Las planchas offset
11 de julio de 2008
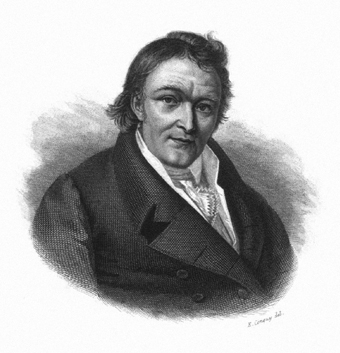
No fue hasta 1904-1907 cuando resultó viable el moderno proceso de impresión offset, también basado en fenómenos físico-químicos, dejando atrás el proceso tradicional sobre piedras, que utilizaban extractos de grasa y agua.
El offset, líder actual de la impresión, surgió de los desarrollos creados en el campo de las planchas de zinc a comienzos del siglo XX, haciendo uso de la impresión indirecta, que ya se utilizaba para imprimir hojalata. Sin embargo, la gran expansión del offset llegó en los años 50, cuando los proveedores de la industria gráfica perfeccionaron sus productos, en particular las tintas, soluciones de mojado y demás agentes del proceso.
Un procedimiento de impresión universal, con calidad fotográfica
Así, vemos que la historia del éxito del offset no es, en primer término, mérito de la máquina de imprimir, pues un análisis histórico de la impresión offset demuestra que fue la preparación de la forma impresora, con sus continuos progresos, la que ha conducido a lo que es hoy el offset: un procedimiento de impresión universal, con calidad fotográfica.
El principio básico de impresión, o sea, el proceso de transferencia de la tinta con los tres cilindros: cilindro portaplancha, cilindro portamantilla y de contrapresión o cilindro impresor, no ha variado desde que fue patentado por Ira Washington Rubel y Caspar Hermann en 1904, hasta nuestros días. Donde verdaderamente se han producido cambios revolucionarios ha sido en la plancha o forma impresora y en su modo de preparación, cuya cronología aproximada presentamos seguidamente.
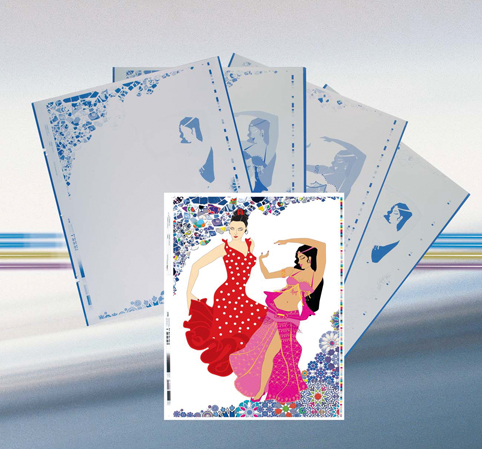
1900-1947
Utilización de técnicas manuales litográficas sobre piedra y zinc. En ambos casos se requería una cuidadosa preparación de la superficie mediante soluciones ácidas, seguidas de un pulido y toscado con polvo de piedra pómez, para obtener la aspereza y graneado necesarios para el proceso litográfico a base de betún de Judea y lápices grasos y, posteriormente, se llegó al primer proceso fotomecánico de copia, en negativo con albúmina-dicromato y en positivo con soluciones de goma arábiga dicromatada.
1947-1956
Hans Eggen introdujo la emulsión de copia a base de alcohol polivinílico que podía ser revelada con agua y que supuso, tras sucesivos perfeccionamientos, una mejora considerable en la preparación de las planchas. Se utilizaban planchas de zinc que se pulian y graneaban, fina y uniformemente, en los mismos talleres de imprenta, para conseguir la reproducción de las tramas y al mismo tiempo, la condución del agua durante el tiraje.
En 1949, la firma Kalle patentó la primera plancha presensibilizada con base de aluminio graneado mecánicamente, lo que supuso un progreso decisivo en el campo de la preparación de la forma impresora para offset.
Otro avance muy importante se produjo en 1956 con la aparición de las planchas de aluminio micrograneadas de un solo uso y que dieron un claro impulso a la calidad de la impresión offset, pues su grano, mucho más fino que el de las planchas de zinc, permitía una reproducción más fina, exacta y uniforme de los puntos de la película fotográfica tramada.
1956-1965
Se introdujeron las planchas de aluminio anodizadas, graneadas mecánica o electrolíticamente, que hicieron también una importante contribución a la mejora de la impresión offset por su buen comportamiento en la máquina de imprimir, pues requerían menos agua, permitían tirajes más largos y eran más resistentes que las de aluminio micrograno al desgaste y a la oxidación. Aún hoy en día, prácticamente todas las planchas offset que se utilizan en el mundo, sean presensibilizadas convencionales o las nuevas planchas digitales para CtP, se fabrican sobre esta misma base de aluminio electrograneado y anodizado.
En esta época llegaron también las planchas metálicas de varias capas, bi y trimetálicas, que tuvieron un papel significativo para los altos tirajes, pero prácticamente desaparecidas en la actualidad.
1965-2005
A partir de mediados de los años 60, una vez caducadas las primeras patentes de Kalle, se extendió paulatinamente por todo el mundo la fabricación y uso de las planchas presensibilizadas positivas y negativas, que han constituido el estándar universal de la forma impresora para offset en estos últimos 30 años.
Cabe mencionar, no obstante, la aparición a principios de los años 80 de las planchas sin agua o ‘waterless’, en las que la superficie no impresora está constituida por una capa de silicona que rechaza la tinta, y que a pesar de su gran calidad de impresión sigue teniendo un uso limitado por los problemas prácticos que implica su utilización.
Sin dejar de citar otros tipos de planchas como las electrofotográficas, de difusión de plata, o con base de papel y poliéster, ya casi desaparecidas, se puede afirmar que el cambio más importante y revolucionario en el modo de preparar la plancha offset, desde sus inicios hace más de 100 años, ha sido la aparición del sistema Computer to Plate (CtP) con el que ya no es necesaria el empleo de técnicas fotográficas, pues la imagen se forma en la plancha por la acción de un rayo láser controlado por ordenador. Las diferentes planchas que emplean esta tecnología, están provistas de recubrimientos sensibles a los distintos tipos de láseres utilizados: emulsiones fotopolimeras, de haluros de plata, térmicas, ablativas y sin procesado, entre otros.
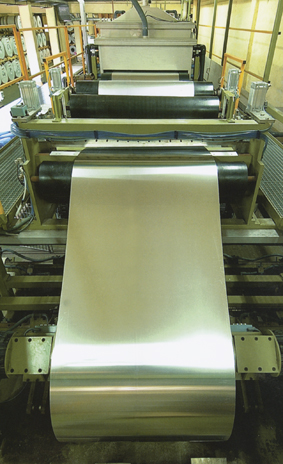
Se calcula que casi el 50 por ciento de las planchas offset utilizadas actualmente en todo el mundo ya corresponden a estas tecnologías, y su implantación sigue creciendo rápidamente, por lo que en muy pocos años, las planchas analógicas o convencionales pasarán a ser cosa del pasado, como sucedió con las planchas de zinc o de aluminio micrograneado.
Curiosamente, donde no se han producido cambios o mejoras significativas durante los últimos 40 años ha sido en el material de base de las planchas, pues tanto en las planchas analógicas como en las nuevas digitales sigue estando constituida por una lámina de aluminio electrograneada y anodizada sobre la que se deposita la capa sensible correspondiente. Probablemente esta continuidad ha sido debida a que, por un lado, el aluminio constituye una base relativamente económica y por otro, al comportamiento aceptablemente bueno de las planchas anodizadas en la máquina de imprimir.
Recientemente se ha producido una novedad importante en este campo, que ha despertado una gran expectación: la aparición de planchas con recubrimiento cerámico. Estas planchas, también con base de aluminio, están provistas de varias capas de material cerámico, en lugar de la clásica superficie electrograneada y anodizada que se ha utilizado hasta ahora por todos los fabricantes de soportes impresores.
Cabe esperar que este nuevo sustrato cerámico, fruto del trabajo de varios años de investigación de un fabricante español de planchas, sea acogido favorable y rápidamente por el mercado, ya que aporta indudables ventajas para la impresión offset: requiere menos cantidad de solución mojadora y alcohol en máquina, aumentando así sensiblemente la calidad de impresión y es muy resistente a la abrasión, permitiendo largos tirajes sin horneado. Además, no se oxida. En su fabricación no se produce disolución de aluminio contaminante de la aguas residuales, como ocurre en el proceso de electrograneado y anodizado, y su utilización permite a los impresores reducir la cantidad de alcohol isopropilico o eliminarlo totalmente.
Podemos por tanto augurar que la plancha offset que se utilizará en los próximos años será una plancha de aluminio con sustrato cerámico y provista de una capa sensible que no requerirá ningún tipo de procesado químico, uniendo la facilidad y calidad en la impresión, con el respeto al medio ambiente.