De las prótesis estandarizadas a las personalizadas gracias a la fabricación aditiva
Hasta hace pocos años sólo se disponía de prótesis estandarizadas y fabricadas convencionalmente —o en casos muy limitados prótesis personalizadas— para pacientes con tumores óseos. Hoy en día, una combinación de fabricación aditiva y de imágenes por TAC está haciendo posible la creación de prótesis verdaderamente personalizadas. A la vanguardia de esta tecnología está MT Ortho, con sede en la isla italiana de Sicilia.
Basándose en la experiencia de dos décadas en el mercado clínico-hospitalario italiano de prótesis estandarizadas, MT Ortho comenzó a adoptar la fabricación aditiva en 2014. Ese año también marcó una serie de llegadas a la compañía; un ingeniero recién graduado, Simone Di Bella, que se había especializado en la fabricación aditiva y dos máquinas de GE Additive Arcam Electron Beam Melting (EBM).
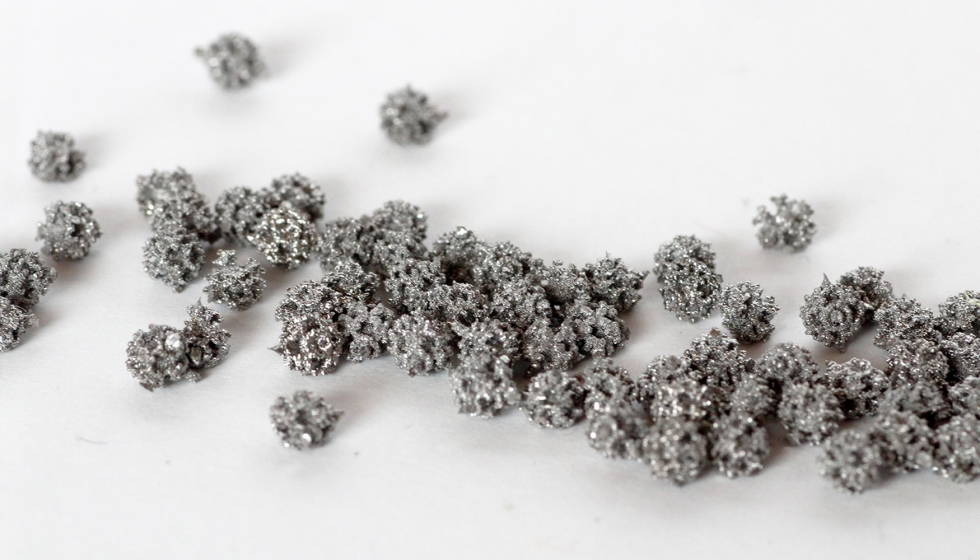
El equipo de MT Ortho se centró inicialmente en la producción de prótesis personalizadas, para aplicaciones neuroquirúrgicas (craneoplastia personalizada) y ortopedia oncológica (reconstrucción de mega prótesis). Al mismo tiempo, la empresa puso en marcha varios proyectos para obtener la marca CE europea para varios dispositivos en el ámbito de la neurocirugía.
Uno de estos proyectos incluye un trabajo innovador para desarrollar un innovador implante de cifoplastía para el tratamiento del colapso vertebral. Este dispositivo permitirá sustituir los actuales rellenos óseos, como los cementos y biocementos, por un material osteoinductivo que eliminará todos los posibles efectos negativos relacionados con la tecnología actualmente en uso.
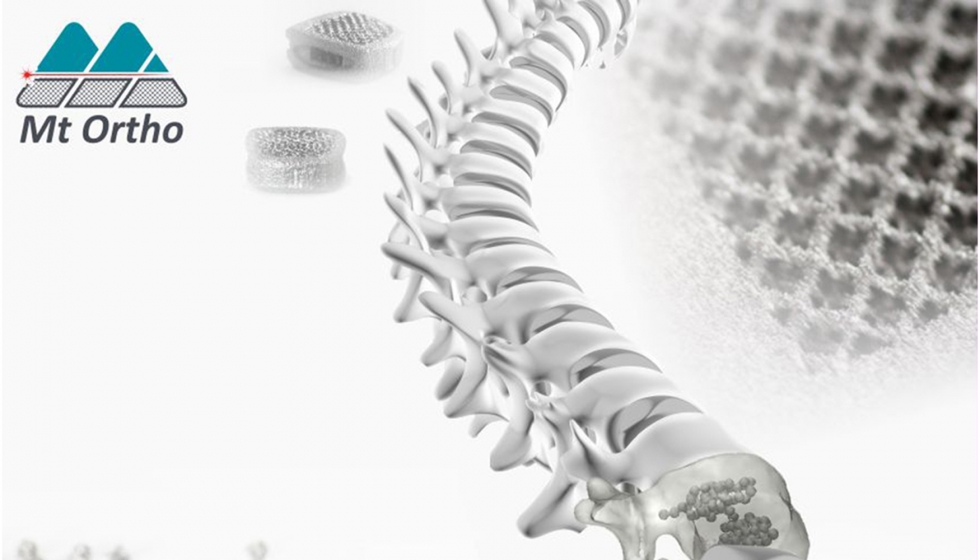
El diagnóstico por imágenes y el diseño para aditiva
Las prótesis personalizadas son dispositivos médicos diseñados exclusivamente para un paciente individual, a fin de adaptarse a su patología particular, y luego se fabrican de acuerdo con sus imágenes de diagnóstico específicas.
Este tipo de implante se utiliza principalmente cuando la geometría ósea no se encuentra dentro del rango dimensional de los implantes estándar, cuando existen requisitos especiales debido a la enfermedad, o simplemente cuando una solución a medida permite un mejor resultado clínico.
Para el uso exitoso de las prótesis personalizadas es clave la cooperación interprofesional y la comunicación entre el cirujano ortopédico y el diseñador del implante.
Es posible que el diseñador del implante no esté familiarizado con los procedimientos anatomopatológicos, epidemiológicos, quirúrgicos o de resección/reconstrucción. Mientras que, el cirujano ortopédico puede no tener una comprensión profunda del proceso de producción de un modelo físico fabricado aditivamente.
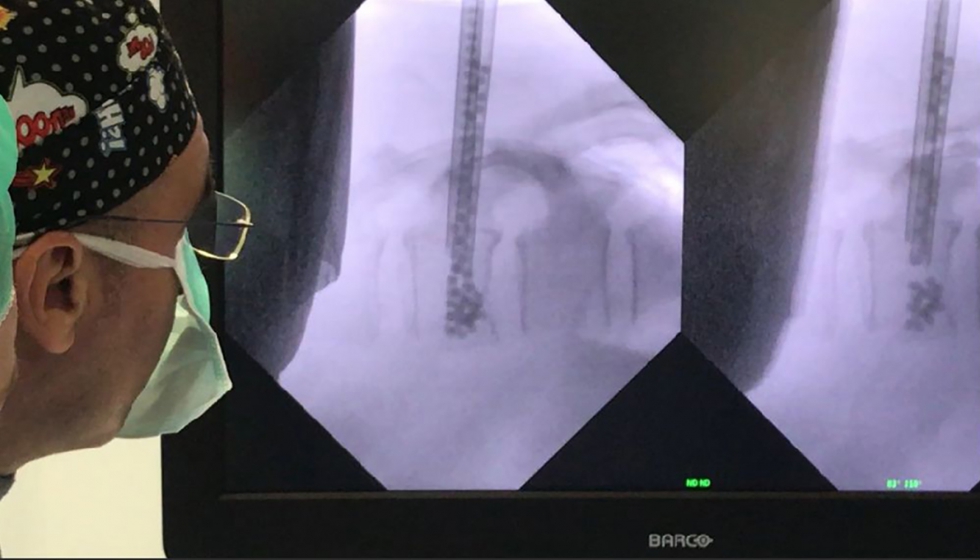
Impulsar los avances en la craneoplastia
Esto ha dado lugar al desarrollo de una nueva línea de prótesis de craneoplastia personalizada, que se utiliza actualmente en toda Europa. El uso de la tecnología de aditivos en la craneoplastia hace que el proceso de fabricación de las prótesis sea más fácil y mucho más preciso. Además, las características de la tecnología permiten lograr una estructura óptima para la osteointegración.
Y en virtud de la rapidez y precisión de la tecnología también es mucho más fácil hoy en día realizar las llamadas operaciones de demolición/reconstrucción de la craneoplastia en un solo paso.
Estas intervenciones se basan en una estrategia quirúrgica completamente diferente, que permite la planificación más precisa de la intervención, para lo cual MT Ortho proporciona no sólo la prótesis, sino también las plantillas de corte, siguiendo el mapeo preciso del área de intervención por medio de una tomografía computarizada.
En la cirugía, la extracción del área afectada por la enfermedad y la inserción de la prótesis craneal pueden tener lugar simultáneamente, reduciendo drásticamente el tiempo de hospitalización y recuperación postoperatoria y el riesgo de infección. Esto es particularmente importante para las intervenciones en zonas sensibles como la órbita ocular o la región craneomaxilofacial.
Fabricación aditiva de prótesis personalizadas
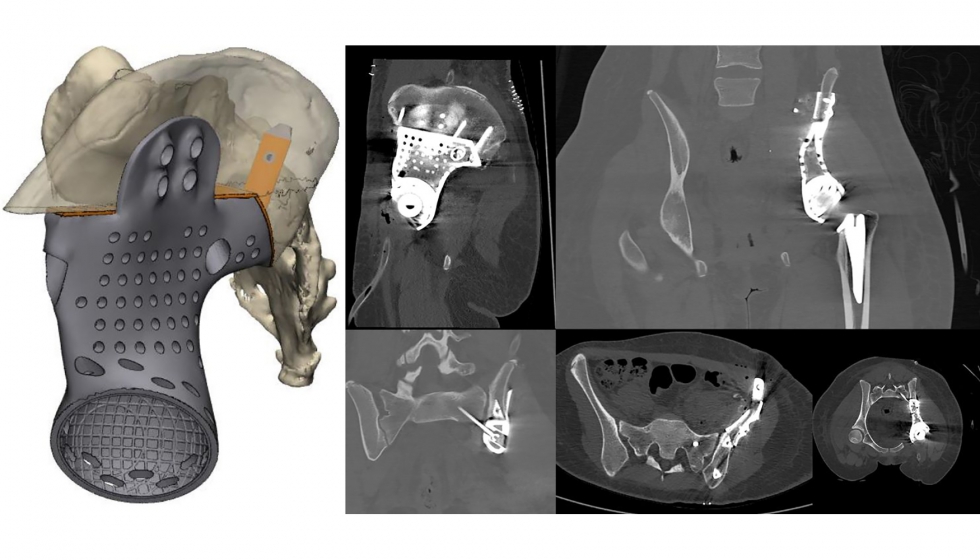
Desde el principio, este proceso requiere una estrecha colaboración entre el cirujano responsable del procedimiento y el equipo de ingeniería de MT Ortho.
El primer paso es una tomografía computarizada, con el fin de hacer posible la construcción de un modelo 3D de las características anatómicas específicas del paciente.
- A continuación se realiza una conferencia telefónica con el médico, donde se discute la intervención y se identifican las vías de acceso.
- A continuación, los diseñadores determinan las características de los sistemas de fijación, teniendo en cuenta la resistencia del material.
- Se diseña la prótesis, y luego se revisa con el cirujano, para todos los aspectos de viabilidad.
- Finalmente, la prótesis se imprime, a menudo con una copia de seguridad, para apoyar cualquier evento o problema inesperado. Por lo general, la prótesis no requiere ningún tratamiento posterior especial, salvo el lavado y la esterilización final, que puede tener lugar en la fuente o en un autoclave en el hospital de destino.
- Los especialistas en productos ortopédicos de MT Ortho a veces están presentes en el quirófano durante la cirugía y ayudan al cirujano con la colocación adecuada.

Soluciones a medida para pacientes con cáncer de huesos
La plena libertad de diseño que ofrece la tecnología aditiva permite la fabricación de prótesis personalizadas que tienen en cuenta la deformación y la necesidad de distribuir adecuadamente las cargas.
Una de las áreas de especialización desarrolladas por MT Ortho es la prótesis para el cáncer, para sarcomas óseos o condrosarcomas.
Mediante el uso de tecnologías aditivas, es posible reconstruir perfectamente la anatomía ósea de los pacientes después de una cirugía de demolición realizada para la extirpación de un tumor.
Esta área de especialización ha tenido un éxito especial gracias a la colaboración con el Departamento de Ortopedia Oncológica del Instituto Nacional del Cáncer Regina Elena de Roma (IRE), donde MT Ortho está logrando resultados alentadores de la intervención. Esta colaboración está llevando a la empresa a ampliar aún más sus servicios para incluir ayudas quirúrgicas, como guías de corte y posicionamiento de precisión de las prótesis.
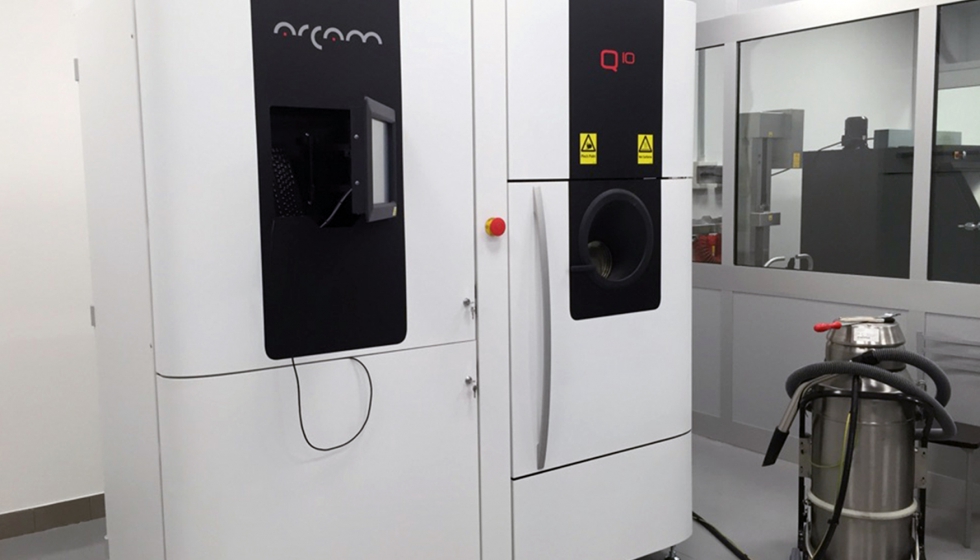
Consideraciones sobre el coste
Teniendo en cuenta los tiempos de hospitalización más cortos y los resultados más eficaces, el estudio mostró un ahorro global de costes del 13% cuando se utilizaron prótesis personalizadas en el campo de la oncología.
Dado que el estudio suponía una estancia postoperatoria media de cuatro a cinco días en el caso de las prótesis personalizadas, en comparación con una media de siete a diez días en el caso de las prótesis estandarizadas, sin mencionar la necesidad de disponer de un gran stock de tamaños y materiales.
Y dado que la hospitalización es una de las mayores cargas de costes del sistema sanitario, si se añade el ahorro de tiempo para el personal de quirófano y de quirófano, el presupuesto final es decididamente favorable a las prótesis personalizadas.