Cabezales de rodillos sin disolvente
Dar una mejor impresión
Los disolventes químicos que se usan para preparar las mantillas de impresión se asocian cada vez más a riesgos medioambientales. Los cabezales de rodillos sin disolvente de Trelleborg reducen el impacto medioambiental a la vez que mejoran la velocidad y la eficiencia de la impresión.
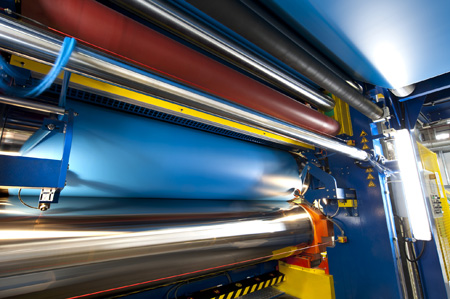
Un poco de seguridad vale mucho, dice Linus, el amigo de Charlie Brown que nunca se separa de su manta en la historieta 'Peanuts'. La seguridad también vale mucho en la vida real, sobre todo cuando la “manta” forma parte de una moderna máquina impresora. Las mantillas de impresión son tejidos compuestos con un recubrimiento polimérico usados para transferir la tinta desde la plancha a la superficie de impresión. En su fabricación, tradicionalmente, se han utilizado productos químicos inflamables.
El impacto medioambiental no era un tema prioritario cuando se desarrolló la prensa offset de bobina en 1904. Pero las demandas han cambiado en los últimos 110 años. Hoy se reconocen cada vez más los inconvenientes de los disolventes químicos usados para preparar las mantillas de impresión. Antes, las prensas se utilizaban más que nada para imprimir periódicos. Hoy, son máquinas especializadas que producen sofisticados embalajes y aplicaciones con decoración metálica.
Con más de medio siglo de experiencia en la producción de mantillas para prensas digitales y offset, Trelleborg es especialista en su sector y, además de calidad y prestaciones, también piensa en la sostenibilidad medioambiental.
“La atención al medio ambiente, la salud laboral y la seguridad (EHS) es un deber para Trelleborg”, dice Biagio Montano, jefe de ingeniería responsable de EHS de Trelleborg Coated Systems en Lodi Vecchio, Italia. Aunque la tecnología tradicional para la producción de mantillas de impresión precisa disolventes, Trelleborg siempre ha cumplido las leyes y normativas locales y es una empresa puntera en el respeto por el entorno y el control de su proceso de fabricación para lograr niveles muy bajos de emisiones.
Las soluciones sin disolvente empezaron a aparecer hacia finales de la década pasada. Trelleborg decidió desarrollar su propia solución sin disolvente, incorporando no sólo lo último en tecnología de impresión sino también cumpliendo las expectativas de sus clientes en materia de calidad, velocidad y flexibilidad. Ante la tendencia hacia cilindros más grandes, Trelleborg decidió además dotar su nueva línea de cabezales de rodillos sin disolvente de la capacidad necesaria para producir la mantilla más grande del mercado, de 2,7 metros.
Para producir una mantilla de impresión tan grande, no basta con alargar el cilindro. “Fue un proyecto enorme en términos de complejidad, dimensiones, tiempo, impacto en la planta, sofisticación de la automatización y controles de todos los parámetros”, explica Montano. “La tecnología de producción de las mantillas ha pasado de extender y recubrir a extruir y calandrar, transformando totalmente el proceso de trabajo”.
La nueva línea fue estrenada a principios de 2013. A finales de 2014, la Línea de cabezales de rodillos sin disolvente representará el 70% de la producción de mantillas de Trelleborg en la planta de Lodi Vecchio, llegando al 100% en un plazo de cinco años. “Trelleborg fabrica 70 tipos distintos de mantilla de impresión para diferentes aplicaciones. Sería muy difícil cambiar inmediatamente una gama de productos tan compleja y tan amplia”, explica Montano.
Pero hecho el cambio, los resultados han sido impresionantes. En la planta de producción de mantillas de impresión de Lodi Vecchio, el consumo diario medio de disolventes había sido de unos 150.000 litros. Durante 2013, este consumo bajó un 30%. En 2014, se cree que bajará al 50% y en 2015, la reducción se situará en el 70%. El potencial para asegurar la satisfacción del cliente ha crecido a un ritmo igual de espectacular. El número de fases de producción ha bajado de 19 a 11, aportando un claro valor añadido al cliente en términos de eficiencia y tiempo. El grosor de la mantilla de caucho está mucho más controlado y ha mejorado el acabado de superficie. Otras iniciativas de Trelleborg Coated Systems para 2014 incluyen un plan para sustituir sus compresores de aire con versiones de bajo consumo energético y motores de velocidad variable. Estos nuevos compresores reducirán el consumo de electricidad un 10% y disminuirán las emisiones de CO2.
Linus, siempre con su manta, y su amigo Charlie Brown, tan preocupado por el medio ambiente, probablemente lo aprobarían.
La solución
Al no utilizar disolventes, el cabezal de rodillos desarrollado por Trelleborg ha reducido el impacto medioambiental. Pero no es el único beneficio. Al eliminar ocho pasos en el proceso de recubrimiento con caucho, de 19 a 11, la solución de Trelleborg aumenta la velocidad de producción a la vez que mejora la calidad. El producto resultante beneficia al cliente, a la comunidad y también a la empresa.
Línea de cabezales de rodillos sin disolvente
La línea de cabezales de rodillos sin disolvente revoluciona el proceso de recubrimiento con caucho para la impresión, produciendo avanzados sustratos de caucho de doble recubrimiento sin necesidad de disolventes. Con 3,2 metros y tres rodillos, su calandra es la más grande de su clase actualmente en uso y un 30% más grande que la alternativa más próxima.