Una variante de las soluciones basadas en máquinas híbridas son las que integran la fabricación aditiva y el mecanizado en 5 ejes
Máquinas híbridas: ¿El ‘multitasking’ llevado hasta el límite?
Una variante de las soluciones basadas en máquinas híbridas son las que integran la fabricación aditiva y el mecanizado en 5 ejes. Esta combinación permite incrementar la flexibilidad y posibilita la fabricación de componentes de alta complejidad con un aprovechamiento del material muy elevado. Este tipo de máquinas permite combinar lo mejor de ambas técnicas: flexibilidad, capacidad de fabricación de geometrías complejas y aprovechamiento de material de la Fabricación Aditiva, con el acabado superficial y precisión del mecanizado. Sin embargo, se trata de sistemas que presentan algunas barreras de entrada por su elevado coste o la falta de madurez de la tecnología, pero no hay duda de que se trata de una puerta hacia una flexibilización de la producción de componentes complejos que antes era inimaginable.
La fabricación aditiva y el mecanizado: ¿Unidos para siempre?
La fabricación aditiva consiste básicamente en depositar material de forma precisa hasta construir un sólido. Esta etapa de aporte de material permite obtener una pieza de geometría cuasi final (lo que se conoce como proceso Near Net-Shape). El empleo de técnicas de fabricación aditiva en la actualidad es ya una realidad y hay decenas de soluciones que están en el mercado, sin embargo, la mayoría de estas soluciones se limitan al procesado de materiales plásticos.
Si nos centramos en fabricación aditiva de componentes metálicos, las soluciones son más limitadas (y más costosas) todavía. Aunque el número de equipos vendido durante los últimos años crece de forma sostenida y, tal y como se indica en el último informe Wohlers Report correspondiente al año 2015, las ventas de equipos de fabricación aditiva para piezas metálicas crecieron un 55%. Todo apunta a que este crecimiento continúe y que el número de usuarios de esta tecnología crezca en volumen debido a que:
- El coste de los equipos de fabricación aditiva se mantiene o está bajando.
- La tecnología empieza a ser conocida y madura.
- El precio de la materia prima (aun siendo muy elevado) presenta tendencias hacia precios más competitivos.
Estos factores, entre otros, han permitido que la fabricación aditiva se considere ya por parte de diferentes usuarios como una alternativa a la fabricación de diferentes elementos de alta complejidad. De hecho, la presencia de la fabricación aditiva en la industria es bastante heterogénea, mientras en algunos sectores como los implantes médicos o dentales, existen fabricantes que emplean esta tecnología en su día a día, en otros sectores como la automoción, energía, bienes de equipo, etc. se trata de una tecnología de fabricación emergente y con poco peso todavía. En cualquier caso, todos los estudios apuntan a un crecimiento de las técnicas de fabricación aditiva en todos los campos.
Las soluciones de fabricación aditiva para piezas metálicas se pueden dividir en dos grandes grupos dependiendo de la forma de aportar material. Por un lado, están los procesos de fabricación aditiva mediante fusión selectiva de polvo, el cual ha sido previamente depositado en una capa. Estos procesos, también conocidos por su acrónimo inglés Selective Laser Melting o SLM, se basan en la fabricación de una pieza capa a capa, partiendo de cero y empleando una placa de apoyo sobre la que se va añadiendo el material.
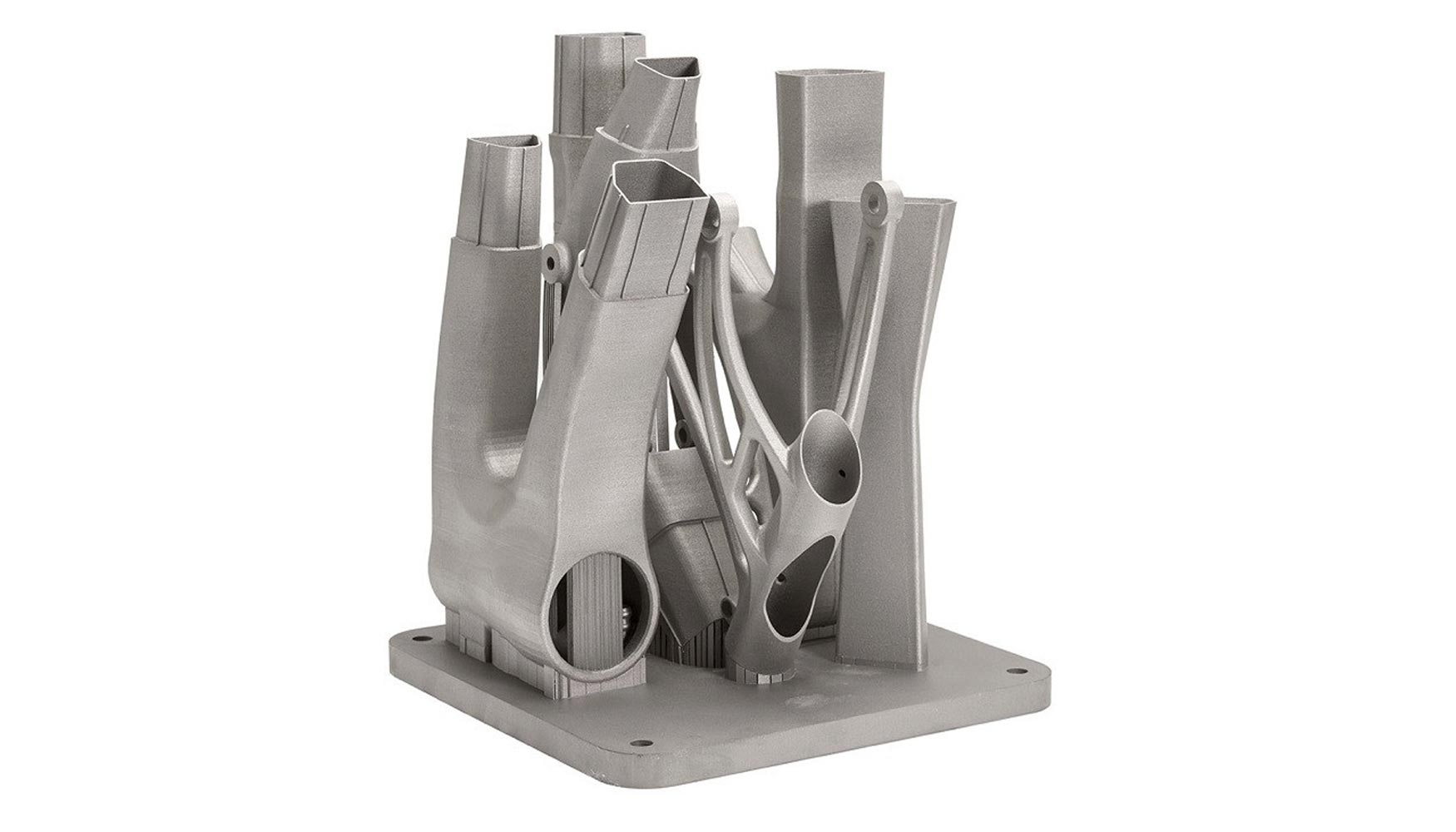
Se trata de métodos que parten de material en polvo y que lo consolidan capa a capa con la idea de generar una pieza en 3D completa. Los sistemas de fabricación aditiva mediante polvos predepositados son la evolución de las impresoras 3D a piezas metálicas. Este tipo de sistemas incorporan una fuente de energía en forma de láser (SLM) o un haz de electrones (EBM), lo suficientemente potente como para fundir una amplia gama de materiales que se suministran en forma de polvo. Se obtienen piezas de alta calidad, con capas de un espesor que puede oscilar entre 20 y 150 micras. La principal aplicación es para la realización de piezas completas en 3D, pero presentan una gran limitación de tamaño y productividad.
Este tipo de procesos permite una altísima libertad de diseño debido a que es posible fabricar casi cualquier tipo de geometría. Así, se pueden emplear herramientas de optimización topológica para minimizar la cantidad de material empleado o realizar diseños biocompatibles para mejorar la osteointegración de implantes con estructuras que imitan las formas que se crean en la naturaleza. Una de las principales características de estos procesos suele ser que la tecnología está en manos de los principales fabricantes de máquina y se ofrece una solución cerrada, en la que el usuario no solo recibe la máquina, sino el material, la tecnología, software, etc. consiguiendo el fabricante de la máquina, no únicamente vender la máquina, sino el servicio en forma de solución completa del proceso.
Por otro lado, dentro de la fabricación aditiva de piezas metálicas, otra posibilidad es inyectar material en forma de polvo o hilo, directamente sobre una pieza que hace de material base y sobre la que se deposita material capa a capa. Estas técnicas de aporte directo, conocidas también como Laser Material Deposition o LMD, suelen emplearse sobre piezas que ya han sido fabricadas por fundición o forja, donde se aporta material en zonas en las que se requieren estructuras complejas añadidas. El proceso LMD también se emplea en la reparación de componentes que han sufrido algún desgaste o que necesitan añadir material en alguna zona por razones de diseño. En este caso, en comparación con las soluciones basadas en SLM, los sistemas son mucho más abiertos y habitualmente se emplean máquinas-herramientas o robots como plataformas cinemáticas a las que se les ha incorporado una fuente láser y un sistema de alimentación de polvo o hilo. Así, es habitual que este proceso emplee un material en polvo algo más grueso que en los procesos SLM, siendo el tamaño de las partículas de polvo variable entre las 45 μm y 160 μm en función del tipo de recargue y el material depositado. Con estas técnicas, dependiendo del tipo de boquilla y del tamaño de spot del láser, es posible realizar desde grandes recargas, de incluso más de 10 mm de anchura, hasta recargas de detalle de pocas décimas de milímetro.
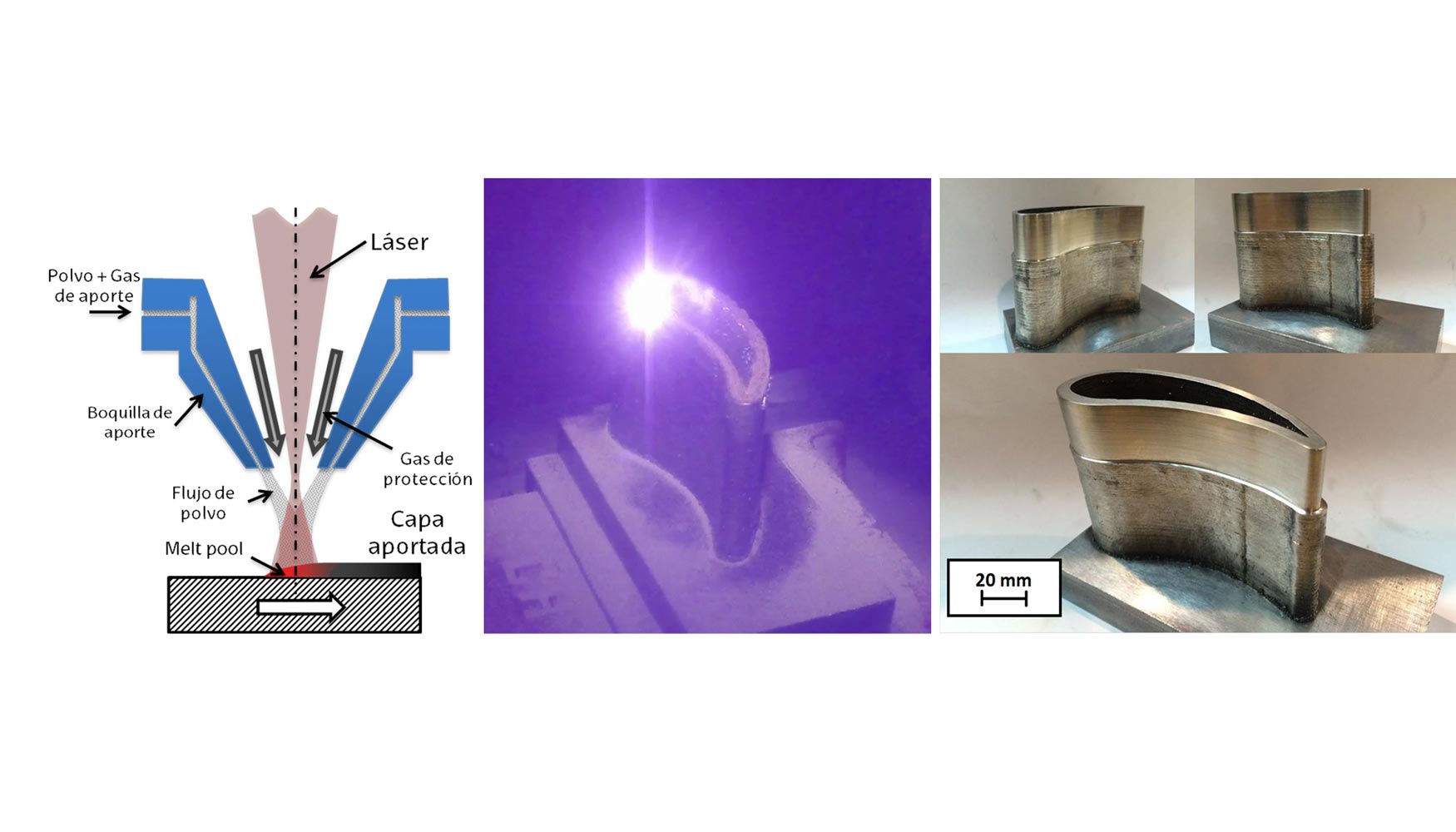
La principal diferencia entre los procesos SLM y LMD, es que los métodos basados en polvos predepositados (SLM), se suelen emplear para la fabricación directa de piezas completas empleando máquinas especializadas, mientras que el proceso LMD se emplea para añadir material de forma controlada y flexible sobre un componente prexistente y que es suelte estar basado en plataformas cinemáticas basadas en máquinas-herramienta convencionales.
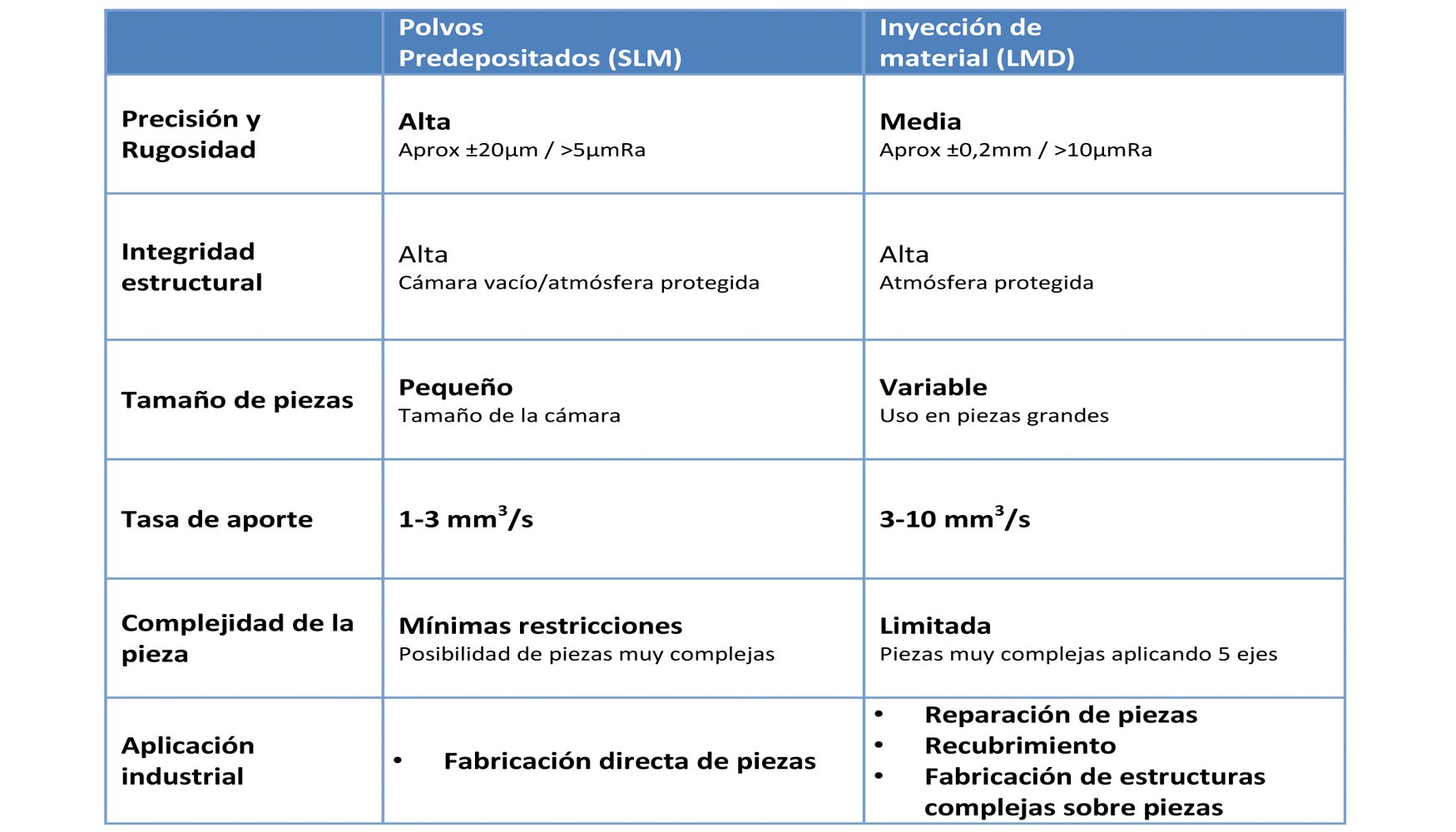
Independientemente del proceso de fabricación aditiva empleado y de las condiciones, es necesario realizar operaciones de acabado posteriores en aquellas cotas que requieran una precisión elevada. Estos métodos de acabado suelen ser operaciones tradicionales de mecanizado, electroerosión o rectificado que permiten alcanzar tolerancias mucho más estrechas que las que se obtienen por fabricación aditiva.
Así, una de las principales dificultades que existen en la actualidad a la hora de implantar estos procesos de forma industrial, es que las empresas especializadas en procesos de fabricación aditiva no dominan las tecnologías de mecanizado para el acabado posterior de las piezas, y en ocasiones, las empresas que emplean tecnologías de fabricación aditiva no disponen de los medios necesarios para realizar este tipo de acabados, recurriendo a subcontratistas y perdiendo agilidad en el proceso de fabricación.
La respuesta a este dilema ha sida la aparición de algunos prototipos que han integrado las tecnologías de aporte de material con el mecanizado en la misma máquina, desarrollando así máquinas híbridas capaces de realizar ambos procesos. A lo largo de los últimos años han aparecido diferentes sistemas que permiten aportar material y, en la misma máquina y sin necesidad de realizar ningún cambio de útil, mecanizar la pieza que acaba de ser fabricada por aporte. La combinación de ambas tecnologías en la misma plataforma introduce una serie de ventajas que hace que la industria esté atenta al desarrollo y exista una proliferación de estos modelos de máquinas en las últimas ferias.
¿Y por qué en la misma máquina?
La integración de las operaciones de fabricación aditiva y mecanizado en una plataforma común obedecen al mismo propósito que la integración de otros procesos en máquinas-herramienta como, por ejemplo, pueden ser las máquinas multitarea que integran cabezales de fresado y torneado. La principal ventaja es que partiendo de un material que haga de base común, se realizan las operaciones de aporte de material y mecanizado en el mismo equipo, sin necesidad de ejecutar transportes de piezas, nuevos reglajes en máquinas, búsqueda de ceros, etc. resultando en la fabricación completa de una pieza desde el inicio. Fundamentalmente, esta integración conlleva principalmente tres grandes ventajas:
- Mejora de tiempos de proceso: Las operaciones de fabricación aditiva y mecanizado se realizan en una secuencia programada y sin necesidad de cambiar de máquina. Así, el tiempo total de operación es inferior al que se emplea cuando se utiliza un equipo de fabricación aditiva y posteriormente una máquina de arranque de material. En caso de realizar las operaciones por separado, además del tiempo requerido en el transporte de una máquina a otra, es necesario sumar el tiempo de colocación y ajuste para realizar las operaciones de mecanizado.
- Mejora de precisión: Dado que las operaciones de mecanizado se realizan directamente sobre la pieza que se ha fabricado por aporte, empleando el mismo útil y sin cambiar la posición de la misma, la precisión que se puede conseguir es superior a la que se obtiene en los casos donde se debe recolocar la pieza en una máquina de arranque, donde, en el traslado de la pieza, se introducen errores debidos a la desviación de la pieza respecto al origen teórico. Por otro lado, para mejorar la precisión, las máquinas híbridas pueden incorporar sistemas de palpado que permiten hacer una medición in-process o ayudar a colocar la referencia de la pieza tras el aporte de material de forma precisa.
- Posibilidad de intercalar operaciones de fabricación aditiva y mecanizado: En el caso de disponer de dos sistemas separados, lo habitual es realizar primero las operaciones de fabricación aditiva de forma completa y, posteriormente, mecanizar la pieza en otra máquina. Sin embargo, si se emplea una máquina que integra ambos procesos, es posible intercalar operaciones de fabricación aditiva y mecanizado de forma alterna, pudiendo mecanizar una pieza parcialmente fabricada y, posteriormente, continuar con el proceso de aporte de material, haciendo aún más versátil el proceso de aporte.
Asimismo, las máquinas híbridas presentan otras ventajas como el empleo de una cinemática común para realizar todas las operaciones (con el ahorro que ello conlleva) o el empleo de un único sistema por lo que se ahorra superficie útil en la planta. También se emplea un CNC común que se puede programar con las mismas instrucciones, lo que permite estandarizar el proceso de forma más simple.
Uno de los primeros sistemas que integraron el proceso de aporte de material y mecanizado fue el desarrollado por la empresa japonesa Matsuura en el modelo Lumex Advance 25, la cual combina un sistema de fabricación aditiva basada en polvo predepositado con una fresadora de 3 ejes. En este caso, el sistema de fabricación aditiva y la fresadora prácticamente no comparten elementos mecánicos, ya que las operaciones de fabricación aditiva emplean un láser que es guiado por un escáner galvanométrico 2D, mientras que la fresadora dispone de 3 ejes independientes situados dentro de la propia cámara donde se fabrican las piezas.
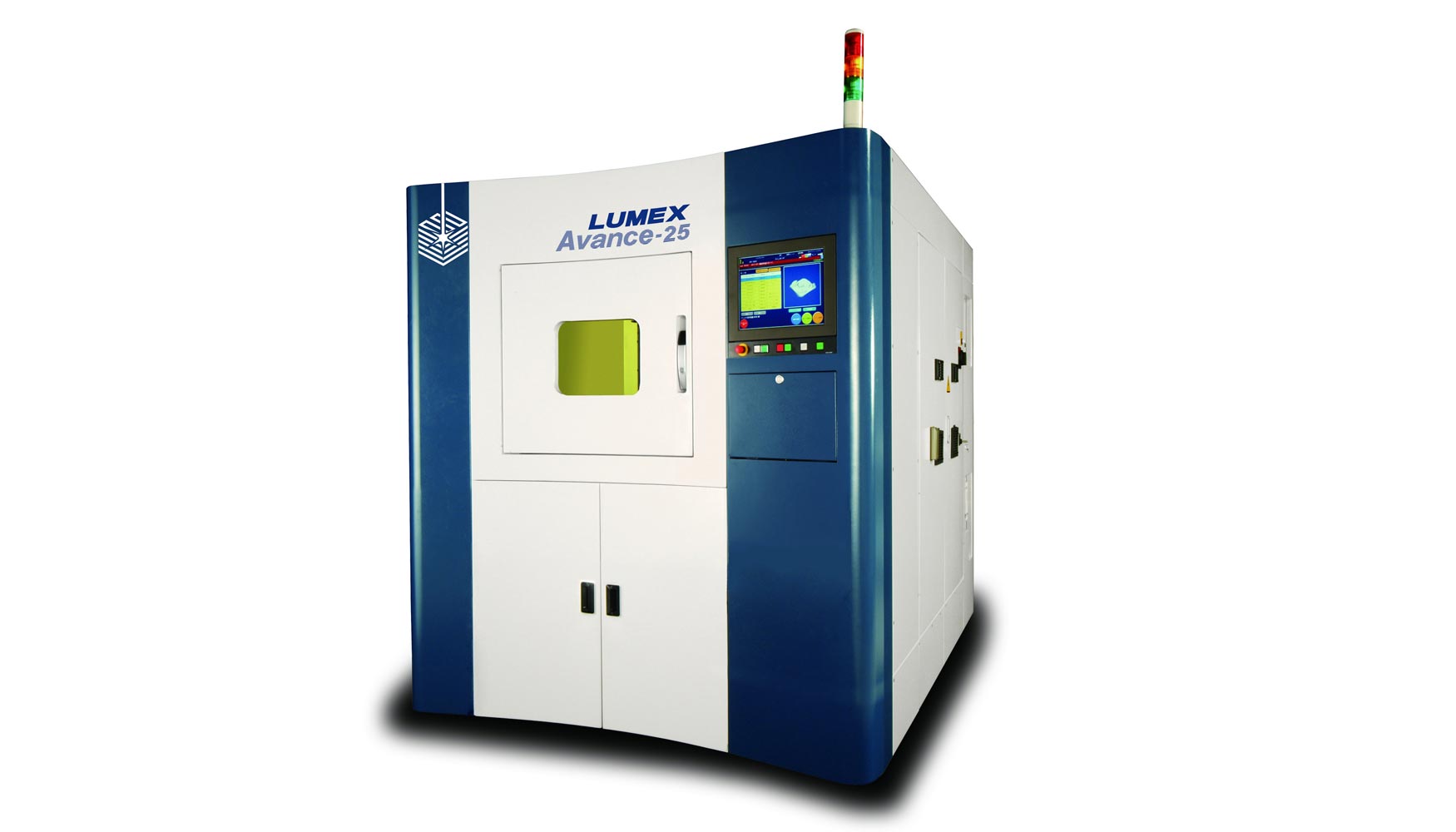
A pesar de este desarrollo, en la actualidad, la mayoría de los sistemas se basan en combinar un proceso de fabricación aditiva con boquilla de aporte. Así, lo habitual es encontrarse con sistemas que combinan la tecnología LMD y mecanizado. Este hecho se debe fundamentalmente a que partiendo de una máquina convencional, es relativamente sencillo integrar una boquilla de aporte y un láser para dotar a la máquina de capacidades de aporte de material. Además, se mantiene toda la estructura de la máquina (incluyendo el cabezal de fresado, cargador de herramientas, etc.) lo que facilita la integración de ambos procesos.
En resumen, los sistemas que se deben incorporar en una máquina-herramienta para darle capacidad de aporte de material son:
- Láser y refrigeradora: Se suelen utilizar láser de estado sólido que se pueden transportar por fibra, por lo que se pueden colocar anexos a la máquina.
- Fibra de transporte y óptica: Sirven para transportar el haz láser y focalizarlo en la superficie de la pieza. Es importante proteger estos elementos y garantizar que la fibra no se curve en exceso, ya que se puede romper por flexión.
- Alimentador de polvo: De la misma manera que el láser, es un sistema que se puede colocar anexo a la máquina y sirve para alimentar una serie de conductos con polvo metálico.
- Boquilla de aporte: Se coloca fijado a la óptica y en ella confluyen el láser y los conductos que arrastran el polvo. Es la ‘herramienta’ del proceso LMD, por lo que es importante evitar colisiones.
La principal dificultad de integrar estos sistemas en una máquina herramienta reside en la necesidad de proteger las ópticas, la fibra de transporte del láser y la boquilla de aporte de posibles colisiones y virutas que se generan en el proceso de mecanizado. El resto de elementos, siendo sensibles, están alejados de la zona de trabajo por lo que no presentan problemas.
Los diferentes fabricantes que han integrado el proceso de aporte en máquinas-herramienta han optado por diferentes soluciones, pero todas ellas tienen en común que amarran la óptica+cabezal de aporte con un cono (ISO o HSK) al cabezal de fresado de la máquina. A este elemento, se le acopla la fibra de transporte, la cual va directamente al láser por un camino óptico directo, externo al cabezal de fresado, y de esta forma, se consiguen integrar los elementos necesarios en la misma máquina aportando todas las ventajas citadas.
Y si todo es tan bueno, ¿por qué no se venden más máquinas híbridas?
A pesar del crecimiento experimentado por la tecnología existen varias las dificultades presentes y que deben abordarse en la actualidad. Dichas dificultades afectan tanto a los fabricantes como a los usuarios de máquinas híbridas.
El mayor reto de la tecnología híbrida reside en la madurez de la misma. Expertos en el área pronostican que todavía quedan entre 10 y 15 años para que se alcance el nivel de conocimiento requerido entorno al proceso. Varios factores afectan directamente al resultado final del producto que se fabrica, tales como los materiales de aporte y la compatibilidad entre el material del substrato y los materiales aportados, o las condiciones de aporte (potencia, volumen de polvo, gas, velocidad de avance), etc. La experiencia y el conocimiento sobre todos estos factores es clave a la hora de dominar el proceso híbrido de fabricación.
Por otro lado, la tecnología CAD/CAM está actualmente evolucionando para dar servicio a los procesos de aporte láser tipo LMD. Tradicionalmente el software CAM solamente contemplaba la opción de sustracción de material, orientado a las operaciones más comunes de mecanizado. Sin embargo, este tipo de sistemas requieren también la incorporación de operaciones para aporte de material. En este sentido, no solo es necesario calcular las trayectorias del proceso teórico, sino que hay que tener en cuenta factores y zonas de la pieza susceptibles de mayores crecimientos de cordones de aporte y que pueden distorsionar el resultado final. Además, es importante realizar una simulación virtual fiel de las operaciones para evitar colisiones y evaluar el proceso. En la actualidad, hay alguna aproximación, como la realizada por el sistema de Siemens NX, pero se trata de un módulo de CAM que todavía está en fase de desarrollo y además en la actualidad es exclusividad de un fabricante de máquinas híbridas.
Por otro lado, como ocurre con casi todo, el precio de las máquinas híbridas y el coste de fabricación, son dos factores condicionantes de la evolución de la tecnología. A día de hoy el precio de las máquinas híbridas disponibles en el mercado es muy elevado y si se añade que es necesario considerar el mantenimiento de las mismas, la potencia eléctrica requerida, etc. el precio es todavía mayor. Uno de los elementos más costosos de este tipo de máquinas es el propio láser. A futuro se espera una bajada del precio de las máquinas híbridas conforme vayan apareciendo más modelos en el mercado y los fabricantes comiencen a fabricarlas en serie, sin embrago, no es probable que este hecho ocurra en un plazo cercano.
Dada la elevada inversión que debe realizarse para la compra de una máquina híbrida, una de las opciones en boga actualmente es el retrofitting. De esta forma es posible acercarse a la tecnología y conocerla para posteriormente contemplar la inversión en una maquina inicialmente concebida como híbrida. Esta tendencia es seguida por ciertas universidades o centros de investigación en sus acercamientos iniciales con la tecnología. Sin embargo, estos equipos experimentales no explotan el 100% de capacidad de un sistema híbrido, en el que se integran los sistemas de aporte de material y mecanizado desde el origen.
Desde el punto de vista del usuario final, otro de los factores a tener en cuenta es la homologación o certificación de estos procesos de fabricación en piezas pertenecientes a sectores con especificaciones críticas. Por ejemplo, en el sector aeronáutico hay algunas aplicaciones homologadas, pero todavía se está muy lejos de poder emplear estas técnicas de manera masiva. Lo mismo sucede en otros sectores como energía o transporte donde también hay una estricta política de homologación de procesos.
Por último, existen barreras tecnológicas que es necesario considerar. Una de ellas parte de la propia concepción de la máquina, en la que se requiere una cinemática de altas prestaciones para las operaciones de mecanizado, que luego se emplea también para operaciones de aporte de material. Si tenemos en cuenta que los requisitos de precisión y velocidades/aceleraciones de las operaciones de aporte por láser son muchísimo más sencillos de conseguir que los de las operaciones de mecanizado, se puede afirmar que se está empleando una cinemática sobredimensionada y extremadamente precisa para una operación que no lo requiere. Por otro lado, tras realizar operaciones de aporte por láser siempre se derrama polvo resultante de partículas que no se han fundido y que han salido rebotadas fuera de la zona de aporte. Este polvo residual, queda esparcido por la zona de trabajo de la máquina, y debido a su pequeño tamaño (el diámetro de algunas partículas son inferiores a 45 micras), puede introducirse entre los cubreguías, pares de rotación de los ejes rotativos, etc con el consiguiente daño. Por tanto, resulta muy importante tratar de contener el polvo residual dentro de un contenedor durante el proceso.
Asimismo, y en relación al problema anterior, puede haber una gran limitación en el empleo de fluidos de corte. Dado que hay una capa de polvo alrededor de la pieza, en el momento que se activa el fluido de corte, este arrastra el polvo hasta los tanques de taladrina y se pueden provocar atascos o daños en el sistema de bombeo. Para solucionar el problema es necesario disponer de filtros que separen el polvo del fluido de corte, pero con una capacidad de filtrado de partículas muy finas, lo que complica de una manera notable el sistema de filtrado y suministro de taladrina.
Por último, y no menos importante, es necesario recalcar que las máquinas híbridas integran dos tecnologías muy diferentes y con particularidades propias. Por un lado, el aporte por láser en el que es necesario dominar aspectos como el láser, condiciones de aporte de diferentes materiales, flujos de gases, polvo, etc. y por otro lado, las operaciones de mecanizado en 5 ejes o sistemas multitarea, que incorporan fresado y torneado, donde es necesario dominar los sistemas de CAM, herramientas de corte, parámetros de mecanizado, etc. El incorporar estas dos tecnologías en la misma máquina obliga a los usuarios a disponer de personas que dominen ambas técnicas, lo cual es un reto a fecha de hoy. En este sentido existe una necesidad creciente de formar a personas específicamente en estas tecnoilogías.
Los pioneros. Ejemplos industriales
Como en toda tecnología, a pesar de los problemas que existen, de la falta de madurez de la tecnología, de la falta de usuarios, … siempre hay alguien que da el primer paso y se atreve a poner en el mercado un primer prototipo. En el caso de las máquinas híbridas así ha sido, y por ello, a lo largo de este apartado, trataremos de describir brevemente las máquinas híbridas que hay en el mercado y cuáles son sus características principales.
La emergencia en el mercado de las máquinas híbridas que combinan procesos de fabricación aditiva con la tradicional tecnología de eliminación de material en maquinas CNC ha suscitado un enorme interés en el mercado de la máquina herramienta. En la actualidad, las maquinas híbridas solamente representan una pequeña fracción de todos los sistemas de fabricación aditiva presentes en el mercado. Estas primeras unidades han sido fabricadas por empresas pioneras como DMG MORI, Hermle, Ibarmia, Mazak o WFL.
DMG MORI
Características: Presente en el mercado de las máquinas híbridas con la Lasertec 65 3D. La cinemática de la máquina es la de una fresadora de 5 ejes tipo monoblock de Deckel Maho en la que se puede trabajar con piezas de hasta 600 mm de diámetro y el control CELOS de DMG MORI. Gracias a su acuerdo con Siemens, DMG MORI tiene a su disposición un módulo exclusivo de Additive Manufacturing integrado en el software de CAD/CAM NX de Siemens.
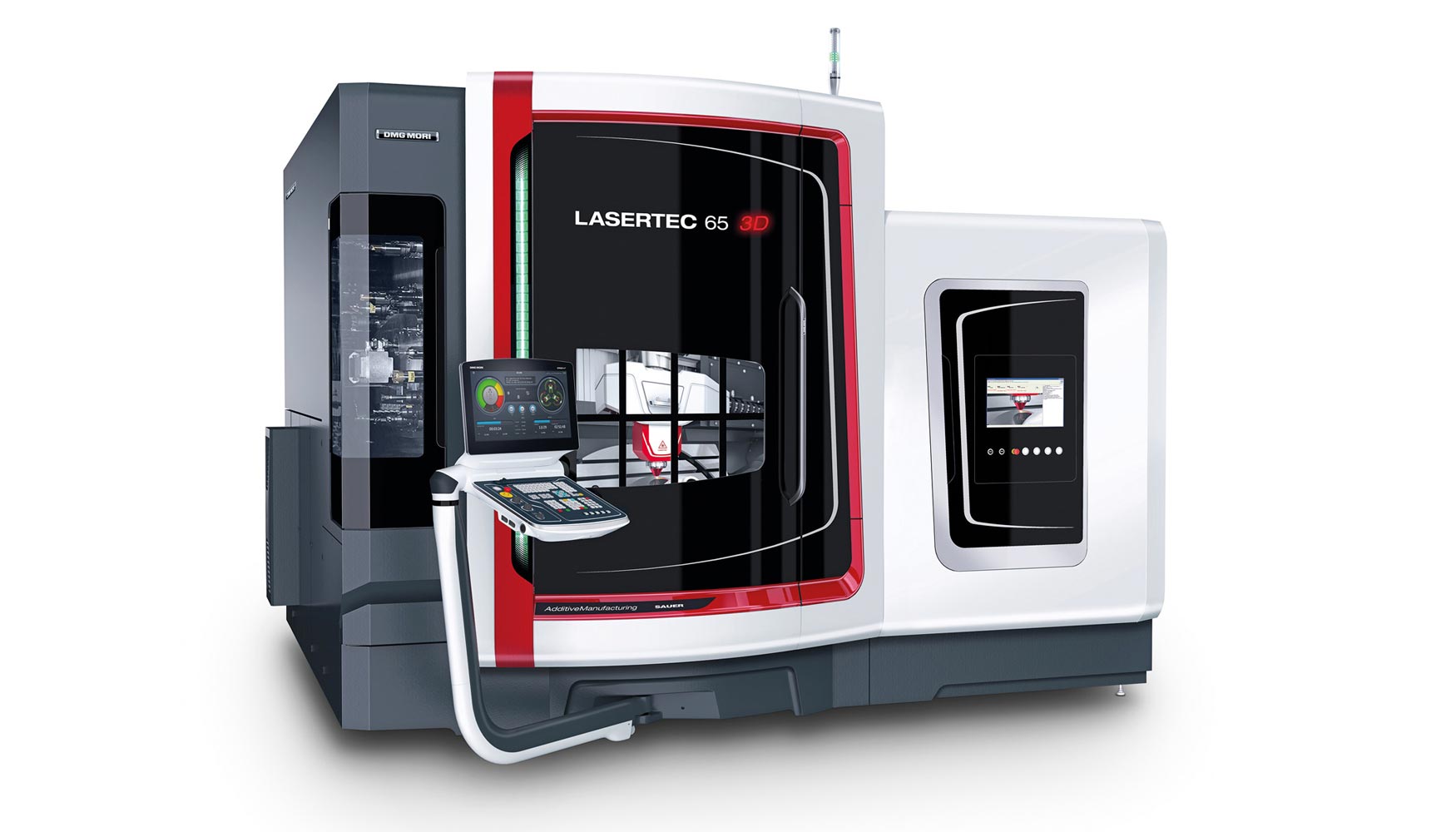
Mazak
Características: Parte de la base de una máquina multitask Integrex 400 y adapta un sistema LMD. Lo más destacable de la máquina multitarea Integrex i-400AM es la incorporación del sistema Ambit que permite disponer de diferentes cabezales aporte intercambiables en función de las necesidades. Estos cabezales de aporte se cambian como una herramienta de corte ya que van montados sobre un cono portaherramientas. El sistema Ambit de cabezales de aporte láser intercambiable ha sido recientemente premiado con el prestigioso IAMA International Additive Manufacturing Award.
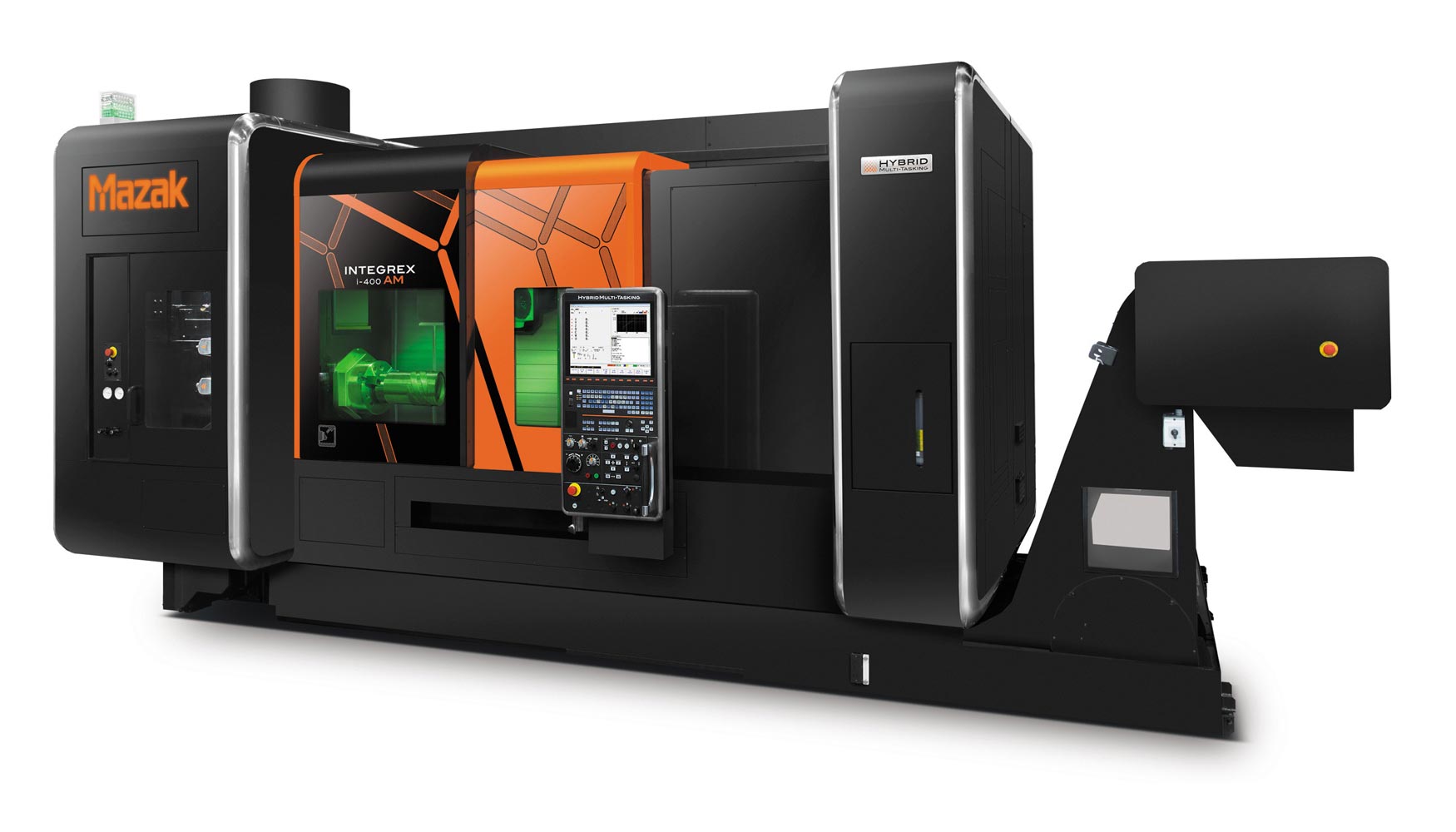
Ibarmia
Características: Se trata del primer modelo a nivel nacional y es el más grande que existe en la actualidad. Partiendo de la estructura de una máquina multiproceso ZVH, la ADD+Process incorpora un sistema de aporte con un láser de fibra y un cabezal de aporte coaxial sensorizado. La máquina presentada por Ibarmia en la EMO de Milán celebrada en octubre de 2015 se suma a la lista de máquina híbridas que integran el aporte láser y permiten además el mecanizado multitarea.
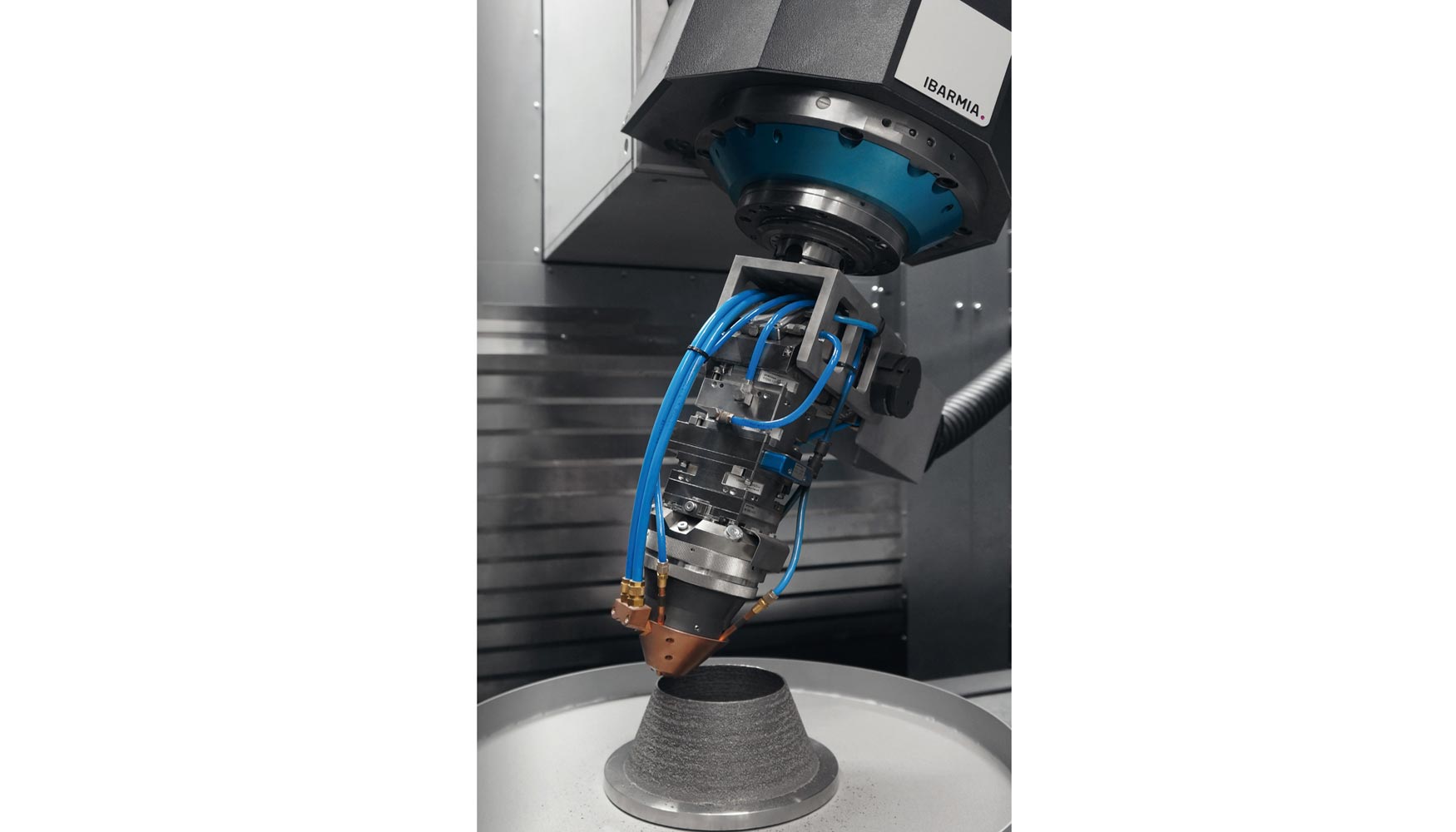
Hermle
Características: Se trata de una fresadora de 5 ejes de la marca Hermle que integra la tecnología de fabricación aditiva en un centro de mecanizado de 5 ejes. La máquina recibe el nombre de MPA 40 y dispone de una boquilla de aporte de material en polvo montada en el husillo vertical. Al igual que sus competidoras, la máquina está pensada para piezas de gran tamaño.
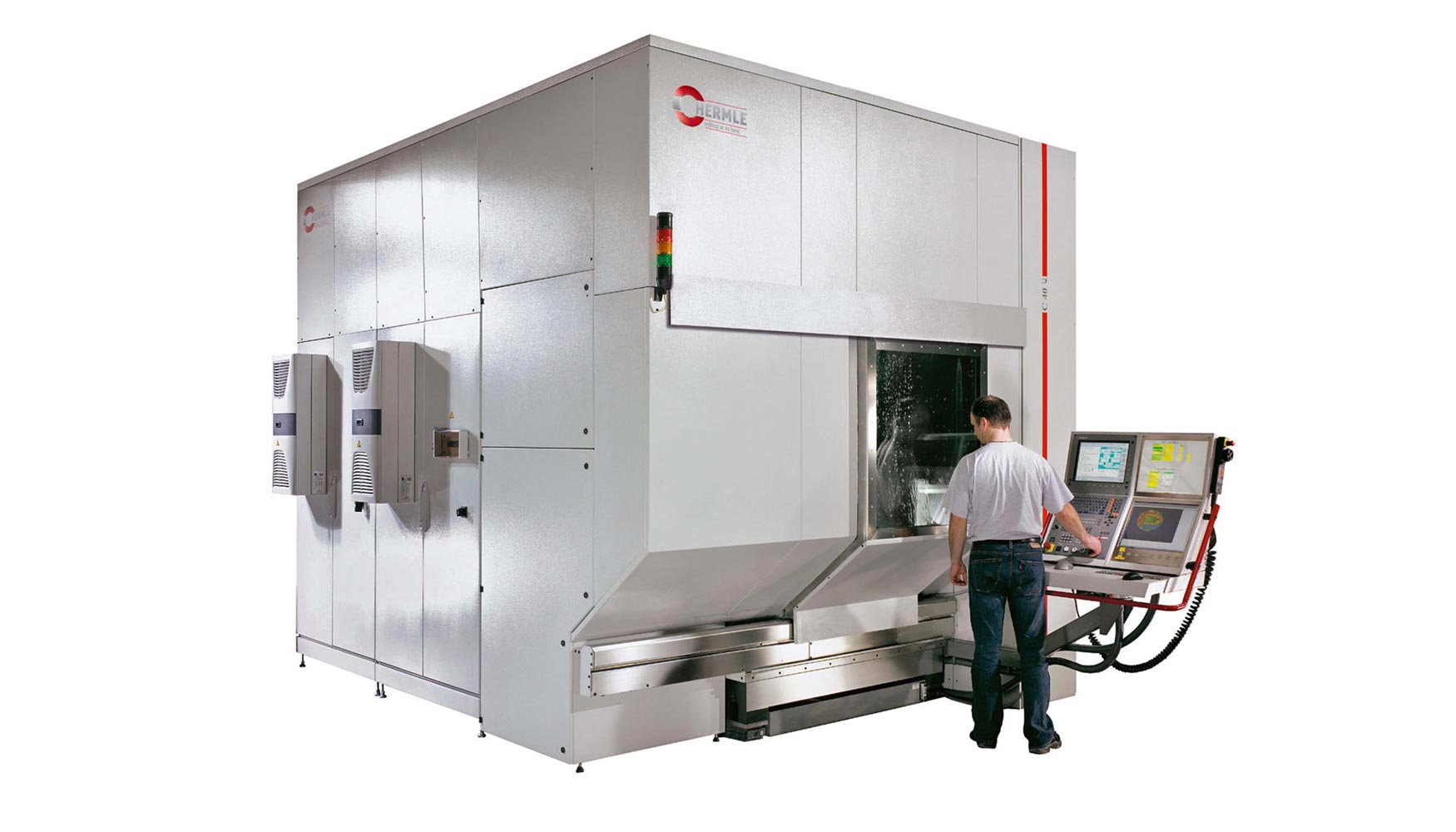
WFL
Características: Se trata de una solución desarrollada a partir de un centro multitarea de gran tamaño que integra de un láser de diodod de 6 kW. La M80 Millturn de WFL incorpora la técnica de aporte por láser, pero orientada a piezas de gran tamaño. Así el sistema que integra dispone de una mayor tasa de aporte de material pero menor capacidad de reproducción de detalles. Además, combina la posibilidad de realizar temples superficiales por láser debido a la tecnología láser que incorpora.
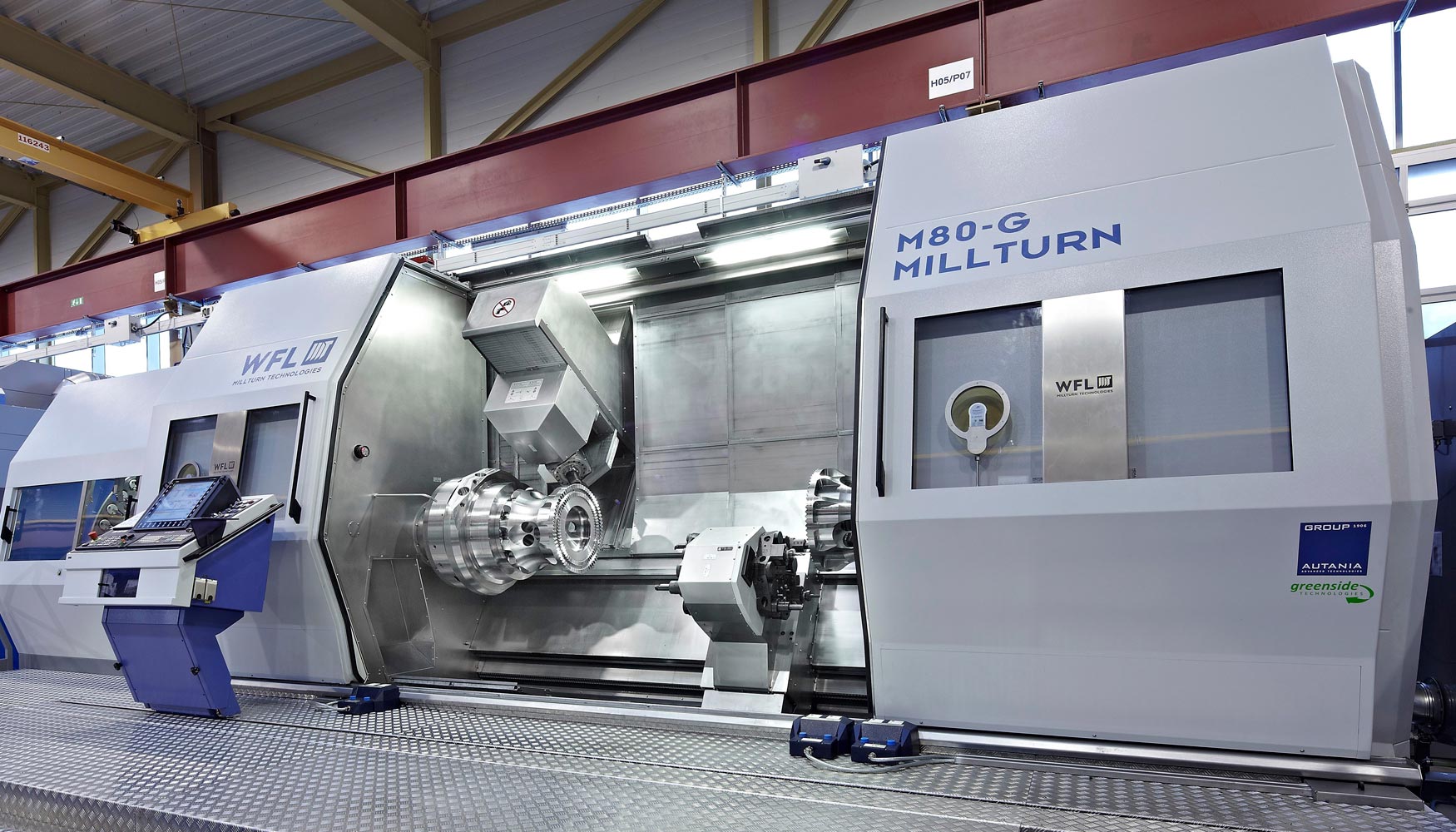
Elb-Schliff WZM
Características: Desarrollo que nace fruto de colaboración entre Hybrid Manufacturing Technologies y el fabricante de rectificadoras ELB Elb-Schliff WZM GmbH surge la máquina Millgrind que incorpora la tecnología láser con el sistema de boquillas intercambiables de Ambit.
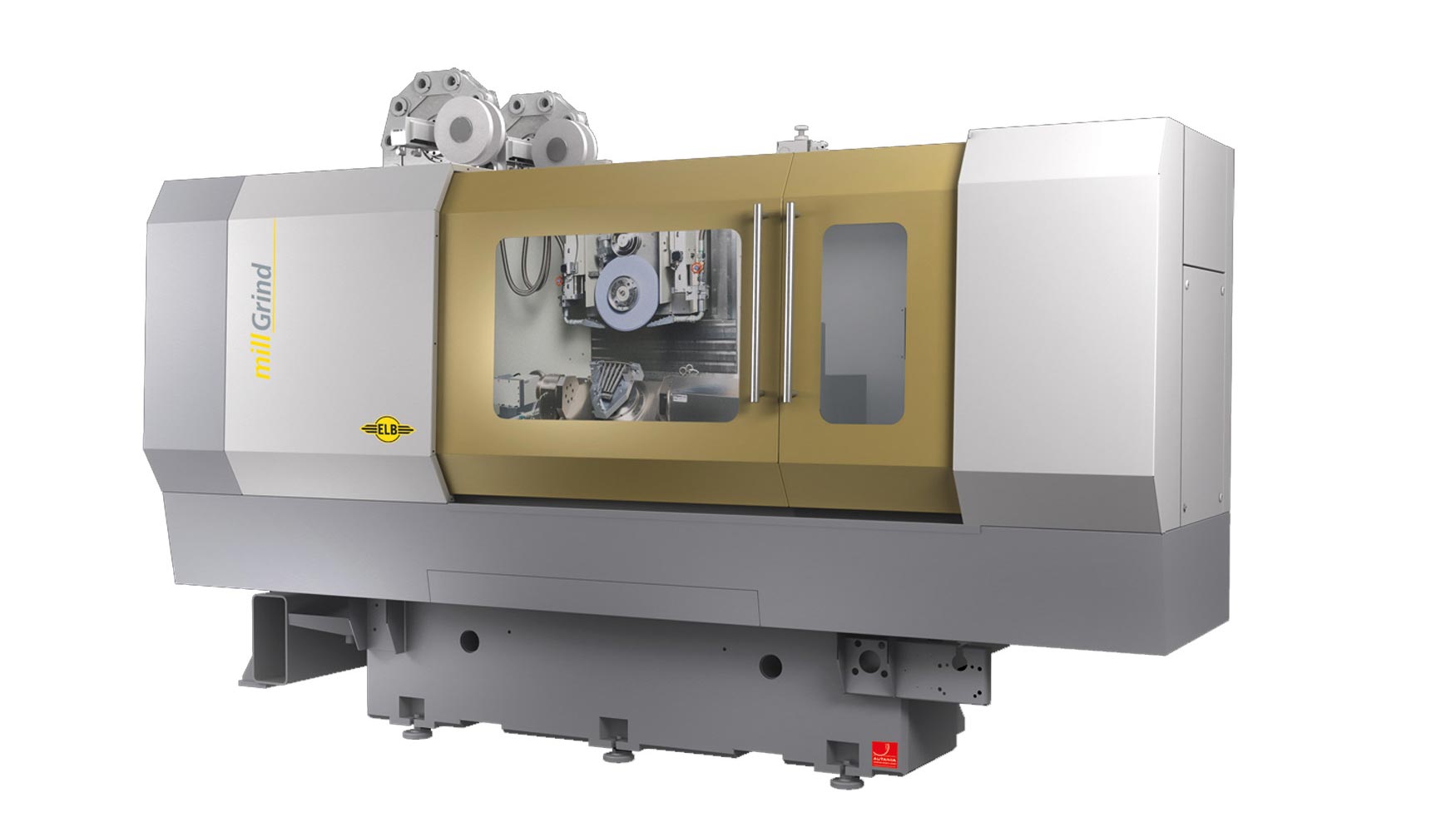
HMT Hybrid anufacturing technologies y Uk’s Manufacturing technology center (MTC)
Características: Se trata de un prototipo que nace fruto de un proyecto de investigación sobre la tecnología de fabricación híbrida. La máquina HSTM 1000 es el resultado de la colaboracion entre dos de los miembros del proyecto como son HMT Hybrid anufacturing technologies y Uk’s Manufacturing technology center (MTC). Actualmente el uso de la máquina está limitado a la reparación de álabes para el mercado aeronaútico pero está previsto ampliar su rango de aplicación.
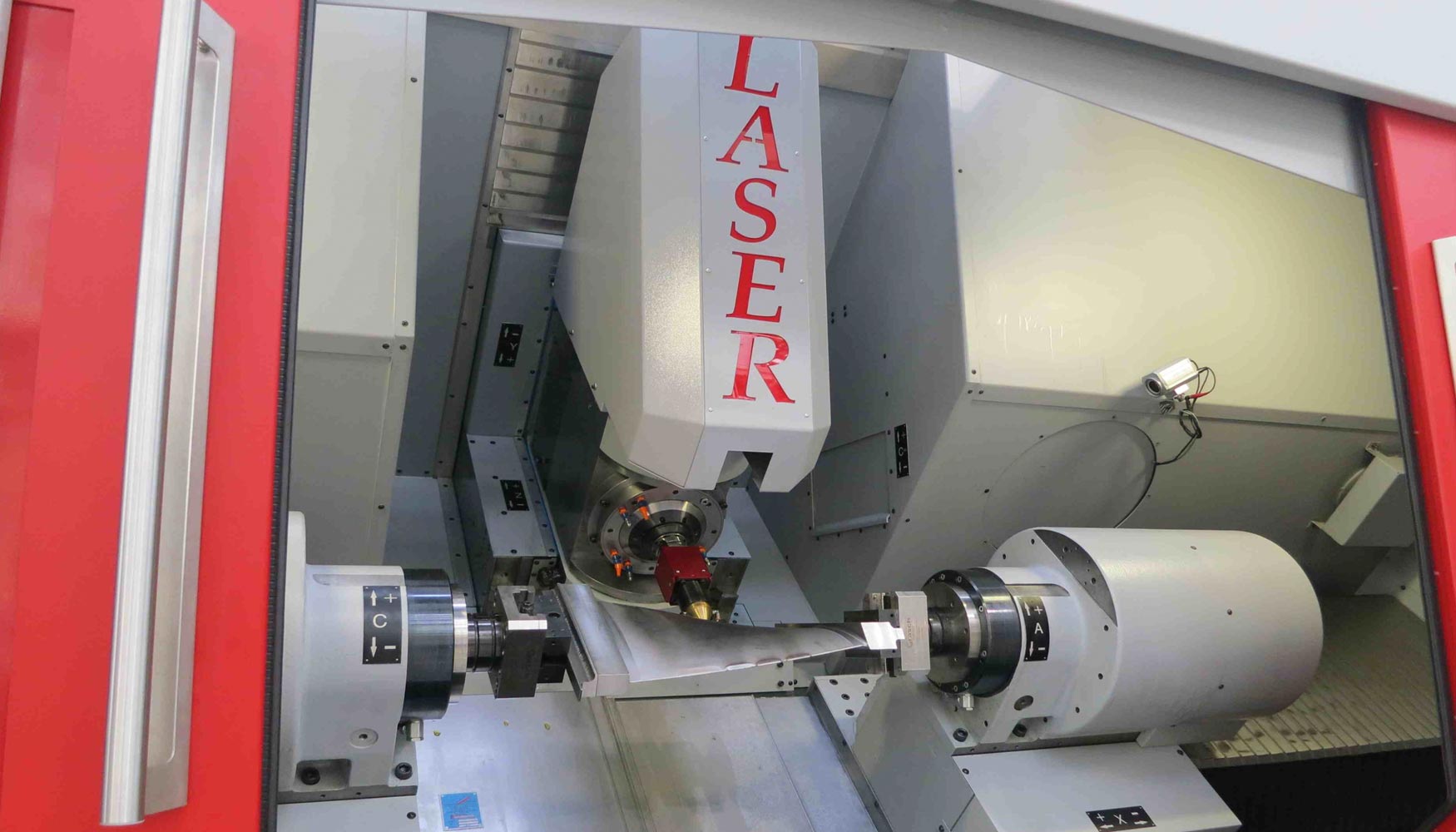
A modo de conclusiones
La incorporación de sistemas de aporte de material a equipos avanzados de mecanizado comienza a ser una realidad en la actualidad. Se trata de una tecnología que todavía tiene camino por delante antes de convertirse en una alternativa madura, pero comienza a emplearse en algunas aplicaciones puntuales (como la reparación de puntas de álabes de turbina) y muchos sectores están vigilando de cerca los avances que se están dando.
A lo largo de este artículo se han presentado las principales ventajas e inconvenientes de estos sistemas, así como un listado de los equipos existentes en la actualidad y que incorporan estos avances. Es difícil hacer una estimación de hasta dónde va a llegar esta tecnología, pero todo apunta a que se va a ir desarrollando y aplicando en diferentes sectores.
La monitorización de la temperatura durante el proceso de LMD: un chivato controlable
La monitorización de la temperatura durante el procesado superficial de materiales con tecnologías láser, como los tratamientos térmicos por láser o los procesos de fabricación aditiva, es una acción clave con la que se puede llegar a controlar la validez del tratamiento o proceso de fabricación. Por ejemplo, durante el proceso de temple por láser se monitoriza y controla la temperatura en lazo cerrado para mantenerla constante durante el proceso o, en otras ocasiones, se estudian, tras el temple, las temperaturas registradas durante el proceso para dar por válida o rechazar la pieza.
Por ello, la medición de temperatura durante los procesos superficiales por láser, se puede realizar mediante sensores ópticos que miden la temperatura sin contacto, como son los pirómetros o las cámaras termográficas. Por un lado, los pirómetros (Dr. Mergenthaler, Impac, …) son sensores de medición puntual que se dividen principalmente en dos tipos: los monocromáticos y los multi-cromáticos, o de varios colores. En los primeros es necesario introducir valores de emisividad para medir la temperatura real mientras que los multi-cromáticos recogen la temperatura real directamente, en base a un considerable aumento en el precio y a un menor rango de medición, con temperaturas mínimas que rondan los 300 °C. Por otro lado, las cámaras termográficas (Optris, Flir, …) se pueden definir cómo una matriz de pirómetros monocromáticos que tienen la gran ventaja de medir temperatura simultáneamente en un área, pero, es estrictamente necesario introducir correctamente la emisividad para dar con la medida de temperatura real.
Así, el concepto de medición óptica, ya sea con pirómetros o con cámaras termográficas, en procesos donde la herramienta de trabajo es un láser permite dos variantes de configuración: la medida coaxial al camino óptico del láser, donde el sensor se integra en el cabezal de la máquina, y la medida exterior, donde el sensor se posiciona externamente al cabezal, en el espacio de trabajo de la máquina láser.
En lo que se refiere al proceso de LMD (Laser Material Deposition), la correcta medición y monitorización de la temperatura durante el proceso proporciona datos sobre la calidad de la pieza final tras el proceso o, también, avisa de que algo no se ésta desarrollando correctamente durante el proceso. En este caso, las variaciones de la temperatura medida durante el aporte, si este se realiza con una velocidad de avance de máquina constante, pueden deberse a dos factores: a un recalentamiento local de la superficie o a un aporte de material irregular. En primer lugar, un recalentamiento local provoca una coloración desigual en las distintas zonas y advierte de que el aporte no es regular en las distintas zonas; creándose mayores distorsiones y defectos, como mayor porosidad, que afectan a la integridad de la pieza final. Por otro lado, una variación de temperatura debida a un aporte irregular, se debe a que la posición del foco del sensor de medición óptico respecto a la superficie de material que se está aportando va variando, dando un error en altura sobre la superficie de la pieza. Esta altura irregular es debida a un aporte de polvo irregular por un mal ajuste de la boquilla o por una variación incontrolada de la velocidad de avance de la máquina, entre otros factores.
Así, en lo que se refiere a la monitorización de la temperatura durante el proceso de LMD, por parte del departamento de Ingeniería Mecánica de la Universidad del País Vasco (UPV/EHU) se está estudiando la forma más correcta de medir la temperatura, la influencia de la variación de temperatura en la defectología final de la pieza, así como, la posible minimización de esos defectos mediante la medición y control de la temperatura in-process.
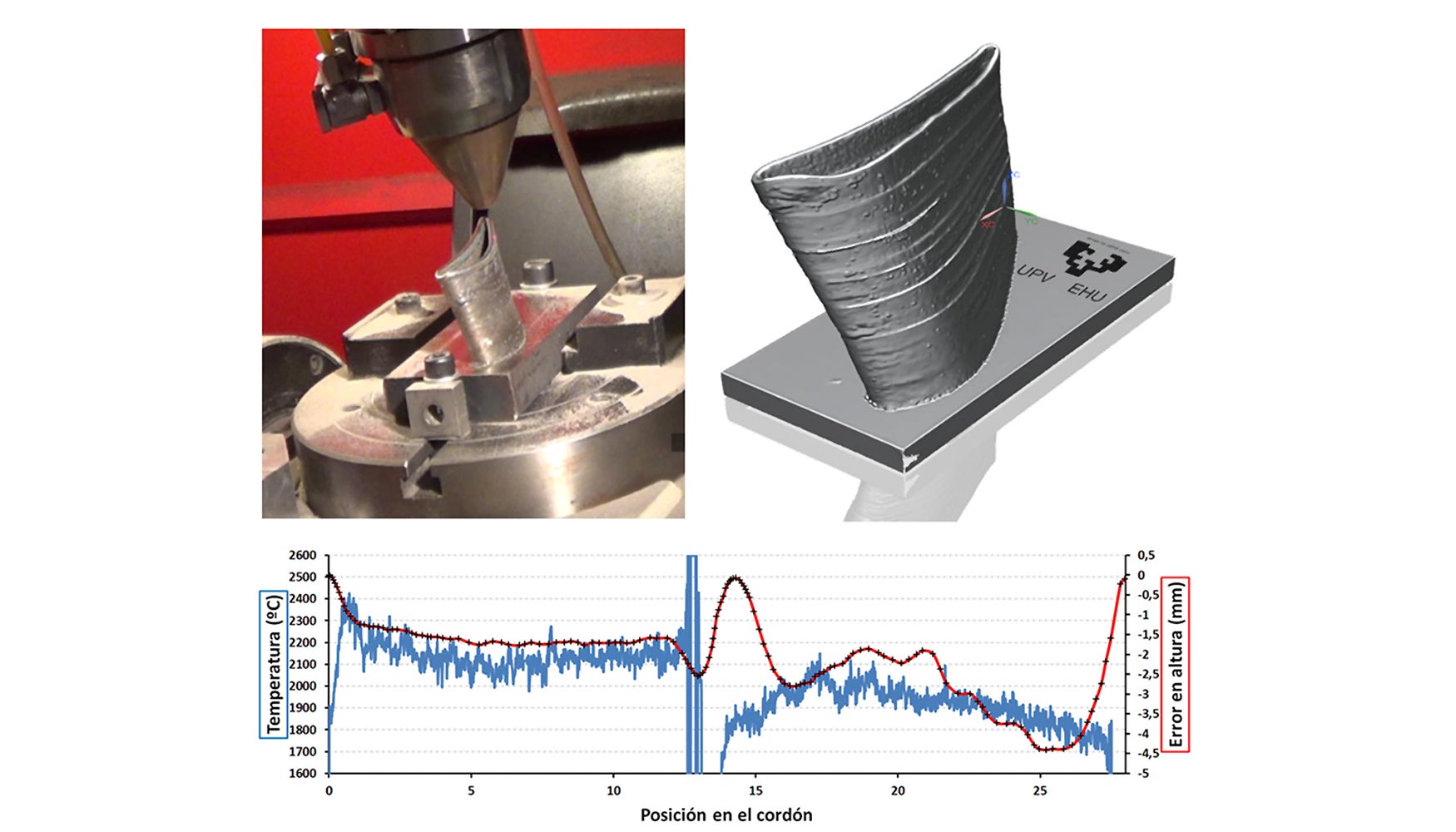
Reciclado de polvo en el proceso de LMD
El proceso de fabricación aditiva denominado como LMD (Laser Metal Deposition) se basa en el aporte o deposición de un polvo metálico que se hace pasar a través de una boquilla y se proyecta sobre la pieza o sustrato en el interior de un baño fundido que se ha creado por calentamiento, usando un haz láser como fuente de calor. El proceso de LMD presenta una desventaja importante y es la baja eficiencia del polvo aportado, es decir, el ratio entre la cantidad de polvo que sale de la boquilla y la que finalmente queda adherida al substrato es muy bajo. Normalmente, la eficiencia depende de la configuración del sistema de aporte de LMD (tamaño del haz láser, diseño de la propia boquilla, etc.). Así, un valor típico de eficiencia es el 40%, pero, en el peor de los casos, se puede desperdiciar hasta el 95%.
Una de las principales aplicaciones del proceso de LMD es la reparación de piezas de alto valor añadido. Por ello, es común el uso de polvos metálicos de superaleaciones (Ti6Al4V, Inconel® 718, Waspaloy™, ...). Estos polvos metálicos, además de las especificaciones en composición propias de la aleación, deben de cumplir estrictas restricciones en cuanto a tamaño de grano, geometría y calidad superficial; se utilizan polvos de granulometría esférica, sin protuberancias o bultos en la superficie, producidos por atomización por gas. Así, por las razones expuestas, la producción de este polvo tiene un costo que puede triplicar o cuadruplicar el valor de un tocho del mismo material fabricado por fundición. Además, por su tamaño micrométrico, en un rango entre 45-150 micras en el proceso de LMD, es un tipo de desperdicio difícil de tratar y procesar, de ahí que su recuperación y reciclado a nivel industrial presente ventajas muy claras.
La recuperación del polvo es un proceso relativamente sencillo que se puede dividir en tres etapas: la recolección del polvo metálico que sale rebotado de la zona de trabajo, el reacondicionamiento del mismo y la evaluación de su composición química y de sus propiedades mecánicas.
El propósito general de la recolección es evitar la contaminación con sustancias ajenas, por ejemplo con aceite, del polvo que se proyecta desde la zona donde se está aportando. Para ello, es conveniente considerar como parte del utillaje de la pieza a reparar un sistema de recolección del polvo metálico. En algunas ocasiones, en función de la reactividad del polvo, es posible el uso de un sistema de aspiración por vacío. Por otro lado, debido a posibles contaminaciones u oxidaciones, es recomendable evitar que el polvo metálico esté expuesto demasiado tiempo al medio ambiente.
El reacondicionamiento consiste en la separación por granulometría del polvo recolectado. Para ello, se le hace pasar a través de tamices que reproduzcan distintos rangos granulométricos, recogiendo únicamente los deseados para el polvo reciclado. En ciertas ocasiones, dependiendo del tipo de aleación, es posible separar fases indeseables por medio de imanes. Tras esto, es conveniente una etapa de secado para retirar toda humedad acumulada ya que los polvos metálicos son altamente higroscópicos.
La última etapa sería el análisis del polvo reciclado para ver si cumple las especificaciones para su reutilización. Esta etapa se realizaría una única vez tras cada cambio en los parámetros del proceso. Por un lado, se evalúa la composición química del polvo reciclado por medio de microscopía electrónica de barrido o por medio de rayos X, donde se analizan muestras de polvo reciclado en busca de cambios en su composición respecto de la original. Además, en esta etapa es importante analizar el contenido de óxidos de la aleación. Por otro lado, se evalúan, comparándolas con las de polvo metálico nuevo, las propiedades mecánicas de probetas fabricadas por el proceso de LMD a partir de polvo reciclado que se someten a ensayos estándar de tracción y fatiga, entre otros. En función de los resultados de las propiedades mecánicas y químicas del polvo reciclado se determinará si es recomendable o no su reutilización.
Para concluir, decir que es sensato evaluar la posibilidad de reutilizar el polvo metálico no aprovechado en el proceso de LMD. Si las tres etapas descritas se realizan con precaución, es posible obtener piezas con las mismas propiedades, tanto químicas como mecánicas, que las fabricadas a partir de polvo metálico nuevo, con el ahorro económico que conlleva.
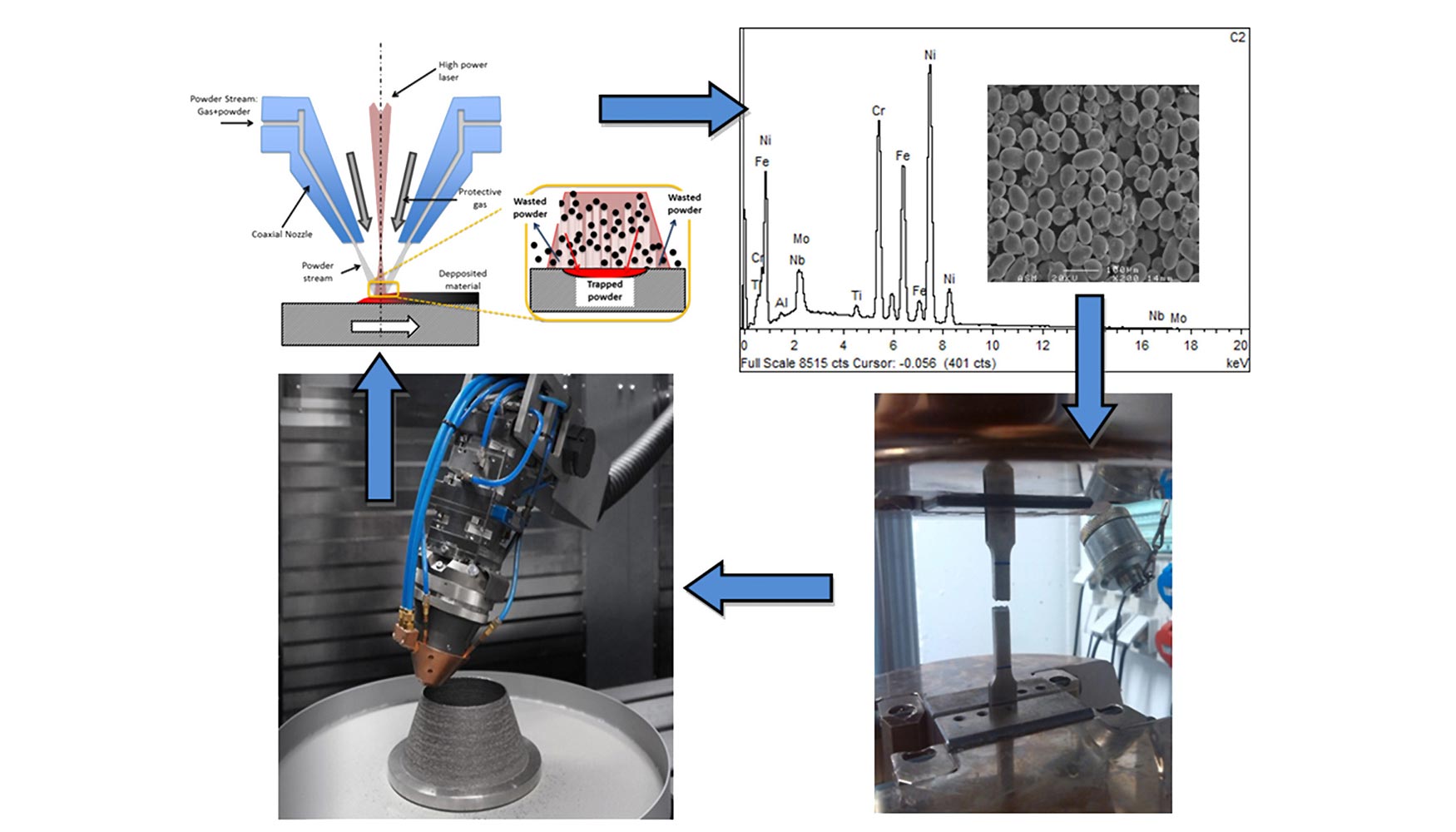