Planchas CTP con superficie cerámica: la evolución de la especie
20 de enero de 2011
Recordando brevemente la historia del offset, podemos constatar que el gran éxito de este sistema de impresión no fue, en primer término, mérito de la máquina de imprimir sino de la preparación de la forma impresora que, con sus continuos progresos, condujo a lo que hoy es el offset: un procedimiento de impresión universal con calidad fotográfica.
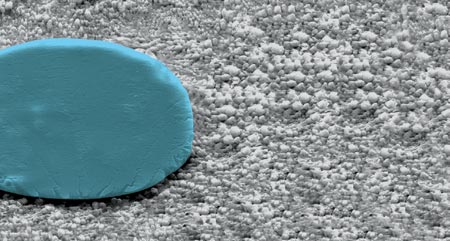
El offset y las planchas en la Historia
El gerente de LithoPlate explica que el principio básico del offset, es decir, el proceso de transferencia de la tinta con los tres cilindros (cilindro portaplancha, cilindro portamantilla y cilindro impresor o de contrapresión) no ha variado desde que fue patentado por Ira Washington Rubel y Caspar Hermann en 1904. “Donde verdaderamente se han producido cambios muy importantes ha sido en las planchas y en su modo de preparación”, sostiene Juan Hernández. Después de las piedras litográficas, las primeras planchas metálicas que se utilizaron desde principios del siglo XX hasta los años de las décadas de 1950 y 1960 fueron las planchas de zinc, que podían fijarse a la máquina de imprimir curvadas sobre un cilindro.
Estas primitivas planchas se reutilizaban varias veces para diferentes trabajos y su preparación artesanal resultaba muy larga y laboriosa, ya que cada plancha requería más de diez operaciones diferentes: borrado del trabajo anterior, graneado mecánico, limpieza, emulsionado, exposición, revelado, corrección, grabado, lacado, decapado y engomado, entre otras. “Este proceso se acortó durante los años de la década de 1960 con las planchas de aluminio micrograneadas de un solo uso, ya listas para ser emulsionadas”, añade el gerente de Lithoplate.
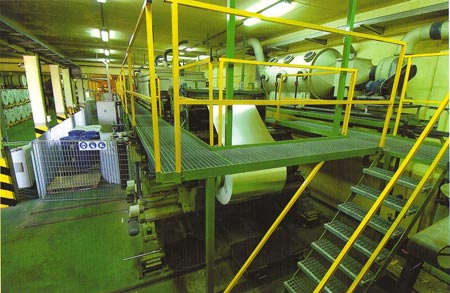
El material de las planchas
La aparición años más tarde de las planchas presensibilizadas, positivas y negativas, que sólo necesitaban la exposición y el revelado, contribuyó decisivamente a la expansión del offset, por la facilidad y rapidez de su preparación.
Este tipo de planchas presensibilizadas de tipo analógico o convencional, sigue utilizándose en todo el mundo, aunque cada vez en menor proporción, sustituidas por las modernas planchas digitales CTP: térmicas, de luz visible, ink-jet, sin revelado...
Curiosamente, explica Hernández, donde no se han producido cambios o mejoras significativas durante los últimos 40 años ha sido en el material de base de las planchas, pues tanto las planchas analógicas como las nuevas digitales siguen incorporando una lámina de aluminio electrograneada y anodizada sobre la que se deposita la capa sensible correspondiente. Probablemente, sostiene el gerente de Lithoplate, “esta continuidad ha sido debida a que, por un lado, el aluminio electrograneado constituye una base relativamente económica y, por otro, al comportamiento aceptablemente bueno de las planchas anodizadas en la máquina de imprimir”.
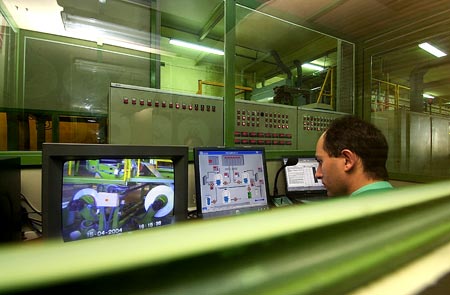
Tras años de investigación
A finales de la década de 1990, LithoPlate, “el más veterano fabricante de planchas español”, retomó la idea de otro fabricante nacional ya desaparecido, la empresa Sers, para el desarrollo de una nueva superficie impresora de base cerámica. “Las primeras pruebas a nivel de laboratorio dieron resultados muy prometedores, por lo que iniciamos un largo proceso de investigación y desarrollo que culminó, años más tarde, en la obtención de una patente internacional y en la construcción de una moderna línea de fabricación a escala industrial”, explica Hernández.
“Inicialmente, se fabricaron varios miles de metros cuadrados de planchas cerámicas con emulsión positiva convencional, que despertaron gran interés en numerosos impresores por su excelente resultado en la máquina de imprimir”, comenta. No obstante, el mercado de las planchas convencionales empezaba a ser “muy limitado”, debido a la rápida expansión del sistema CTP, por lo que se decidió poner a punto una emulsión CTP térmica compatible con el nuevo substrato cerámico.
Las planchas cerámicas y el entorno
Según sostiene Hernández, las planchas cerámicas contribuyen también a la mejora ambiental, pues reducen o eliminan el alcohol isopropílico en la impresión, disminuyen el consumo de revelador y, durante su fabricación industrial, no se produce disolución de aluminio ni vertidos que deban ser neutralizados, como ocurre en la fabricación de todas las demás planchas no cerámicas.
A lo largo de los años 2009 y 2010 se logró optimizar dicha emulsión, y se realizó un gran número de pruebas y series beta con un grupo seleccionado de impresores, que permitieron su ajuste definitivo y la puesta a punto de un proceso automatizado de fabricación en continuo, que garantiza la producción de planchas cien por cien fiables y de constante buen resultado.
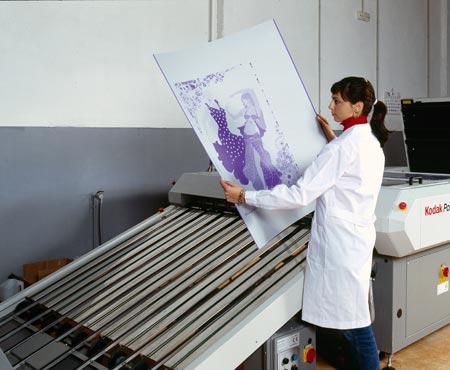
“Actualmente, LithoPlate fabrica con regularidad las planchas CTP térmicas (Ceramic Thermal Plate), que son usadas por un número cada vez mayor de impresores, pues todos los que las prueban constatan, sin excepción, su excelente calidad de impresión”, afirma el gerente de la compañía. Esta mayor calidad de impresión se obtiene gracias a que permiten reducir la humectación, entre un 20 y un 30%, según el sistema de mojado y los aditivos utilizados en cada caso.
Con su utilización práctica en muchos talleres, han aparecido otras ventajas que no estaban inicialmente previstas, como son la facilidad de exposición y revelado que alarga la duración del revelador y de los diodos térmicos, debido a la sinergia que se produce entre la capa cerámica (aislante del calor) y la emulsión térmica.
Las planchas CTP cerámicas son para Juan Hernández “las más ecológicas y, probablemente, las que proporcionan la mejor calidad de impresión del mercado, por lo que representan una importante contribución al constante progreso de la impresión en offset”.