Impresión 3D de filamento fundido (FFF) en metal
Aunque los procesos convencionales de impresión 3D en metal no están maduros para su adopción masiva, los nuevos —como la fabricación con filamento fundido en metal (metal FFF)— son accesibles, asequibles y fáciles de usar. Diversos sectores, desde el de automoción hasta el aeroespacial, han aprovechado esta tecnología adaptable para producir innumerables piezas funcionales. La tecnología de impresión FFF en metal se basa en la tecnología MIM (Metal Injection Molding) y se trata de un proceso de tres pasos: Markforged ha creado un sistema holístico para lograr que el proceso sea simple y accesible a cualquier empresa. Este documento técnico profundiza en el proceso de impresión 3D FFF en metal, examina el enfoque específico de Markforged y detalla las principales consideraciones a tener cuenta al adoptarla.
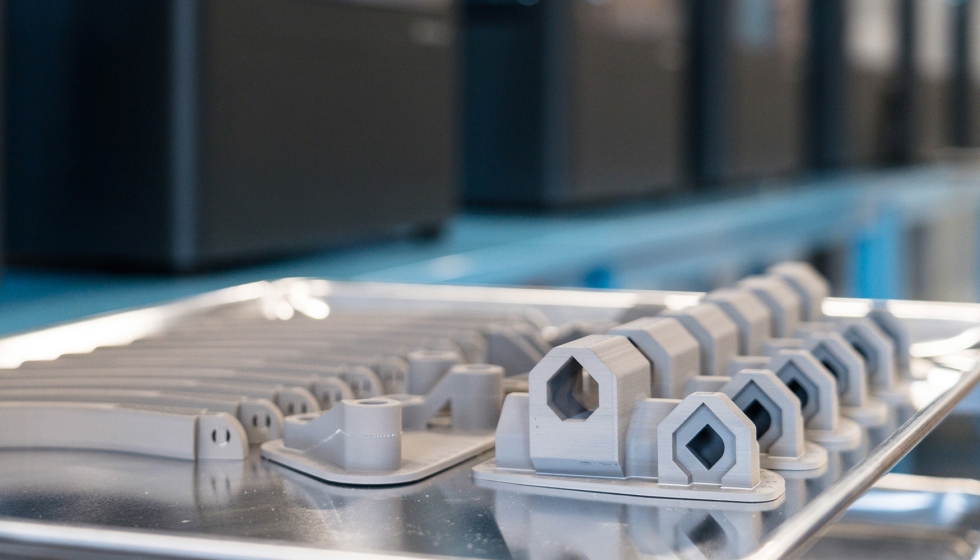
Impresión FFF en metal
Una impresora 3D de tecnología FFF en metal es un equipo altamente especializado y optimizado para imprimir en medios MIM. La impresora no imprime piezas metálicas acabadas, sino piezas en “verde”, que luego hay que desaglomerar y sinterizar. Siempre se aumenta la escala de las piezas en “verde” del 15 al 20% teniendo en cuenta las dimensiones de las piezas finales para compensar la reducción repetible y predecible durante la sinterización.
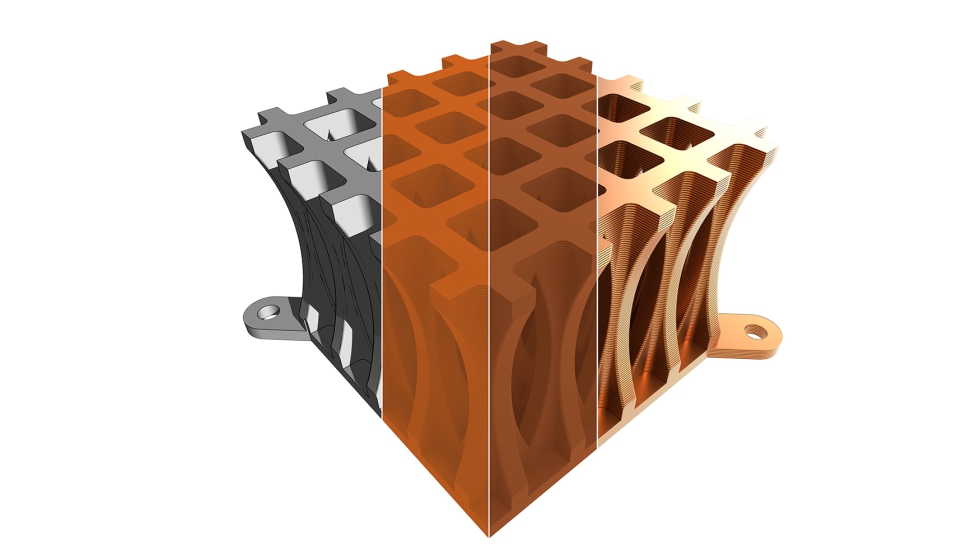
Proceso de impresión en tres pasos
Impresión
La pieza se imprime capa a capa depositando polvo metálico con aglutinante plástico. Se aumenta la escala de las piezas para compensar la reducción durante el proceso de sinterización. Las piezas resultantes se conocen como piezas en “verde”.
Desaglomerado
Después de imprimir, las piezas en “verde” pasan al proceso de desaglomerado que disuelve la mayor parte del aglutinante usando un disolvente orgánico. Una vez lavadas, se conocen como piezas en “marrón”.
Sinterización
Las piezas en “marrón” lavadas se colocan en un horno, donde se calientan con un perfil apropiado para cada material; primero, para eliminar los restos de aglutinante y, a continuación, para solidificar el polvo metálico y convertirlo en una pieza acabada.
Un proceso familiar
Una impresora 3D FFF en metal utiliza un proceso casi idéntico al de las impresoras FFF convencionales, con la excepción de que usa una hoja de impresión sellada al vacío en lugar de un lecho de impresión convencional. Los pasos que sigue el usuario son los siguientes:
- Laminar las piezas en una plataforma de software
- Colocar una hoja de impresión sellada al vacío en el lecho de impresión
- Comenzar el proceso de impresión
- Extraer la pieza impresa de la impresora una vez liberado el vacío
- Desprender la pieza en “verde” de la hoja de impresión.
Extrusión dual optimizada con materia prima MIM
Las máquinas de extrusión dual son habituales en la impresión 3D. Sin embargo, la impresora FFF en metal se ha optimizado de una manera diferente: filamento MIM en una boquilla y filamento de interfaz cerámica en la otra.
Una boquilla de extrusión está diseñada para imprimir materia prima MIM, que es polvo metálico en un material aglutinante plástico de dos partes. Este material forma la pieza en sí misma, así como los soportes y la malla encargada de desprender la hoja de impresión. Markforged ofrece en la actualidad seis materiales diferentes de grado comercial: acero inoxidable 17-4 PH, acero H13, A2 y D2 para herramientas, cobre e Inconel.
La otra boquilla imprime material cerámico, que provee la superficie/interfaz entre la pieza y el soporte/malla. Además, es importante observar lo esencial que resulta el material de soporte para el proceso. Sin un material de soporte, las piezas que lo requieren no podrían imprimirse. El proceso de sinterización convierte este material en polvo, lo cual permite que la pieza se separe con facilidad de los soportes.
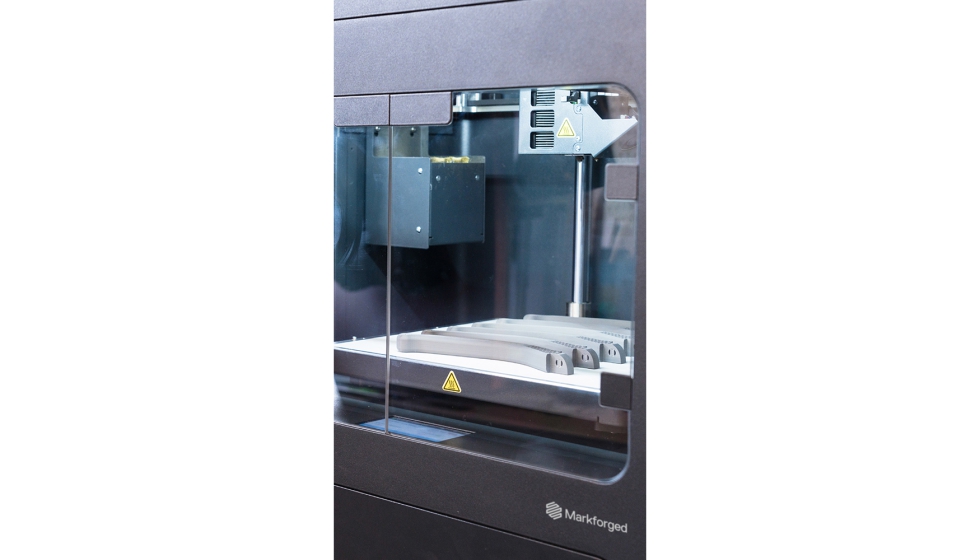
Tamaño y relleno de la pieza
Las piezas ideales para impresión FFF en metal son las que tienen desde el tamaño de una uña hasta el de un puño, pero pueden imprimirse piezas más grandes. Las piezas impresas con tecnología FFF en metal suelen ser mucho más grandes que las piezas MIM, que son extremadamente pequeñas. El proceso de impresión de FFF en metal está optimizado para las piezas MIM pequeñas, por lo que el tiempo de lavado será exponencialmente mayor cuanto más grandes sean las piezas.
Cuando las piezas sólidas exceden cierto grosor, el tiempo de lavado puede ser extremadamente largo.
La mayoría de las piezas impresas con tecnología FFF en metal utilizan relleno de celda cerrada. Si bien es posible imprimir piezas sólidas, hacerlo implica la aparición de complejidades y restricciones.
Desaglomerado FFF en metal
En el paso de desaglomerado se elimina la mayor parte del aglutinante y se produce una pieza en “marrón” lista para sinterizar. La pieza en “verde” se coloca primero en una estación de lavado para bañarla en un disolvente caliente, usándose una solución desengrasante para disolver el material aglutinante principal. Las máquinas con tecnología FFF de Markforged para impresión 3D en metal utilizan Wash-1, una solución separadora a base de disolventes. Se usa sobre todo el líquido Opteon SD-79 como disolvente, un producto que ofrece una capacidad de lavado superior, alta eficiencia y que es seguro ambientalmente.
Uso del sistema de desaglomerado FFF en metal
La màquina se separación FFF en metal es muy sencilla de usar y requiere solo equipos básicos de protección individual (es decir, gafas de seguridad y guantes de película laminada).
Los pasos a seguir por el usuario son los siguientes:
- Agregar piezas en “verde” a una cesta de lavado, sumergirlas en la máquina con el disolvente y cerrar la tapa
- Abrir la tapa, después de un tiempo de lavado determinado, y extraer las piezas de la cesta de lavado
- Colocar las piezas en una cámara de secado al aire, en la estación de lavado
- Extraer las piezas de la estación de lavado no bien se secan.
Y, ¿qué sucede con una pieza durante el lavado? El baño en el disolvente de separación diluye el material aglutinante principal de la pieza verde. A medida que se disuelve el aglutinante, el disolvente crea surcos microscópicos en la pieza para que el disolvente fluya a mayor profundidad y disuelva más.
Consideraciones sobre la separación FFF en metal
En esta sección se abordan aspectos relativos al grosor de las piezas, al relleno sólido en comparación con el relleno de celda cerrada, y cuestiones de seguridad y de salud ambiental.
Grosor de la pieza: el tiempo de lavado se correlaciona con el grosor máximo de la pieza, no con su tamaño ni con su peso. Para determinar el grosor, se utiliza el método del círculo inscrito, que establece la esfera del diámetro más grande que podría caber dentro de los límites de la pieza.
Relleno sólido en comparación con relleno de celda cerrada: el tiempo de lavado guarda una relación exponencial con el grosor de la pieza sólida, restringiendo su tamaño máximo. Como resultado, las piezas sólidas deben ser pequeñas o solo tener diseños finos. Al usar el relleno de celda cerrada, es posible imprimir piezas más grandes o más gruesas conservando tiempos de lavado manejables.
Consideraciones de seguridad: los sistemas de desaglomerado son bastante simples y seguros. Suelen estar conectados a un sistema de ventilación interno.
El disolvente principal, Opteon SF-79, se usa mucho en el sector, si bien hay otros disolventes disponibles. La exposición para los usuarios se encuentra muy por debajo de los niveles OSHA recomendados durante el funcionamiento de la máquina; la exposición en un entorno operativo típico es de 40 veces por debajo de los niveles recomendados y más de 2 veces por debajo de dichos niveles durante la exposición máxima. Opteon SF-79 también está clasificado como líquido no inflamable.
El baño en disolvente en versus el horno como paso principal de desaglomerado
Si bien es posible separar las piezas MIM por completo en un horno de sinterización, este enfoque presenta varios desafíos. Un impacto de dicho enfoque es el tiempo. Según Randall German, un líder experto en procesos de desaglomerado y de sinterización basados en la tecnología MIM, un proceso de desaglomerado basado en la sinterización es de seis a diez veces más lento que el desaglomerado basado en disolventes. Además, un ciclo de desaglomerado que solo se realiza en un horno lleva exponencialmente más tiempo cuanto más grande es la pieza, lo cual influye en gran medida en los tiempos de las piezas finales.
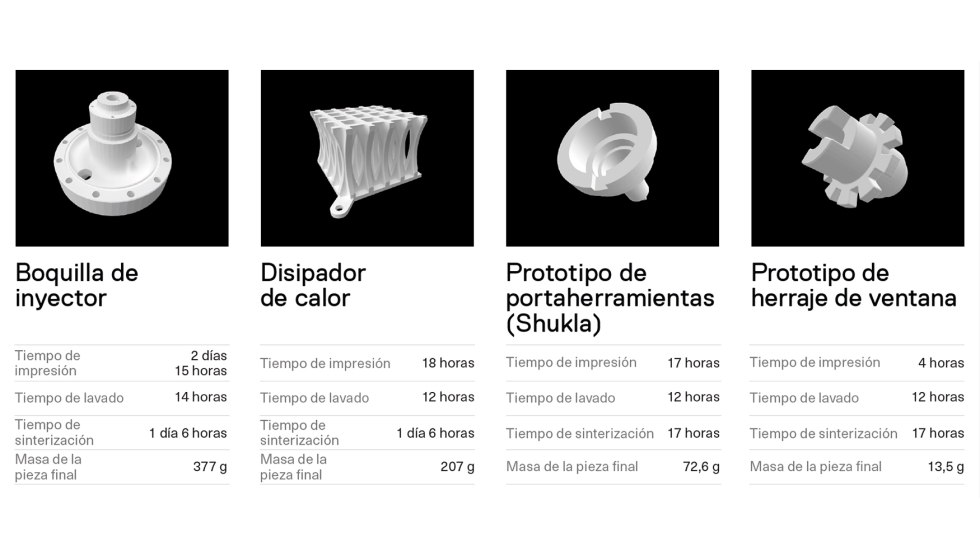
Sinterización FFF en metal
Este apartado está dedicado a un paso final esencial en un proceso de impresión FFF en metal: la sinterización. La sinterización abarca extraer las piezas en “marrón” del paso de separación, eliminar los restos de aglutinante usando calor sinterizar finalmente la pieza a una temperatura cercana a la de fusión. Todo esto se realiza en una atmósfera precisa y controlada. El proceso automatizado es extremadamente complejo y requiere un control preciso de un entorno de alta energía.
Uso del horno de sinterización
El usuario que utiliza un horno de sinterización debe seguir estos sencillos pasos:
- Primero, agregar piezas a la placa de fijación
- Colocar la placa de fijación en el horno
- Cerrar la puerta del horno
- Comenzar el proceso de sinterización
- Completar el proceso.
Los hornos de sinterización de Markforged suelen completar un ciclo de sinterización en un período de diecisiete a treinta horas. El proceso de sinterización consta de varias etapas principales. Primero, la pieza se calienta a una temperatura intermedia para eliminar los restos de aglutinante, que se eliminan de la pieza a través de los microsurcos creados durante el proceso de desaglomerado a base de disolventes. Segundo, la pieza se calienta a la temperatura de sinterización, desde la que se contrae partiendo del mayor tamaño como pieza “verde” o “marrón” al tamaño de la pieza final. Las geometrías sólidas se fusionan con una porosidad de más del 95%, pero permanece el relleno de celda cerrada. El material cerámico que actúa como interfaz se convierte en polvo, permitiendo al usuario separar con facilidad la pieza de la malla y de los soportes.
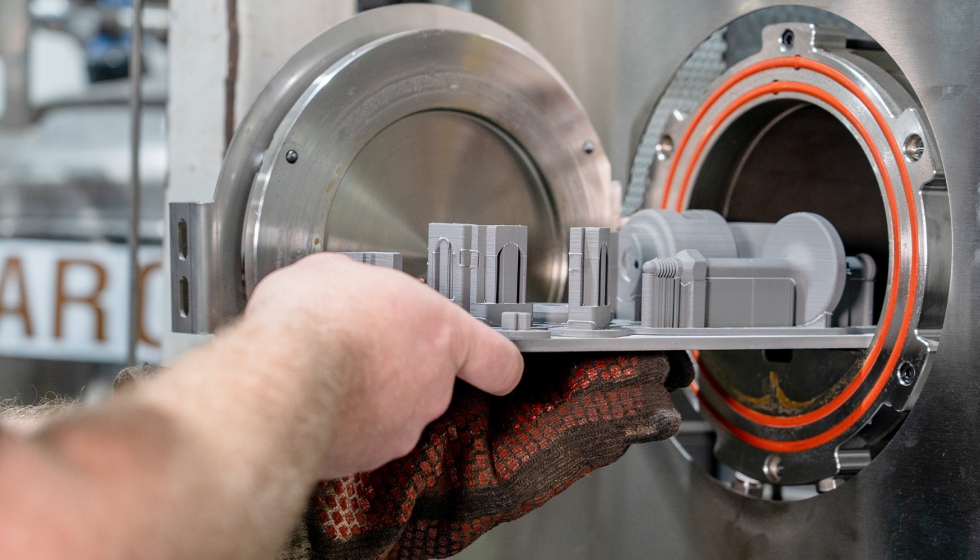
Consideraciones sobre la sinterización FFF en metal
Los hornos de sinterización FFF en metal son más complejos que los habituales porque los hornos de tecnología MIM deben funcionar en entornos inertes a temperaturas específicas. Esto se debe a la naturaleza de la materia prima y y al funcionamiento específico de este proceso de sinterización.
La dificultad y las restricciones aumentan exponencialmente con el tamaño de la pieza. Las piezas más grandes deben diseñarse para la fabricación aditiva.
El desaglomerado y la sinterización requieren altos niveles de precisión y de control. Una composición atmosférica precisa y una retorta sin carbono evitan que las piezas se contaminen durante el proceso de sinterización de alta energía. Un control preciso y predecible de la temperatura reduce la deformación y las grietas en las piezas, y permite una contracción predecible.
Posprocesamiento
Una vez sinterizadas las piezas, estas son totalmente metálicas y pueden posprocesarse de cualquier manera que el usuario estime adecuado. Los procesos de posprocesamiento más habituales son el tratamiento térmico, el pulido en tambor para acabado de superficies y el mecanizado.
Consideraciones de sobre instalaciones y cuestiones ambientales, de seguridad y salud (EHS, por sus siglas en inglés)
Los hornos de sinterización están optimizados para un entorno de talleres de impresión o de laboratorio. Requieren una ventilación básica y suministro de alimentación trifásica. Los componentes consumibles están diseñados para intercambiarlos con facilidad. Los hornos de sinterización FFF en metal utilizan una combinación de gas inerte y de mezcla, que pueden obtenerse en todo el mundo.
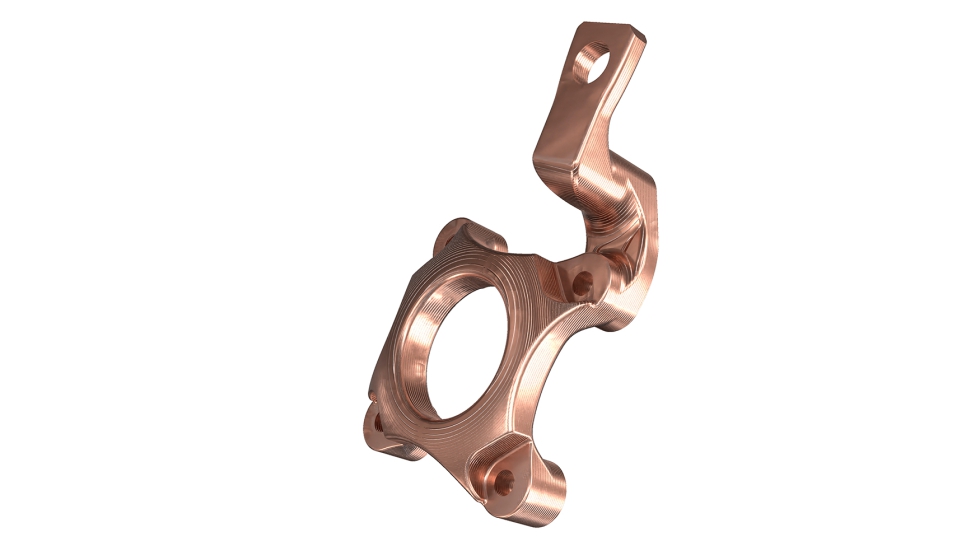
Markforged, una empresa innovadora en impresión 3D en metal
La impresión 3D en metal está en continua expansión y cuenta con una gran variedad de soluciones, capacidades y evoluciones. Poner en paralelo sus necesidades con la situación actual de esta tecnología puede mostrarle cómo debe invertir en ella. A la hora de implementar soluciones, es importante asociarse con un proveedor de tecnología como Markforged, que tiene los más amplios conocimientos y experiencia en impresión 3D en metal a escala mundial.
Markforged lo consigue gracias a Metal X, una solución de impresión 3D integral y accesible diseñada para producir piezas funcionales en metal. Metal X es la impresora 3D en metal más intuitiva y fácil de usar que se encuentra en el mercado. Permite imprimir una amplia variedad de materiales, desde acero inoxidable hasta cobre, con muy poca formación y en un flujo de trabajo cerrado. Metal X está diseñada para que sea seguro usarla para que la pueda usar todo aquel quiera fabricar en 3D. Cuesta de cinco a diez veces menos que los sistemas de impresión 3D en metal que utilizan polvo; no requiere un operadores especializados ni sistema de gestión de polvo, y necesita una cantidad mínima de equipos de protección individual. Markforged reúne el mejor software de su clase, investigación de materiales y un sistema avanzado de movimiento para fabricar piezas de grado industrial de manera fiable.