Arburg presenta en la K 2022 su nueva Freeformer 750-3X, con cámara de construcción 2,5 veces más grande
Gracias al uso de la unidad de mando Gestica, optimizada para el proceso de fabricación aditiva, el Freeformer 750-3X también aporta mejoras a la estabilidad del proceso, la calidad de los componentes y la optimización del tiempo de fabricación.
El principio de preparación del material del Freeformer 750-3X es el mismo que el del Freeformer 300-3X, pero todo el sistema ha sido optimizado para que el diseño de la nueva unidad sea aún más compacto. A simple vista, el Freeformer 750-3X no se diferencia del 300-3X, ya que cuenta con las mismas dimensiones externas. No obstante, el portador de componente es aproximadamente 2,5 veces más grande, con unos 750 centímetros cuadrados, a los que hace referencia el nombre del nuevo sistema. La cámara de construcción considerablemente ampliada, que mide 330 milímetros x 230 milímetros x 230 milímetros, en la que, por cierto, es posible mantener temperaturas muy estables y homogéneas, es el resultado de diversas innovaciones técnicas. Esto incluye generadores de presión de masa más estrechos y compactos para la dosificación e inyección, los cuales integran los servomotores de AMKmotion, una empresa de la familia Arburg.
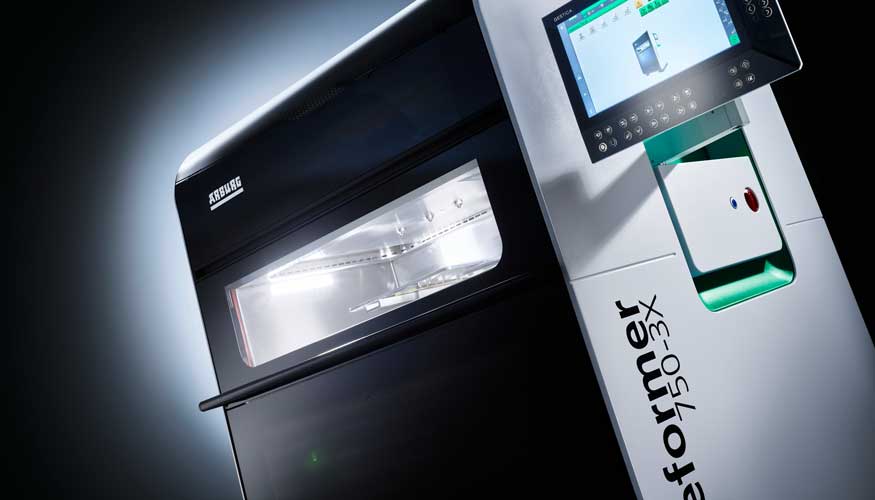
Novedad en el programa de Arburg para la fabricación aditiva industrial: el Freeformer 750-3X. Foto: Arburg.
Unidad de mando Gestica como plataforma conjunta

En el Freeformer 750-3X, las tres unidades de descarga son más compactas y ocupan menos espacio que en la versión 300-3X. Foto: Arburg.
Las novedades en el ámbito de la unidad de mando incluyen concretamente el “mando de producción“ con mando intuitivo, por ejemplo mediante vistas del estado de descarga y fabricación, y la”secuencia de arranque inteligente” para la preparación de la producción que se ejecuta de forma completamente autónoma. A esto se suman la dosificación variable en función de la necesidad, el tiempo reducido de permanencia del material en el cilindro, la dosificación paralela de las distintas secuencias y, consecuentemente, un tiempo de fabricación reducido, así como la optimización y ampliación del procesado de datos y disección por capas en relación a la estrategia de fabricación de las estructuras reticulares y a la denominada estructura de soporte Break-Away. Este término designa la retirada más fácil de las estructuras de soporte. Todo ello contribuye a la mejora de la estabilidad del proceso, la calidad del componente y la optimización del tiempo de fabricación.
Reducciones del tiempo de fabricación hasta en un 85%
Otro ejemplo interesante es la fabricación aditiva de una junta de ventana para automóvil. El tiempo de presión estándar hasta ahora era de 67 horas y 32 minutos. Gracias a una cámara de construcción más grande, ahora los componentes se pueden disponer en horizontal en lugar de en vertical. A esto cabe añadir una estrategia reticular modificada (estructuras de soporte), una aplicación de gota más rápida, el incremento de la frecuencia y el aumento del grosor de capa de 0,2 a 0,25 milímetros, lo que en conjunto se traduce en una reducción del tiempo de presión hasta nueve horas y 38 minutos. Esto significa una reducción del 85%.
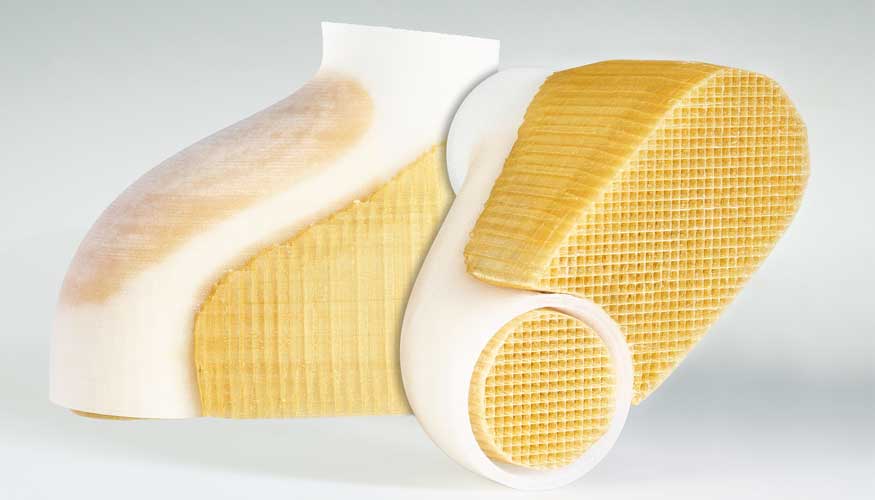
En el ejemplo de componente Hollow Tube, con el nuevo Freeformer 750-3X se redujo el tiempo de fabricación en un 60%. Foto: Arburg.
Arburg crea tendencia
innovatiQ en K 2022
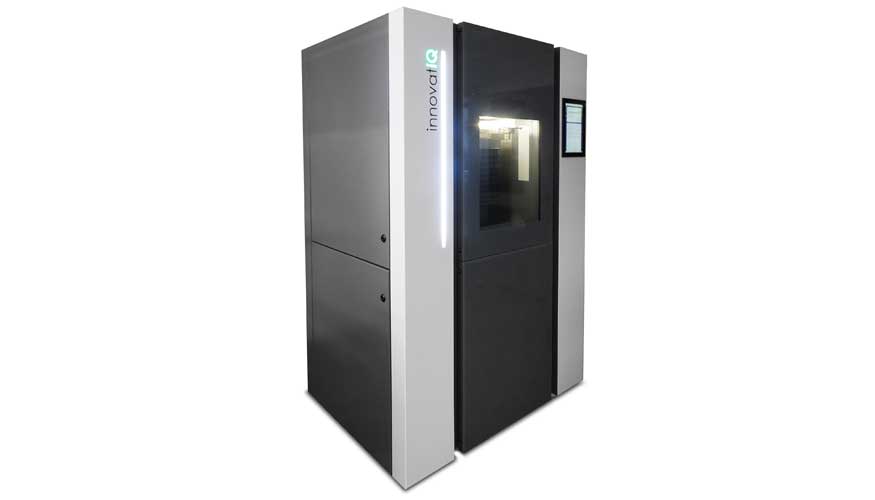
Nuevo: TiQ 2
Con la nueva TiQ 2, innovatiQ ofrece una máquina de producción compacta con control CNC, chasis metálico y una zona de seguridad encapsulada. El cabezal de impresión desarrollado por la propia innovatiQ es especialmente adecuado para los filamentos reforzados con fibra. Gracias a su diseño robusto, garantiza una producción en 3D fiable incluso durante largos periodos de impresión. Muy compacto, el TiQ 2 es especialmente adecuado para la producción de materiales auxiliares y de funcionamiento y, por tanto, complementa cualquier unidad de producción. innovatiQ ha equipado el TiQ 2 con un sistema de materiales abierto, pero todos los parámetros se centran en el uso de PA con fibras de carbono. El refuerzo de fibra del filamento permite la impresión en 3D de pinzas de máquina individuales o de todas las herramientas de fin de brazo (EOAT) necesarias en la producción de moldeo por inyección. Con su bajo precio de entrada, la TiQ 2 también es adecuada para la llamada personalización en masa, es decir, la producción en serie personalizada de variantes de componentes. De este modo, la TiQ 2 cumple todos los requisitos de una máquina complementaria en la producción flexible actual.
Novedad: LiQ 5 amplía la impresión 3D con silicona LSR para incluir el control de la temperatura del proceso
En el campo de los sistemas de impresión para procesar silicona líquida LSR estándar (Liquid Additive Manufacturing), innovatiQ está realizando un trabajo pionero, incluso mediante patentes para esta forma de procesamiento. La serie LiQ 5 para el procesamiento de LSR está ahora equipada con una cámara de construcción activamente calentable y permite alcanzar temperaturas de hasta 80 °C. El control muy uniforme de la temperatura en la cámara de construcción aumenta significativamente la fiabilidad y la calidad de la superficie cuando se imprimen componentes de alto formato hechos de silicona LSR.
Nueva versión GestiQ-Pro: interfaz hombre-máquina (HMI) intuitiva
Todas las series de impresoras innovatiQ se manejan a través del intuitivo sistema de control industrial GestiQ-Pro, que en la nueva generación de impresoras se encuentra ahora en una gran pantalla táctil. GestiQ-Pro se ha ampliado con SmartFunctions adicionales. Las SmartFunctions facilitan el manejo y la configuración de los sistemas de impresión y aumentan la productividad en el funcionamiento diario. Con la ayuda de una clara estructura de menús, se pueden controlar todas las funciones relevantes del sistema de impresión 3D.
Otra novedad es el sistema SmartMonitoring, disponible opcionalmente, que permite supervisar la producción de varias impresoras. En combinación con una interfaz OPC-UA, las impresoras innovatiQ ahora también pueden conectarse al sistema informático anfitrión ALS de Arburg.