Integración funcional: impresión 3D de una herramienta de moldeo por inyección de metal (MIM) con refrigeración cercana al contorno
La Cátedra de Microfluidos de la Universidad de Rostock colabora con Stenzel MIM Technik GmbH (Tiefenbronn, cerca de Pforzheim) en un proyecto para imprimir una herramienta 3D de moldeo por inyección de metal (MIM). La base del desarrollo es el uso de la tecnología CEM de AIM3D con un sistema ExAM 255. El sistema ExAM 255 combina una gran precisión de los componentes 3D con altas velocidades de construcción para la fabricación aditiva (AM). En comparación con un enfoque convencional de mecanizado, el uso de un proceso de AM para producir una herramienta MIM reduce el tiempo total de producción de unas 8 semanas a aproximadamente 5 días.
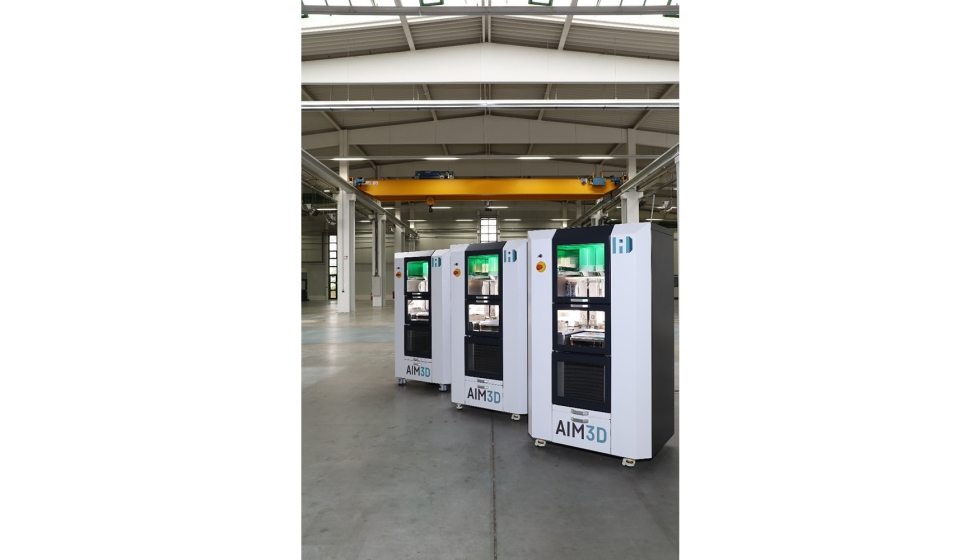
Impresora 3D multimaterial ExAM 255. Foto: AIM3D.
Como parte de un proyecto financiado por el Ministerio Federal Alemán de Economía y Energía (BMWi), la herramienta MIM impresa en 3D es un desarrollo cooperativo entre la Cátedra de Microfluídica (LFM) de la Universidad de Rostock y Stenzel MIM Technik GmbH. La duración del proyecto es de abril de 2021 a octubre de 2023. La base del proceso y la aplicación es el uso de la tecnología CEM de AIM3D, implementada en un sistema ExAM 255. El proyecto representa el estado actual de la técnica en impresión 3D de metales.
Herramienta 3D con refrigeración próxima al contorno para moldeo por inyección de metal (MIM)
El objetivo del proyecto conjunto entre la Universidad de Rostock y Stenzel MIM Technik era utilizar la impresión 3D para fabricar una herramienta para el moldeo por inyección de metales con refrigeración próxima al contorno. En la impresión 3D, la refrigeración próxima al contorno puede incorporarse como una integración funcional con canales helicoidales directamente en la herramienta. En otras palabras, no está incrustada como entradas, como ocurre con las herramientas de mayor tamaño. El objetivo de cualquier refrigeración próxima al contorno de moldes de inyección de metales o polímeros es reducir significativamente el tiempo de ciclo. El principio de la refrigeración próxima al contorno consiste en guiar los fluidos refrigerantes a través de canales de refrigeración próximos al contorno con secciones transversales bajas. Enfrían el componente ya durante el ciclo. De este modo se acelera el proceso de desmoldeo, lo que acorta considerablemente el ciclo.
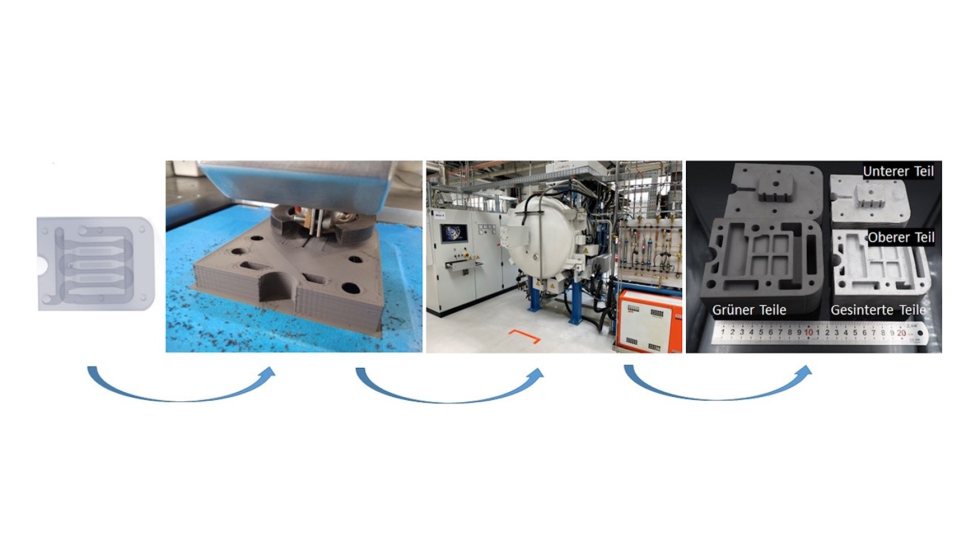
Cadena de producción de una herramienta MIM. Foto: AIM3D.
La compleja geometría de los canales de refrigeración helicoidales se crea con ayuda de la tecnología CAD utilizando modelos de simulación basados en las “necesidades” del componente. La experiencia a largo plazo muestra una reducción del tiempo de ciclo de alrededor del 20%, en función del grosor y el tamaño de la pared.
Como solución de componente integrado, la impresión en 3D ofrece la ventaja de una “técnica de una sola vez“como integración funcional en comparación con los procesos con molde. El ejemplo de aplicación demuestra, por tanto, una oportunidad para reducir drásticamente el”tiempo de comercialización”. El objetivo del proyecto de cooperación es desarrollar una nueva cadena de procesos para la producción rentable y rápida de herramientas MIM. Hasta ahora, se necesitaban plazos de hasta ocho semanas para producir un molde de inyección metálica convencional. Con la impresión 3D de metales, el tiempo de suministro de una herramienta MIM puede reducirse a unos cinco días.
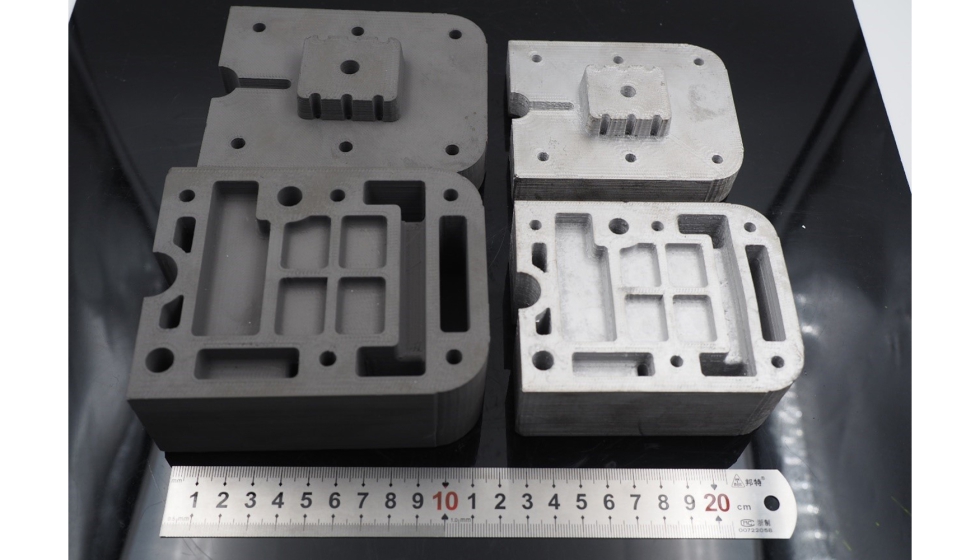
Herramienta MIM producida con el proceso CEM. Foto: AIM3D.
Detalles del desarrollo de la herramienta en la Universidad de Rostock
Como parte de la cooperación, se desarrolló inicialmente un modelo 3D optimizado de la herramienta utilizando herramientas CAD y de simulación. A continuación, estos datos se transfirieron al sistema CEM ExAM 255, junto con los parámetros de proceso necesarios. A continuación, se imprime en 3D la denominada “pieza verde”. A continuación, la pieza se sinteriza en un proceso de varias etapas para obtener las propiedades finales del material.
Con este proceso se pueden fabricar rápidamente componentes metálicos complejos tras los pasos necesarios de desbobinado y sinterización. Al mismo tiempo, el proceso CEM permite controlar la contracción volumétrica asociada a la sinterización. El molde resultante tiene una cavidad. El componente consiste en una pieza de pared gruesa con aletas finas. Estas aletas no pueden fabricarse sin refrigeración próxima al contorno, ya que son difíciles de desmoldar. Stenzel MIM Technik espera conseguir una reducción significativa del tiempo de ciclo para este componente de hasta un 70-80%. No obstante, aún están pendientes los ensayos de moldeo por inyección para las pruebas.
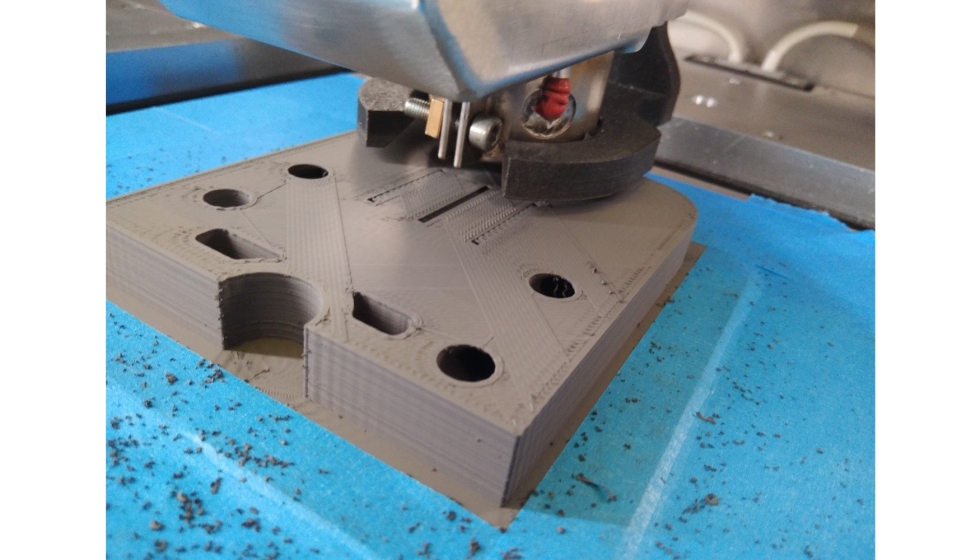
Producción de una herramienta 3D para el moldeo por inyección de metal en una ExAM 255. Foto: AIM3D.
Diversidad de materiales con la ExAM 255
La impresora 3D multimaterial ExAM 255 puede utilizarse con distintos materiales (metales, plásticos, cerámica) y con diversos procesos (componentes híbridos). En comparación con los procesos de lecho de polvo o incluso con otros procesos de impresión 3D que utilizan filamentos, los sistemas que utilizan el proceso CEM alcanzan resistencias a la tracción que se acercan al clásico moldeo por inyección termoplástico unido a molde. La ventaja de precio de la impresión 3D es especialmente llamativa cuando se utilizan granulados disponibles en el mercado en lugar de filamentos. Cuando se utilizan granulados, el proceso CEM supone un ahorro de costes de hasta 10 veces.
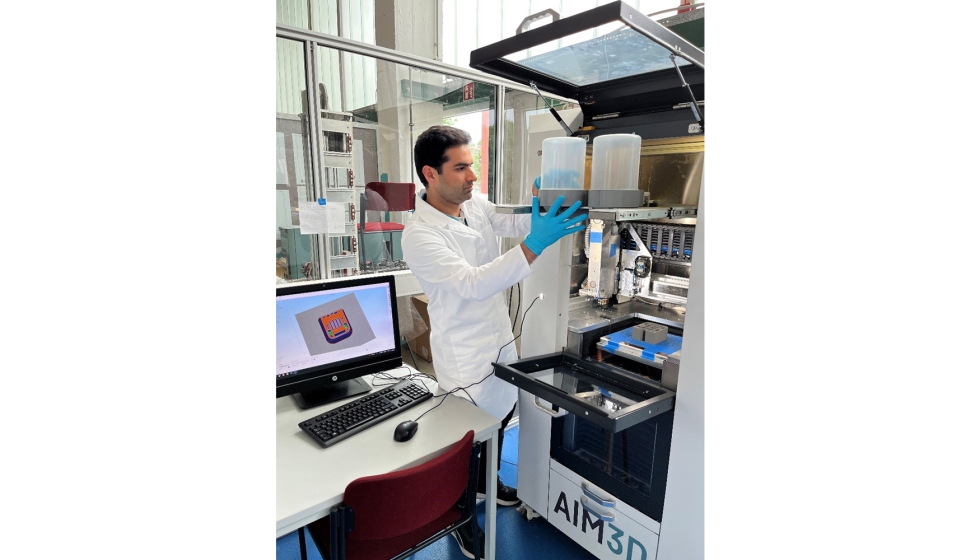
Abdullah Riaz, director del proyecto y miembro de la Cátedra de Microfluidos de la Universidad de Rostock (LFM): “Con el proceso CEM pueden reducirse tanto los costes de material como los de las máquinas, al tiempo que se evitan los problemas de la fabricación aditiva en lo que respecta a las tensiones residuales y los ajustes de material en máquinas individuales. Esta innovadora solución permite fabricar herramientas entre 4 y 8 veces más rápido y, al mismo tiempo, de forma más rentable”. Foto: AIM3D.