El diseño de la mascarilla optimiza la ergonomía, respirabilidad y biocompatibilidad en el contacto con la piel de los modelos ya existentes
El CIM UPC libera una mascarilla de uso general para imprimir en 3D
El CIM UPC ha liberado una mascarilla de uso general que lleva al límite la impresión 3D para obtener máxima comodidad y seguridad. La mascarilla diseñada por el CIM UPC se puede fabricar en cualquier impresora SLS, SLA o MJF y puede ser usada con cualquier tipo de tela homologada. Además, ha sido creada para poder reutilizarse y, gracias a una estructura específicamente diseñada para sacar el máximo partido del Additive Manufacturing en su proceso de fabricación, es mucho más cómoda y estanca que los modelos existentes en la red. Actualmente se encuentra en proceso de homologación.
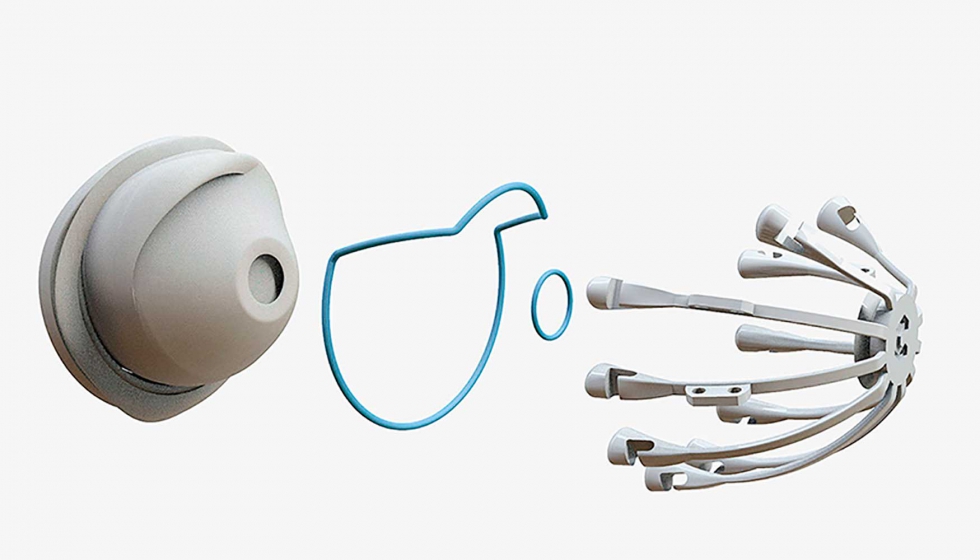
En cuestión de días, aparecieron los primeros diseños de mascarillas, respiradores y protecciones diversas compartidos en la red, con el principal objetivo de ser rápida y fácilmente reproducibles mediante tecnología FFF (Fabricación por Filamento Fundido), y empezó una producción colaborativa masiva. En este contexto, la impresión 3D se consolidó indudablemente como una solución de primer nivel a la incapacidad de abastecimiento de estas herramientas.
Con el avance de la lucha contra el coronavirus, y basándose en opiniones y críticas recogidas por parte de los medios de comunicación, sanitarios y otros usuarios de las mascarillas, fueron detectándose aspectos seriamente mejorables en lo que al material y diseño se refería. El CIM UPC, centro tecnológico de referencia en fabricación aditiva de la Universitat Politècnica de Catalunya, emprende entonces un nuevo proyecto para trabajar de forma intensiva en el desarrollo de estos EPI. Se plantean principalmente tres retos a optimizar, a partir de los diseños existentes en la red: ergonomía, respirabilidad y biocompatibilidad en el contacto con la piel.
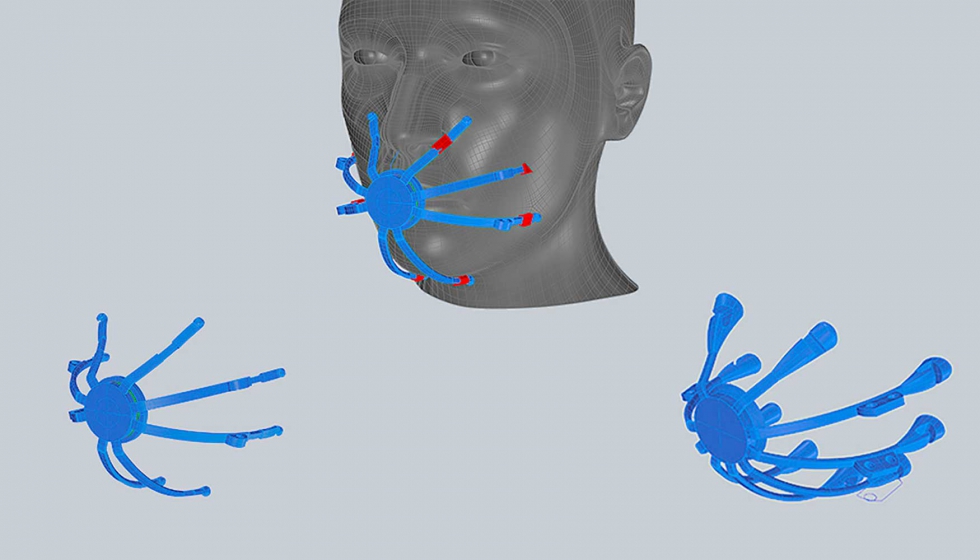
Estos atributos fueron posibles gracias a la tecnología SLS (Sinterizado selectivo por láser), cuyo sistema de fabricación 3D aporta al prototipo gran flexibilidad, pudiéndose fabricar geometrías muy complejas que no podrían materializarse mediante ningún otro método. De hecho, esta tecnología revolucionó en su momento el mundo de la impresión 3D, ofreciendo la posibilidad no solo de realizar prototipos para validaciones de diseño o ensayos sino también para la producción de piezas finales de alta calidad o preseries cortas, lo cual la convirtió en la opción más adecuada para el caso que nos ocupa. El material usado fue poliamida (PA12), un plástico técnico muy utilizado en piezas industriales de elevadas prestaciones.
Finalmente pero no menos importante, se plantea el reto de poder ofrecer un producto para proteger el rostro que no provocara molestia, irritación o incomodidad en el contacto con la piel. Primeramente se apreció que no todos los materiales disponibles para la fabricación aditiva cuentan con el grado de biocompatibilidad y capacidad de esterilización requeridos para la utilización en contacto directo con la piel, además de tener la capacidad para ser fabricados garantizando un acabado suficientemente suave y/o cómodo para su utilización en una zona tan sensible como el rostro.
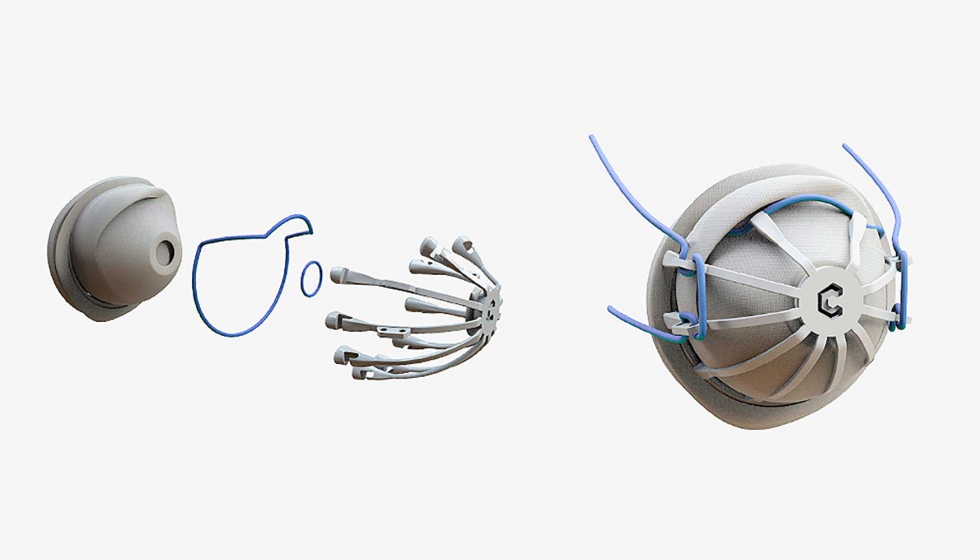
En consecuencia, se procedió a adaptar el presente diseño mediante un concepto de mascarilla esqueleto, en el interior del cual se coloca la tela filtrante, con unas sujeciones en las puntas de las varillas que permitieran acoplar internamente la tela con un elástico y externamente en cada uno de los extremos de la estructura, a lo largo del perímetro de la mascarilla. De ese modo, el diseño quedaba completo garantizando que pudiera usarse cómodamente sin desgaste durante todo su ciclo de vida.
Para poder completar el proyecto, el CIM UPC se propuso generar ciertas sinergias estratégicas con los agentes expertos en el tejido filtrante de la mascarilla, y por ello se contó con la colaboración del Clúster de Materiales Avanzados, en el cual participa activamente la Universitat Politècnica de Catalunya (CIT UPC), y de Texsilk de Sant Salvador de Guardiola, que facilitó una muestra de tela apta para los requerimientos de la mascarilla. El tejido original sirve habitualmente para productos como parasoles de jardín, preparados para duras condiciones ambientales, y resulta perfecto para un uso inesperado como las mascarillas.
En cuanto a su producción, una vez optimizado el producto para que se pueda fabricar a gran escala con las principales tecnologías de impresión 3D, el CIM UPC prevé fabricar mediante tecnología SLS 140 mascarillas a la semana. En el caso de utilizar la tecnología MJF, se podrían fabricar hasta 36 máscaras cada 8 horas.
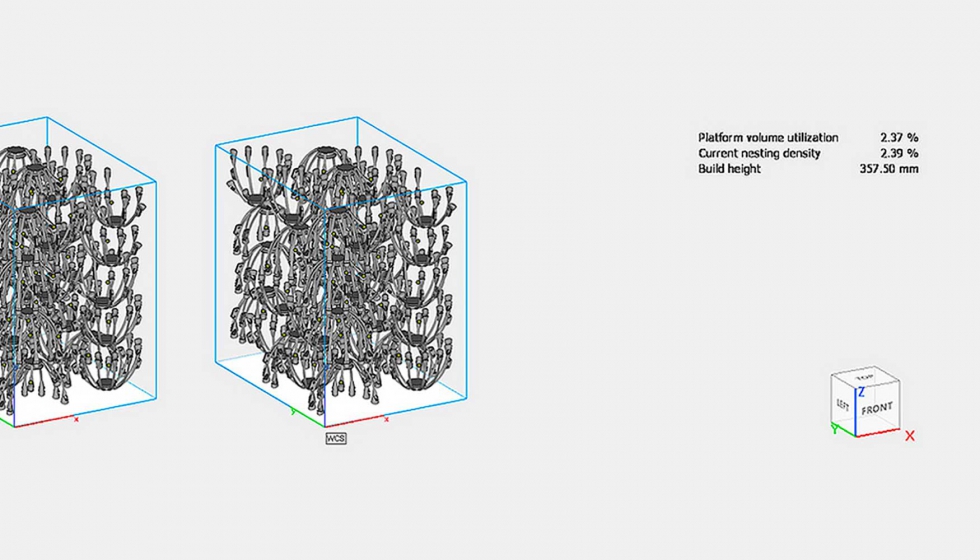
De forma acelerada se están abordando los pasos para poder verla convertida en un nuevo estándar que ayude a superar la crisis. De hecho, entre estos pasos, encontramos una fase de optimización del actual diseño aún por perfeccionar puesto que, a pesar de estar basado en opiniones y críticas de usuarios de otro tipo de mascarillas, es una primera versión. Como en el caso de los respiradores, la homologación es un paso obligado y hay también entidades en la UPC, como el grupo Intertex que están aportando su conocimiento respecto a los requerimientos de las mascarillas reutilizables.
Instrucciones de montaje
La liberación de esta primera versión de la nueva máscara, que puede ser descargada tanto para su uso como para ser modificada adaptándose a un ámbito de aplicación más concreto, se añade al Arm Door Opener como herramienta para reducir el factor RO (?) de contagio, otro elemento open source desarrollado en el CIM UPC y que ya se puede descargar libremente sin limitaciones, como corresponde al paradigma de la Industria 4.0.