Velocidad y escala en los implantes espinales
Desde su fundación hace más de veinte años en el valle biomédico de Italia, cerca de Módena, Tsunami Medical ha seguido evolucionando y aumentando su negocio en respuesta a la dinámica del mercado del siempre cambiante sector de los implantes médicos a nivel mundial. En el centro de la evolución de la empresa se encuentra una sólida estrategia de innovación que abarca e integra nuevas tecnologías como la fabricación aditiva. Esto le permite mantenerse a la vanguardia del diseño, desarrollo y fabricación de dispositivos médicos para la cirugía de la columna vertebral y los procedimientos invasivos.
Después de establecer rápidamente su experiencia en el campo de la biopsia y la vertebroplastia, ya en 2010, Stefano Caselli, fundador y director general de Tsunami Medical y su equipo habían empezado a explorar cómo las tecnologías aditivas metálicas podían aplicarse a las jaulas e implantes de la columna vertebral.
La compra de sus dos primeras máquinas DMLM láser de GE Additive Concept en 2015 marcó un importante hito en el camino de los aditivos de la empresa. Avance rápido cinco años hasta hoy, y Tsunami Medical sigue centrada en el sector de la columna vertebral y hasta la fecha ha fabricado aditivamente más de 50.000 piezas para sus clientes globales.
Para aumentar la producción a escala, a principios de este año, la compañía adquirió dos sistemas adicionales de GE Additive Concept Laser Mlab, duplicando el tamaño de su flota a cuatro máquinas.
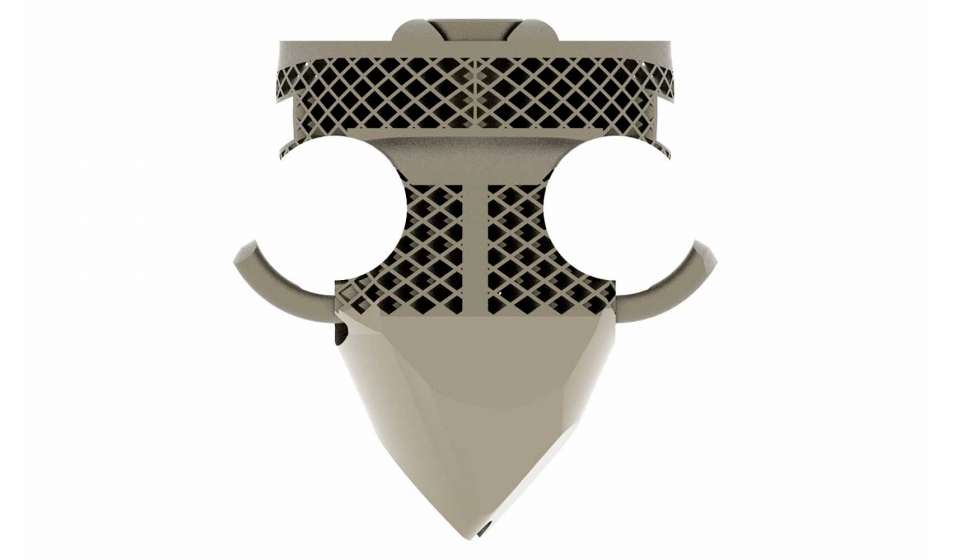
La rápida innovación en los dispositivos de la columna vertebral
La innovación en los implantes de la zona espinal ha recorrido un largo camino en un período relativamente corto de tiempo. Esto es en parte gracias a compañías como Tsunami Medical, que trabajan mano a mano con ortopedas, neurocirujanos y otros profesionales médicos con visión de futuro, para integrar el aditivo metálico en su trabajo.
En comparación con los primeros implantes basados en PEEK, la fabricación aditiva metálica ahora no sólo permite calibrar las propiedades mecánicas, el módulo elástico y la rigidez de un dispositivo, sino que también permite a los diseñadores de dispositivos la libertad de crear estructuras abiertas, en una calidad que se acerca a la de replicar las estructuras porosas del hueso trabecular.
Otra ventaja de las estructuras fabricadas adicionalmente es que pueden incorporarse a la forma del implante y producirse en una sola etapa de producción, sin necesidad de un revestimiento adicional. Esto permite el diseño de estructuras porosas con conformaciones personalizadas de los poros, el grosor y la porosidad general.
“La colaboración y el aprendizaje compartido con los profesionales médicos y de la salud de todo el mundo es inestimable. Sus ideas y su continuo entusiasmo por los aditivos metálicos nos dan energía y ayudan a influir y a dar forma a nuestra estrategia de innovación en el futuro”, añade Caselli, ingeniero biomédico.
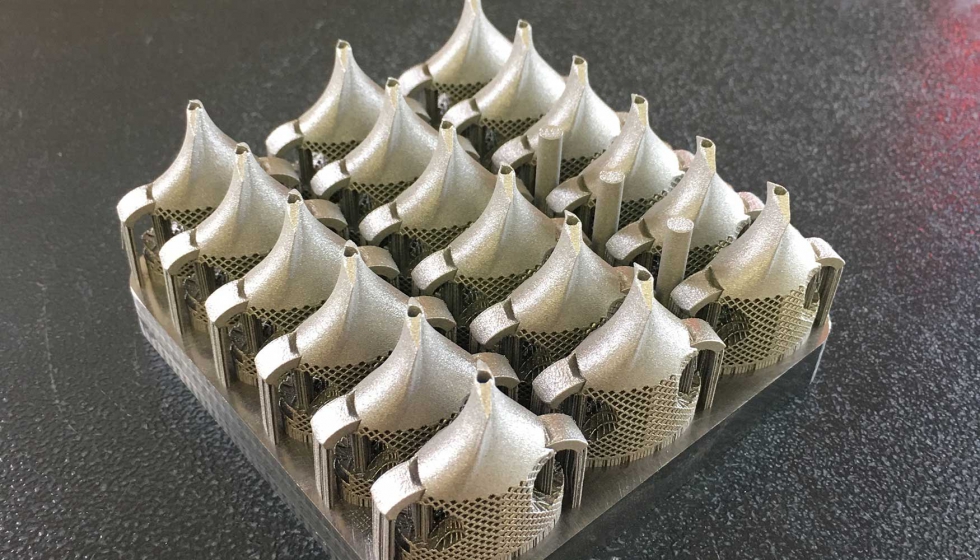
DMLM impulsa la innovación y el aumento de la productividad
El sistema está destinado a las enfermedades lumbares con un requisito segmentario indicado. Esto cubre una amplia gama de condiciones médicas, tales como: enfermedades degenerativas de los discos, inestabilidad vertebral, procedimientos de revisión para el síndrome posdiscectomía, pseudoartrosis, falta de fusión espinal o fusión espinal degenerativa y deformidades en adultos.
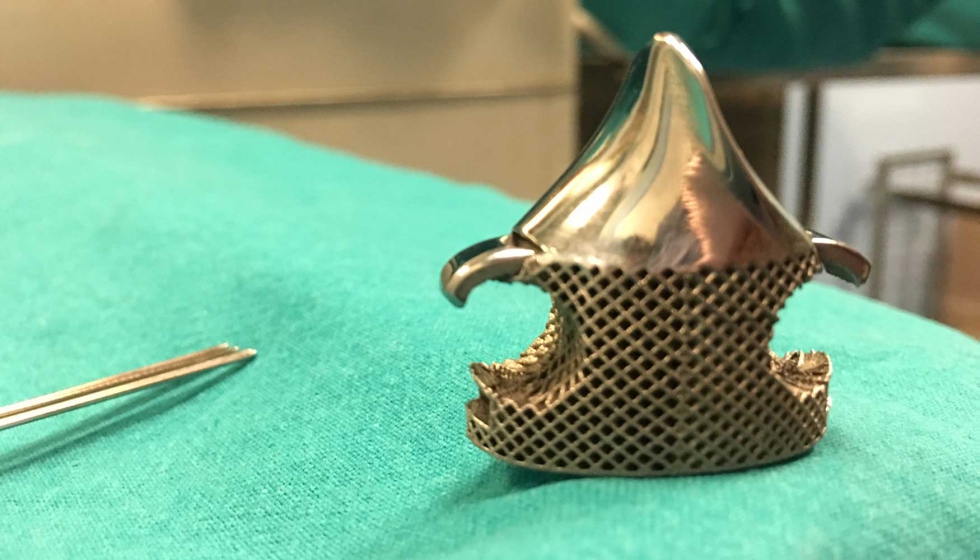
El giglio consiste en un dispositivo espaciador interespinal y las herramientas necesarias para su colocación y fijación dentro de una operación mínimamente invasiva. Cinco piezas móviles y articuladas permiten la extracción de las aletas para el anclaje en las vértebras.
La operación quirúrgica se realiza haciendo una incisión para el paso del dispositivo. Éste se coloca correctamente mediante un alambre guía que se estira desde el punto de inserción. Una vez posicionado el dispositivo, se aprieta con una herramienta especial, que luego se retira, junto con el alambre guía.
Aquí, Tsunami ha podido aprovechar la tecnología DMLM de GE Additive de varias maneras innovadoras. DMLM ofrece la capacidad de crear geometrías precisas, incluyendo engranajes y piezas mecánicas móviles —a muy pequeña escala— sin necesidad de ensamblaje.
“DMLM nos ayuda a lograr la precisión, complejidad e integración funcional que buscamos. También ofrece una gran calidad de superficie que reduce o a veces elimina la necesidad del típico posprocesamiento, lo que a su vez impulsa el aumento de la productividad”, dice Caselli. “El implante sale de la máquina con un ciclo de impresión optimizado de 20 unidades, sin necesidad de estructuras de soporte. Ya está completamente ensamblado y, salvo el pulido final, no requiere posprocesamiento. Ninguna otra máquina hoy en día habría sido capaz de darnos este tipo de rendimiento”, añade.
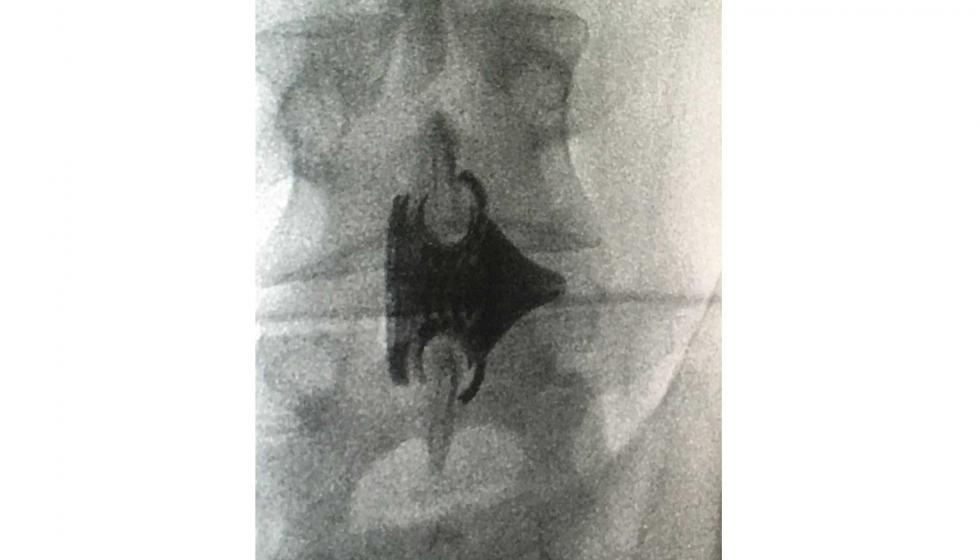
Escalado global
Con dos décadas de experiencia en el sector para construir, profundas conexiones con la comunidad médica y la próxima generación de implantes espinales de la compañía que actualmente está pasando por el proceso de regulación, el 2021 se prepara para ser otro año definitivo para Tsunami Medical.
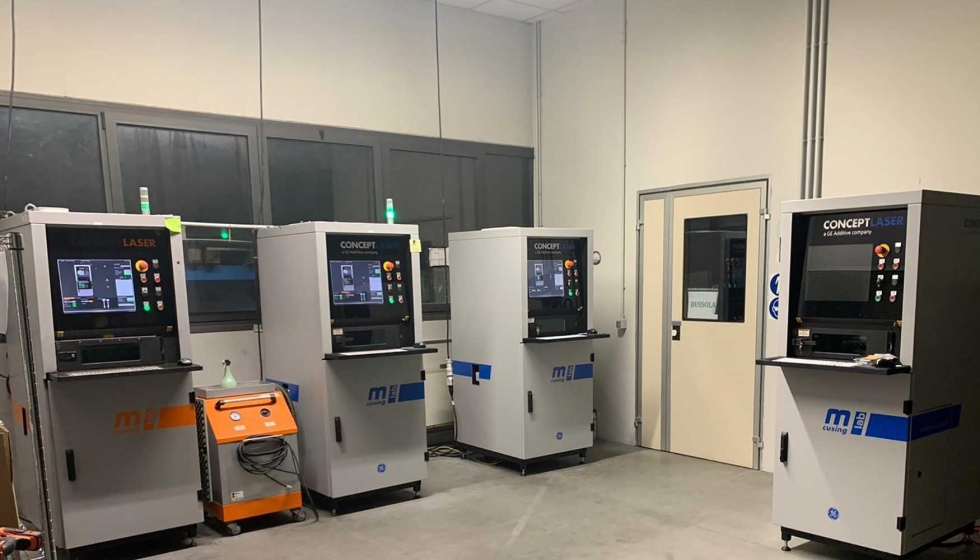