DIP ofrece prototipos funcionales y piezas finales gracias a la fabricación aditiva
DIP se dedica principalmente a ofrecer soluciones para resolver problemas complejos de empresas de los sectores aeroespacial y de automoción. Para ello, desarrolla equipos, investiga conceptos de diseño y fabricación, y ofrece soporte técnico en aquellas áreas en las que dichas empresas no resultan eficientes. “Podemos desarrollar un proyecto desde que se dibuja un boceto en una servilleta de papel hasta que se obtiene un producto final acabado utilizando los conocimientos y las herramientas que tenemos en nuestra empresa”, comenta Francisco Martínez, director general de DIP. “‘Somos un taller de soluciones’”.
Algunos de los servicios que ofrece DIP son el desarrollo de piezas y las pruebas de conceptos y de productos finales para los clientes, todo ello utilizando las últimas tecnologías digitales. Entre sus especialidades, se incluyen los bancos de pruebas para sistemas electrónicos y electromecánicos, equipos para simuladores de vuelo, consolas para pruebas de vuelo y prototipos electrónicos y electromecánicos.
“Aunque nuestros clientes pueden ser grandes fabricantes de aviones y vehículos, no les resulta rentable diseñar, desarrollar y probar cada pieza”, continúa Martínez. “Aunque cuenten con magníficos proveedores para fabricar las piezas, esas empresas no tienen las capacidades de investigación y desarrollo que nosotros ofrecemos. Por otro lado, hacemos que el cliente participe de forma activa en el desarrollo del proyecto, lo que garantiza que su visión se haga realidad”.
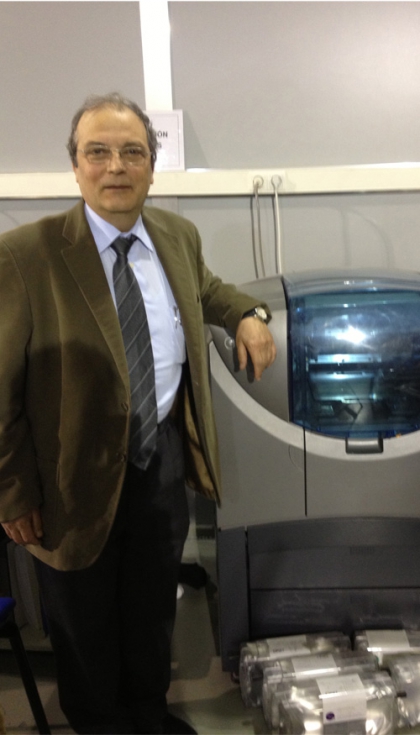
Francisco Martínez, director general de DIP, junto a la impresora 3D Objet Eden260VS.
La función de la impresión 3D
“En 2011, teníamos entre manos un importante proyecto de desarrollo de ingeniería y para poder completarlo necesitábamos un prototipo”, comenta Martínez. “Por aquel entonces, solíamos subcontratar los trabajos de prototipado; pero, los plazos y precios que ofrecían las empresas externas resultaban inaceptables. Fue entonces cuando nos dimos cuenta de que necesitábamos realizar la impresión 3D en nuestras instalaciones.
“Después de analizar varias impresoras 3D, decidimos instalar una Objet Eden260VS de Stratasys”, continúa. “La elegimos por su fiabilidad y precisión, y por la posibilidad de imprimir con una amplia gama de propiedades de material. También pensamos que Stratasys era un proveedor líder que conocía bien el mercado y contaba con la experiencia técnica necesaria para garantizar que pudiéramos mantener el máximo nivel de servicio para nuestros clientes”.
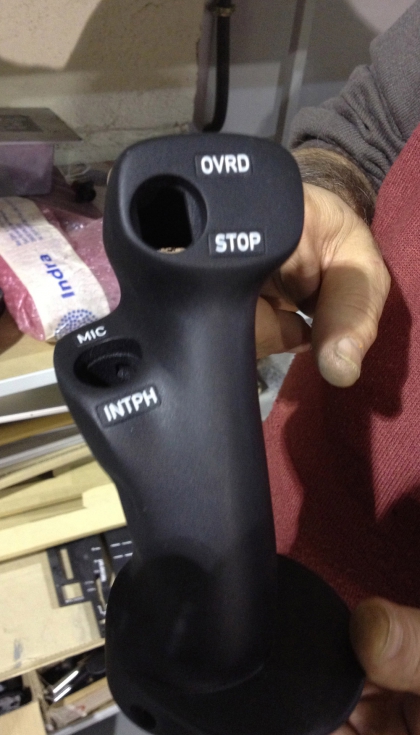
Una palanca de combustible para el repostaje de un Airbus A330 MRTT (avión de transporte/cisterna multifuncional). Impreso en 3D utilizando el material VeroBlack de Stratasys.
La impresora 3D Objet Eden260VS fue la elección perfecta para DIP. Su bandeja de impresión de 260 x 260 x 200 mm y su resolución de capa de 16 micras, única en el sector, ofrecían la velocidad, la calidad y el tamaño de modelo necesarios. “Podemos imprimir geometrías precisas con rapidez y a la perfección, y los modelos ofrecen un nivel de detalle excepcional con un increíble acabado superficial”, comenta Martínez. “Desde que empezamos a imprimir en 3D en nuestras instalaciones, hemos podido reducir drásticamente los ciclos de desarrollo de nuestros productos”, explica. “Normalmente, los prototipos que solían tardar 4 semanas en realizarse, ahora están listos en tan solo 2 días. Esto ha revolucionado nuestra forma de trabajar con los clientes”.
Pruebas operativas y producción de piezas definitivas
La capacidad que ofrece la impresora 3D Objet Eden260VS de crear piezas a partir de materiales rígidos y resistentes, así como de materiales transparentes y flexibles, ha permitido a DIP ampliar sus servicios del prototipado a la fabricación directa. Uno de los proyectos que se benefició de ello fue la creación de una palanca de combustible para el repostaje de un Airbus A330 MRTT (avión de transporte/cisterna multifuncional), un derivado militar del avión de pasajeros A330.
“La pieza impresa en 3D que creamos con nuestra impresora Objet Eden260VS, utilizando el material VeroBlack, se probó y se utilizó como producto final”, comenta Martínez. Se comprobó la resistencia de la pieza a la vibración 8G y a temperaturas de -85 a +50 °C. Una vez que se concretaron las especificaciones, DIP fabricó 50 unidades de esta empuñadura que se instalaron en las palancas de los aviones.
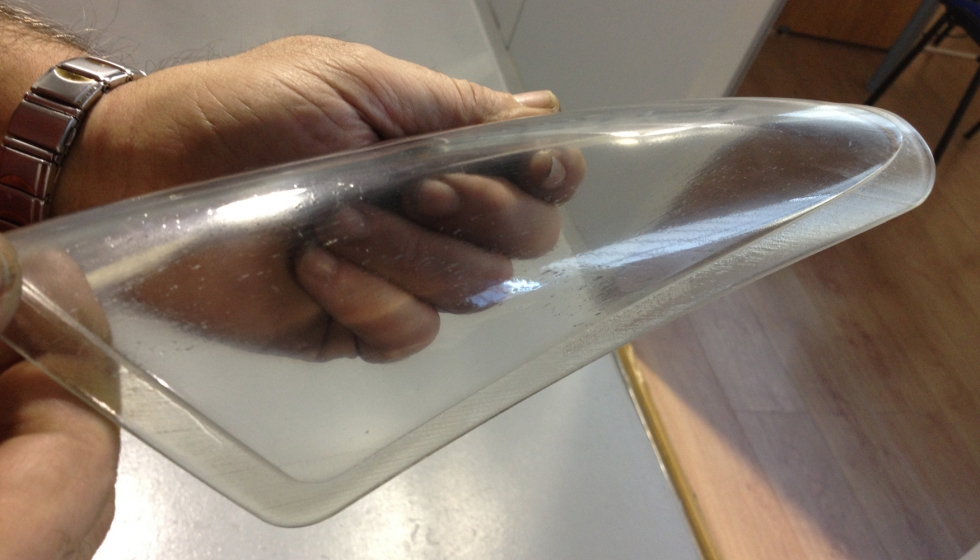
Cubiertas para las luces externas del Airbus C295, impresos utilizando el material transparente VeroClear de Stratasys.
“El hecho de haber conseguido este nivel de integridad del producto demuestra el potencial que ofrece la impresión 3D en los entornos de fabricación tradicionales”, añade. “También fabricamos cubiertas para las luces externas del Airbus C295 utilizando el material transparente VeroClear. Empleamos este material altamente resistente al calor en lugar de una pieza de fabricación tradicional para cubrir las luces intermitentes".
“El uso de la impresora 3D Objet Eden260VS nos permitió tener un mayor control de todo el proceso, algo que para nosotros tuvo un valor incalculable. Esta impresora no solo facilita el desarrollo de prototipos y piezas de producción finales mucho más rápido de lo que jamás podríamos conseguir con la fabricación tradicional, sino que además nos permite hacerlo a un coste mucho menor”, concluye Martínez.