Un cambio en el enfoque de procesos y de control de calidad ligados a la impresión 3D
En campos como la ortodoncia o la implantología, la libertad de diseño y producción ligada a la fabricación aditiva y la impresión 3D industrial permiten obtener soluciones individuales para cada paciente. Por ello no es de extrañar que sectores como el médico y el dental haya apostado fuertemente por esta tecnología. Pero a medida que ha ido creciendo su implantación han aparecido también nuevos retos ligados a los controles de proceso y de calidad, licencias y gestión de riesgos, entre otros. Éstos y otros temas formaron parte de la agenda de la XIII edición de Rapid.Tech, la conferencia internacional sobre fabricación aditiva celebrada en Erfurt (Alemania) del 14 la 16 de junio pasados.
Cada cuerpo es único. Por ello la fabricación de implantes a medida, tecnologías ortopédicas y productos dentales individualizados suponen un proceso muy difícil. Es necesario que estas soluciones se adapten al paciente pero que, además, sean a un coste aceptable y rápidos de fabricar y que cumplan con las altas exigencias de calidad tanto en términos de materiales como de métodos de producción. La fabricación aditiva puede satisfacer estas condiciones y prueba de ello es que se está extendiendo cada vez más en los sectores médico-dentales.
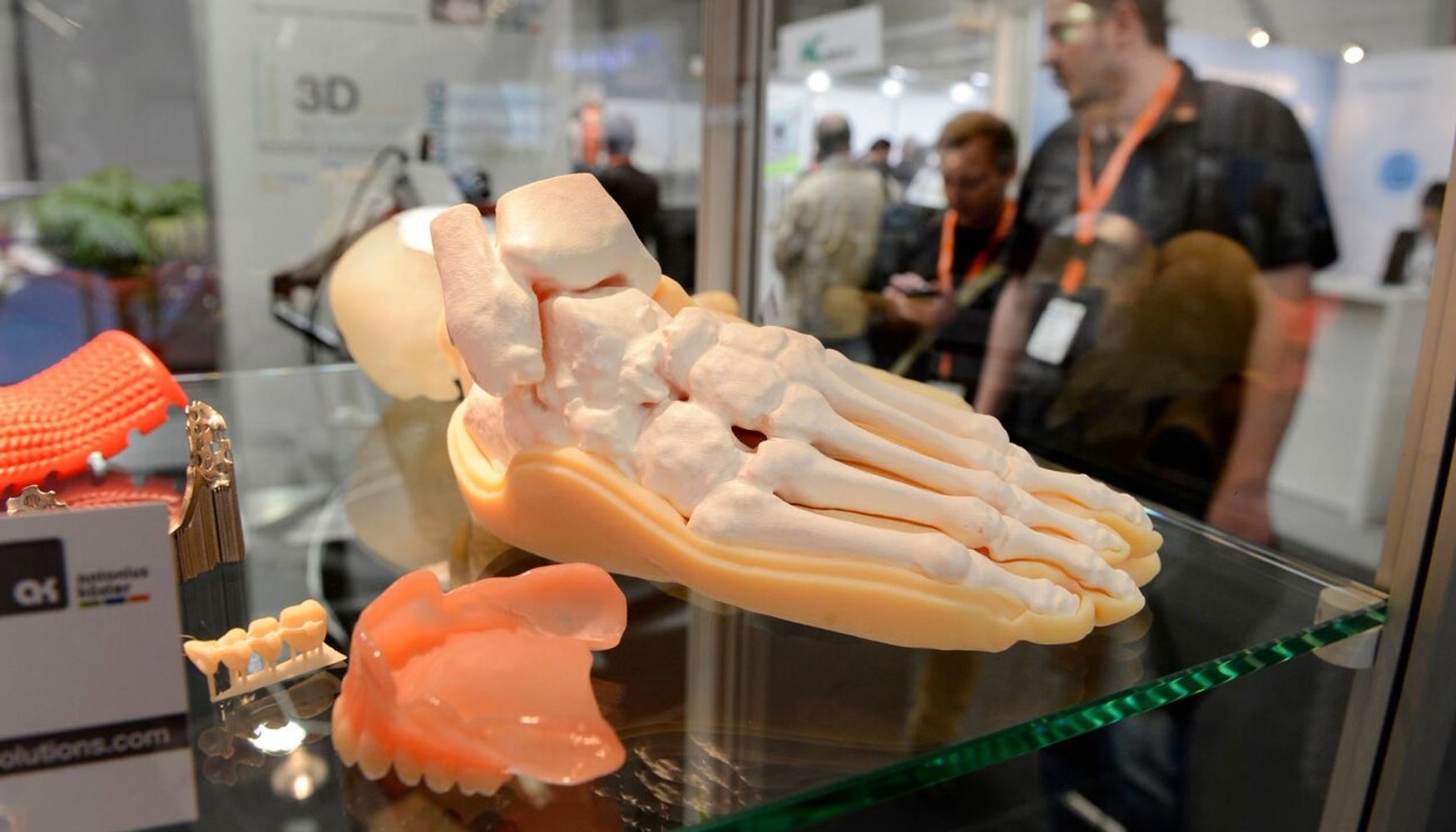
“En los últimos años, los diversos procesos de impresión 3D para la fabricación de implantes se han vuelto cada vez más populares. Ahora el debate es sobre temas como la gestión de riesgos y el control de proceso y de la calidad”, explica Ralf Schumacher, jefe del Laboratorio de fabricación aditiva para el sector médico de la Universidad de Ciencias Aplicadas del Noroeste de Suiza, presidente además del progama de ‘tecnología médica’ de en Rapid.Tech de este año. Precisamente una de las ponencias del foro expuso los 200 o más riesgos que deben tenerse en cuenta a la hora de aplicar la fabricación aditiva en implantes metálicos que utilizan procesos de fusión por láser, incluyendo conceptos como la precisión de repetición y la contaminación. En la charla se explicó cómo diseñar contramedidas y crear un proceso de garantía de la calidad, abordando también aspectos como la limpieza y la prueba mecánica de las estructuras de malla de titanio.
Otros temas abordados en el foro fueron la influencia de la orientación estructural sobre las propiedades mecánicas de poro abierto o las estructuras de láser realizadas con TiAl6V4, una aleación de titanio que se utiliza a menudo para reemplazar el hueso. La jornada también trató sobre el resultado y las perspectivas de desarrollo de implantes del hueso y la base orbital, individualizados para cada paciente mediante la impresión 3D. El tema ocular incluyó también una charla sobre el uso de la fabricación aditiva para lentes específicas para cada paciente. El programa concluyó con un informe de una empresa especializada en la fabricación de implantes mediante impresión 3D, de serie y a medida, así como los instrumentos quirúrgicos y prótesis a medida, utilizando titanio y acero inoxidable.