Mecanizando componentes impresos: un reto y una oportunidad
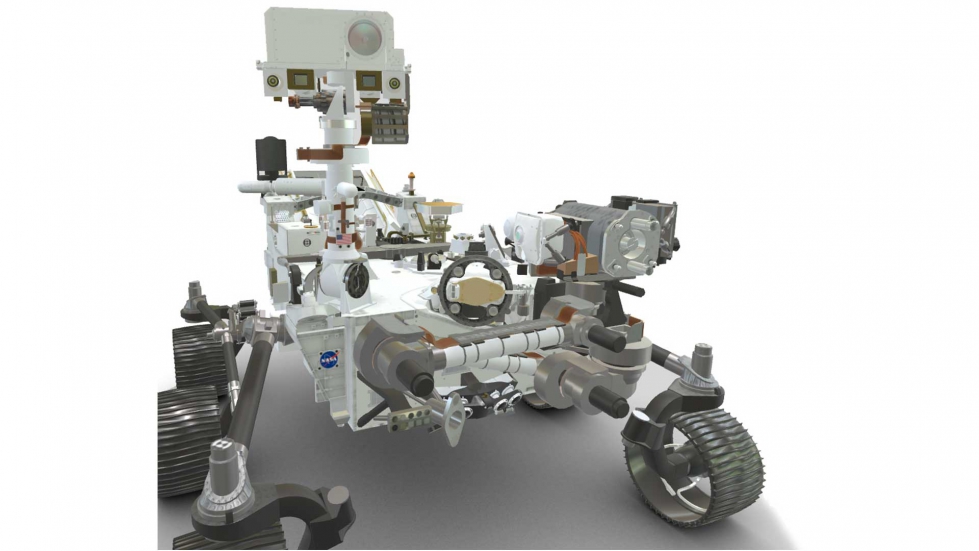
Desde el Curiosity (2012) hasta el Perseverance (2021) se ha tardado casi una década en garantizar la fiabilidad de la fabricación aditiva de componentes críticos para la seguridad y ahora se ha confirmado que los componentes de fabricación aditiva podrían utilizarse para aplicaciones espaciales. Ahora es el momento de que los ingenieros e investigadores de fabricación aprovechen esta oportunidad y empiecen a pensar en una dirección muy positiva de diseño de componentes de fabricación aditiva.
Resulta fascinante saber que los investigadores trabajan sin cesar para imprimir un componente perfecto de fabricación aditiva que no requiera ningún tipo de procesamiento posterior ni mecanizado de acabado. Los componentes de fabricación aditiva sin necesidad de mecanizado o proceso de acabado son el Santo Grial de la industria manufacturera. Sólo el futuro tiene una respuesta a tal tecnología. Mientras tanto, las industrias se centran más en un enfoque convencional de “imprimir más y mecanizar lo menos posible”. Este enfoque de hibridar los procesos de fabricación es menos fascinante, pero más realista. El uso combinado de ambos procesos de fabricación podría contribuir a la rápida adaptación de los componentes de fabricación aditiva para su uso final en aplicaciones aeroespaciales, de automoción y espaciales.
Dentro del Grupo de Fabricación de Alto Rendimiento de la UPV-EHU y el CFAA, con nuestras impresoras de fabricación aditiva de metal de última generación y las tecnologías de mecanizado, pretendemos ofrecer componentes de alta calidad para la fabricación aeroespacial. Pretendemos conectar digitalmente nuestro bucle proceso-propiedad-rendimiento para promover la ciberfabricación orientada al crecimiento y las fábricas de la Industria 4.0.
Una de las líneas de investigación del CFAA en la actualidad tiene que ver con la predicción del efecto de los parámetros de fabricación de LPBF sobre las propiedades mecánicas de las piezas impresas con el fin de facilitar los procesos de posprocesamiento por mecanizado. La fabricación aditiva de piezas metálicas es especialmente competitiva en lotes pequeños y en piezas con formas complejas y de pared delgada. Estas caracteristicas conllevan a que la labor de posprocesamiento por mecanizado sea compleja en términos de la baja rigidez de las piezas, y la posibilidad de deformación elástica durante el clamping o generación de chatter durante el mecanizado. Es por esto que en el CFAA se desarrollan actualmente metodologías relacionadas con la integración de la cadena de proceso desde la concepción del diseño hasta la etapa final del posprocesamiento, teniendo en cuenta cada uno de los efectos de cada etapa sobre la forma, microestructura, cristalografía, propiedades mecánicas, distorsion volumétrica y calidad superficial entre otros.
La fabricación hibrida hace parte del presente y el futuro de la actividad investigativa del CFAA. Dentro del marco de la fabricación hibrida son muchos los aspectos a tener en cuenta para que las piezas fabricadas por aditivo puedan tener uso funcional o industrial, sin embargo, son 3 los aspectos principales que deben monitorizarse para garantizar este objetivo. Uno de estos aspectos es la calidad estructural de la pieza, que se refleja especialmente en el control de los niveles de porosidad y grietas. Otro aspecto importante radica en la integridad superficial, para lo cual se hace necesario que la fabricación y posproceso garanticen bajos niveles de rugosidad y tensiones residuales. El tercer aspecto a considerar es el de las propiedades mecánicas. Todos los aspectos previamente mencionados están relacionados con el diseño de la pieza. el nivel de porosidad y grietas condicionan la vida útil por fatiga, la tenacidad a la fractura y la resistencia a la tracción. La rugosidad a su vez está relacionada con la resistencia a la fatiga y la tribología. Por otro lado, un nivel apropiado de las propiedades mecánicas permite la funcionalidad de los componentes para aplicaciones industriales. Estos tres aspectos están profundamente relacionados con la naturaleza del material, la microestructura y cristalografía.
Una de las estrategias del CFAA para mejorar la eficiencia de la etapa del posprocesamiento es la de conocer la ‘huella microestructural’ que deja el proceso de aditivo sobre sobre el material en función de los parámetros de fabricación aditiva y posteriormente traducir el significado de las caracteristicas de la “huella microestructural” y su efecto sobre los aspectos que afectan el posprocesamiento, esto es por ejemplo: dureza, resistencia al corte, rigidez, entre otros.
Es por esto que el conocimiento de las interacciones entre microestructura, cristalografía y las caracteristicas elásticas y plásticas del material constituyen la clave del éxito del posprocesamiento por mecanizado. Un proceso de mecanizado sobre una estructura flexible es un paso muy necesario en la obtención de las dimensiones definitivas de piezas de aditivo, sin embargo, al mismo tiempo es un reto desde el punto de vista de la rigidez, y es precisamente en este ámbito donde la aplicación de estrategias apropiadas de SLM pueden favorecer esta tarea desde la etapa de diseño y concepción de un proyecto.
Contribución en la revista número 1 de fabricación
Un aspecto fundamental del posprocesamiento por mecanizado de piezas de inconel 718 LPBF es la caracterización de las fuerzas de corte y coeficientes mecanisticos, con el fin de optimizar las operaciones y estrategias de mecanizado sobre piezas de pared delgada. Durante la caracterización de las fuerzas de corte por fresado periférico en el CFAA se identificó una fuerte dependencia entre el nivel de las fuerzas de corte y la orientación relativa de la herramienta respecto a la pieza. El alto nivel de variabilidad de las fuerzas de corte llevó a la necesidad de hacer una evaluación profunda de las características microestructurales del material que generaban anisotropía en las fuerzas de corte. El análisis realizado permitió encontrar establecer que la principal causa de la anisotropía en las fuerzas de corte era la alta intensidad de la textura cristalográfica y la presencia de los granos columnares. Sin embargo, el verdadero reto consistió en la cuantificación del efecto de las propiedades microestructurales y cristalográficas sobre la variabilidad en la resistencia al corte, para este fin fue necesario considerar el efecto de la estructura cristalina dentro de los granos y el efecto de las fronteras de grano sobre la resistencia a las dislocaciones plásticas ejercidas por el campo de esfuerzo que ocasiona el paso de la herramienta sobre el material. Para este fin se desarrollaron modelos basados en la teoría de microplasticidad de Taylor [2], Hall-petch y Zerilli Armstrong [3]. de manera complementaria fue necesaria la discretización de la distribución de orientaciones cristalinas para obtener un factor de taylor macroscópico que pudiera ser representativo de la resistencia al corte en función de la posición de la herramienta. Los resultados permitieron obtener una clara correlación entre el factor de taylor macroscópico en el plano de corte oblicuo y los coeficientes de corte tangenciales. Adicionalmente se encontró una correlación entre la densidad de fronteras de grano y la fuerza de corte.
Esta investigación fue publicada en el Journal # 1 del mundo en el área de fabricación (International Journal of Machine Tools and Manufacture) El pasado mes de septiembre bajo el título: ‘On the relationship between cutting forces and anisotropy features in the milling of LPBF Inconel 718 for net near shape parts’.

Los resultados y conclusiones de esta investigación tienen un importante aporte al conocimiento del mecanizado de esta nueva familia de materiales y permiten conocer Los fundamentos de la mecánica presente en las principales interacciones entre los procesos de LPBF y mecanizado que dan lugar a la dependencia de las fuerzas de corte en función de la orientación relativa de la herramienta respecto a la pieza.
José David Pérez es investigador del CFAA en el área de fabricación hibrida (Aditivo+Mecanizado). Es ingeniero mecánico de la universidad industrial de Santander (Bucaramanga-Colombia), especialista en electrónica industrial y magister en ingeniería mecánica (Universidad del Norte, Barranquilla-Colombia). Actualmente es becario del gobierno de Colombia y desarrolla su doctorado en ingeniería mecánica en la universidad del País Vasco (Bilbao). Cuenta con más de 10 años de experiencia profesional en diferentes sectores industriales (oil&gas, Fabricación y automotriz) y experiencia docente e investigativa en las áreas de integridad estructural, modelización, simulación, fabricación hibrida, entre otros.
Referencias
[1] https://www.nasa.gov/feature/jpl/nasas-perseverance-rover-bringing-3d-printed-metal-parts-to-mars
[2] W.B. Lee, S. To, Y.K. Sze, C.F. Cheung, Effect of material anisotropy on shear angle prediction in metal cutting - A mesoplasticity approach, in: Int. J. Mech. Sci., Pergamon, 2003: pp. 1739–1749. https://doi.org/10.1016/j.ijmecsci.2003.09.024.
[3] F.J. Zerilli, R.W. Armstrong, Constitutive relations for the plastic deformation of metals, in: AIP Conf. Proc., AIP Publishing, 2008: pp. 989–992. https://doi.org/10.1063/1.46201.