Estos son los materiales en los que se puede imprimir en 3D
Los plásticos son los materiales más comunes dentro de la impresión 3D. Filamentos, resinas líquidas, poliamidas, etcétera, cuentan con cualidades diferentes y, por tanto, se utilizan para soluciones distintas. Y, además, no han dejado de desarrollarse para mejorar sus prestaciones.
Se cumple un año desde que HP lanzara la nueva impresora 3D HP Jet Fusion serie 5200, diseñada para optimizar las necesidades de fabricación al proporcionar alta calidad, precisión, repetitibilidad, eficiencia, flexibilidad y mayor capacidad de procesar con éxito en términos de requisitos de piezas y especificaciones técnicas. Un equipo que incorpora nuevos materiales, incluido el TPU Ultrasint desarrollado por BASF, que ofrece la oportunidad de trabajar a alta temperatura y la obtención de piezas flexibles.
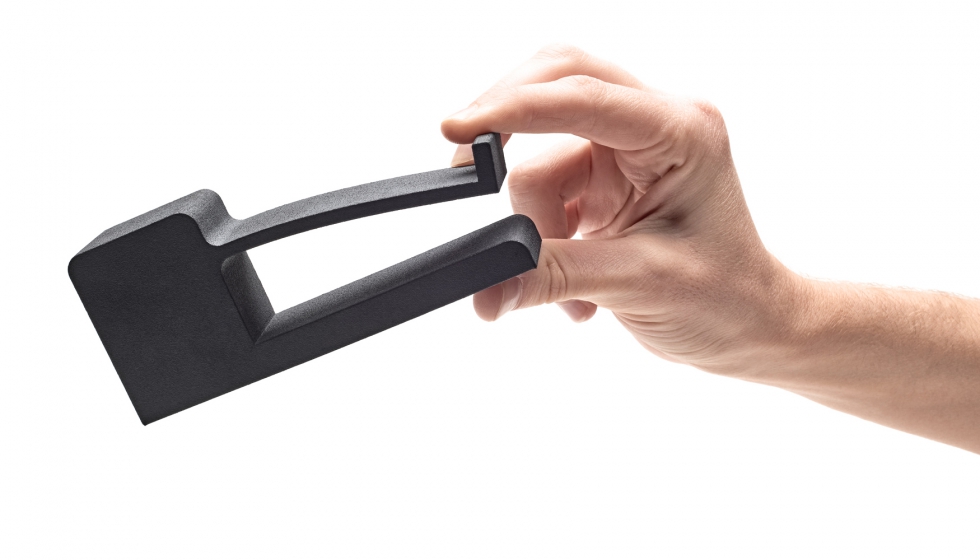
Pieza desarrollada con material flexible.
La innovación constante es la seña de identidad de la tecnología de fabricación aditiva, y muchas empresas punteras como el fabricante de automóviles Land Rover o el diseñador de aerogeneradores Vesta ya la utilizan para aprovecharse, precisamente, de sus avances. También en términos de materiales. No en vano, estas dos empresas son algunas de las organizaciones que ya utilizan la nueva impresora 3D de HP, la Jet Fusion 5200.
El TPU que utiliza el nuevo equipo 3D de HP “es un termoplástico que permite la creación de piezas flexibles y también rígidas, dimensionalmente estables, funcionales y de alta calidad, capaz de resistir fuerzas de compresión y tracción mucho mayores que sus homólogos más comunes, el PLA y el ABS”, explica José María Ferrándiz, director de la Línea de Negocio 3D de Grupo Solitium. “Un material que nos da la oportunidad de fabricar objetos que pueden estirarse, doblarse y retorcerse”, añade.
La innovación en los materiales va ligada a los equipos que pueden manejarlos. Y, en este sentido, la firma HP no ha parado de investigar para poder ampliar su catálogo e incluir componentes que mejoren las opciones de color y acabados e incrementen el número de aplicaciones.
Así, los equipos de HP trabajan en la actualidad con polímeros termoplásticos PA12 y PA11 (poliamidas), que permiten la producción de piezas funcionales, dúctiles y resistentes como prótesis, plantillas, artículos deportivos, broches de presión, bisagras, ensamblajes complejos, carcasas, cajas y aplicaciones herméticas pues proporcionan el mejor equilibrio entre las propiedades mecánicas y la reusabilidad y cuentan con certificaciones de biocompatibilidad (en el caso de la PA12). En el catálogo de materiales de esta firma también se incluyen sendas variantes de PA12, una reforzada con microesferas de vidrio, y otra que ofrece la opción de color y se usa en la serie 500; y acaba de incorporar el PP (polipropileno) y el TPU (poliuretano termoplástico) de dos fabricantes: BASF en el caso del Ultrasint, y Lubrizol con el Estane.
“HP trabaja con fabricantes de materiales en una plataforma abierta de desarrollo a la que, progresivamente y en función del avance y la mejora de las capacidades de los equipos, se van incorporando nuevas familias de producto”, apunta Miguel Ángel Mora, ingeniero responsable de los Servicios de Ingeniería 3D de Grupo Solitium. “De igual manera”, continúa Mora, “hay compañías especializadas en tratamiento y acabado de superficies, como Dyemansion, que, a partir de julio, ofrecerán sus equipos de tratamiento y tintado de piezas de PA12 de las series 4000 y 5000 de HP en 17 colores estándar”.
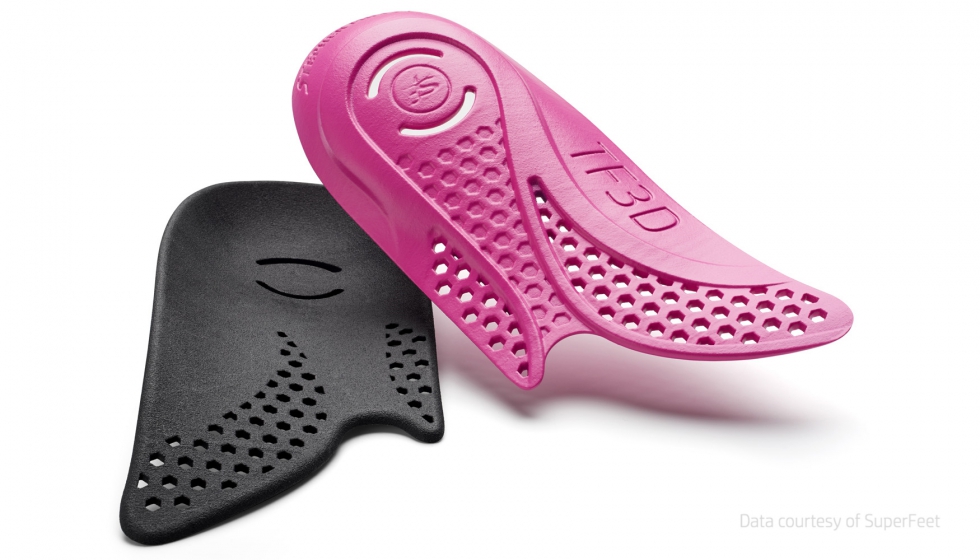
Pieza hecha de material resina. Créditos: Superfeed.
Otras tecnologías
La tecnología Jet Fusion es una de las que más fuerte está pegando en el mercado en términos industriales, pero no es la única en fabricación aditiva. Y en cada caso, el uso de materiales es distinto. Así, mientras HP utiliza principalmente poliamidas para su tecnología de fusión en polvo, otras como Formlabs, usa resina como su principal componente. Esta firma utiliza la estereolitografía como herramienta para, a través de un rayo láser, endurecer la resina y conseguir la pieza o el prototipo deseado. Y es que los equipos de esta marca están pensados para producir piezas calcinables, de alta precisión e incluso biocompatibles, y ofrecen un software sencillo que la convierten en la mejor solución para aquellos profesionales que quieren aplicar la impresión 3D como fuente de innovación en su negocio sin la necesidad de unos conocimientos profundos.
Los equipos que emplean este tipo de material, “suelen emplear resinas de base epoxi, poliuretanos y siliconas con un gran avance en los últimos años gracias a las tecnologías CLIP”, asegura Ferrándiz.
También hay tecnologías de impresión 3D que utilizan los filamentos, “termoplásticos industriales estándar como el ABS, el PLA, el Nylon, el PET, etcétera, y, en función del tipo de equipo también se pueden emplear termoplásticos de mayor temperatura para aplicaciones más exigentes, tipo PA-Carbon, PA6, Peek…”, recuerda el director de la Línea de Negocio 3D de Grupo Solitium.
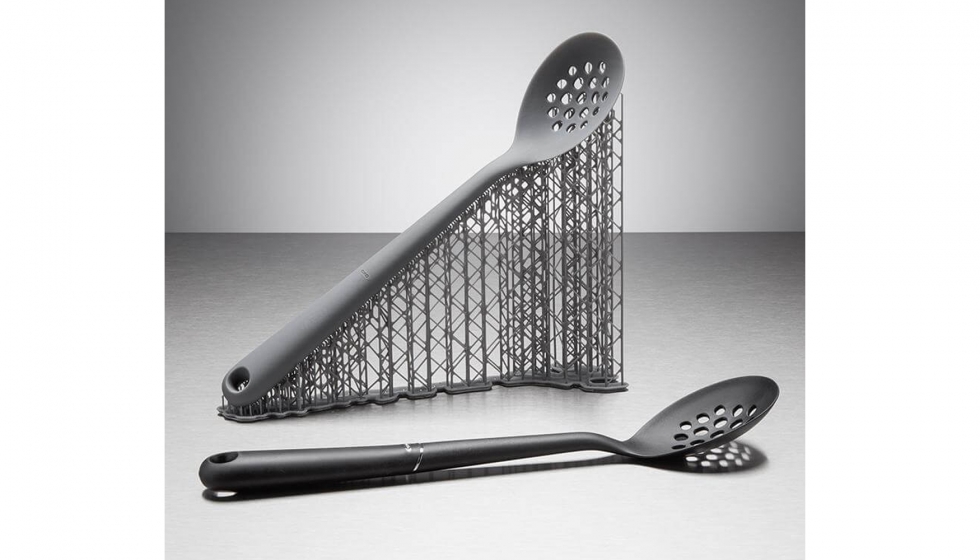
Ejemplo de material poliamida en negro y en color.
Más innovación
El uso de materiales en la impresión 3D depende del tipo de aplicaciones para las que se utilicen. La fabricación aditiva lleva años demostrando su capacidad de revolucionar la producción en muchos sectores. También en el médico, “en el que ha habido un gran progreso en término de materiales al conseguirse los llamados materiales biomédicos, biocompatibles, que permiten el desarrollo de esta tecnología en este sector”, asegura Ferrándiz.
Los nanomateriales y los metales también se están investigando. No en vano, “cabe destacar el desarrollo del primer equipo MetalJet de HP, basado en la tecnología de inyección de aglutinante (Binder Jetting) que, esperamos, pueda presentar en aproximadamente más de año y medio a falta de confirmación oficial por parte del fabricante, y que transformará la fabricación en metal como lo están haciendo ya sus equipos en plástico”, cuenta Mora.
“Tampoco hay que olvidar que HP lleva tiempo trabajando en su proyecto de lograr actuar sobre los materiales a nivel vóxel gracias a distintos agentes”, recuerda Miguel Ángel Mora, ingeniero responsable de los Servicios de Ingeniería 3D de Grupo Solitium. “Lo que busca esta compañía con la tecnología Jet Fusion”, explica Mora, “es que sus equipos lleguen a controlar la fabricación de piezas, modificando propiedades concretas de materiales y haciéndolos interactuar con agentes específicos. Incorporando, por ejemplo, aditivos para lograr mejores propiedades mecánicas, partículas metálicas para poder diseñar e integrar elementos conductores de señales eléctricas, etcétera”. Unos avances que llegarán en el largo plazo.
En el fondo, el desarrollo y la investigación en materiales que se está llevando a cabo en Impresión 3D trata de equiparar las prestaciones de éstos con los de la fabricación tradicional, “para lograr capacidades ignífugas, homologaciones para alimentación, certificaciones militares y aeronáuticas, etcétera”, sostiene el director de Negocio 3D de Grupo Solitium, “para que la innovación no pare”.