La diversidad de necesidades de impresión exige un enfoque nuevo del flujo de trabajo en la imprenta
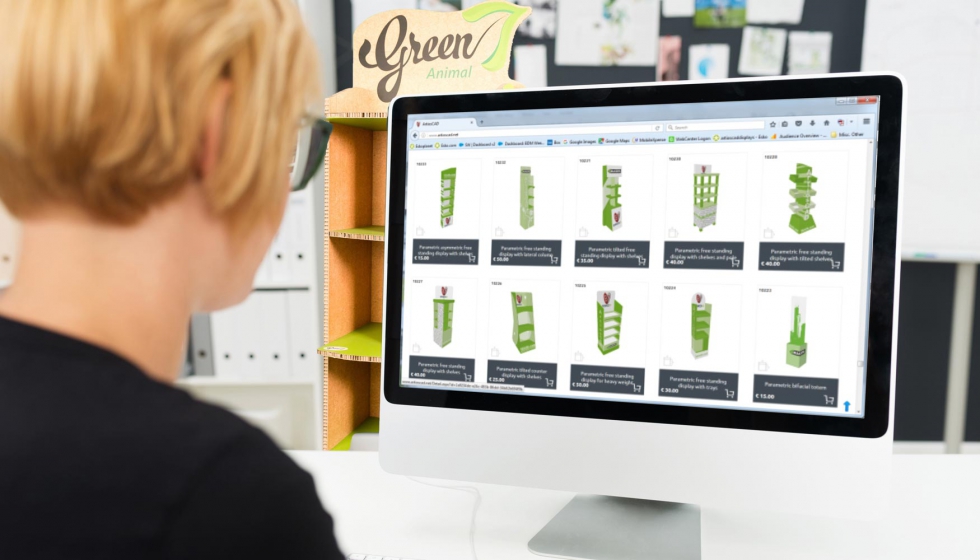
No hace tanto, cuando la capacidad de producción llegaba a su límite, lo primero que se hacía era pensar en adquirir más máquinas. Por entonces las tiradas de impresión eran casi siempre muy largas, por lo que el tiempo de actividad de los equipos era alto. La solución pasaba por invertir en sistemas más nuevos y rápidos que incrementasen la capacidad de producción. Cuando los volúmenes eran grandes y los márgenes, amplios, eso era una opción rentable.
Sin embargo, hoy en día el panorama de la impresión ha cambiado mucho, de ahí que haga falta un enfoque muy distinto en materia de inversiones y funcionamiento. Cada vez más, las marcas demandan tirajes muy cortos, con muchas variantes de diseño y plazos de entrega ajustados. En un sector en el que la mayoría de impresores usan un flujo de trabajo pensado para pocas tiradas muy largas, es normal que la eficacia se resienta, por lo cual resulta necesario revisar los procesos de gestión y producción. Aunque invertir en equipos cada vez más asequibles también es una solución, de ninguna manera es la única opción para las empresas que tienen visión de futuro.
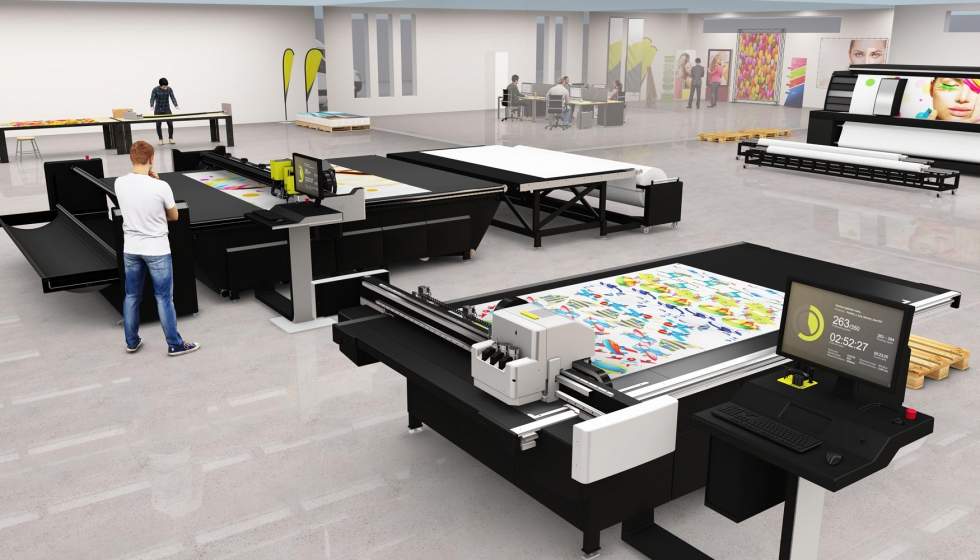
¿Dónde se generan la mayoría de mermas en el flujo de trabajo?
Antes de invertir en equipos nuevos, las empresas deberían evaluar concienzudamente todas las fases del negocio, desde la recepción de pedidos hasta la facturación, pasando por las entregas. A fin de aumentar la eficacia para manejar mejor las tiradas cortas, hace falta examinar a fondo todos los pasos del flujo de trabajo para saber en qué podemos mejorar, o lo que es lo mismo, ahorrar. Si revisamos el proceso de trabajo desde una perspectiva nueva y objetiva, encontraremos oportunidades para reducir costes, acortar plazos y minimizar errores y defectos. Este enfoque deberá tener en cuenta el flujo de trabajo entero: lo último que queremos es adoptar cambios que mejoren la eficacia en un área pero generen cuellos de botella en otra. Una vez que tengamos un flujo de trabajo eficaz, podemos evaluar la capacidad de producción para decidir si necesitamos invertir en equipos nuevos. En la mayoría de casos, al optimizar el flujo de trabajo, incrementamos la capacidad.
Una buena manera de empezar con este enfoque nuevo es plantearse la pregunta siguiente: ¿dónde se generan la mayoría de mermas del flujo de trabajo? Todas las fases del proceso ‒desde la introducción de pedidos hasta la entrega, pasando por la preimpresión‒ pueden producir mermas, sobre todo cuando los requisitos del cliente cambian; es decir, el flujo de trabajo más óptimo en el pasado puede generar un gran desperdicio de recursos hoy. Algunos procesos secundarios pueden ralentizar la producción, ocasionar retrasos y repeticiones, así como aumentar la probabilidad de que las máquinas estén inactivas y de que el cliente rechace el trabajo.
El flujo de trabajo suele estar compuesto de varias fases: diseño, cotización, aprobación del cliente, preimpresión, impresión, corte y empaquetado. En todos estos pasos, hay margen de mejora. Para simplificar el proceso, Esko ha identificado seis aspectos que toda empresa debería evaluar para descubrir en qué puede mejorar. Jan De Roeck, director de gestión de soluciones de Esko, nos ayuda a analizar estos seis factores.
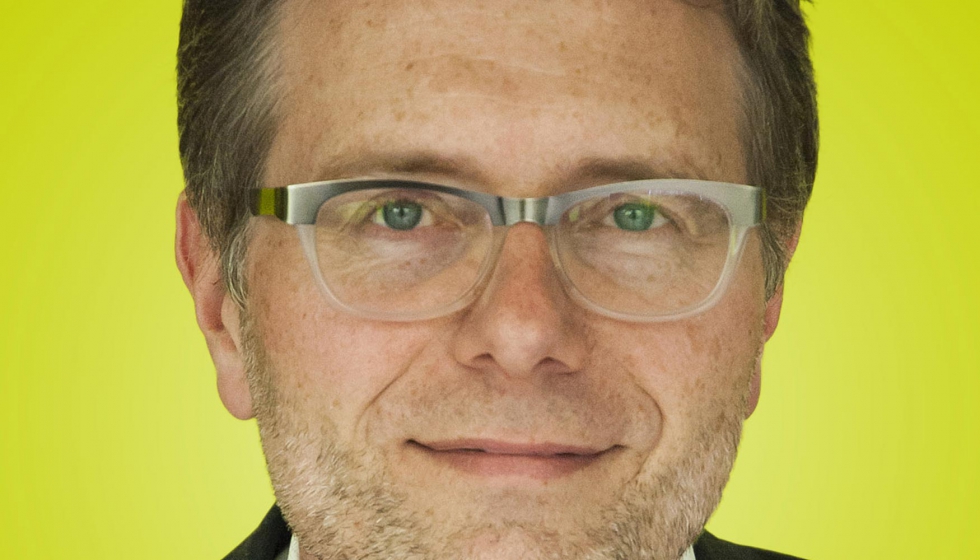
1. Reducción de los ciclos de aprobación
“El proceso de aprobación puede ser muy largo porque con frecuencia hay que presentar varios diseños al cliente hasta que esté totalmente satisfecho. Si usamos la reproducción tridimensional de los diseños de displays antes de fabricar una maqueta física, podemos acortar el ciclo de aprobación de manera considerable. Además, podemos integrar esta función en un flujo de trabajo automatizado por completo, que incluya también la comunicación con el cliente”, explica De Roeck,
Implantar sistemas avanzados de automatización capaces de preparar archivos con la mínima intervención humana es una buena manera de reducir las mermas. Con estos métodos automáticos, integrados en herramientas web de colaboración y aprobación, mejora la eficacia de la cadena de suministro y la interacción entre agencias de diseño, impresores y clientes. No existen dos flujos de trabajo idénticos, así que la forma que tiene cada empresa de llevar un archivo desde la fase de diseño hasta la de entrega varía, de modo que las compañías deberían buscar soluciones que sean lo suficientemente flexibles para adaptarse a sus necesidades concretas.
2. Eliminación de errores en los archivos gráficos
“Los diseños de rótulos o displays pueden venir de muchas fuentes distintas, en formatos diferentes y con componentes diversos", dice De Roeck. “Hay que revisar, corregir y anidar los archivos en el soporte adecuado antes de mandarlos a imprimir para evitar retrasos y costes adicionales, así como mermas, que se generan cuando llegan a la máquina archivos imprecisos. Por desgracia, las comprobaciones manuales suelen provocar cuellos de botella y pérdidas de un tiempo muy valioso durante la fase de preimpresión”.
“Una verificación previa automatizada es un método rápido que contribuye a evitar que el cliente rechace trabajos —con el consiguiente sobrecoste para el impresor— y puede reducir los errores de diseño en un 70%. Con Automation Engine y i-cut Suite de Esko, todos los archivos gráficos pueden convertirse automáticamente a PDF y pasar por el proceso de preimpresión con un editor para, cuando haga falta, uniformizar la calidad y reducir el número de pedidos rechazados por parte del cliente. Estandarizar y automatizar por completo la fase de preimpresión elimina las restricciones de capacidad, lo que permite aceptar un mayor volumen de trabajo”.
La canadiense Holland & Crosby invirtió en dos mesas de acabado Esko Kongsberg C64 para seguir el ritmo de producción de sus rapidísimas impresoras planas. También usa i-cut suite y Automation Engine de Esko para perfeccionar el sistema, de manera que los archivos se verifiquen con mayor rapidez y eficacia. “Antes la fase de impresión solía ser el principal cuello de botella, pero luego nos atascamos con la verificación previa, el acabado, la distribución y las entregas a tiempo”, reconoce Scott Crosby, vicepresidente de ventas y marketing de Holland & Crosby. “Todavía estamos en pleno proceso de mejora del flujo de trabajo, para lo cual Automation Engine y i-cut suite nos están siendo muy útiles”.
3. Importancia del diseño CAD
“La falta de conocimientos en diseño estructural puede ocasionar muchas mermas”, apunta De Roeck. “Además, a veces se pierden encargos porque el proveedor no tiene las habilidades necesarias para diseñar y producir el display que quiere el cliente”.
Con la ayuda de un programa de CAD, puede reducirse el tiempo de diseño en un 90% y, para simplificar el proceso, Esko ofrece QuickBox, una biblioteca opcional de i-cut Production Console con quince mil plantillas de diseño paramétrico de envases para ayudarle a preparar hasta las cajas más complejas. Para diseñar displays de PLV en 3D, ArtiosCAD Display Store es una solución ideal. Y para las empresas que cuentan con diseñadores CAD en plantilla, ArtiosCAD ofrece todas las herramientas necesarias para ser más eficaces.
Un ejemplo es la canadiense Impulse Graphic and Display Solutions, que escogió Automation Engine de Esko para reducir la intervención de los operarios y automatizar el montaje por repetición en las impresoras y en las mesas de corte Kongsberg. La empresa también invirtió en Esko ArtiosCAD para añadir el diseño estructural a su oferta de servicios. “Queríamos adaptar el flujo de trabajo a nuestras necesidades y aprovechar las aplicaciones de Esko para preimpresión”, afirma Alexander Cachia, presidente de Impulse. “Con Esko ArtiosCAD, podemos crear diseños estructurales en 2D o 3D y conectar esos archivos con Automation Engine para imprimirlos y luego acabarlos en las mesas Kongsberg. Así, el proceso de preimpresión es muy fluido y eficaz”.
4. Mejora del control de la producción
De Roeck lanza algunas preguntas al vuelo: “¿Con qué frecuencia la diferencia entre el precio dado al cliente y el coste real de producción se acaba “comiendo” el margen de beneficio? ¿Con qué frecuencia tiene que pedirle a la plantilla que realice un esfuerzo extra para terminar a tiempo un trabajo urgente? Saber con exactitud cuánto se tarda en producir un encargo —tiempo de preparación incluido— y cuándo es el mejor momento de priorizar un trabajo urgente en la cola de impresión es fundamental. La falta de transparencia respecto a la carga de trabajo de los departamentos y las máquinas perjudica su flexibilidad y, en última instancia, la rentabilidad”.
Device Manager de Esko ayuda a las empresas a controlar mejor la producción, ya que permite mejorar la eficacia de aspectos clave de la imprenta. Con este software, puede cotizar los encargos, distribuir la carga de trabajo entre las mesas de corte Kongsberg y dar al personal la posibilidad de conocer el estado de las unidades de acabado desde la comodidad de la oficina. Asimismo, Device Manager genera informes y conserva un historial de actividad para que pueda controlar el tiempo improductivo y conseguir una producción más ajustada (lean).
5. Eficacia de las mesas de corte
“Manejar una mesa de corte puede ser una tarea manual compleja”, dice De Roeck. “Preparar un trabajo puede llevar hasta treinta minutos, lo que, al cabo de muchos encargos, puede ascender a horas de inactividad de las máquinas, sobre todo en el caso de proyectos de tiradas cortas, que pueden llegar al centenar en un día. Encontrar la herramienta de corte o hendido adecuada para cada material no siempre es fácil, y la calidad final a menudo depende de la habilidad del operario en cuestión. A veces, para compensar los pedidos rechazados por el cliente, algunos proveedores incluso añaden un porcentaje a cada trabajo, lo que se traduce en precios menos competitivos y menos rentabilidad”.
Las mesas de corte simplificadas son más rápidas y fáciles de manejar, aumentan la producción en un 10% y reducen los errores. La tecnología Shared Resources de Esko, incluida en i-cut Production Console, permite uniformizar la producción, ya que analiza el archivo de corte y automatiza la preparación de la mesa y la elección de la herramienta.
La británica Data Image Group Ltd ha acortado los plazos de entrega, reducido las mermas, optimizado la producción de los equipos y gestiona las tiradas cortas de manera más eficaz después de haber invertido en un sistema de acabado automático Kongsberg C con brazo robótico. “Automatizar el departamento de acabado es muy importante para el futuro de nuestro negocio”, asegura Robert Farfort, director de Data Image Group. “Al cargar y descargar el material automáticamente, las operaciones de corte son mucho más eficaces”.
Data Image Group también utiliza Device Manager de Esko para supervisar el estado de los trabajos al momento y gestionar y priorizar las colas de producción de todos los dispositivos conectados.
6. La difícil fase final
“El último paso del flujo de trabajo tiene lugar en el departamento de empaquetado. Las consecuencias de las mermas previas se acaban notando aquí”, señala De Roeck. “Una ligera modificación del producto o del flujo de trabajo, que no suele documentarse, puede provocar que el empaquetado sea incorrecto o ineficaz. En el peor de los casos, puede afectar al montaje o la instalación rápida y precisa de los diseños o displays en su destino, lo que a su vez puede ocasionar que el cliente reclame daños y perjuicios, lo que tiene un coste elevadísimo”.
Es posible mejorar la eficacia del transporte con la ayuda de cajas que se adapten perfectamente a los productos acabados. Esko ofrece soluciones como QuickBox, incluida en i-cut Production Console, o el software de paletización Cape para tirajes más largos.
Flujos de trabajo conectados, la respuesta a las nuevas necesidades
Dedicar tiempo a evaluar los pasos que hemos mencionado ayuda a las empresas a tomar mejores decisiones sobre la inversión en equipos de producción. Si implantamos bien estas fases, independientemente de la cantidad de pasos y de su complejidad, el flujo de trabajo entero queda interconectado. Así, las empresas pueden controlar el proceso de producción entero en vez de concentrarse en pasos sueltos de la cadena.
Los clientes piden artículos totalmente acabados, producidos de manera rápida y rentable, una tendencia que solo hará que acentuarse a medida que el mercado se vuelva más competitivo. El enfoque nuevo del flujo de trabajo permite al impresor y a la empresa de manipulado asumir un rol más consultivo en la relación con el cliente que va más allá de imprimir: su papel se vuelve más importante para crear diseños que tengan en cuenta el acabado a fin de eliminar las mermas. De esto modo, los diseños de rótulos y displays pueden optimizarse para aumentar el rendimiento, minimizar el desperdicio, acortar los plazos de entrega y reducir los costes, tal y como demandan los clientes.
“La clave está en identificar en qué aspectos se puede mejorar la eficacia y estandarizar los procesos para eliminar las mermas”, concluye De Roeck. “Las soluciones de Esko ayudan a convertir las mermas en tiempo que aporta valor añadido en todas las fases del proceso. Detectar los pasos ineficaces no es difícil, pero entender cada fase del flujo de trabajo y el funcionamiento en su conjunto puede ser complejo. El compromiso de Esko es ayudar a las empresas a resolver esta complejidad para mantener su competitividad en un mercado dinámico”.