En una entrevista, Mähler contó cómo se puede fabricar un producto acabado utilizando una combinación de diferentes tecnologías de impresión 3D y por qué eligió este proceso
Cómo XSPECTER combina piezas de uso final impresas en SLA y SLS para fabricar su trípode para cámaras de exterior
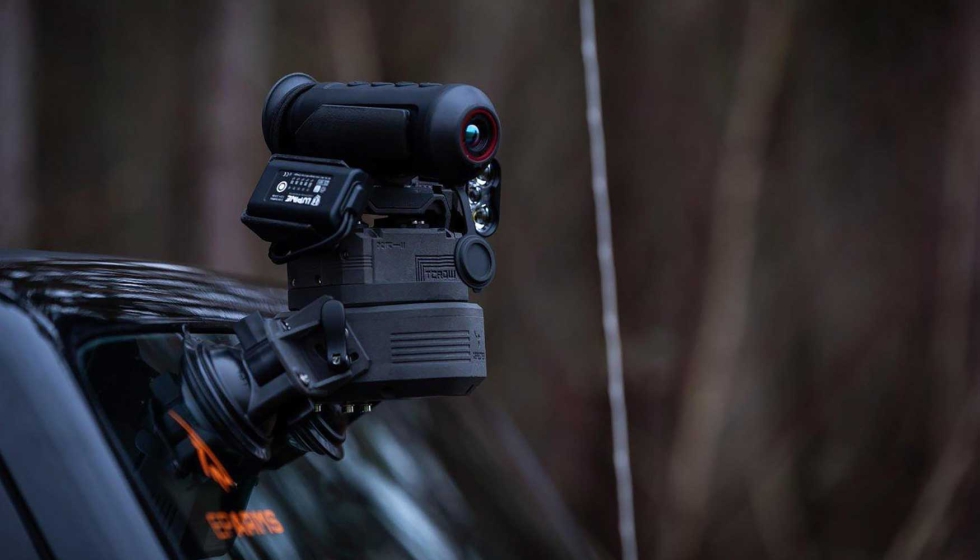
Desarrollo de un trípode de cámara de 360º controlable
El cazador recreativo y empresario Matthias Mähler se dedicó a buscar una solución adecuada para montar sus dispositivos en el exterior de su vehículo.
Tras darse cuenta de que no había ningún soporte o trípode adecuado en el mercado, se puso manos a la obra. Comenzó con la construcción de un prototipo de trípode estabilizador y controlable para dispositivos de visión nocturna y de imagen térmica, que puede montarse en el techo o en el cristal de la ventana de un coche mediante ventosas o pies magnéticos.
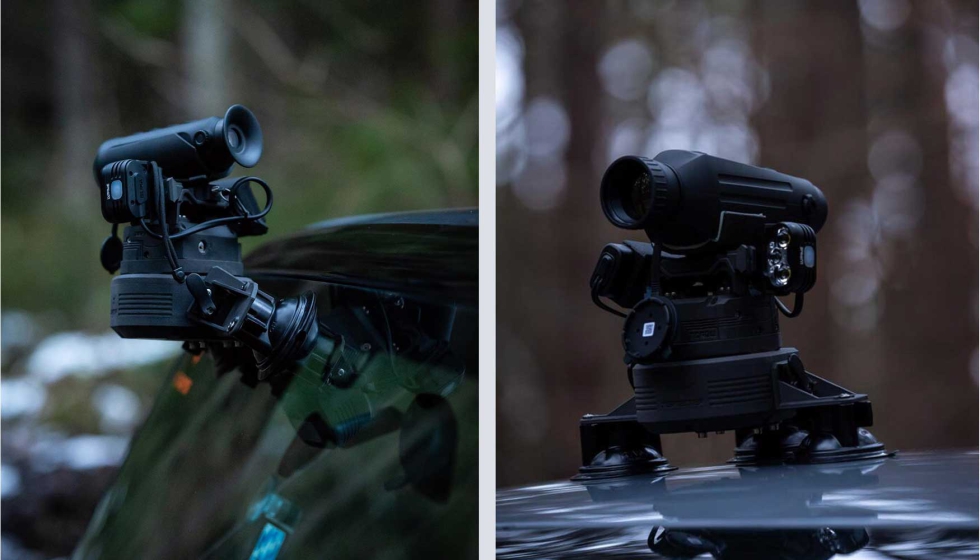
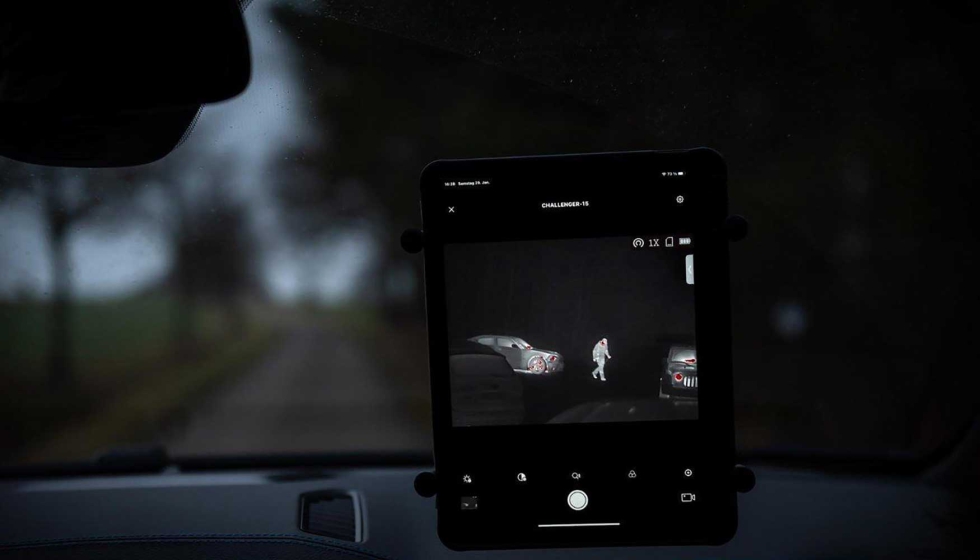
De los prototipos a la producción en serie
“La impresión 3D se integró en mi línea de producción porque utilicé estas tecnologías para producir los prototipos. Funcionó tan bien que acabamos diseñando todo el producto utilizando varias tecnologías de impresión 3D, y todavía lo estamos produciendo con impresión 3D en la actualidad”, dice Mähler.
En primer lugar, Mähler realizó varios prototipos del trípode en colaboración con proveedores de servicios de impresión 3D en impresoras FDM. Una vez que el diseño preliminar del producto estuvo listo, se puso en contacto con el socio de Formlabs, AMPro 3D, para que le asesorara sobre qué tecnologías y materiales de impresión 3D serían adecuados para la primera producción en serie.
"Adaptamos todo al proceso SLS, porque los altos detalles y la falta de estructuras de soporte te brindan muchas más opciones en la impresión SLS. Pasamos casi sin problemas del prototipo a la producción en serie", dice Matthias Mähler.
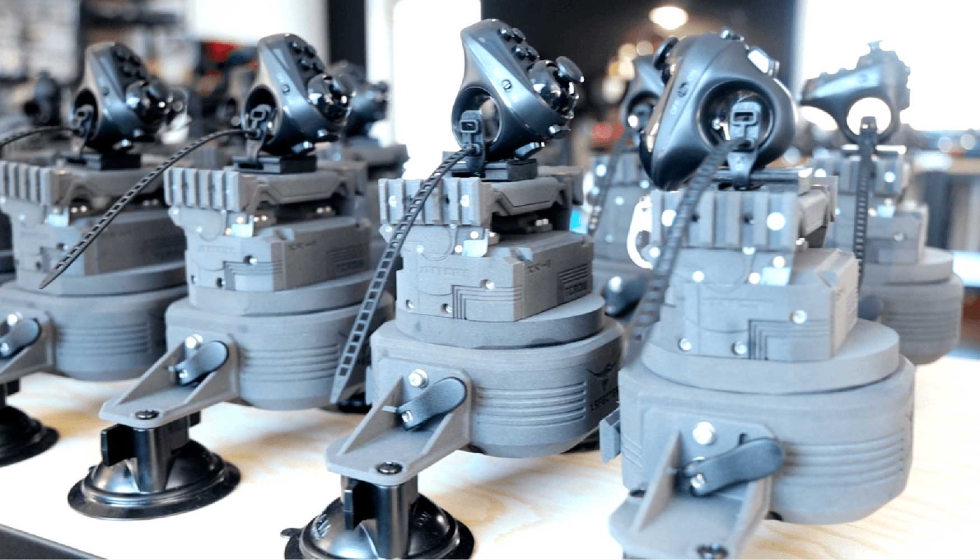
“Creo que las impresoras 3D de Formlabs son realmente las mejores impresoras disponibles actualmente en el mercado en términos de relación calidad-precio” Matthias Mähler
La carcasa se fabrica en la Fuse 1. Gracias al material Nylon 12 Powder de Formlabs, la carcasa sigue siendo ligera y resistente a los impactos ambientales. También es muy adecuado para fundir posteriormente los casquillos roscados durante el montaje.
Para los ejes y engranajes, XSPECTER utiliza su Forma 3L y la resina Durable. Las propiedades flexibles, pero resistentes a los impactos y de baja fricción del material hacen posible la instalación de ajustes de interferencia, que son necesarios para el sistema de control de dos ejes.
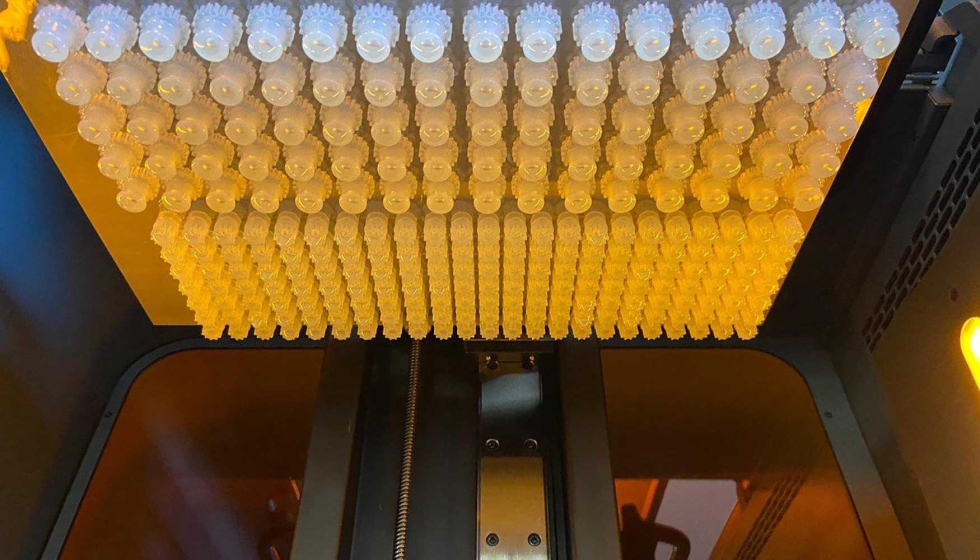
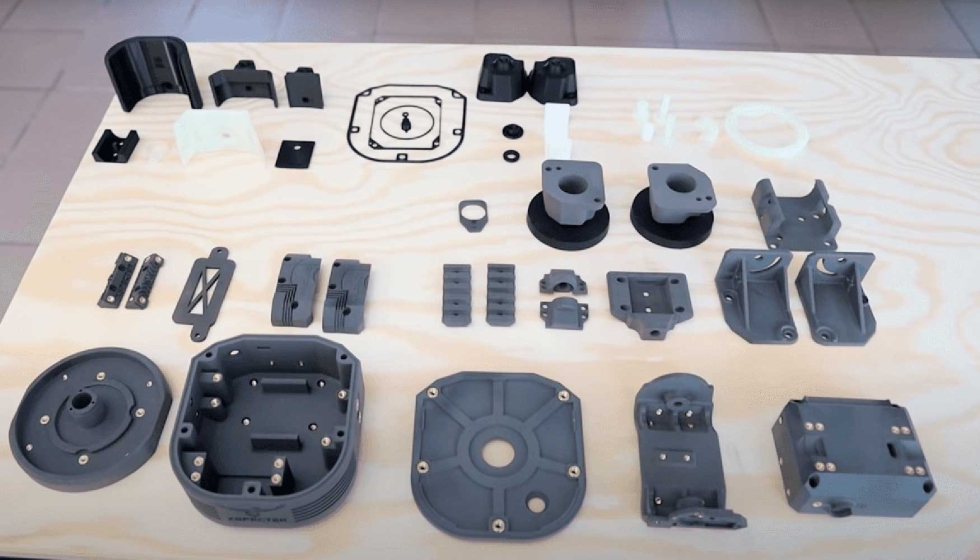
Flexibilidad de diseño gracias a la impresión 3D
“Con la impresión 3D, simplemente tenemos más libertad de diseño que con los métodos convencionales, como el moldeo por inyección. A esto lo llamamos un producto vivo. Si encontramos un error de diseño o recibimos comentarios de los clientes, podemos implementar una nueva iteración de la noche a la mañana. Eso no se puede hacer con ningún otro método”, en palabras de Matthias Mähler.
Los cambios de diseño de este tipo se realizan, por ejemplo, al personalizar los adaptadores de diferentes cámaras, para que los trípodes puedan utilizarse de forma universal. Las diferentes características de diseño se integran directamente en la carcasa impresa en 3D. Cuando sale una nueva cámara al mercado, Mähler puede llevar a cabo rápidamente los cambios correspondientes en su trípode T-Crow y venderlo.
“Una vez dejé de recibir el interruptor de encendido/apagado de nuestro proveedor original y me vi obligado a cambiar a otro. Para nosotros, eso significaba que la abertura para el interruptor de encendido/apagado tenía que ampliarse unos dos milímetros, que cambié casi de la noche a la mañana”, explica Mähler.
Con el utillaje para el moldeo por inyección que se cotizó por unos 120.000 € para empezar, esa modificación del molde original habría requerido bastante más tiempo y dinero.
Dado que XSPECTER consigue la misma cantidad con menores costes de las piezas con la impresión 3D que con el moldeo por inyección, al tiempo que confía mucho en la flexibilidad de la impresión 3D SLS en su estrategia, Mähler no puede imaginar ninguna otra tecnología de fabricación para su producto en un futuro próximo.
Mientras tanto, Mähler ya está trabajando en su próximo proyecto, llamado Sea-Crow: una variante marítima del trípode de la cámara, que también incluye focos de búsqueda y a su vez funciona como ayuda a la navegación nocturna en el agua.