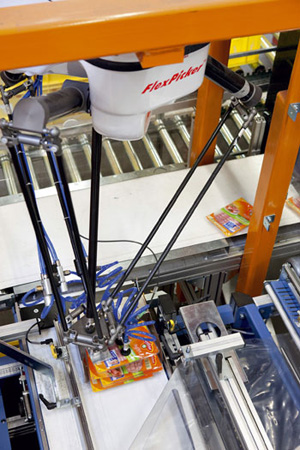
La técnica robótica se aproxima a la industria de la alimentación
En técnica robótica, las innovaciones realizadas para la industria de la alimentación son obvias. Anteriormente, las irregularidades en los alimentos dificultaban una transformación automatizada de los mismos. Una mejor comprensión de los controles de los robots y una mecánica más precisa han contribuido a que este problema sólo exista en casos excepcionales. Por ejemplo, a pesar que el reto de montar un pincho moruno es mayor que el de armar el engranaje de un automóvil, de medidas siempre iguales, los robots actuales son capaces de satisfacer muchos requerimientos en el sector de la alimentación. Además, los sensores han evolucionado de forma considerable en los últimos años. Gracias al procesamiento industrial de imágenes, hoy en día existe un método consolidado y, a menudo aplicado, para efectuar una manipulación precisa en una cinta de transporte.
Con el progreso crece la demanda de automatización. Pero sigue existiendo un problema. El director del departamento de ‘Factory Automation’ de Epson, Volker Spanier, hace hincapié en que muchas empresas alimentarias llevan mucho tiempo, incluso generaciones, fabricando de forma tradicional apenas modificada. “En muchas de estas empresas, el trabajo manual sigue siendo la norma. Por esa razón se han optimizado los procesos internos, los puestos de trabajo y la carga de material ajustándose a estos procedimientos tradicionales”.
Sin embargo, un robot tiene un ciclo diferente al de un trabajador humano y precisa también de otra infraestructura. Mientras hace algunos años todavía se luchaba con las irregularidades de los alimentos, actualmente existen dificultades de integración del robot en un puesto de trabajo originalmente pensado para un modo de trabajar humano. Estos dos retos, la difícil manipulación de ‘material’ muy diverso y las dificultades en la incorporación de un robot a los procesos de trabajo, hacen tan atractivo a este sector. Así, los fabricantes de robots e integradores de sistemas se caracterizan por el hallazgo de soluciones inteligentes.
Embalaje y paletizado son aplicaciones estándares de los robots
Entre las aplicaciones estándar de los robots figuran, en primer lugar, el embalaje y paletizado. La firma Kuka, especializada en robótica de Augsburgo, ofrece una amplia gama de robots paletizadotes, cuya capacidad de carga varía de 40 a 1300 kg. Aunque también disponen de unidades destinadas a la alimentación. Como el modelo KR 15 SL, cuya superficie es de acero inoxidable, un material resistente incluso a los detergentes más agresivos.
La automatización en los diferentes sectores de la alimentación ha avanzado de manera muy diversa, en opinión del responsable de tecnologías clave de la empresa Kuka, Peter Fornoff: "El grado de automatización asciende en la industria de las bebidas al 98% y en las grandes panaderías al 80%. En las empresas procesadoras de carne, de lo contrario, sólo llega al 20%. Aquí todavía hay un gran potencial que queremos aprovechar con nuestros robots”. En definitiva, los robots no sólo paletizan. Por ejemplo, también son aptos para medir, de forma tridimensional, mitades de cerdos, que se trocean y envasan.
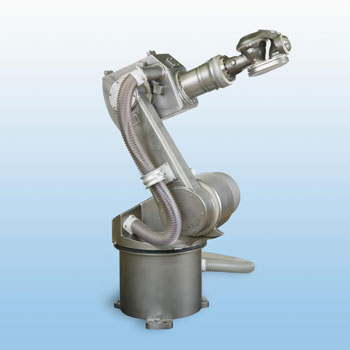
Los desarrollos innovadores incrementan la productividad
Para el sector del envase y el embalaje, las medidas estándar de los palés son decisivas. Los robots encargados de apilar bandejas de carne en un palé deben presentar un alcance suficiente que lo abarque por completo. Los robots de tipo ‘Scara’ instalados en la pared o el techo, ahorran espacio. La filial alemana de Epson se ha especializado en este tipo de automatización y brinda una amplia oferta de robots con un alcance de 175 mm para el ‘Micro-Site-Assembling’ hasta Scaras con un alcance de 1000 mm, que mueven cargas de hasta 20 kg.
La geometría del robot ‘Epson Scara-Spider’ se perfila como una solución ‘prometedora’ en el segmento de la alimentación. Este artefacto, implantado en el techo, evita la zona muerta típica de los ‘Scara’ alrededor del eje de giro 1. De esta manera, el robot puede manipular objetos que se encuentran debajo de él. Donde un sistema ‘Scara’ normal tiene que dar la vuelta, el ‘Spider’ asume el camino directo y consigue tiempos de ciclo extraordinariamente cortos. Este planteamiento permite realizar inversiones más pequeñas del robot y, a la vez, ahorra espacio de producción.
A las principales ventajas de la técnica robótica como la flexibilidad, fiabilidad y posibilidad de uso en entornos difíciles para el ser humano, se han sumado, desde hace algunos años, innovaciones tecnológicas. Por ejemplo, en el ámbito de la seguridad de los robots, una programación y manipulación más sencillas, así como una reducción de los precios. Todo ello ha aportado un gran atractivo a la implantación de los robots, que se incorporan, cada vez más, a nuevos campos de aplicación de la industria general. Es decir, al ámbito de la no automoción. Así pues, cada vez hay más robots diseñados específicamente para su empleo en la industria alimentaria.
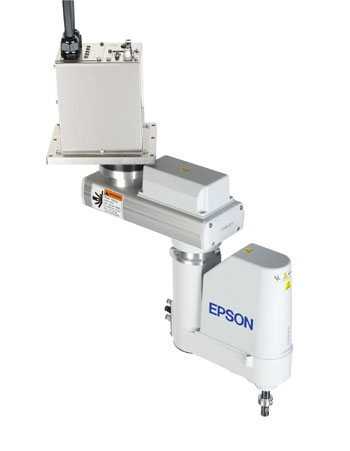
Un moderno software de procesos simplifica las aplicaciones
El director de la división de Robotics de ABB, Frank-Peter Kirgis, insiste en que no sólo las soluciones robóticas innovadoras aportan una mayor automatización en el envasado y la logística, sino que el software también desempeña un importante papel. "Un software de procesos como el ABB PickMaster desarrollado para escoger, empaquetar y paletizar, permite al usuario realizar una aplicación en muy poco tiempo. Además, es muy importante la ampliación de las interfaces correspondientes con otras plataformas de control utilizadas en el sistema. En definitiva, los instaladores de equipos quieren lograr un concepto de manejo integral de máquinas de embalaje y robots”.
Los ejemplos prácticos convencen a los más escépticos
Muchos jefes de producción que habían visto, con cierto escepticismo, la aplicación de robots en el sector de la alimentación, se muestran mucho más receptivos tras la observación de ejemplos prácticos en el mercado. Por citar un ejemplo, el uso del ABB FlexPicker en un proceso de transformación de embutidos. En particular, del sellado, la clasificación y paletizado, trabajos que hasta la fecha se habían hecho a mano en la fábrica de embutidos Heinrich Nölke situada en Versmold, en el este de Westfalia. La empresa sella envases acabados de capas de diferentes tamaños para suministrar al cliente. Debido a la creciente cantidad de productos, el fabricante decidió automatizar esta operación. Un componente de la compleja instalación es un ABB IRB 340 FlexPicker que coloca los diferentes productos en el lugar deseado en el dispositivo de sellado, donde se sellan, etiquetan y transportan a una mesa. Allí caen en una caja que se paletiza para su posterior uso. El responsable del integrador externo de sistemas de Man Industrie-Automation, Tobias de Man, afirma: "A la hora de elegir el robot, para mí fue decisivo no sólo el aspecto de las posibilidades de limpieza y estanqueidad, sino también la rapidez y precisión del robot ABB. Además, su área de trabajo está hecha a medida de la aplicación”.