Investigadores del LLNL-Lawrence Livermore National Laboratory (California) logran un gran avance en fabricación aditiva metálica
Acero inoxidable de grado marino 316L impreso en 3D
Investigadores del Laboratorio Nacional Lawrence Livermore (LLNL), junto con colaboradores del Ames National Laboratory, la Universidad de Georgia Tech, y la Universidad Estatal de Oregon han logrado un gran avance en la impresión en 3D de una de las formas más comunes de acero inoxidable de grado marino —un tipo de bajo carbono llamado 316L— que promete una combinación sin igual de propiedades de alta resistencia y alta ductilidad para esta aleación omnipresente. La investigación aparece en la versión online de la revista Nature Materials el 30 de octubre.
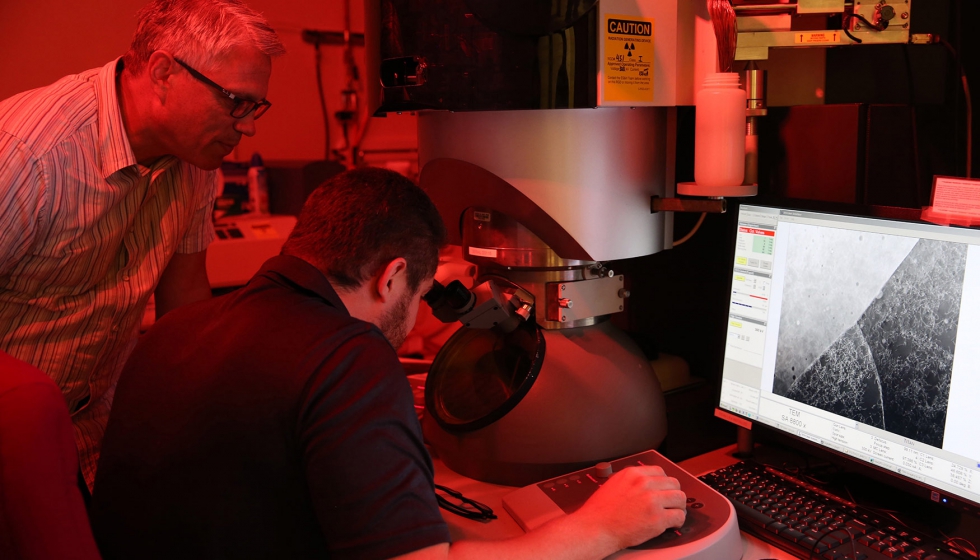
El científico de materiales de LLNL, Joe McKeown, observa a Thomas Voisin, investigador de posdoctorado, que examina una muestra de acero inoxidable impreso en 3D. Foto: Kate Hunts / LLNL.
“Para poder hacer que todos los componentes que intentamos imprimir sean útiles, debe tener esta propiedad de material al menos igual a la de la metalurgia tradicional”, dijo el científico de materiales de LLNL y autor principal del trabajo Morris Wang. “Pudimos imprimir en 3D componentes reales en el laboratorio con acero inoxidable 316L, y el rendimiento del material fue en realidad mejor que los fabricados con el enfoque tradicional. Es un gran salto. Hace que la fabricación aditiva sea muy atractiva y llena un hueco importante”.
Wang afirma que la metodología podría abrir las compuertas a la impresión 3D generalizada de dichos componentes de acero inoxidable, particularmente en las industrias aeroespacial, automotriz, petrolera y gas, donde se necesitan materiales fuertes y resistentes para tolerar la fuerza extrema en entornos hostiles difíciles.
Para cumplir con éxito, y superar, los requisitos de rendimiento necesarios para el acero inoxidable 316L, los investigadores primero tuvieron que superar un importante cuello de botella limitando el potencial para la impresión en 3D de metales de alta calidad, la porosidad causada durante la fusión láser (o fusión) de polvos metálicos que puede causar que las piezas se degraden y fracturen fácilmente. Los investigadores abordaron esto a través de un proceso de optimización de la densidad que incluía experimentos y modelado por ordenador y manipulando la microestructura subyacente de los materiales.
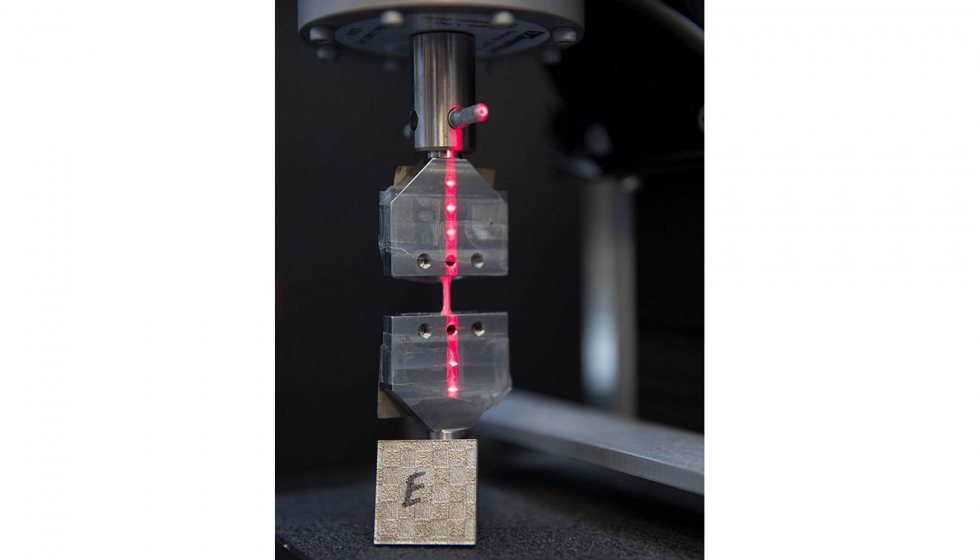
Los investigadores dicen que la capacidad de imprimir en 3D acero inoxidable con bajo contenido de carbono y grado marino (316L) podría tener amplias implicaciones para industrias como la aeroespacial, automotriz y de petróleo y gas. Foto: Kate Hunts / LLNL.
“Esta microestructura que desarrollamos rompe la tradicional barrera de intercambio de resistencia-ductilidad”, dice Wang. “Si quieres hacer más fuerte el acero pierdes ductilidad; no puedes tener ambos. Pero con la impresión 3D podemos mover este límite más allá de la compensación actual”.
Usando dos máquinas diferentes de fusión de lecho de polvo con láser, los investigadores imprimieron láminas delgadas de acero inoxidable 316L para pruebas mecánicas. Según los investigadores, la técnica de fusión por láser resultó inherentemente en estructuras jerárquicas parecidas a células que podrían ajustarse para alterar las propiedades mecánicas.
“La clave fue hacer toda la caracterización y observar las propiedades que estábamos obteniendo”, afirma el científico de LLNL Alex Hamza, quien supervisó la producción de algunos componentes fabricados aditivamente. “Cuando se fabrica 316L de forma aditiva, se crea una estructura de grano interesante, algo así como una ventana de vidrios de colores. Los granos no son muy pequeños, pero las estructuras celulares y otros defectos dentro de los granos que se ven comúnmente en la soldadura parecen controlar las propiedades. Este fue el descubrimiento. No nos propusimos hacer algo mejor que la fabricación tradicional; solo funcionaba de esa manera”.
El investigador de posdoctorado de LLNL Thomas Voisin, un colaborador clave del trabajo, ha realizado descripciones exhaustivas de metales impresos en 3D desde que se unió al laboratorio en 2016. Cree que la investigación podría proporcionar nuevos conocimientos sobre la relación estructura-propiedad de los materiales fabricados aditivamente.
“La deformación de los metales se controla principalmente por la forma en que los defectos a nanoescala se mueven e interactúan en la microestructura”, explica Voisin. “Curiosamente, encontramos que esta estructura celular actúa como un filtro, lo que permite que algunos defectos se muevan libremente y, por lo tanto, proporcionan la ductilidad necesaria mientras que bloquean a otros para proporcionar la fuerza. Observar estos mecanismos y comprender su complejidad ahora nos permite pensar en nuevas formas de controlar las propiedades mecánicas de estos materiales impresos en 3D”.
Wang explica que el proyecto se benefició de años de simulación, modelado y experimentación realizados en su laboratorio de impresión 3D de metales para comprender el vínculo entre la microestructura y las propiedades mecánicas. Llamó al acero inoxidable un sistema de ‘material sustitutivo’ que podría usarse para otros tipos de metales.
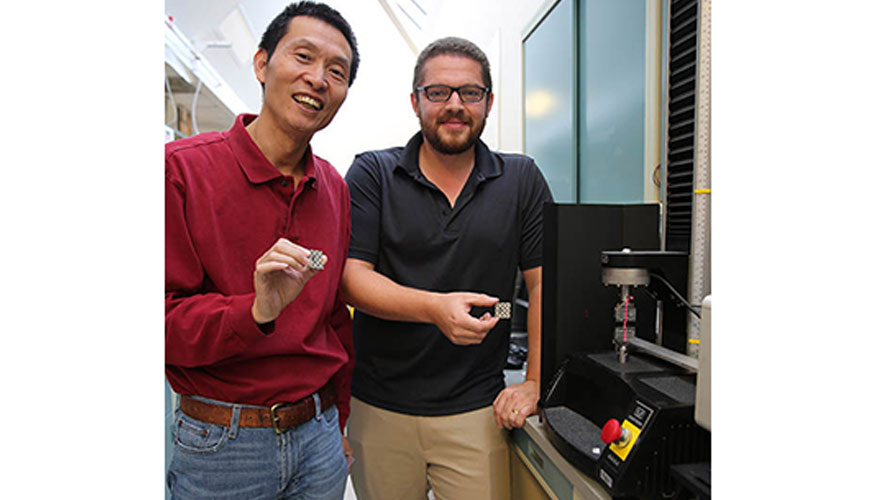
El científico de LLNL Morris Wang (izquierda) y el investigador postdoc Thomas Voisin desempeñaron papeles clave en una colaboración que imprimió con éxito 3D una de las formas más comunes de acero inoxidable de grado marino que promete superar la barrera de intercambio de resistencia-ductilidad. Foto: Kate Hunts / LLNL.
El objetivo final, explica, es utilizar la informática de alto rendimiento para validar y predecir el rendimiento futuro del acero inoxidable, utilizando modelos para controlar la microestructura subyacente y descubrir cómo fabricar aceros de alto rendimiento, incluida la resistencia a la corrosión. Los investigadores luego considerarán emplear una estrategia similar con otras aleaciones más livianas que son más frágiles y propensas a agrietarse.
El trabajo llevó varios años y requirió las contribuciones del Laboratorio Ames, que hizo difracción de rayos X para comprender el rendimiento del material; Georgia Tech, que realizó modelado para comprender cómo el material podría tener alta resistencia y alta ductilidad, y Oregon State, que realizó análisis de caracterización y composición.
Otros colaboradores de LLNL son: Joe McKeown, Jianchao Ye, Nicholas Calta, Zan Li, Wen Chen, Tien Tran Roehling, Phil Depond e Ibo Matthews.