La estrategia Voxelfill supera las resistencias no homogéneas en la impresión 3D
AIM3D consigue demostrar las ventajas del método patentado Voxelfill. Las pruebas de resistencia demuestran que este método puede superar las resistencias no homogéneas de los componentes 3D en los ejes de X, Y Z, alcanzando la efectividad de métodos convencionales como el moldeo por inyección. Además, se puede obtener la licencia de Voxelfill para usuarios de otros métodos de impresión 3D de la extrusión de materiales conforme a EP 4100235-B1.
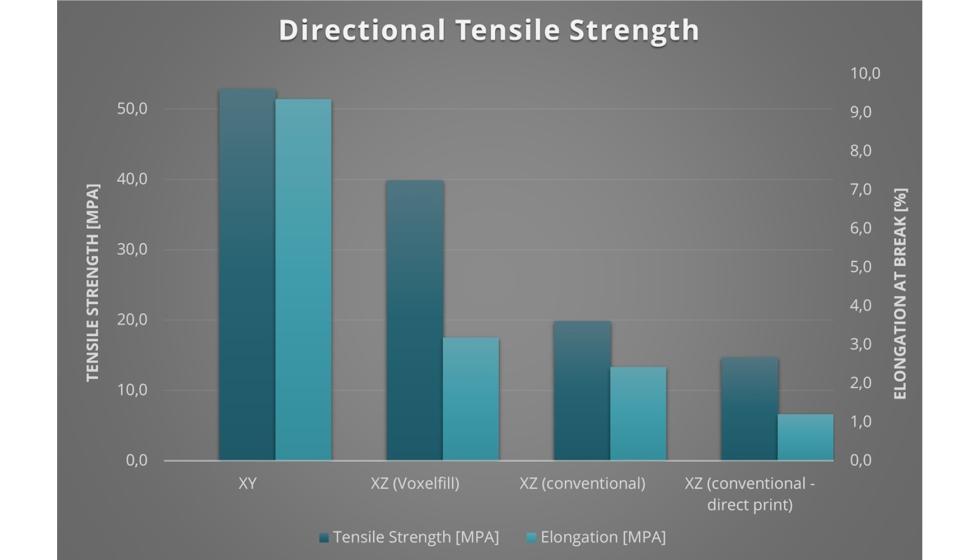
Comparativa de resistencias: En horizontal, en vertical (con Voxelfill) y en vertical (de forma convencional). Foto: AIM3D.
AIM3D lleva apostando desde 2017 de forma sistemática por las impresoras 3D de pellets, en contraste con las impresoras 3D FDM, que procesan granulado en lugar de filamentos. Una reducción considerable de los costes de material del granulado y el uso de material regenerado, procedente directamente del molino, constituyen la base de la alta rentabilidad de esta estrategia de fabricación AM con impresoras 3D de pellets. Clemens Lieberwirth, CTO de AIM3D explica: “Creemos más que nunca en nuestra tecnología CEM y en la eficacia probada del equipo de AIM3D. Las impresoras 3D de pellets ofrecen la posibilidad única de reproducir de forma muy rentable las características de los componentes fabricados de forma convencional mediante una estrategia de fabricación aditiva. Con la estrategia Voxelfill, la impresión 3D ahora alcanza resistencias similares a las del clásico moldeo por inyección”.
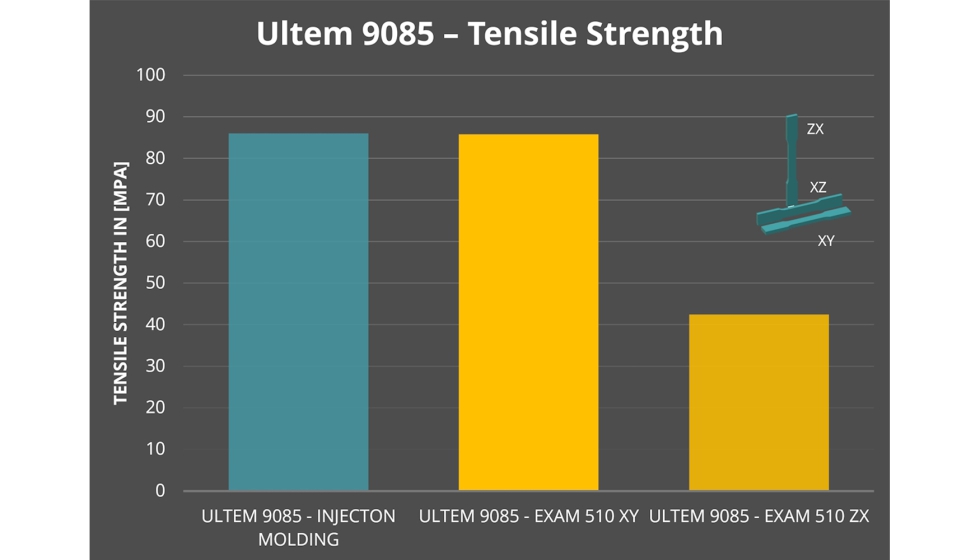
Ultem 9085: comparación de resistencias a la tracción en MPa (sin Voxelfill). Foto: AIM3D.
Innovador y disruptivo: el principio Voxelfill supera resistencias no homogéneas
En la fabricación de componentes por el proceso aditivo de polímeros, estos presentan unos valores de resistencia no homogéneos debido al proceso de adición por capas. Esto se manifiesta principalmente en forma de desventajas en cuanto a las resistencias a la tracción y a la flexión, así como en un comportamiento muy frágil a lo largo del eje Z. En cambio, las resistencias alcanzables a lo largo de los ejes X e Y de algunos procesos se acercan ya bastante a las resistencias de los procesos clásicos de moldeo por inyección. AIM3D ya lo demostró con la elaboración de componentes rellenos de fibra como PA6 GF30 y materiales puramente termoelásticos como Ultem 9085. Para ampliar el espectro de aplicación de los componentes 3D, es necesario solucionar de manera básica el fenómeno de las resistencias no homogéneas. Utilizando la tecnología de extrusión 3D del proceso CEM, AIM3D ha desarrollado una estrategia Voxelfill que supera estas limitaciones y aumenta la rentabilidad del proceso CEM. Voxelfill puede utilizarse además para producir piezas de varios materiales y, como norma general, es adecuado para los grupos de materiales plástico, metal y cerámica para la construcción de piezas 3D. Clemens Lieberwirth, CTO de AIM3D explica: “Con Voxelfill, el transformador tiene la oportunidad única de mejorar la resistencia Z y la velocidad de impresión. Por ello continuamos trabajando sistemáticamente en el perfeccionamiento de esta tecnología”.
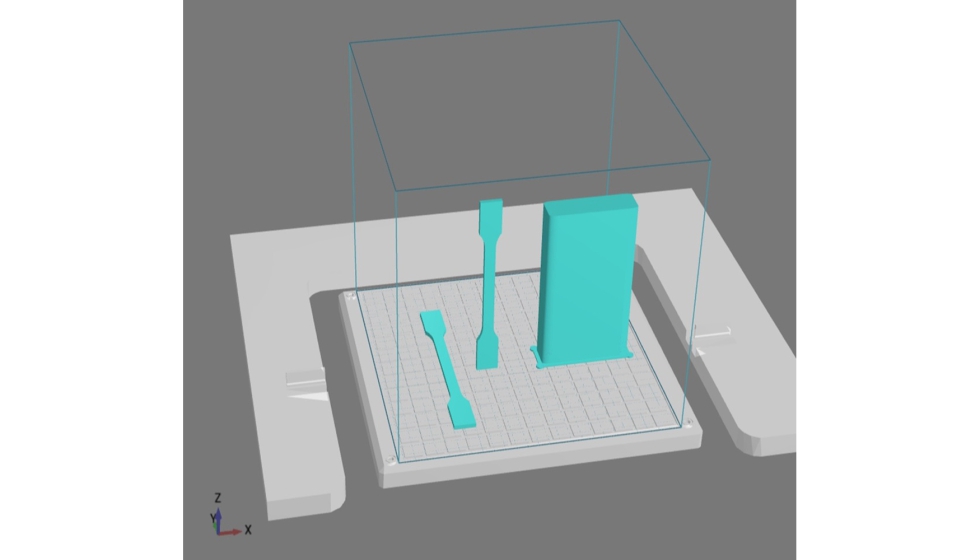
Estructura de los ensayos con Voxelfill: geometrías de barra de tracción para determinar la resistencia XY y la resistencia Z. Foto: AIM3D.
Descripción general de la estrategia Voxelfill
El objetivo del desarrollo de Voxelfill fue superar las resistencias no homogéneas en la impresión 3D. Actualmente la impresión 3D por extrusión de material alcanza, en función del material utilizado, cerca de un 50% de resistencia en dirección de la presión. Por ello, las capas impresas se rompen y las piezas solo pueden utilizarse generalmente para prototipos. Con Voxelfill, AIM3D ahora alcanza el 80% de resistencia en comparación con el método de moldeo por inyección ligado a un molde, por lo que permite la aplicación técnica de las piezas impresas en 3D con granulado certificado. El potencial al que se aspira es incluso del 100%. Voxelfill es una combinación de moldeo por inyección e impresión por extrusión 3D basada en el método CEM. Con Voxelfill se consiguen propiedades en el material casi isotrópicas en todas las direcciones de construcción, además de una mayor productividad y una orientación de las fibras en dirección Z. Clemens Lieberwirth, CTO de AIM 3D explica: “Voxelfill se convierte así en un punto de inflexión en el ámbito de las resistencias de las piezas 3D”.
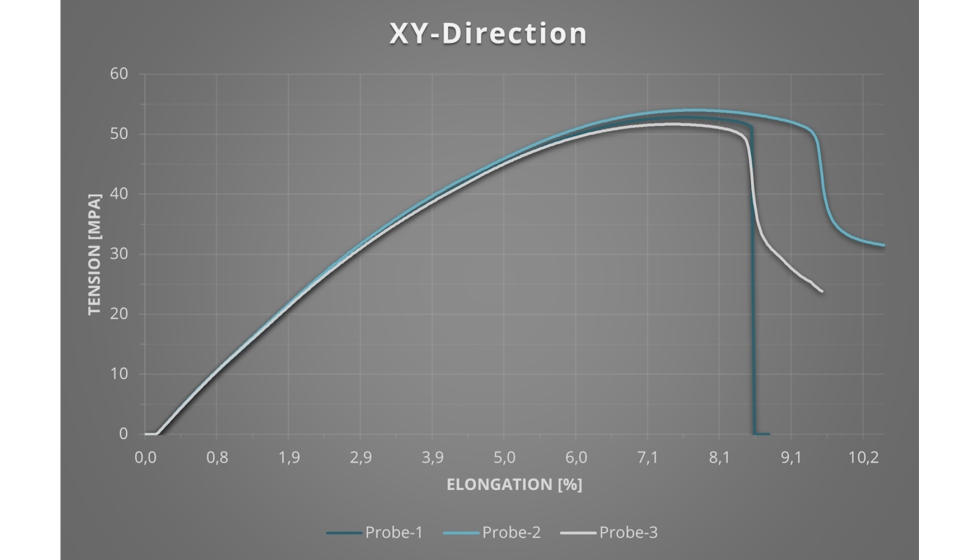
Referencia de Voxelfill con barras de tracción en horizontal en el plano XY con medición de la tensión (MPa) y la dilatación (%). Foto: AIM3D.
Implementación de las series de ensayos con Voxelfill
Con Voxelfill se alcanzan resistencias del 80% en el plano en comparación con el moldeo por inyección. Los primeros valores obtenidos son válidos para polímeros técnicos sin relleno. Esto da como resultado el doble de resistencia que la impresión 3D convencional con impresoras FDM. En el caso de los polímeros técnicos rellenos de fibras, el aumento previsto de la resistencia frente a la impresión 3D convencional con impresoras FDM es aún mayor. La serie de ensayos con Voxelfill se organizó con geometrías de barra de tracción para determinar la resistencia XY y la resistencia Z. La variante A reprodujo barras de tracción en posición horizontal con dirección de tracción en el plano XY. La variante B eran barras de tracción en posición vertical con dirección de tracción en el plano XZ. La variante C la formaba un bloque con dirección de tracción en el plano XZ tomando como base muestras fresadas. Durante el estudio de viabilidad de AIM3D se midieron la tensión (MPa) y la dilatación (%) para las variantes A a C (material Polycore PETG-1000 de Polymaker).
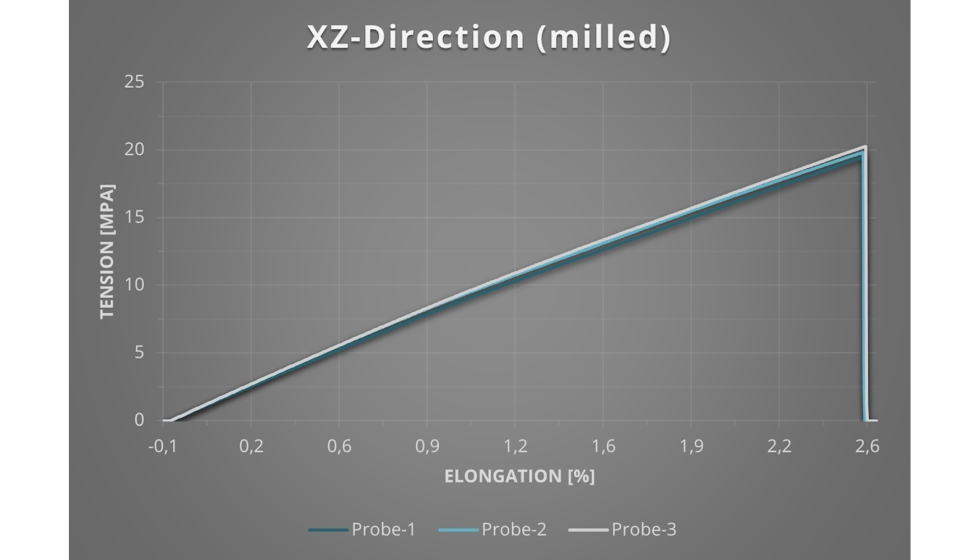
Referencia de Voxelfill con barras de tracción en vertical en el plano XZ con medición de la tensión (MPa) y la dilatación (%). Foto: AIM3D.
Análisis óptico de las muestras
A pesar de su elevada resistencia a la tracción, las muestras de Voxelfill aún presentaban poros, es decir, burbujas de aire de un tamaño <0,15 mm³. Por lo tanto, es posible una mayor resistencia a la tracción y, por ello, una mejor isotropía mediante una continua optimización. El potencial del método Voxelfill se amplía mediante el uso de polímeros rellenos de fibra.
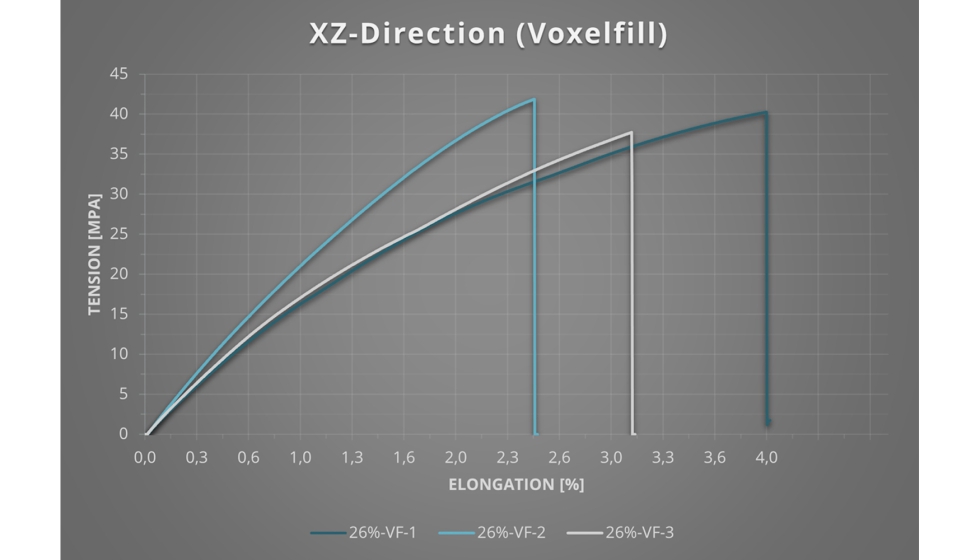
Referencia de Voxelfill con barras de tracción en vertical, fresadas, en el plano XZ con medición de la tensión (MPa) y la dilatación (%). Foto: AIM3D.
Conclusiones a partir de las series de ensayos efectuadas
Los resultados extraídos de los primeros ensayos demuestran el gran potencial de Voxelfill. Constituyen la ‘Proof of Concept’ de esta combinación de impresión 3D por extrusión de material y moldeo por inyección. Al observar los resultados de las muestras fabricadas mediante el método convencional de capa por capa (Layer by Layer), resulta evidente el punto débil de la anisotropía en las piezas de impresión 3D. Las muestras impresas con la orientación XY muestran una trayectoria dúctil tensión-dilatación, tal y como es típica de un plástico sin relleno. La resistencia a la tracción, de 52,83 MPa, se encuentra incluso ligeramente por encima del valor extraído de la ficha de datos del material (50 +/-1,1 MPa) para el moldeo por inyección. En comparación con las muestras convencionales impresas en dirección XZ, una vez directamente como barra de tracción en posición vertical y una vez en forma de bloque, para la posterior fabricación con arranque de viruta de las barras de tracción, aparecen discrepancias tanto en la resistencia a la tracción como en la desviación estándar. Esto se debe a la geometría tan desfavorable que tiene una barra de tracción en posición vertical para la impresión 3D por extrusión de material. Físicamente se explica de la siguiente manera: debido a la reducida superficie de apoyo sobre la base respecto a la altura excesiva en proporción, con una sección variable, las muestras están expuestas a vibraciones en caso de fabricación directa, lo que puede causar un desplazamiento de las bandas de material. Estas imprecisiones condicionadas por la geometría provocan un debilitamiento de la estructura del material, ya que influyen en la sección del material y se pueden producir muescas.
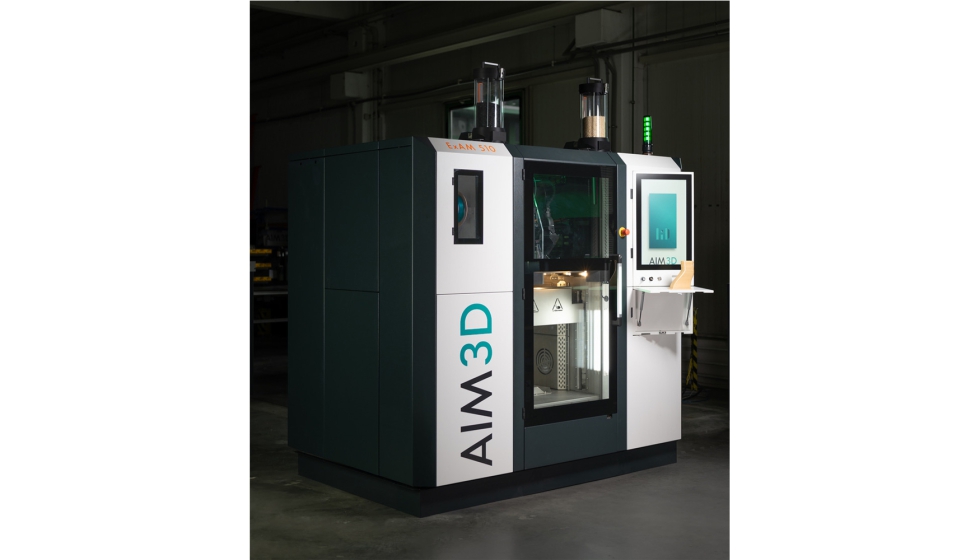
ExAM 510 con una velocidad de construcción máxima actualmente de 150 cm³/h. De cara al futuro, el fabricante aspira a alcanzar velocidades de construcción entre 300 y 600 cm³/h. Foto: AIM3D.
La alta desviación del estándar es un indicio probable de que, en este caso, un efecto estocástico, como la vibración de la barra de tracción, desempeña un papel importante. No obstante, un ensayo de tracción, es una prueba en la que no deberían observarse efectos causados por la geometría ni muescas. Por ello, para continuar observando la resistencia en dirección de impresión XZ se centró la atención en las muestras fresadas a partir de un bloque impreso en posición vertical. La posible fusión parcial de las capas posterior, causada por el mecanizado con arranque de viruta, se evitó mediante las herramientas y la refrigeración adecuadas. Es decir, si se comparan entonces las muestras impresas en dirección XZ de forma convencional, con las muestras de Voxelfill, se comprueba que la resistencia a la tracción se ha duplicado. Esta aumenta de 20 MPa en el caso de las muestras impresas de forma convencional a 40 MPa en las muestras de Voxelfill. En comparación, la resistencia de las muestras impresas horizontalmente fue de 53 MPa. Como resultado, se puede llegar a la siguiente conclusión: esto equivale a una anisotropía del 70% en las muestras impresas de forma convencional y una anisotropía de tan solo el 23% en la muestras de Voxelfill.

Comparativa de precios (precio por kg) de PA6 GF30, ULTEM 9085 y 316-L de la impresión 3D de pellets frente a la impresión FDM con filamentos. Foto: AIM3D.
Nuevas series de ensayos con materiales rellenos de fibras sorprenden por la mejora de su resistencia
La aplicación del proceso con Voxelfill en plásticos rellenos de fibras confirma la influencia positiva en la resistencia Z. Se llevaron a cabo ensayos con PETG GF30 de Polymaker a una temperatura de extrusión de 270 °C. Se organizó una serie de ensayos para determinar los parámetros óptimos de impresión para valorar la comparación con la máxima resistencia alcanzable, tanto en la impresión convencional como con Voxelfill. Se fabricaron barras de tracción en posición horizontal XY como referencia. Se imprimieron en dos orientaciones de relleno diferentes, una vez alineadas con la dirección de tracción y otra vez a +/-45° respecto a la dirección de tracción. La resistencia a la tracción fue la mayor en el caso del relleno alineado en dirección a la tracción: fue de aprox. 72,4 MPa. Esto corresponde a un caso con un diseño muy concreto, que no se daría en un caso real de una pieza moldeada por inyección, ya que la distribución de las fibras depende de la geometría de la pieza y del número y la orientación de los puntos de inyección. En comparación, las barras de tracción en posición horizontal con orientación de relleno de +/- 45° alcanzaron los 50,1 MPa. A continuación se imprimieron barras de tracción en posición vertical sin Voxelfill, con relleno por capas convencional (lo que equivale al estado de las impresoras 3D normales). Estas alcanzaron una resistencia a la tracción de 12,8 MPa. Las piezas sometidas a ensayo impresas mediante Voxelfill en posición vertical alcanzaron, en comparación, una resistencia superior de 40,7 MPa.
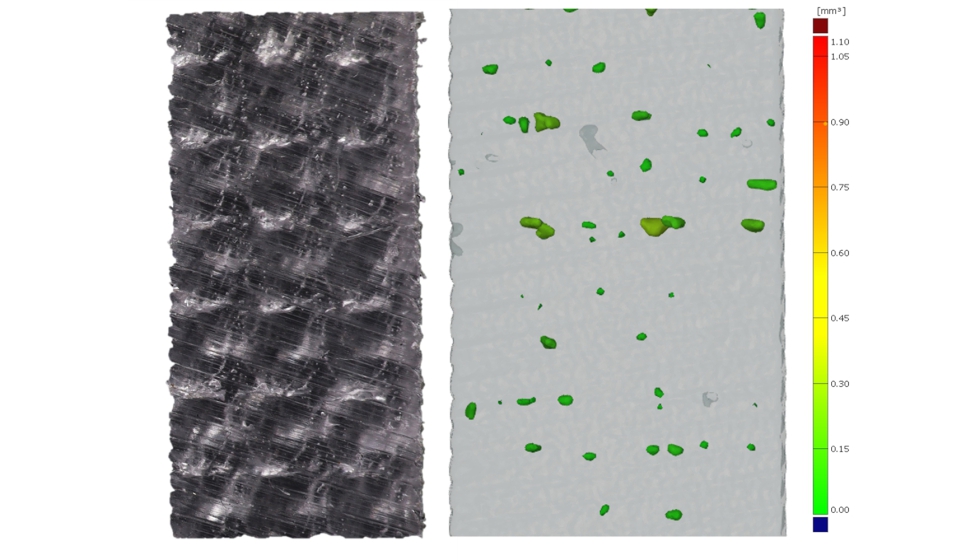
Análisis óptico de las muestras. Foto: AIM3D.
Conclusiones sobre la homogeneidad y la resistencia derivadas de las series de ensayos con materiales rellenos
Si se comparan entre sí los valores determinados para averiguar la homogeneidad de la resistencia, se comprueba que, en el caso de Voxelfill, la homogeneidad es del 81%, en comparación con las muestras de referencia impresas a +/-45° y del 56% con las muestras de referencia alineadas. En cambio, las barras de tracción impresas de forma convencional alcanzan solo un homogeneidad del 25%, en comparación con las muestras de referencia a +/-45° y del 18% con las muestras de referencia alineadas. Es decir, el efecto de aumento de la resistencia de Voxelfill, que produce características de mayor homogeneidad en las piezas en comparación con el moldeo por inyección, también se demostró en los plásticos rellenos de fibras (ver al respecto el diagrama comparativo con los diferentes valores de resistencia). Al observar la distribución de las fibras bajo el microscopio confocal, se pueden ver asimismo las fibras alineadas en dirección Z aportadas por el proceso de inyección vertical con Voxelfill. Clemens Lieberwirth, CTO de AIM3D explica: “Este efecto de la alineación de las fibras es exclusivo de Voxelfill y no se consigue con la impresión 3D por extrusión convencional por capas”.
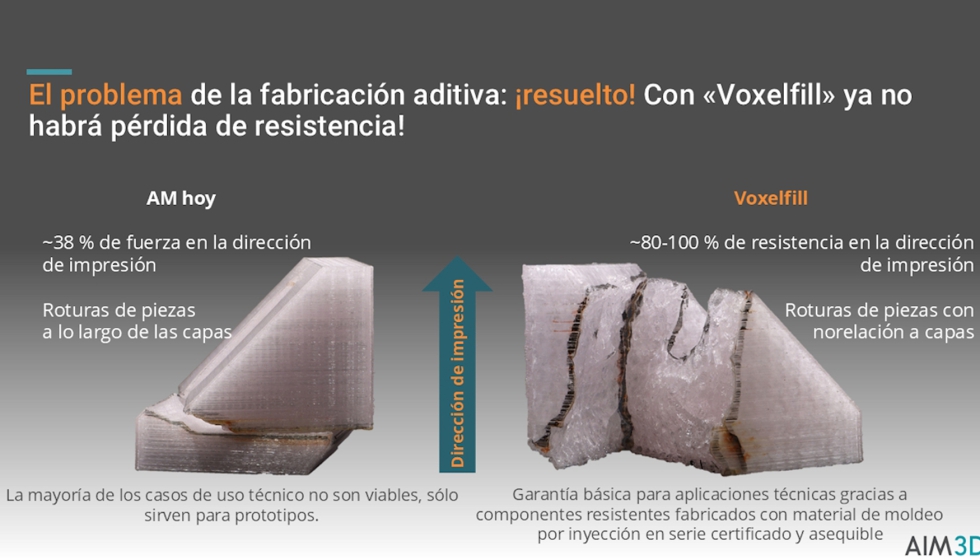
Comparación entre Voxelfill y la impresión 3D convencional con una escuadra impresa. Foto: AIM3D.
Mejora de la reproducibilidad de las aplicaciones de Ultem con una impresora 3D de pellets
La instalación ExAM 510 de AIM3D está prevista para el uso en la producción industrial. La instalación ExAM 510, presentada en el año 2022, funciona a una velocidad máxima de construcción actualmente de 150 cm³/h. De cara al futuro, según las afirmaciones del fabricante se aspira a alcanzar velocidades de construcción entre 300 y 600 cm³/h. Se pretenden alcanzar así volúmenes de procesamiento entre 1000 y 4000 kg al año (todos los datos se refieren a piezas con una calidad como máx. de 150 µm de grosor de capa y usando una boquilla de 0,4 mm en la impresora 3D, siendo así comparables a los componentes 3D del Fused Deposition Modeling (FDM)). Lo decisivo para la construcción de un componente 3D es, sobre todo, la reproducibilidad, es decir, la exactitud en la reproducción del proceso. Para el usuario, es el aspecto más importante para obtener una calidad uniforme en el componente, específicamente en la fabricación en serie de series pequeñas y medianas. Los componentes de la técnica de moldeo por inyección y los componentes 3D presentan valores de homogeneidad del material similares, ya que se utiliza Ultem 9085 en forma de granulado. Los últimos ensayos de tracción conforme a UNE-EN ISO 527-2, tipo 1A evidencian una gran estabilidad del proceso por las escasas desviaciones del estándar. Esta se consigue, sobre todo, gracias a la tecnología patentada de extrusora-granulado, que garantiza un procesado que protege el material y minimiza la degradación de los polímeros en la extrusora.
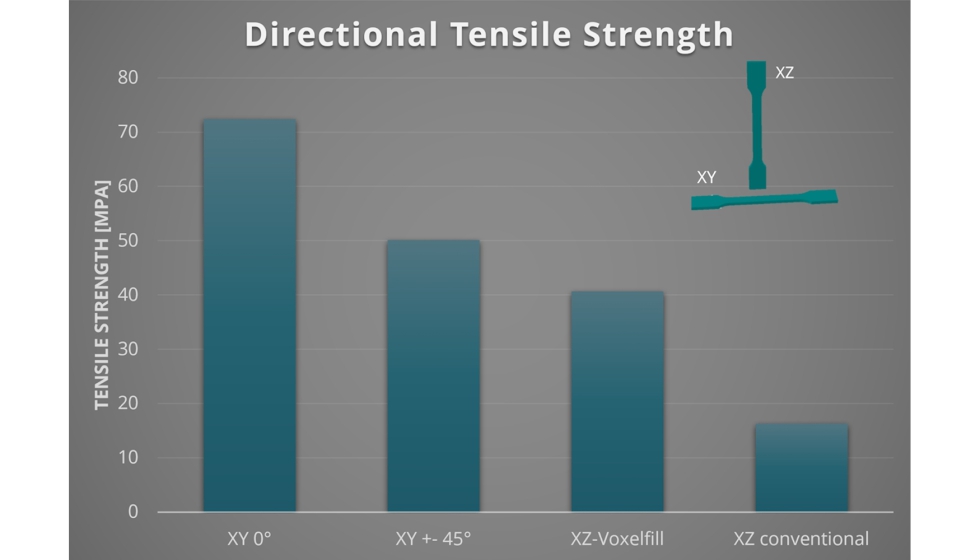
Comparativa de resistencias en plástico relleno de fibras: en horizontal 90°, en horizontal +7-45°, en vertical (con Voxelfill) y en vertical (de forma convencional). Foto: AIM3D.
La impresión 3D de pellets abre nuevos campos al versátil material PEI
Las impresoras 3D de pellets ExAM 255 y ExAM 510 de AIM3D permiten el uso de granulado estándar con o sin materiales de relleno para generar piezas 3D resistentes. El PEI es difícilmente inflamable conforme a UL 94-VO. El PEI es apto para el uso a altas temperaturas, es decir 180 °C, de forma continuada (217 °C hasta pasar a cristal). Con el material de PEI Sabic Ultem 9085, la impresión 3D de pellets abre nuevos campos a las propiedades de las piezas, que se asemejan a las que se consiguen con el clásico método de moldeo por inyección. Se obtiene así un alargamiento de rotura 100% superior que con las impresoras FDM. Por ello, el PEI abre nuevos campos de aplicación en la automoción, la ingeniería aeroespacial, los vehículos ferroviarios y la tecnología militar.
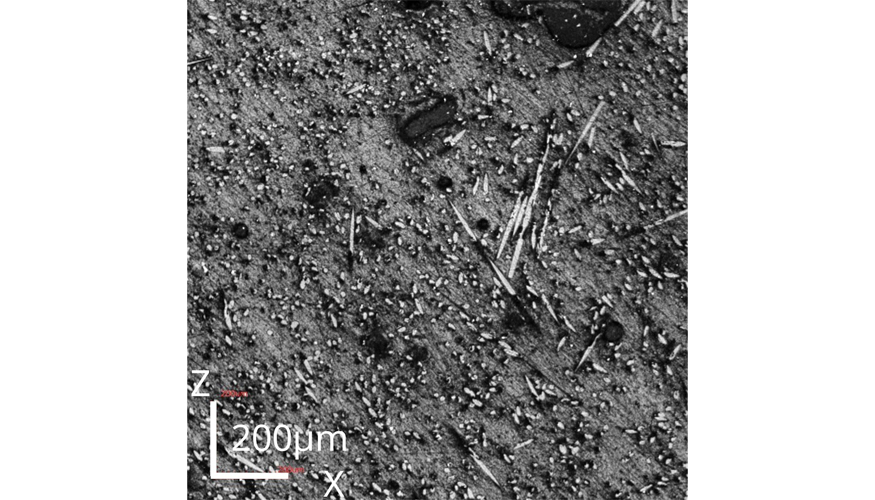
Observación bajo el microscopio confocal de una muestra impresa con Voxelfill en el plano XZ. Foto: AIM3D.
Perspectiva del potencial de Voxelfill
La estrategia Voxelfill permite, mediante procesos CEM, el uso de diferentes materiales: son posibles soluciones multimateriales híbridas con diferentes materiales de llenado de vóxeles y materiales de construcción para el contorno o la estructura de las paredes interiores. De ese modo pueden ‘personalizarse’ las propiedades de los materiales. Se pueden definir tridimensionalmente y adaptar a la aplicación tanto el peso de las piezas como las propiedades de amortiguación o las elasticidades, o bien manipular el centro de gravedad. Mediante el relleno selectivo de determinadas cámaras de volumen (densidades selectivas), sobre la base de simulaciones FE, podría influirse de manera selectiva en las propiedades de las piezas. Es decir, Voxelfill permite rellenar solo las zonas de un componente que son absolutamente necesarias para el flujo de fuerzas.
El resultado son unas piezas ‘clásicas’ en términos puramente visuales y con todas las ventajas para su tratamiento posterior. Con la particularidad de que la impresión 3D se lleva a cabo reduciendo el material y el peso, incluso hasta obtener piezas de construcción ligera. Especialmente cuando se utilizan materiales reforzados con fibras, el uso de Voxelfill ofrece la opción adicional de alinear las fibras en la pieza de manera selectiva con el fin de aumentar las propiedades mecánicas. El proceso CEM ya ofrece muy buenas posibilidades de controlar la orientación de las fibras en el plano. Con la estrategia Voxelfill, esta posibilidad se amplía al contorno y las paredes interiores de la pieza. Mediante la inyección del material en las cámaras de volumen (llenando de los vóxeles), el componente 3D recibe fibras que también están alineadas en el eje Z, mejorando así aún más las propiedades mecánicas. Clemens Lieberwirth, CTO de AIM3D explica: “El proceso Voxelfill resulta especialmente indicado para la impresión 3D de plásticos con y sin relleno de fibras, pero también se puede utilizar para la impresión 3D de piezas de metal y cerámica por el proceso CEM. En general, las ventajas se derivan de la mayor velocidad de construcción y del relleno que transciende las capas”.