Colaboración entre el Centro Tecnológico Aiju y la empresa Sarabia Plastics
Las tecnologías de impresión 3D reducen los costes y tiempos de fabricación de moldes prototipo de termoconformado
El proceso de moldeo por termoconformado de envases de gran tamaño conlleva una serie de dificultades asociadas a esta tipología de piezas, como son la escasa rigidez de los envases y la posible pérdida de las propiedades barrera por un exceso de deformación de la lámina. Para evitar este tipo de problemas, el Centro Tecnológico Aiju, en colaboración con la empresa Sarabia Plastics, ha desarrollado un novedoso proceso de fabricación de moldes prototipo mediante tecnologías de impresión 3D para reducir considerablemente los costes de fabricación y los tiempos de lanzamiento de nuevos productos respecto a las tecnologías tradicionales de arranque de viruta.
Introducción
En la fabricación de los primeros moldes prototipo de termoconformado se comenzaron a emplear hace años diferentes tipos de materiales como la madera de pino, escayola, poliéster, resina epoxi, etc. La elección de uno de estos materiales se realizaba en función de la calidad superficial que se pretendía obtener. Además, se les podía aplicar un recubrimiento superficial o barniz para eliminar las imperfecciones que pudieran tener y al mismo tiempo, endurecer su superficie.
Como la conductividad térmica de estos materiales es muy baja, posteriormente se empezó a utilizar el aluminio debido a su elevada conductividad. Estos moldes de aluminio se pueden fabricar mediante colada o empleando tecnologías de arranque de viruta.
En el moldeo por colada, pese a ser un proceso de fabricación muy económico, la calidad superficial obtenida no es muy buena, ya que suelen presentar porosidades debido al aire atrapado en el proceso de fabricación. En cambio, la calidad superficial de los moldes fabricados mediante las tecnologías de arranque de viruta puede llegar a ser excepcional. Esto, junto con la elevada maquinabilidad del aluminio, hacen que los moldes mecanizados de aluminio sean los más empleados en la actualidad para la obtención de series cortas de piezas de termoconformado.
Moldes de impresión 3D
Para solucionar la problemática de las piezas de gran formato con propiedades barrera, así como para abaratar costes y plazos de fabricación de moldes prototipo, se han empleado ha propuesto en este proyecto el empleo de tecnologías de impresión 3D. De este modo se pueden obtener, en un breve espacio de tiempo, pequeñas series de piezas termoconformadas con el material que posteriormente se empleará para la fabricación industrial. Este aspecto es de vital importancia puesto que así las industrias de envasado de alimentos pueden validar estos nuevos diseños en las líneas de envasado y posteriormente realizar los test de caducidad de los productos, lo que garantizará el éxito del proceso de escalado industrial.
Tecnología |
Material |
Sinterizado láser (SL) |
Poliamida 12 con 50% de esferas de vidrio |
Poliamida 12 con 50% de aluminio |
|
PolyJet |
ABS digital |
Tabla1: Materiales i3D empleados en la fabricación de moldes prototipo de termoconformado.

Figura 1: Diseño 1 molde circular de gran formato.
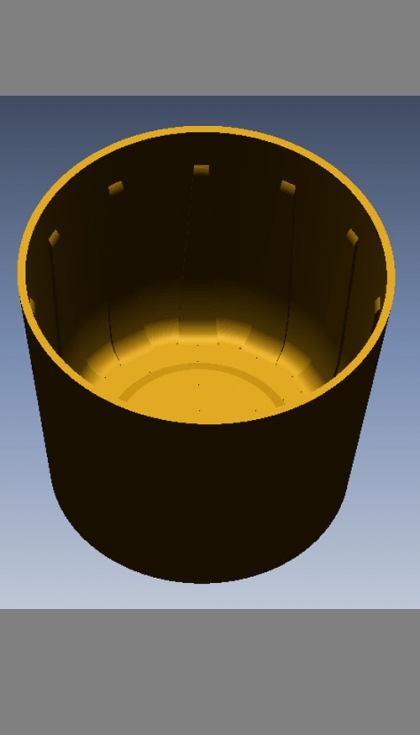
A continuación se muestran algunas imágenes de los moldes fabricados mediante las tecnologías de sinterizado láser e impresión PolyJet.
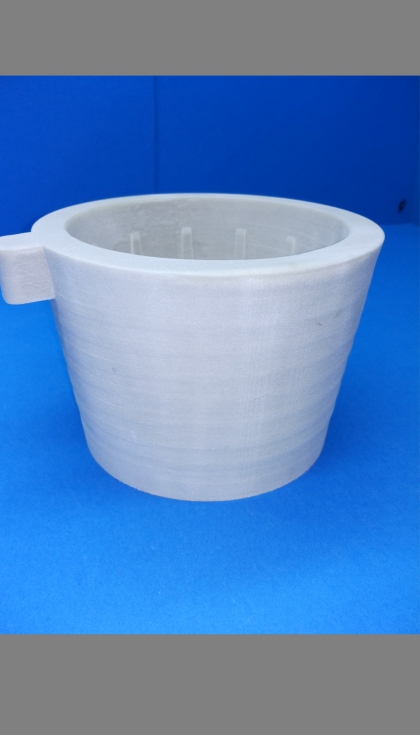
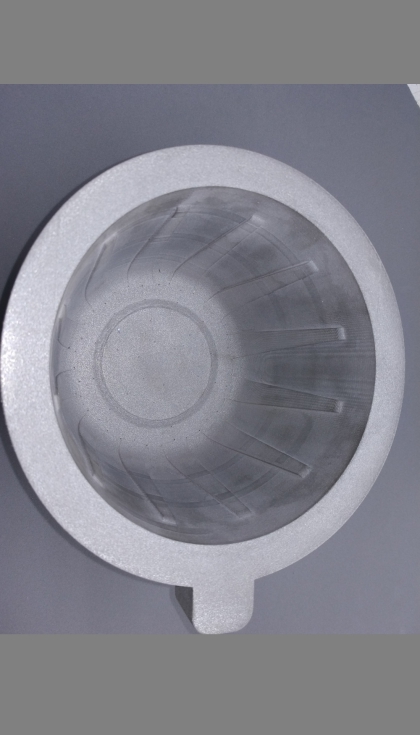
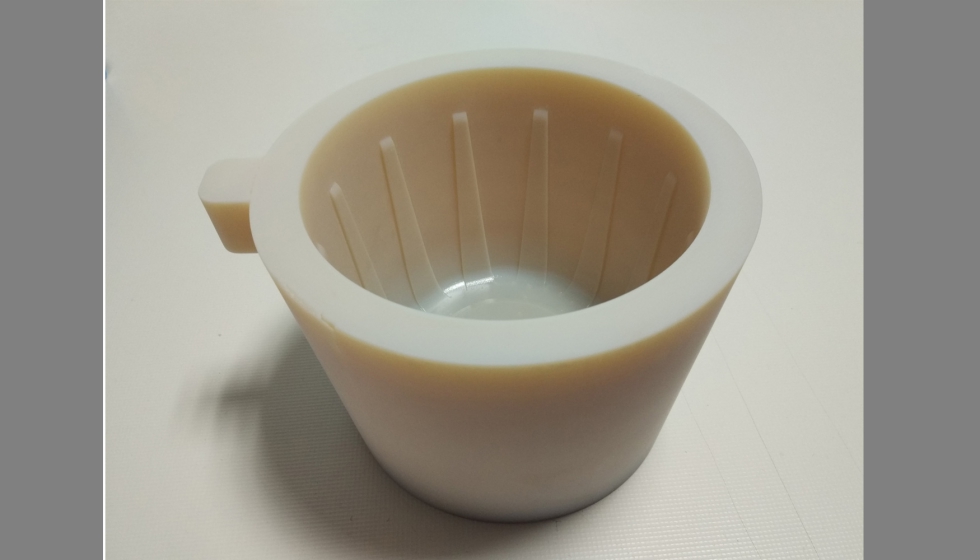
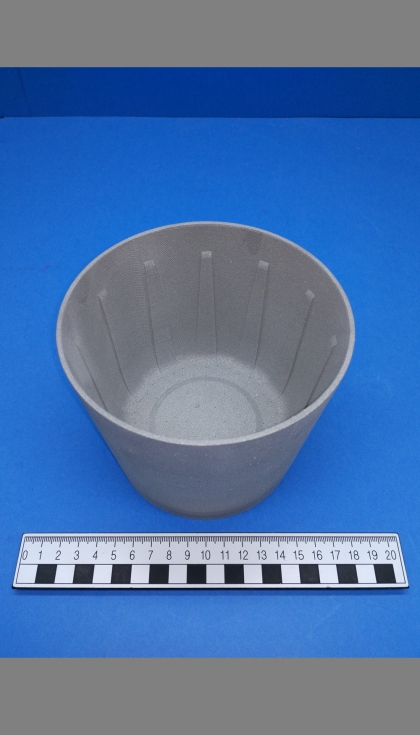
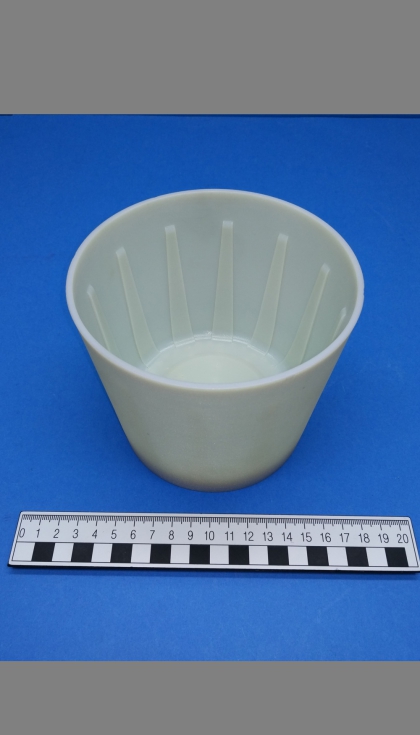
Una vez fabricados los moldes prototipo, se llevó a cabo el ajuste de éstos sobre el portamoldes y se realizaron las pruebas en la planta de termoconformado de Sarabia Plastics empleando una máquina modelo Kiefel Speedformar KMD64. Para la realización de las pruebas, se emplearon varios tipos de film, tanto monocapa como multicapa con diferentes espesores.
A continuación se muestran algunas piezas obtenidas con estos moldes y el detalle del acabado superficial de las piezas en función de la tecnología empleada. Este acabado es el que se obtiene directamente, sin realizar ningún tipo de proceso posterior de acabado superficial.
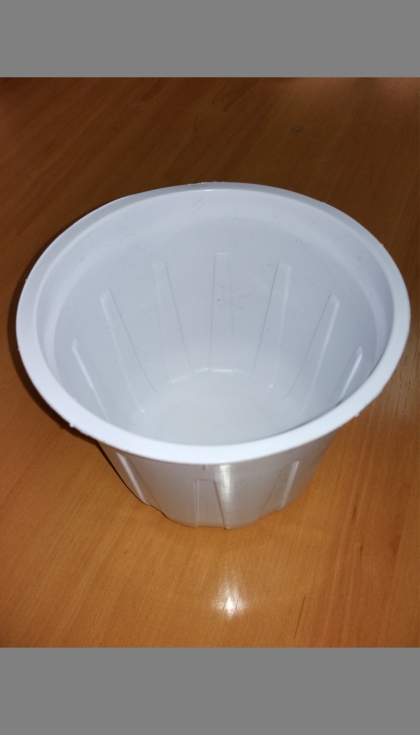
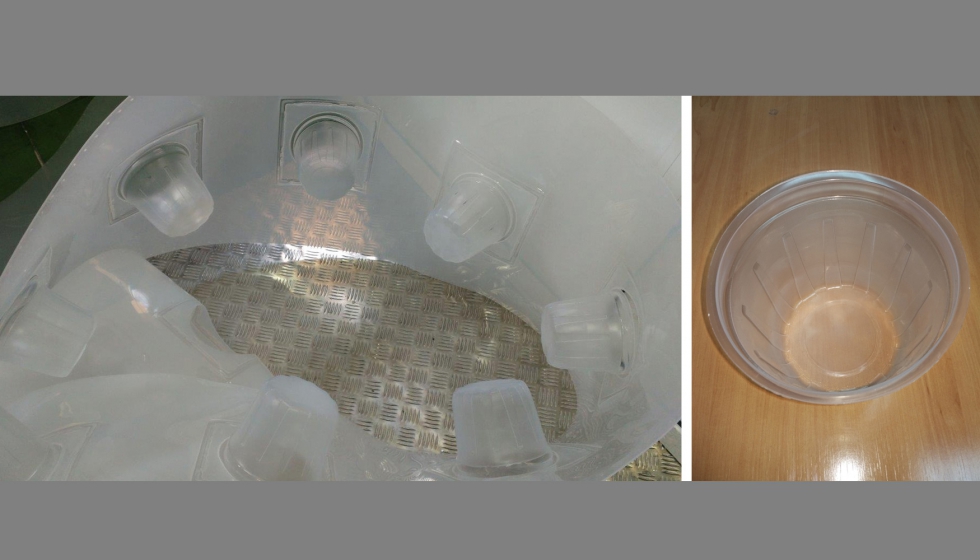
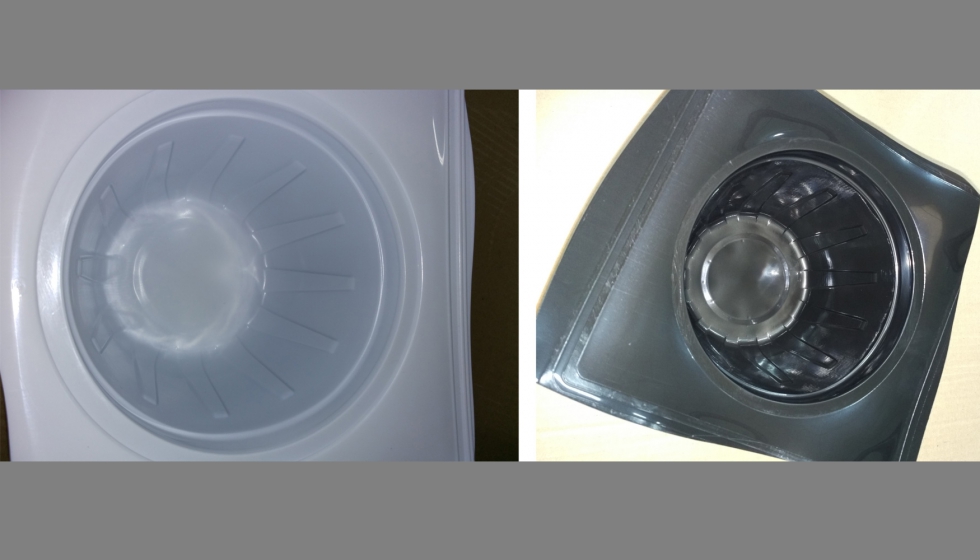
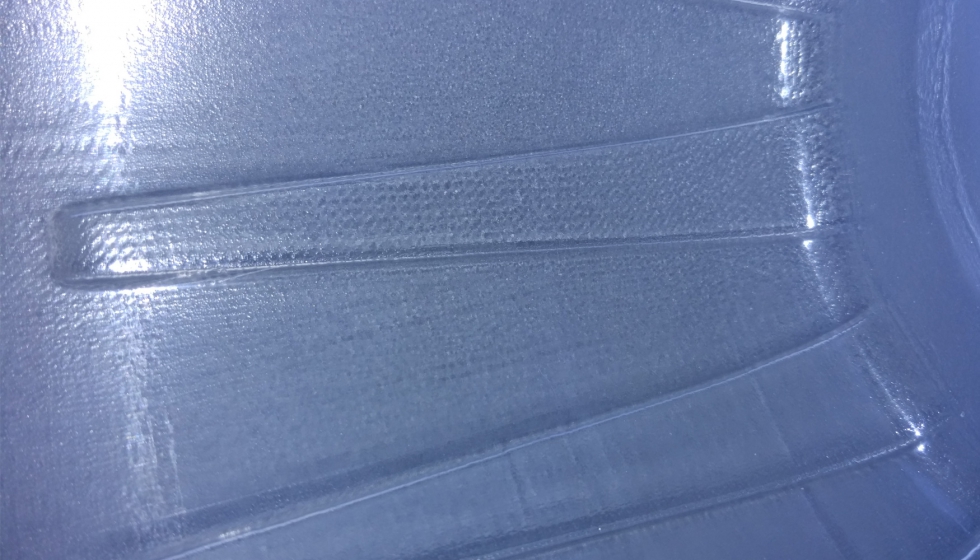
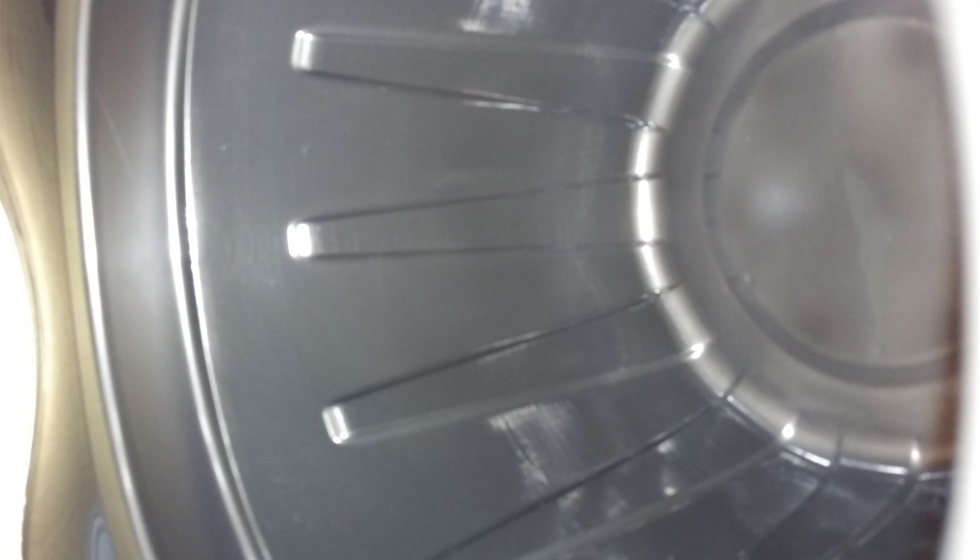
Tras las pruebas de termoconformado realizadas, no se observaron indicios significativos de degradación de los moldes, obteniéndose más de 50 piezas en todos los casos. Posteriormente, las piezas obtenidas fueron sometidas a ensayos químicos de migración según las normas UNE EN 1186-3:2002 y UNE EN 1186-3:2002. Los ensayos fueron superados satisfactoriamente, ya que no se superaron los límites de migración para cada uno de los ensayos realizados en las condiciones OM5, por lo que se puede establecer que no se ha producido ningún tipo de interacción entre las láminas y los moldes durante el proceso de termoconformado que pudiera afectar al uso final de las piezas obtenidas.
Conclusiones
Con una adecuada selección de materiales y tecnologías de impresión 3D, se puede conseguir reducir el coste de la fabricación de los moldes prototipo de termoconformado de envases de gran formato cerca de un 60% respecto a la fabricación mediante las tecnologías tradicionales.
Además, Sarabia Plástics ha logrado la reducción del proceso de lanzamiento de estos nuevos productos al mercado, pudiendo optimizar tanto el diseño para obtener envases con la rigidez suficiente, como el espesor del film empleado para no perder el efecto barrera. Teniendo en cuenta únicamente el tiempo de fabricación de los moldes mediante ambos sistemas de producción, se ha conseguido reducir el tiempo de fabricación de los moldes prototipo hasta en un 40%, lo que supone un importante avance competitivo para las empresas.
El proyecto ha sido financiado por el Centro para el Desarrollo Tecnológico Industrial (CDTI).