El paso del prototipo a prototipo funcional o pieza de serie supone un impulso en la actividad investigadora en nuevos materiales para estas tecnologías para las que hay que diseñar materiales específicos
El reto de la ingeniería de materiales en la impresión 3D
Laura Marín Perales, miembro del Comité Certificación Fabricación Aditiva de Cesol,
María Sierra Aramburu, especialista en Procesos Especiales de Fabricación y Fabricación Aditiva
13/05/2020Los materiales dentro de la impresión 3D han sido los grandes olvidados hasta hace unos años. El paso del prototipo a prototipo funcional o pieza de serie ha supuesto un impulso en la actividad investigadora en nuevos materiales para estas tecnologías que suponen un nuevo método de producción para el que hay que diseñar materiales específicos para acercarnos a las propiedades de las piezas fabricadas por métodos tradicionales.
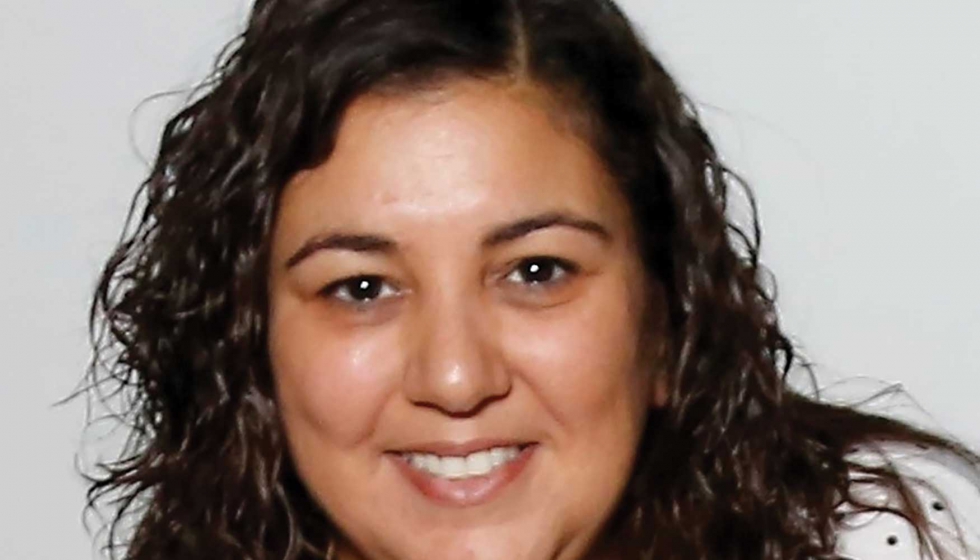
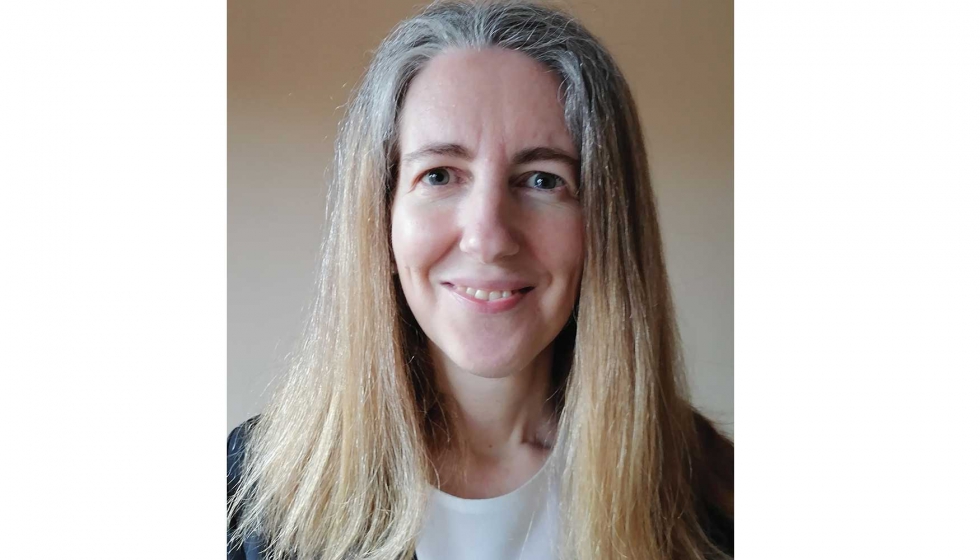
La anisotropía, la defectología y la rugosidad son los principales factores que se deben tener en cuenta al abordar el diseño de piezas que van a fabricarse usando esta tecnología.
La anisotropía no se manifiesta sólo en la miscroestructura a escala de grano (y por tanto en las propiedades mecánicas y químicas) sino también en la textura del material y por tanto en propiedades físicas como el módulo elástico. Es por ello que el diseño tiene que tener en consideración el método de fabricación aditiva incluso a nivel de máquina y la orientación de la pieza en la cámara.
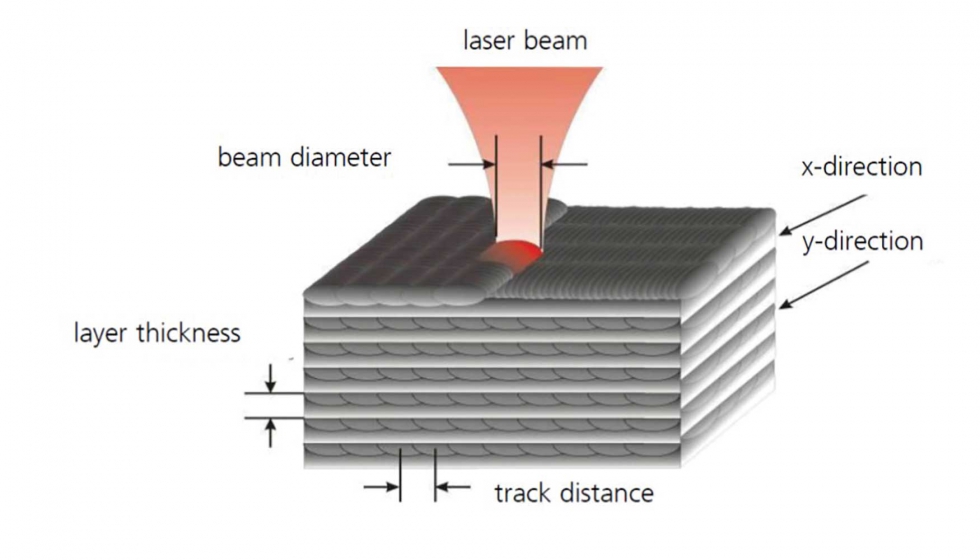
Las piezas solicitadas y sometidas a fatiga son las que se ven afectada su resistencia por la presencia de defectología y por la rugosidad superficial.
Este proceso de fabricación produce una elevada rugosidad en superficies con orientaciones no favorables a la dirección de crecimiento. Piezas que requieran superficies de acabado fino o con secciones solicitadas a fatiga requieren un posprocesado o que desde el diseño se considere la reducción de propiedades a fatiga asociada a esta característica. Hay que tener en cuenta la dificultad de realizar acabados en ciertas superficies internas, habituales en muchas geometrías complejas que son de interés para la impresión 3D. El uso de flujos abrasivos o acabados mediante procesos químicos se está implantando ya en la industria.
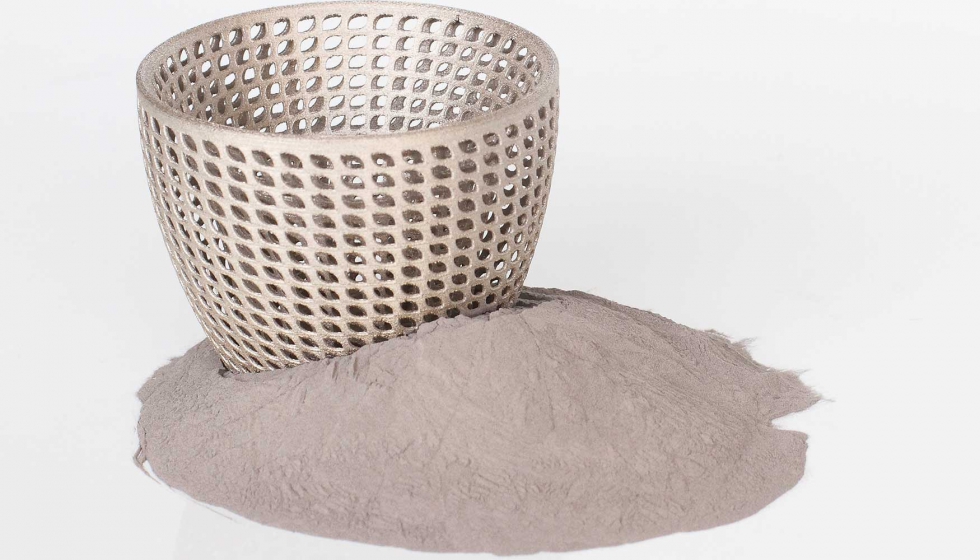
Las propiedades mecánicas (límite elástico y tensión última de rotura) son comparables a las de material forjado y superiores a las de material de fundición. Las piezas solicitadas y sometidas a fatiga son las que se ven afectada su resistencia por la presencia de defectología y por la rugosidad superficial. La resistencia en ambientes corrosivos también se puede ver comprometida por estas características. Este tipo de componentes requieren por tanto un estricto control del proceso de fabricación y del producto final.
Además, imprime al material una porosidad que no existe los métodos de fabricación tradicional, que va en detrimento de sus propiedades mecánicas sobre todo las referentes a la elasticidad del material (elongación a rotura, elongación yield).
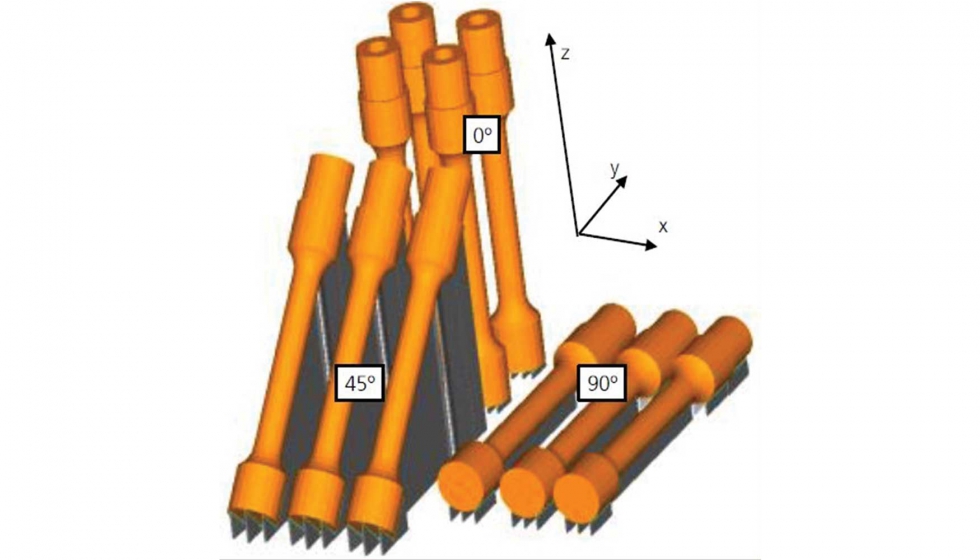
Por si esto no fuera suficiente hay tres tecnologías para plásticos donde los materiales se comportan de forma distinta:
- SLA: materiales poliméricos que fotopolimerizan, es decir, que forman su cadena polimérica por acción del haz UV de la máquina, muy buenas propiedades estéticas. Materiales muy tenaces, frágiles y nada elásticos.
- SLS: la técnica láser para polímeros, para materiales semicristalinos, los materiales amorfos no se comportan bien en esta técnica, esto hace que la gama de materiales poliméricos en esta técnica sea reducida, fundamentalmente PA12 y compuestos. Si indagamos un poco, en este material vemos que en el consumo mundial apenas el 0,02 % de los materiales plásticos y hay una ausencia casi nula de materiales tradicionales como el polipropileno, polietileno etc… En esta técnica a parte de la escasez de materiales, nos enfrentamos igualmente a la anisotropía de las propiedades de la pieza final, la rugosidad debida igualmente a la fabricación capa a capa. Otro aspecto a tener en cuenta en el aspecto estético es la monocromía de las piezas que fabricamos, incluso en un tratamiento posterior de coloración.
-
FDM: la técnica más comodity de todas, basada en la fusión del polímero, fundamentalmente para polímeros amorfos o de muy baja cristalinidad. Al igual que en la anterior y si cabe más acusado por ser una técnica mucho más lenta, se produce anisotropía en la pieza fabricada, porosidad y rugosidad. Es la única de las técnicas de impresión 3D que tiene una gama de materiales muy amplia pero que sus propiedades no van más allá del prototipado.
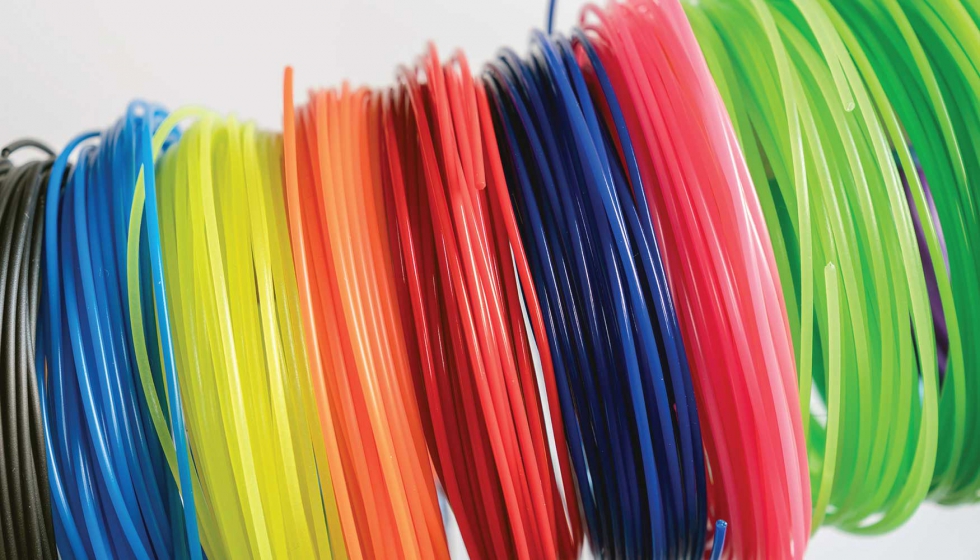