Lortek culmina con éxito el proyecto Additool
Donostia-San Sebastián acogió el pasado 9 de febrero el último evento de diseminación del proyecto Additool, donde se expusieron los resultados técnicos de cinco casos de uso propuestos por empresas del sector de la herramienta y utillaje. Al evento asistieron más de 100 personas.
Additool es un proyecto de consorcio europeo cofinanciado por los fondos de Desarrollo Regional Europeo a través del programa Interreg Sudoe que comenzó en noviembre de 2020. Su objetivo ha sido difundir las tecnologías más innovadoras de fabricación aditiva metálica para el sector de la herramienta y utillaje. En Lortek se ha trabajado en varias líneas; en el desarrollo de dos casos de uso empleando diferentes tecnologías de fabricación aditiva metálica, en formación a través de impartición de clases, webinars e intercambio de investigadores entre centros de investigación, y en un diagnóstico de necesidades y oportunidades para el sector. Además, tras el desarrollo de los casos de uso se elaboró un estudio de viabilidad técnico y financiero para su implementación en empresas.
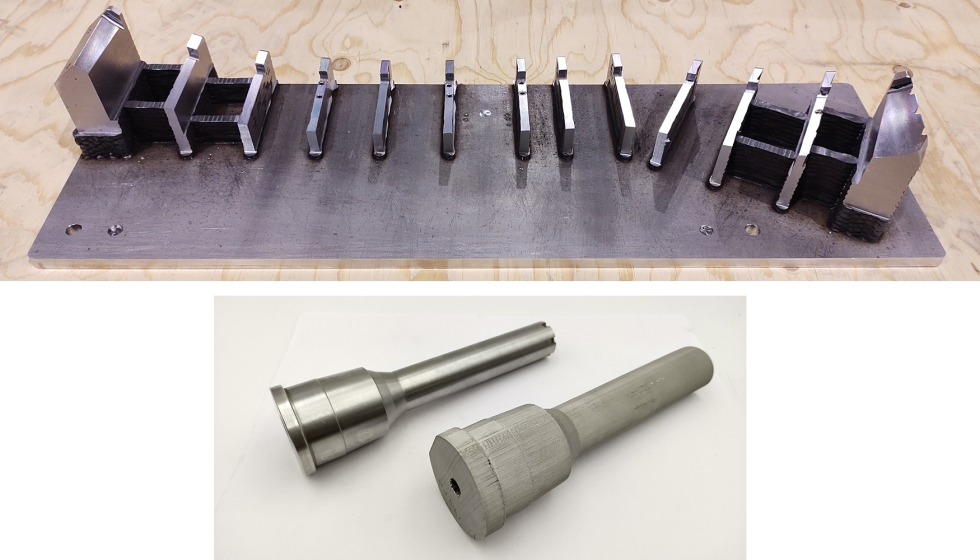
Casos de uso desarrollados: Arriba, utillaje de control. Abajo, inserto con refrigeración para molde.
La conferencia de Lortek se centró en uno de los casos de uso en los que ha participado. El caso de uso se trataba de una pieza metálica consistente en un utillaje de control de 560 x 172 x 85 mm con un requisito de tolerancia dimensional muy estrecho (propuesta de Lauak). Se fabricó en acero de alta resistencia mediante la tecnología Wire and Arc Additive Manufacturing (Waam). El diseño se adaptó con el objetivo de reducir su peso en un 28% y, por lo tanto, también el calor aportado y las distorsiones asociadas. La cantidad de material a eliminar mediante mecanizado partiendo de un bloque macizo es de 40 kg, siendo en el caso de la fabricación por Waam menos de 1 kg. El tiempo calculado de entrega es un 66% menor.
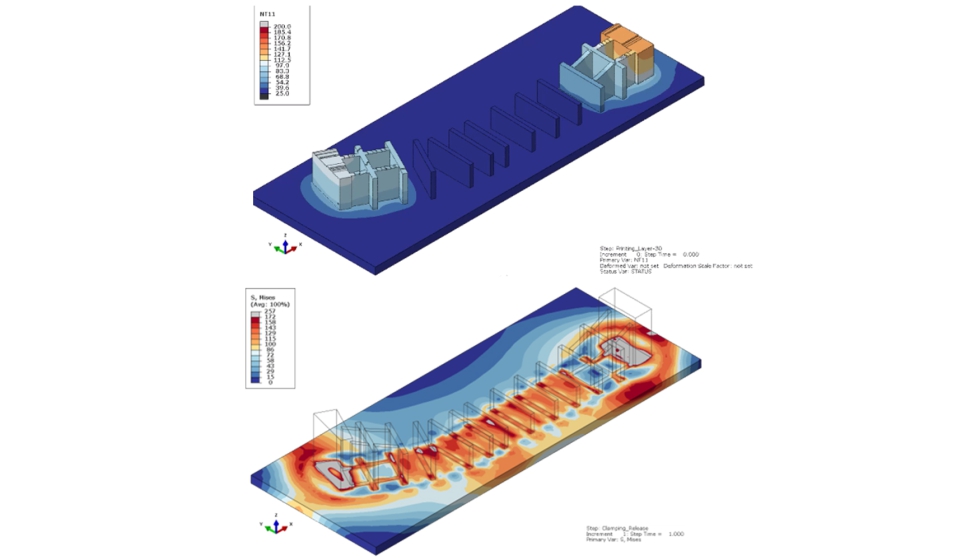
Resultados de simulación de: arriba, temperaturas entre pasadas. Abajo, tensiones residuales.
El utillaje se fabricó aplicando un tiempo de espera por capa obtenido por simulación. De esta manera, se consigue un crecimiento estable sin calentamiento excesivo de la pieza durante la fabricación y con un tiempo de fabricación total optimizado. Concretamente, consiste en un tiempo de espera variable por tramos de capas con un límite de temperatura entre capas establecido. Esto asegura la ausencia de distorsiones significativas evitando problemas durante la fabricación.
Lortek también participó activamente en otro de los casos desarrollados en el proyecto (propuesta de Somocap). Concretamente en un inserto para un molde de piezas de plástico al que se le añadió un canal interno conformado para una refrigeración optimizada (rediseñado por Estia-Addimadour). El desarrollo llevó a cabo mediante la aplicación de la tecnología de Fused Filament Fabricación (FFF) en los aceros H13 y 17.4PH.
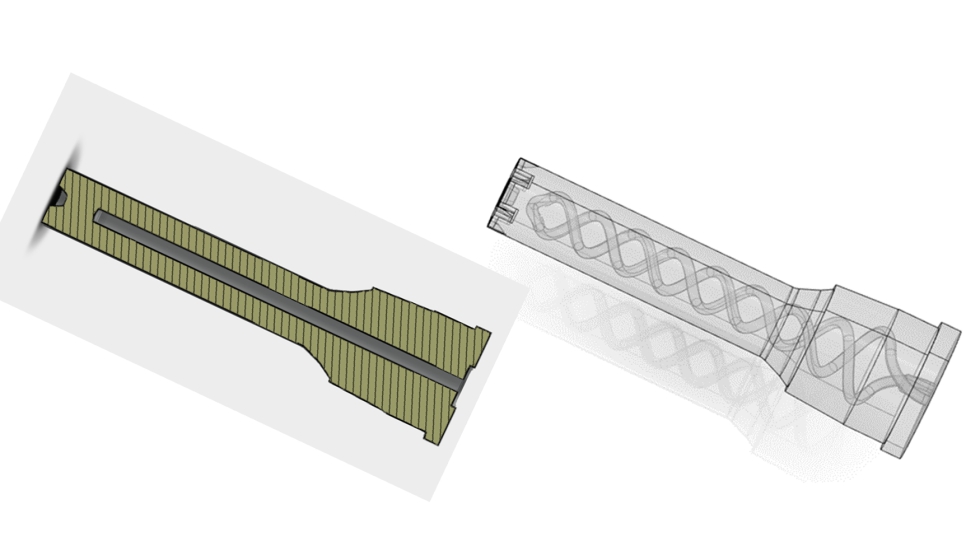
Refrigeración interna convencional diseñada para mecanizado y refrigeración conformada diseñada para fabricación aditiva.
Tras el evento, todos los y las asistentes pudieron disfrutar de un encuentro donde las empresas interesadas pudieran ver de cerca los casos de uso físicos, aclarar dudas o resolver cualquier curiosidad directamente con los miembros del proyecto.
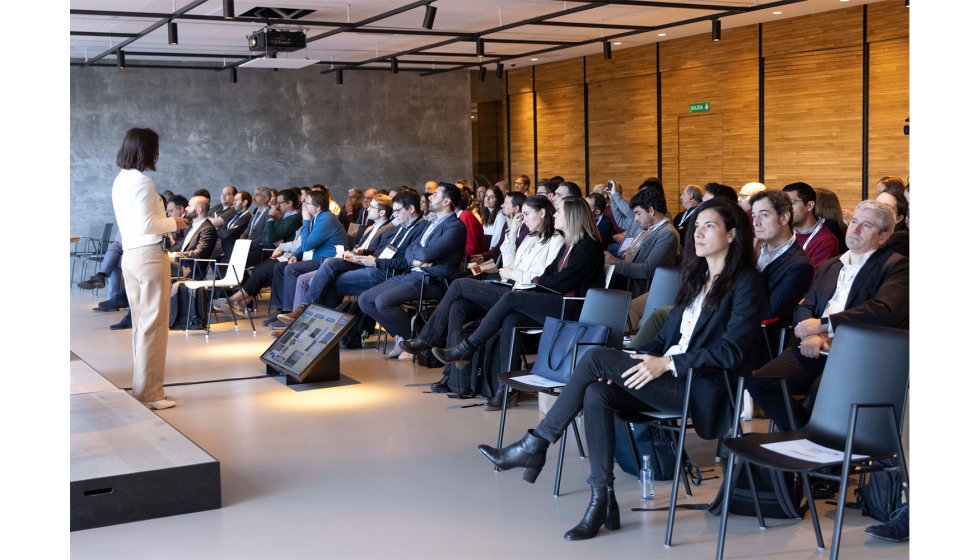
Evento celebrado en Donostia-San Sebastián para la diseminación de los resultados del proyecto.
Tras el cierre del proyecto, el 28 de febrero, el consorcio desea en un futuro muy cercano seguir colaborando y contribuyendo en estos aspectos.