La impresión 3D se emplea cada vez más en el desarrollo de prototipos, utillaje, componentes y aviones no tripulados
La fabricación aditiva gana presencia en los sectores aeroespacial, aeronáutico y de defensa
La sede del Instituto Nacional de Técnica Aeroespacial (INTA) en Torrejón de Ardoz (Madrid), acogió la primera edición de la jornada técnica ‘Fabricación aditiva aplicada a la industria aeroespacial, aeronáutica y de defensa’, un encuentro organizado por la empresa Análisis y Simulación, representante en España de la firma especializada Stratasys desde hace siete años, en el que se puso de manifiesto el gran potencial de crecimiento que atesora la manufactura aditiva.
Stratasys está considerado, según indicaba en la jornada técnica su directora comercial para España y Portugal, Inma Vázquez, como “el líder mundial de sistemas de impresión 3D”, contando con una larga e intensa experiencia en el mundo de la fabricación aditiva. En 1994, por ejemplo, Stratasys ya vendía el primer termoplástico disponible para un proceso de impresión 3D (plástico ABS); en 2008 lanzaba al mercado la primera máquina para producción (Fortus 900mc); y en 2012 contribuía con sus soluciones a desarrollar el primer prototipo de avión no tripulado con alas impresas enteramente en 3D (creado por Aurora Flight Sciences).
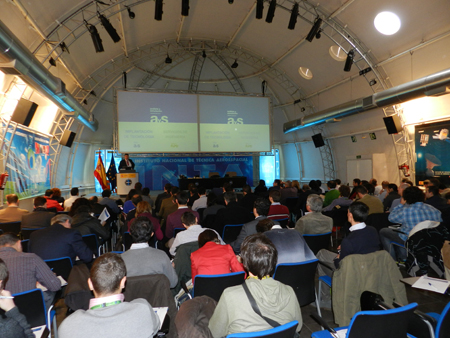
La jornada organizada por Análisis y Simulación gozó de un gran éxito de asistencia.
También en 2012, tuvo lugar un hecho decisivo en la trayectoria más reciente de Stratasys, al fusionarse con Objet, otra empresa de referencia en el campo de la impresión 3D, nacida en 1998 y que entre otros logros históricos tiene el haber fabricado la primera impresora 3D de escritorio del mundo con 7 materiales (Objet 30P) y la primera máquina de impresión 3D con más de 100 materiales.
Hoy, la compañía cuenta con más de 1.000 empleados y cerca de 500 patentes en materia de fabricación aditiva, ofreciendo sus soluciones en ámbitos tan variados como la industria aeroespacial, la automoción, la industria militar, la arquitectura, la medicina, el sector bucodental, etc. En total, estima que ha podido instalar más de 75.000 sistemas. “Creemos apasionadamente en el proceso aditivo”, señalaba Inma Vázquez, para quien este tipo de sistemas va a favorecer una nueva “revolución industrial, en la que la creatividad ya no tendrá límites”.
Para este cambio tecnológico, Stratasys se ha preparado con una completa gama de soluciones, estructurada en tres grandes series: Idea (los equipos más pequeños, pensados para la modelación de conceptos), Diseño (centrado en la impresión 3D de prototipos) y Producción (los conocidos equipos Fortus).
En impresión 3D, Stratasys emplea fundamentalmente dos tecnologías: polyjet (fotopolímeros) en aquellos casos en los que se requiere una alta precisión, y FDM (termoplásticos) para las aplicaciones en las que se exige un alto rendimiento.
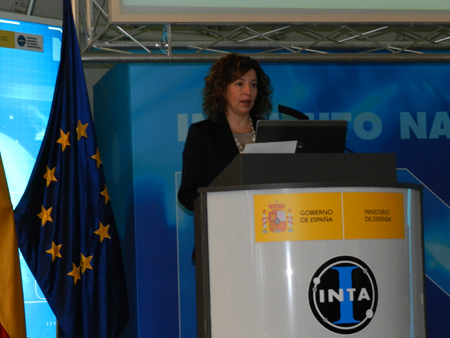
Su vocación innovadora en este campo no se detiene y la compañía ya anuncia el lanzamiento de nuevas y revolucionarias impresoras 3D, como la Objet 500 Connex 3. Todo ello para permitir que los procesos de fabricación ganen en rapidez y eficiencia y siguiendo una tendencia imparable, que fue incluso reconocida por el propio presidente de los EE UU, Barack Obama, en el discurso del Estado de la Unión del 2013 al mostrar su intención de incorporar la fabricación aditiva como un tema prioritario en todos los institutos y centros de formación del país. “Tenemos que invertir en las mejores ideas”, terminaba diciendo Inma Vázquez.
Retos superados por la fabricación aditiva
A través de su ponencia, Iker Galdos, director de producto para Fabricación Aditiva en Análisis y Simulación, quiso destacar las razones de la efervescencia que está viviendo en estos últimos años todo lo relacionado con la impresión 3D. Según reconocía, la posibilidad de imprimir un producto en cualquier parte del mundo a partir de un simple archivo informático, abre todo un mundo de posibilidades. Además, se trata de un proceso que, frente a otras alternativas tradicionales de fabricación, supone grandes ahorros económicos y de tiempo. A todo ello hay que sumar que ya han caducado las patentes de dos líderes del mercado como son Stratasys y 3D Systems, por lo que se está produciendo un 'boom' mundial de nuevos agentes que quieren entrar en este sector.
Según la definición empleada por Iker Galdos, la manufactura aditiva consiste en “manipular material a escala micrométrica y depositarlo generalmente capa a capa, para crear objetos a partir de datos 3D de un modelo, de forma opuesta a las técnicas de fabricación sustractiva”. Y dentro de este ámbito general los procesos pueden ser de lo más variado: laminación o LOM (empleo de capas de diferentes materiales), fotolitografía o estereolitografía (uso de luz UV como proceso básico de solidificación), fusión o sinterización selectiva por láser (uso de un haz de láser y electrones para la consolidación del material), polyjet (se inyectan capas de fotopolímero líquido en una bandeja y se cura al instante mediante luz UV) y modelado o deposición fundida - FDM (deposición de hilo fundido capa a capa, de termoplásticos, ABS, como material básico).
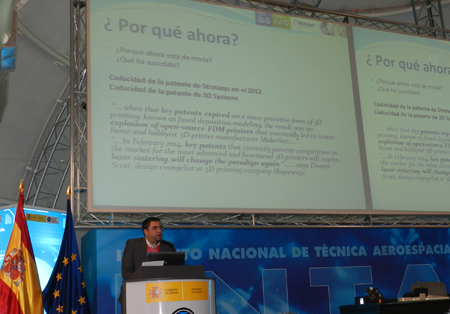
La impresión 3D avanza a un ritmo vertiginoso y tras comenzar como una fórmula de fabricación rápida de prototipos, ha pasado a ser también una alternativa rentable para la fabricación de utillaje y, más recientemente, a una opción con un alto potencial en la fabricación directa digital (piezas de uso final, en series cortas).
A pesar de las posibilidades que ofrecen estas tecnologías, España, como reconocía Iker Galdos, no aparece en el ranking de los países que más hacen uso de ellas actualmente (EE UU, Japón, Alemania, China, Reino Unido y Francia lideran esta clasificación), debido sobre todo a la tradicional reticencia de nuestra industria a avances tan revolucionarios y a la crisis económica que viene atravesando nuestro país en los últimos años.
Desde luego, la fabricación aditiva, con los últimos avances, ha conseguido superar retos que parecían insalvables en los procesos productivos: reducción de peso, mejora de la calidad, reducción de costes de desarrollo, menores tiempos de producción…, por lo que su futuro promete ser muy positivo.
Sector aeroespacial
Para conocer las oportunidades que ofrece concretamente la fabricación aditiva en el sector aeroespacial se contó en la jornada con la presencia de Santiago Martín Iglesias, ingeniero aeroespacial del INTA. Un claro ejemplo de éxito de la penetración del 3D en este ámbito es el proyecto Diana. El INTA desarrolla, desde hace años, un amplio programa de investigación para el desarrollo de las tecnologías necesarias que permitan el diseño y construcción de una gama de aviones no tripulados. Uno de estos productos es el llamado Diana, un sistema de blanco aéreo de altas prestaciones desarrollado para simular amenazas reales. Por su versatilidad, el sistema puede emplearse como sistema de entrenamiento aéreo para gran cantidad de armas actuales y futuras.
En la fabricación de las superficies móviles (estructurales) de este avión no tripulado se ha sustituido los elementos de polímero reforzado por fibra de carbono (CFRP) por elementales integrales de poliamidas. Con ello, según confirmaba Santiago Martín, se han reducido los tiempos en un 50% para producción unitaria (80% en serie) y los costes en un 70% respecto al laminado con núcleo.
Los principales logros de esta sustitución en los procesos de fabricación los resumía el responsable del INTA en tres: reducción de tiempos de desarrollo (optimización), flexibilidad en la producción y repuestos a bajo coste (rápida respuesta sea cual sea la versión del diseño).
Todos los ensayos estructurales que se han realizado sobre el avión no tripulado Diana han dado resultados positivos, y las pruebas de vuelo realizadas también han sido exitosas.
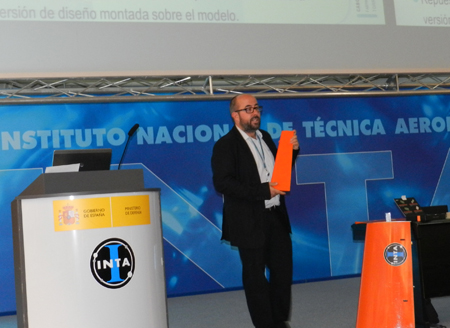
Santiago Martín Iglesias, ingeniero aeroespacial del INTA.
Como aplicaciones potenciales de la fabricación aditiva dentro del sector aeronáutico, Santiago Martín apunta, entre otras, la optimización topológica de las estructuras, sistemas optimizados de refrigeración, elementos de radiofrecuencia, maquetas y las estructuras primarias especiales (refrigeración integrada, por ejemplo).
No quiso terminar el responsable del INTA su ponencia sin antes mencionar algunas necesidades que tienen los diseñadores e ingenieros de este tipo de productos y en cuya solución aún podrían profundizar las soluciones de impresión 3D, sobre todo en el ámbito aeroespacial donde un mínimo error puede ser fatal: mejorar el binomio máquina-material, optimización de estrategias productivas, desarrollo de nuevos materiales, nuevas estrategias de diseño, tratamientos superficiales específicos, posicionamiento de insertos durante el proceso, inserción de fibras continuas direccionales, mayor rapidez, precisión y trazabilidad de la calidad… En resumen, y como concluía el responsable del INTA, “hay que arriesgar, hay que apoyar este tipo de desarrollos, sin perder las ganas y la ilusión”.
Antes de la pausa del café, David del Fresno, de Análisis y Simulación, hizo un breve resumen de los tres modelos Fortus que hay actualmente en el mercado, 360 mc, 400 mc y 900 mc, los cuales se diferencian entre sí, fundamentalmente, por el tamaño y por los materiales que pueden emplear. “Las máquinas Fortus son las más fiables que he visto en este mercado, se amortizan en muy poco tiempo, permiten fabricar de una forma muy ágil y su instalación es realmente sencilla”, afirmaba.
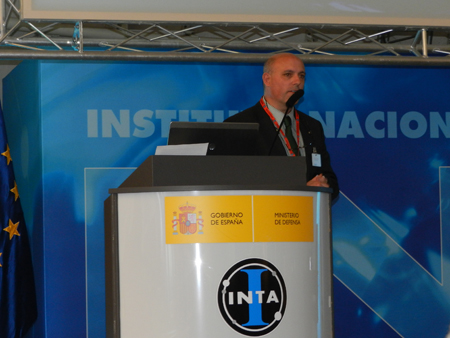
David del Fresno, de Análisis y Simulación.
Materiales actuales en FDM
En 1988 Scott Crump inventó el modelado por deposición fundida (FDM) en la cocina de su casa familiar mediante la mezcla de las fórmulas de cera y plástico. Desde entonces, las variedades que se pueden emplear con esta tecnología han crecido exponencialmente. FDM usa termoplásticos de calidad industrial y el material adecuado está en función de la aplicación que se le vaya a dar y de la temperatura que se vaya a alcanzar.
Algunos de los materiales más empleados actualmente son: ABS-M30, ABS-ESD7, PC (policarbonato), PC-ABS, PPSF/PPSU, FDM Nylon 12 y Ultem 9085 (un material cada vez más utilizado por su altísimo rendimiento).
Estos materiales se utilizan, por ejemplo, en el diseño y prototipado funcional, del que David del Fresno puso, en otra de sus ponencias, algunos ejemplos de éxito que han conllevado importantes ahorros de dinero y tiempo respecto a los procesos de fabricación anteriormente utilizados. Un caso muy notable es el de un motopropulsor de más de 200 piezas que con el empleo de una Fortus 900mc permitió un ahorro de 875.000 dólares (la fabricación del prototipo tan sólo costó 25.000 dólares frente a los 900.000 dólares que hubiera costado si se hubiera mecanizado), así como una reducción de 7,5 meses en el tiempo de producción (con la Fortus se pudo hacer el prototipo en 1,5 meses frente a los 9 meses que se hubiera tardado si se hubiera mecanizado).
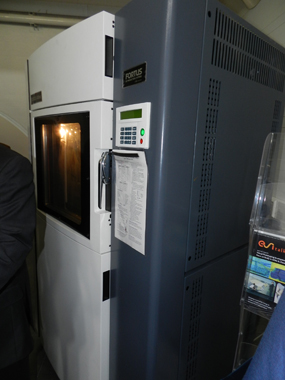
También se han logrado importantes ahorros de dinero y tiempo en la fabricación de otro tipo de prototipos, como los conductos de conducción hidráulica de un híbrido avión-helicóptero, en el tren de aterrizaje de un avión… En el campo aeroespacial, David del Fresno se detuvo en dos casos muy llamativos en cuyos prototipos se ha empleado fabricación aditiva. Para trabajar en la Estación Espacial Internacional se ha desarrollado el robot Robonaut 2, cuyo prototipo se ha realizado con máquinas Fortus y con el policarbonato como material. Para realizar este prototipo se ha tardado dos semanas con un coste de 36.000 euros, mientras que con las fórmulas tradicionales se hubiera tardado 36 semanas con un coste de 180.000 euros.
Para la exploración del planeta Marte también ha sido decisiva la participación de las máquinas Fortus ya que cerca del 70% de las piezas empleadas en la fabricación del robot Rover están hechas en policarbonato con este tipo de máquinas.
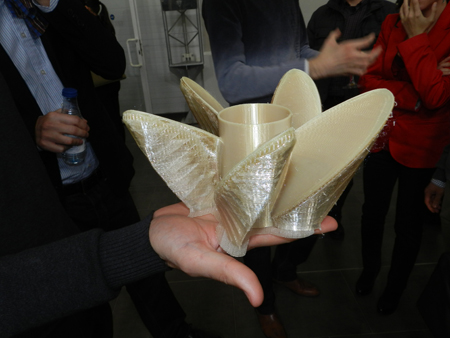
Fabricación directa
La jornada organizada por Análisis y Simulación en el INTA terminó con la exposición de diferentes casos reales de fabricación directa de utillaje aeronáutico, aviones no tripulados y componentes aeronáuticos. El propio David del Fresno expuso diferentes ejemplos de cómo la fabricación aditiva ha conseguido reducir los costes económicos y el tiempo empleado para el desarrollo de diferentes productos. Hay casos en los que los fabricantes han obtenido ahorros en los costes de hasta el 95% y de los tiempos de un 88%, como el mencionado en la jornada de un fabricante que pasó a fabricar con ABS en lugar de por fundición por proceso a cera perdida.
En procesos como la fabricación de cascos para uso militar, composites para la reparación de helicópteros, componentes destinados al interior de aeronaves de lujo, piezas de gimbals de vigilancia, carcasas ignífugas para instrumentación de aviones, fuselajes y carenados para aviones no tripulados, etc. se emplean ya con éxito sistemas de manufactura aditiva.
Boing, por ejemplo, fabrica aviones no tripulados ligeros para uso militar (UAV RM-1) mediante máquinas Fortus 400mc y empleando como material ABS. En apenas tres días puede fabricar uno de estos aviones. E incluso hay una empresa, UAV Solutions, que ya desarrolla aviones no tripulados íntegramente en Ultem 9085.
El futuro más inmediato en el campo de los aviones no tripulados, como concluía David del Fresno, pasa también por la impresión directa de los circuitos, un ámbito en el que ya hay empresas trabajando intensamente (fase de desarrollo).
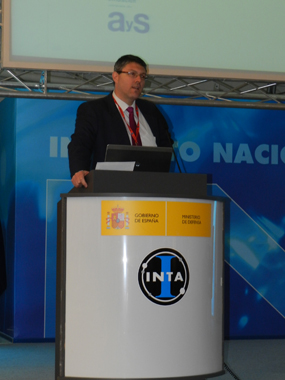
Soluciones adaptadas a las necesidades de los clientes
Análisis y Simulación es, como indica su director gerente José Julián Martínez, “una ingeniería especializada en la integración e implantación de tecnología avanzada, para el desarrollo e innovación de producto, optimización y mejora de los procesos de fabricación, gestión e infraestructura”.
Dentro de la estructura de este grupo también se encuentra la empresa P&PD, una ingeniería de servicios especializada en el diseño, simulación y desarrollo de producto, teniendo en cuenta el proceso fabril.
Con el lema ‘Nuevas formas de hacer’ desde la compañía se trabaja para crear hábitos con las nuevas tecnologías, colaborar y ejecutar nuevos proyectos y capacitar a las personas para el desempeño de sus funciones. “Queremos aportar valor a las empresas”, resumía José Julián Martínez.
Análisis y Simulación, fundada en 1997, cuenta a día de hoy con 74 trabajadores, los cuales conforman “un equipo estable, motivado, capacitado, multidisciplinar y orientado a las personas”, indicaba el máximo responsable de la compañía. Tiene sedes en Álava, Barcelona, Guadalajara, Reino Unido y China, y ofrece una amplia variedad de servicios preventa/consultoría (rediseño de piezas, cálculo, simulación, fabricación aditiva, ensayos…) y servicios postventa (instalación de máquinas y sistemas, formación, asistencia técnica, mantenimiento…). Además, para aquellos clientes que lo requieran la compañía también pone a su disposición paquetes completos de trabajo con recursos humanos y técnicos de Análisis y Simulación (salvo los trabajos de laboratorio, que se externalizan).