El caso de Volkswagen Autoeuropa ilustra cómo la impresión 3D puede ser de gran valor para la industria
Volkswagen: herramientas 3D para optimizar costes
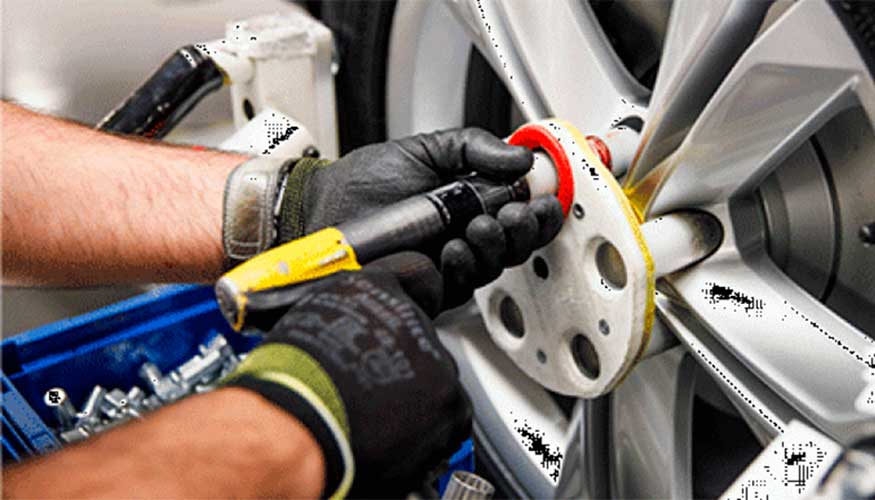
Mediante el uso de herramientas, plantillas y accesorios impresos en 3D, Volkswagen Autoeuropa reduce el tiempo fabricación, mejora la ergonomía de la herramienta y reduce a una décima parte el coste habitual.
Mediante el uso de herramientas, plantillas y accesorios impresos en 3D, Volkswagen Autoeuropa, que es responsable de la fabricación de modelos emblemáticos de Volkswagen como el Scirocco y Sharan, reduce el tiempo fabricación, la mano de obra y la necesidad de volver a trabajar, a la vez que mejora la ergonomía de la herramienta y reduce a una décima parte el coste habitual.
A pesar de contar con maquinaria de vanguardia y robots de fabricación industrial que pueden costar millones de euros, la mayoría de las plantas de ensamblaje automotriz subcontratan la fabricación de herramientas y prototipos personalizados a un tercero.
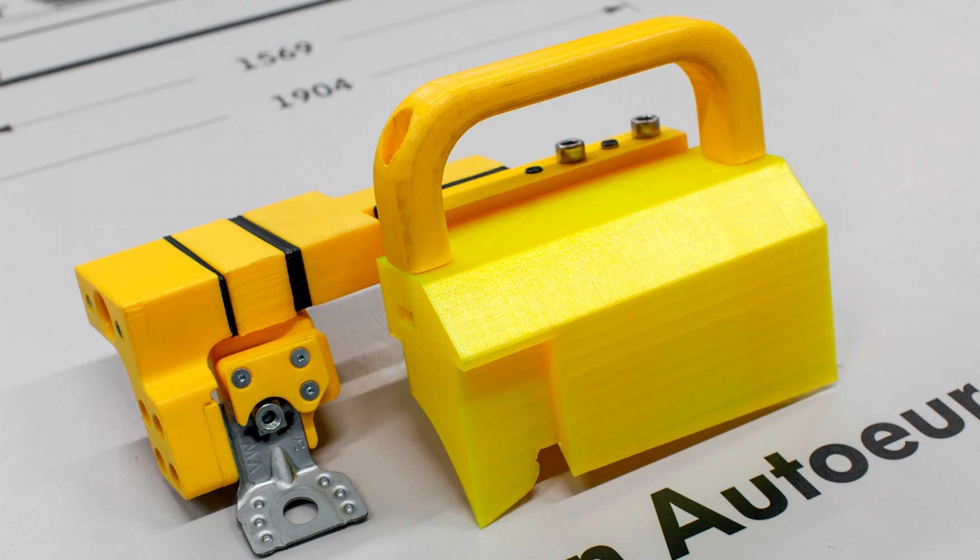
Volkswagen Autoeuropa era una de esas plantas de ensamblaje automotriz, pero al utilizar la impresión 3D, ha podido mover la fabricación de herramientas y prototipos personalizados internamente para reducir los costes y mejorar la producción.
Volkswagen Autoeuropa decidió prescindir de terceros y apostar por la impresión 3D con el fin de lograr dos objetivos principales: reducir el coste por pieza y reducir el tiempo de desarrollo de la herramienta.
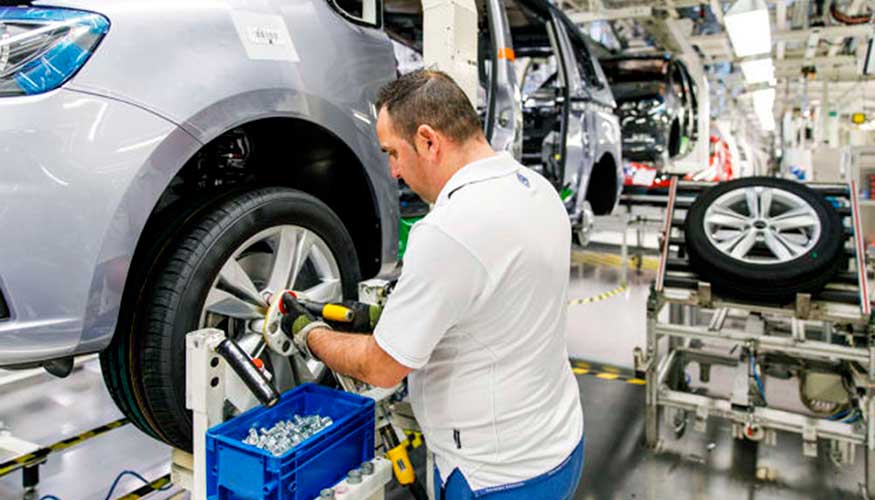
Como hemos indicado al comienzo, se logró una reducción de costes del 91% mediante la impresión 3D de sus propias piezas en comparación con la contratación de un tercero. También ahorraron un 95% de tiempo, lo que permitió al equipo concentrarse en tareas más importantes.
En términos de ahorro de costes, cuando se utilizaba terceros para fabricar un dispositivo de protección de ruedas Poka-Yoke, el coste promedio por pieza era de 800 € y su fabricación tardaba 56 días. Al usar las impresoras 3D, el coste promedio por pieza es de 21 € y la fabricación requiere solo 10 días. Fabricar un dispositivo de insignia de compuerta levadiza, le costaría a Volkswagen Autoeuropa 400 € con un tercero, pero solo cuesta 10 € fabricándolo con la tecnología FDM.
“Además del ahorro de tiempo y costes, las herramientas que generamos son más complejas y ergonómicas, y, en última instancia, mucho más útiles en nuestras operaciones diarias porque se adaptan a nuestras necesidades”, comenta Luis Pascoa de Volkswagen Autoeuropa.
La planta de Volkswagen Autoeuropa emplea a 4.000 personas. El año pasado, la instalación 3D imprimió aproximadamente 1.000 piezas. Calcula que ahorró 160.000 $ en 2016 gracias a la integración de la impresión 3D (también obtuvo el 100% de retorno de la inversión solo dos meses después de instalar las impresoras), y espera haber aumentado sus ahorros a 200.000 $ en 2017.
En otras palabras, la tecnología de impresión en 3D se ha integrado sin problemas en las operaciones de la instalación con una pequeña inversión inicial, escalabilidad simple y una curva de aprendizaje nada empinada para los trabajadores.
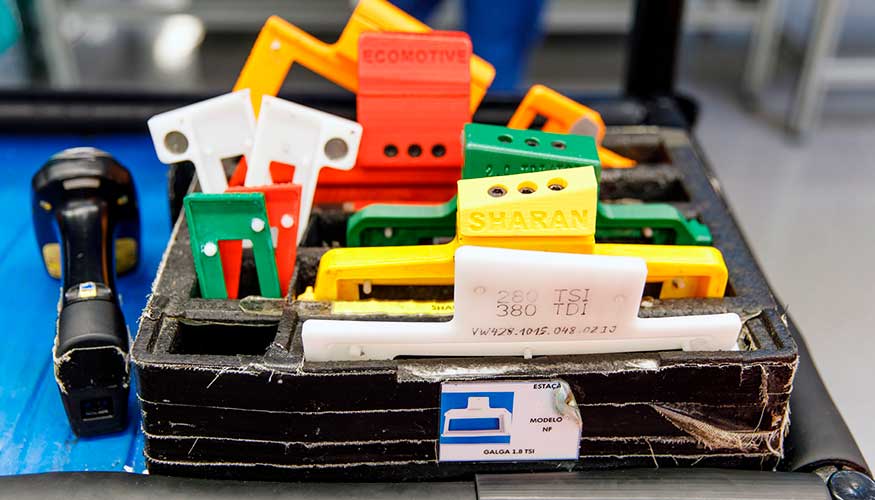
El año pasado, la instalación 3D imprimió aproximadamente 1.000 piezas y calcula que ahorró 160.000 $ en 2016.
Al producir las herramientas internamente, se puede omitir el departamento de compras y se tiene la capacidad de desarrollar ideas para herramientas nuevas o mejoradas junto con los operadores, cosa impensable anteriormente.
Se puede imprimir una nueva herramienta durante la noche, y a la mañana siguiente los operadores la prueban en la línea de montaje. Sus comentarios se pueden incorporar en iteraciones de diseño consecutivas hasta que se haga la herramienta perfecta y esta herramienta se puede imprimir tantas veces como sea necesario y a un coste muy bajo.
Sorprendentemente, las impresoras 3D que se utilizan no son máquinas industriales sino impresoras 3D de sobremesa Ultimaker, del mismo tipo que la Entresd Up Box+.
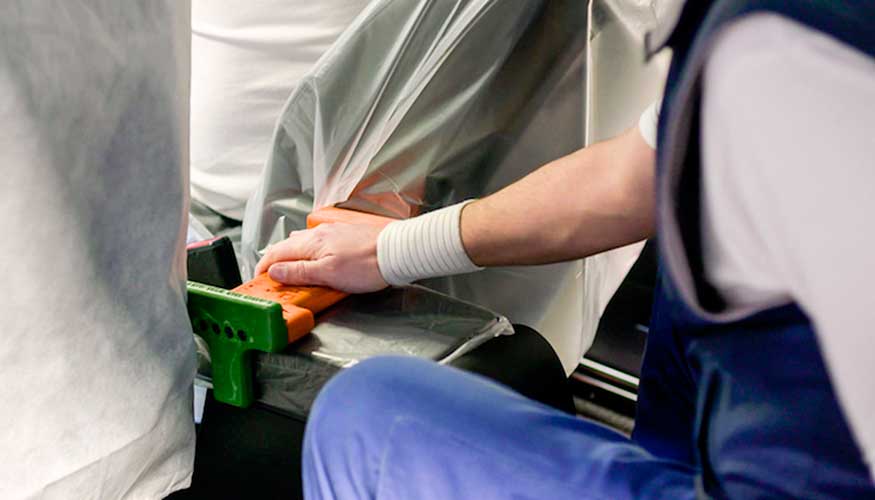