Addipref: impresión 3D de preformas de fibra continua
Los composites de fibra continua aportan prestaciones mecánicas equiparables a los metales, pero mejores en libertad de diseño y peso. Hasta ahora, los costes de fabricación y las limitaciones geométricas han dificultado su extensión a sectores diferentes del aeroespacial y deporte – competición. Addipref es un proceso nuevo de Preformado Aditivo de composites de fibra continua que simplifica la fabricación y reducen los actuales costes.
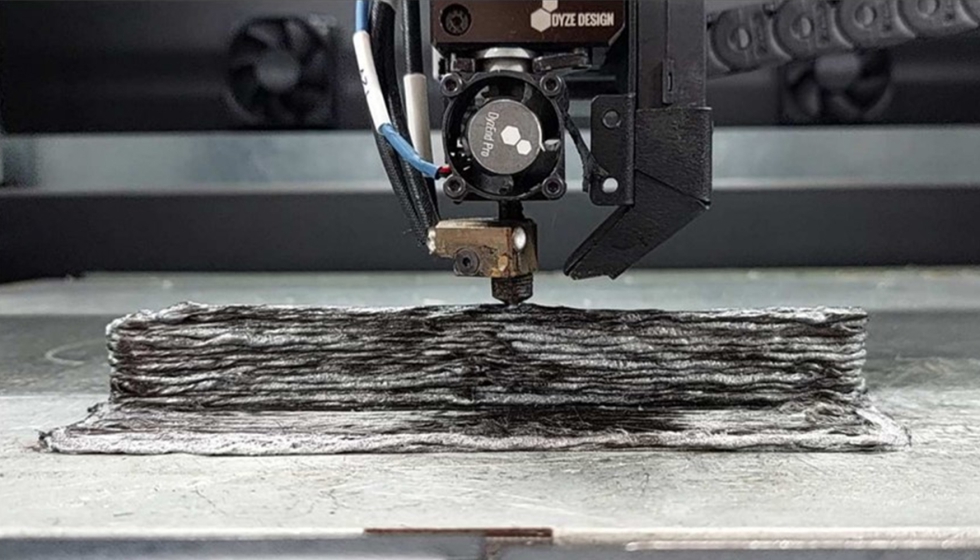
La fabricación aditiva de una preforma de fibra continua (de carbono, vidrio, aramida o textil) elimina las fases de un proceso de preformado convencional manual o automatizado (corte de telas, apilamiento y preformado) y minimiza las limitaciones de diseño. La preforma obtenida podrá impregnarse en resina mediante infusión o RTM si estamos fabricando un composite termoestable o conformarse en caliente si ha sido formulada para obtener un composite termoplástico.
Este artículo expone el contexto de mercado, así como los fundamentos de la tecnología desarrollada por Tecnalia e identifica sus potenciales campos de aplicación. También menciona los retos pendientes para escalarla y extender su uso a Sectores y tipologías de pieza diversas. Para ello se requerirá de la implicación multidisciplinar de toda la cadena de valor: materiales, fabricantes de equipamiento, desarrolladores de software, proveedores de componentes, usuarios finales e ingenierías.
Contexto de mercado
La fabricación aditiva de composites contempla dos familias principales de formatos de refuerzo:
- Los composites reforzados con fibra corta
- Los composites reforzados con fibra continua.
Los polímeros y resinas reforzados con fibra corta se procesan con las mismas tecnologías que los materiales no reforzados. Sin embargo, los procesos de impresión de fibra continua son específicos para este formato. En función de si la matriz plástica es termoplástica o termoestable (resinas fotocurables) existirán diferentes tipos de cabezales.
Existe igualmente tecnologías para fibra continua que no son estrictamente procesos de impresión, sino adaptaciones o miniaturización de procesos convencionales como el ATL y el Winding. En estos casos se pierden algunas de las capacidades que proporciona la impresión 3D (prescindir de moldes o mandriles, impresión de geometrías complejas, etc.).
Con respecto al producto impreso se ofrece:
- Impresión de la pieza final
- Impresión de un producto intermedio (pendiente de un postproceso de impregnación, consolidación o mecanizado).
Se considera que las propiedades mecánicas de un composite están directamente relacionadas con el contenido en fibra, compactación y porosidad de la pieza, Los procesos de impresión que no aplican presión (por ejemplo, con rodillos) no pueden proporcionar prestaciones mecánicas equiparables a las tecnologías convencionales. La incorporación de sistemas de compactación limita las geometrías que pueden obtenerse. Por ello, la estrategia de fabricar en modo aditivo solo la preforma permite:
- Optimizar la fase más costosa del proceso de moldeo de composites estructurales
- Obtener componentes con prestaciones mecánicas equivalentes a los procesos convencionales
- Aprovechar al máximo las posibilidades de complejidad geométrica.
El proceso de preformado de tejidos de refuerzo es la fase más costosa y limitante del moldeo de composites. La contribución al coste final de este preproceso limita la extensión en el uso de los composites. Por ello, la automatización es una tendencia permanente en este sector. El preformado aditivo integra automatización y digitalización en un único proceso. Adicionalmente, alguna de las tecnologías aditivas en desarrollo, posibilita maximizar la optimización topológica y la complejidad geométricas de las piezas. Todo ello genera un gran potencial de mejora competitiva procedente tanto desde los costes y del valor aportado (nuevas y mejores prestaciones) como de los posibles nuevos modelos de negocio (personalización, fabricación in-situ, etc.)
Desde que en 2013 Markforged introdujo en el mercado la primera impresora 3D capaz de imprimir estructuras basadas en polímero con fibra larga continua, el desarrollo ha sido continuo, y las formas de llevar a cabo esa integración e impresión, variadas. En la última edición de la Feria JEC de Paris hubo comenzaron a tener presencia las tecnologías de impresión de fibra continua. Organizaciones como Orbital, 9TLabs, Fraunhofer - ICT, Tecnalia o IMT - Institut Mines Télécom presentaron desarrollos en diferentes niveles de madurez orientados a la fabricación aditiva de piezas finales o intermedias.
Diferencias entre el preformado convencional y el aditivo
Los procesos de moldeo de composites vía líquida como la infusión, el RTM o el HPRTM aplican un alto porcentaje de fibra obtenido mediante la utilización de preformas como estado intermedio, previo al proceso final de fabricación. Estos procesos consisten en la colocación del refuerzo dentro de un molde cerrado, seguido de la introducción de resina liquida que impregne adecuadamente esas fibras. La preforma tiene la misma geometría que la pieza final. Está formada por capas de tejido de refuerzo compactadas en el molde bajo presión para obtener el porcentaje de fibra requerido por la función de la pieza.
En la figura siguiente se representa la diferencia entre el moldeo convencionales y el que aplica preformado aditivo.
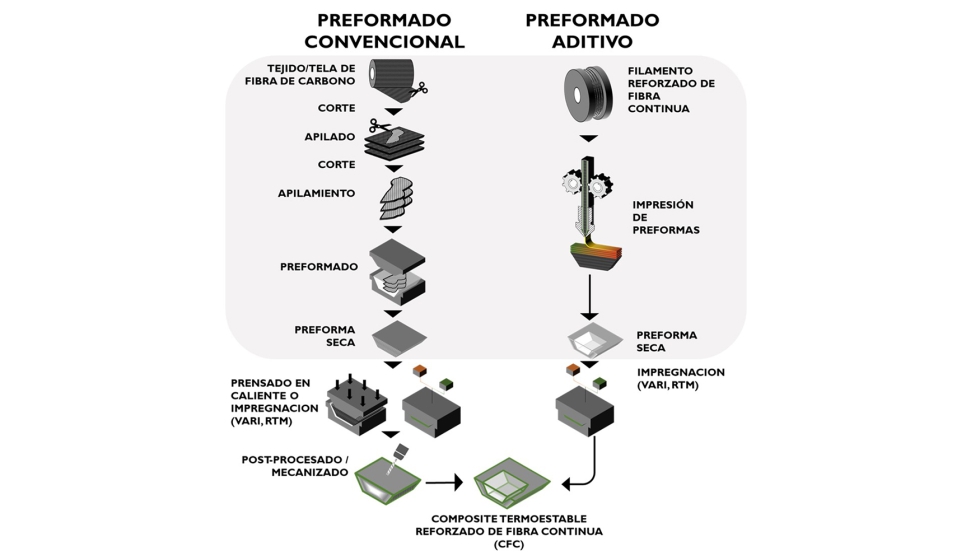
Tecnalia ha desarrollado la fabricación de preformas mediante la impresión de filamentos formados por fibra de refuerzo continua (CF), recubiertos de polímero termoplástico, utilizando la tecnología aditiva de FDM adaptada. Esta tecnología se basa en la extrusión del material a través de una boquilla, y su posterior deposición en capas sucesivas. La composición y configuración de los filamentos debe de permitir:
- Su imprimibilidad
- La impregnación de la fibra de refuerzo con la resina
- El mantenimiento de propiedades mecánicas del composite final o la mejora de alguna de ellas.
Para cumplir estos requisitos, ha sido necesario:
- Minimizar el % de binder o recubrimiento plástico que posibilita la impresión
- Configurar el roving de forma que se asegure su posterior mojabilidad con la resina
- Seleccionar las combinaciones binder – resina que no perjudique las propiedades mecánicas del composite obtenido
- Adaptar el equipamiento y el software a las nuevas exigencias requeridas por los filamentos constituidos fundamentalmente por fibra continua.
La figura inferior representa algunas de las diferentes configuraciones de filamento y boquilla que presenta la tecnología FDM y que determinan el proceso de impresión. Existen otras variantes en función de si el embebido de la fibra en el polimero es in-situ o no, pero la estrategia de impresión no varía.
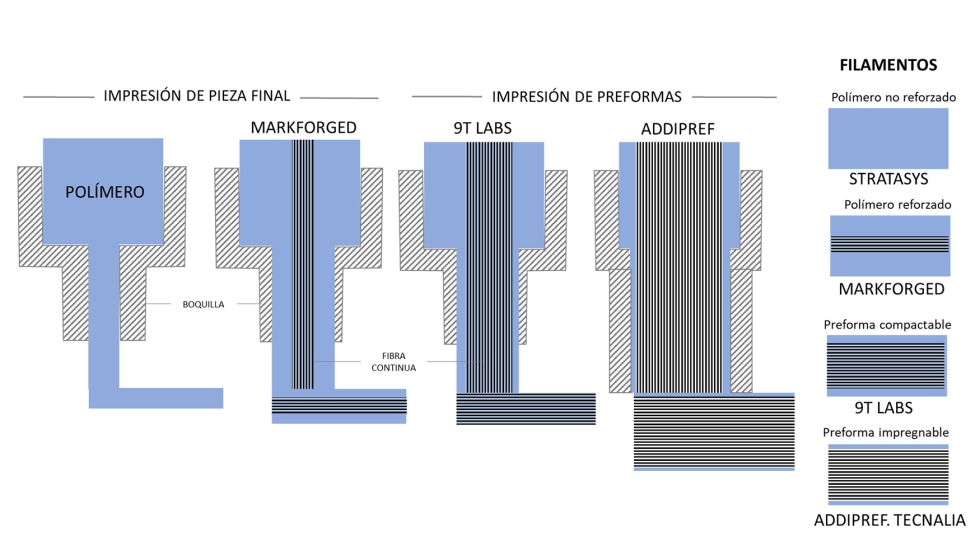
La impresión de preformas impregnables requiere de modificaciones importantes tanto el software como en el hardware. Los requerimientos de post-procesado (impregnación) propios de los procesos de infusión o RTM son también críticos.
La fabricación de preformas mediante tecnología FDM ha supuesto dos retos tecnológicos importantes. El primero, el desarrollo de este tipo de filamentos mediante procesos convencionales de extrusión y el segundo, la puesta a punto de la propia tecnología de FDM para su impresión.
Addipref ha requerido el desarrollo y puesta en marcha de 4 líneas tecnológicas:
- Desarrollo de filamentos de fibra continua por extrusión
- Puesta a punto de la tecnología aditiva FDM de los filamentos de fibra continua
- Selección de la mezcla matriz termoestable-aglomerante termoplástico
- Impresión de preformas impregnables.
Desarrollo de filamentos
Mediante procesos convencionales de extrusión, optimizados para la industria del cableado eléctrico, se ha desarrollado este tipo de filamentos, donde los hilos de cobre han sido sustituidos por hilos de carbono o vidrio, y donde el recubrimiento se selecciona en función de la matriz que se vaya a utilizar en la fabricación del componente de composite. EL objetivo es que la matriz, generalmente resina epoxi, disuelva el recubrimiento de los filamentos dejando el refuerzo (carbono o vidrio) desnudo para ser impregnado adecuadamente por la resina y así obtener esa pieza final con el porcentaje adecuado de fibra.
Los filamentos desarrollados tienen un diámetro total de 1,75 mm, formados por un núcleo de carbono o vidrio recubiertos de un polímero termoplástico, donde el porcentaje de refuerzo alcanza el 70% en peso. La función de ese recubrimiento es exclusivamente la de vehículo para poder imprimir esos hilos de refuerzo, por eso la cantidad debe ser la justa para ello. Policarbonato, poliuretanos termoplásticos y fenoxi han sido algunos de los materiales utilizados como recubrimiento debido a su solubilidad en resina epoxi.
Campos de aplicación
La tecnología Addipref se orienta, preliminarmente, hacia los campos de aplicación siguientes: isogrids, preformas impregnables (Infusión, RTM), preformas de consolidado en caliente (Organosheets 3D), nervaduras, refuerzos localizados para sobremoldear por inyección, preformas de composite C-C, parches de reparación, tirantes, liners, preformas 3D (Bulk), piezas auto-infusionables (sin necesidad de molde) y circuitos termo-resistivos.

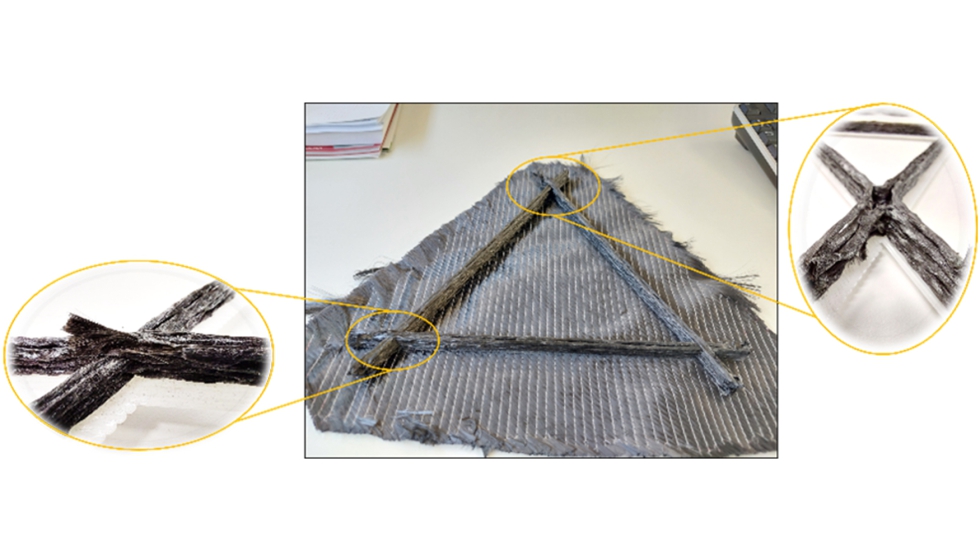
Estructuras nervadas.
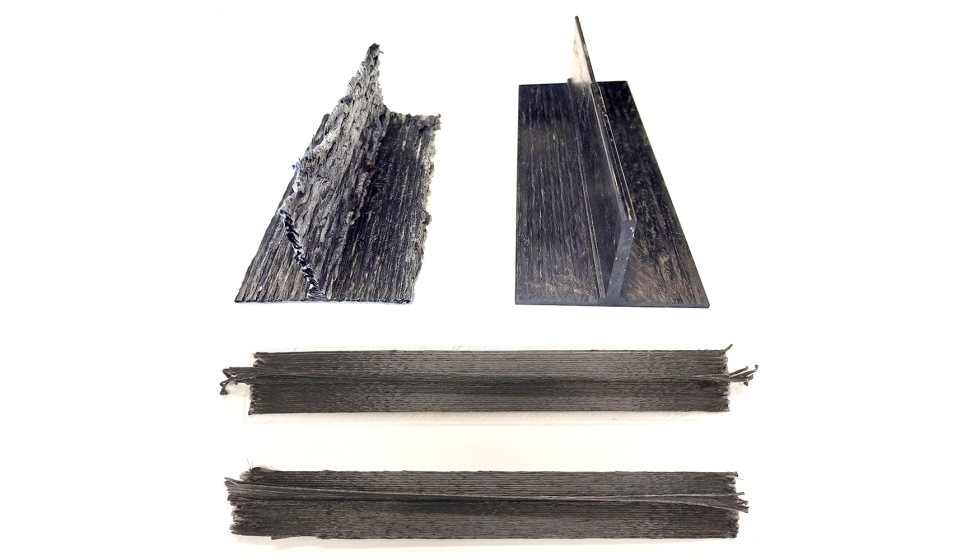
Preforma y pieza final obtenida.
Conclusiones
Del desarrollo abordado hasta el momento se puede concluir:
- Mediante un proceso de extrusión convencional adaptado, es posible obtener filamentos formados por fibra continua recubierta de material polimérico con alto contenido en fibra imprimibles mediante tecnología FDM. Este método es novedoso en el ámbito de la fabricación aditiva de fibra continua, y añade una opción más a las tecnologías ya identificadas.
- La impresión mediante FDM de estos filamentos fibra continua/polímero es posible fabricar “preformas” que permitirán fabricar componentes de composites con formas complejas, imposibles de fabricar mediante otros procesos.
- El preformado aditivo maximiza la optimización topológica de las piezas y con ello su peso.
- El escalado de este proceso de impresión mediante la sustitución del equipo de impresión cartesiano utilizado por un robot al que se implementará un cabezal de extrusión, permitirá además de la fabricación de componentes complejos, la fabricación de componentes de gran tamaño.
- El proceso de fabricación de preformas mediante tecnología FDM ofrece una ventaja económica en comparación con el proceso convencional de compresión.
Los retos futuros de este proceso aditivo de fabricación de preformas está orientado a:
- Optimizar la fabricación de filamentos identificando el recubrimiento más compatible con la resina de procesado posterior, y ajustar la relación fibra de carbono continua/polímero para garantizar la mejor mojabilidad y menor interferencia posible en el proceso posterior de moldeo de composites.
- Desarrollar herramientas (software y hardware) capaces garantizar la robustez del proceso de impresión.
- Establecer los parámetros y condiciones de impregnación adecuadas (RTM o infusiona) para asegurar los requerimientos de contenido de refuerzo y porosidad máxima.
- Extender esta Tecnología a la fabricación de preformas 3D consolidables mediante presión y temperatura para obtener composites termoplásticos.
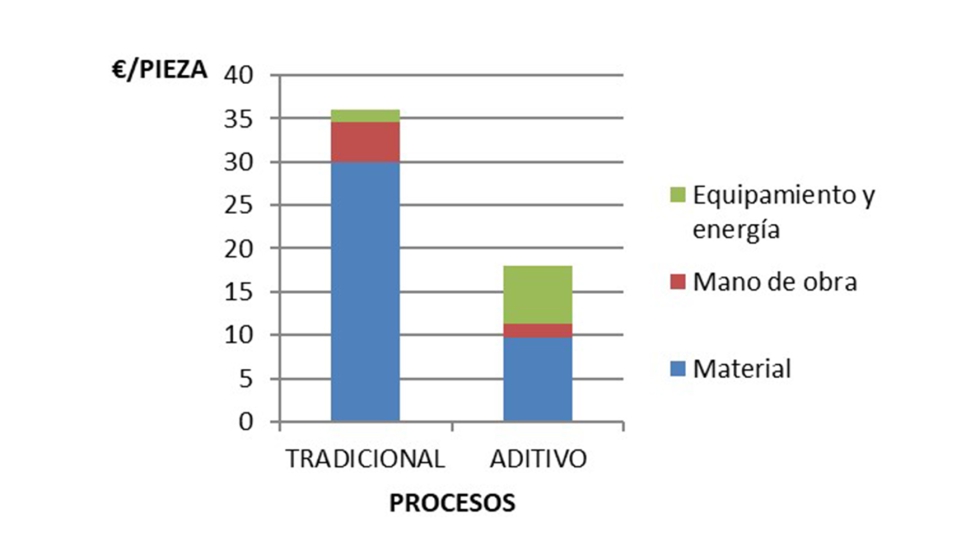
Análisis comparativo de costes de preformado para una pieza de 500 mm x 500 mm, de geometría compleja, 600 g de fibra de carbono y un tamaño de serie de 2.000 unidades (sector automoción o deporte – ocio).