Mecanizado de componentes aeronáuticos con alto requerimiento de integridad superficial
El objetivo de este trabajo es describir una metodología de trabajo para estudiar la integridad superficial y vida a fatiga de componentes críticos mecanizados a través de ensayos realizados en laboratorios. Esta metodología permitirá optimizar o modificar los parámetros de procesos de mecanizado de una manera más ágil asegurando la integridad superficial y comportamiento del componente a lo largo de la vida en servicio. Concretamente la metodología definida se presenta a través de un ejemplo, donde se analiza la influencia de la geometría de la herramienta en la integridad superficial y vida a fatiga al tornear discos de la aleación de base níquel Inconel 718. En primer lugar se describen los ensayos de mecanizado, análisis topográfico, medición de tensiones residuales, medición de microdurezas, observaciones microscópicas y ensayos a fatiga. A continuación se analizan los resultados, los cuales confirman que la vida a fatiga de las probetas del disco con mejor integridad superficial son sensiblemente más largas. Finalmente se recomienda el empleo de la herramienta empleada en el mecanizado del disco con mejor integridad superficial.
1. Introducción
El transporte aéreo ha evolucionado considerablemente desde sus inicios y es actualmente uno de los medios de transporte más importantes. Concretamente, el continuo desarrollo de los motores aeronáuticos ha sido uno de los factores principales en la evolución del transporte aéreo, permitiendo aumentar la capacidad de pasajeros por siete y triplicar la autonomía de los vuelos durante los últimos 60 años [1]. Los motores aeronáuticos cada vez deben enfrentarse a temperaturas de trabajo más elevadas, y para ello se han desarrollado nuevas aleaciones resistentes con excelentes propiedades mecánicas y químicas a temperaturas elevadas [1]. El desarrollo de estas aleaciones resistentes a altas temperaturas junto con los avances en tecnologías de fabricación ha permitido fabricar motores más eficientes y más potentes [2]. Las aleaciones resistentes a altas temperaturas empleadas en la fabricación de motores aeronáuticos se pueden clasificar en cuatro grupos [2]: aleaciones de base níquel, aleaciones de base cobalto, aleaciones de base hierro y aleaciones de titanio. Dependiendo de las cargas mecánicas que debe de soportar el componente y la temperatura de trabajo se selecciona una aleación u otra. Por ejemplo, las aleaciones de base níquel se emplean en las zonas con mayores presiones y temperaturas de trabajo, mientras que las aleaciones de titanio se utilizan en las zonas con temperaturas de trabajo más bajas.
Los componentes de motores aeronáuticos se clasifican como críticos o no críticos dependiendo de las consecuencias que pueda acarrear un mal funcionamiento del componente en el avión. Por ejemplo, los discos de turbina se clasifican como componentes críticos aeronáuticos. Los discos de turbina almacenan una gran cantidad de energía cinética, sobre todo durante las secuencias de despegue-aterrizaje. Bajo estas condiciones de trabajo se generan elevadas tensiones cíclicas que ocasionalmente pueden producir fallos por fatiga de bajos ciclos [3]. En consecuencia, un segmento fracturado de un disco de turbina contiene una enorme cantidad de energía [1] y al impactar sobre la estructura puede poner en alto riesgo la seguridad del propio avión y pasajeros. Por ello, el diseño y fabricación de componentes críticos es meticuloso, con el fin de asegurar la seguridad del propio avión, tripulación y pasajeros.
Generalmente en la última etapa de fabricación de componentes críticos de motores aeronáuticos, tales como discos de turbina, se realizan operaciones de mecanizado. Las aleaciones resistentes a altas temperaturas son difíciles de mecanizar debido a los siguientes factores [2]:
- Baja conductividad térmica
- Tendencia a endurecimiento
- Tenencia a producirse filo recrecido
- Presencias de carburos abrasivos en la microestructura
Por lo tanto, si las condiciones de mecanizado no se seleccionan adecuadamente, la integridad superficial del componente mecanizado puede verse afectada adversamente (daño microestructural, rugosidad superficial excesiva y tensiones superficiales tractivas). Si no se cumplen los requerimientos de integridad superficial la vida a fatiga de los componentes críticos puede reducirse de forma drástica. Por ello, durante el proceso de fabricación de componentes críticos aeronáuticos se realizan controles exigentes con el fin de asegurar el correcto funcionamiento y seguridad a lo largo de toda la vida en servicio del componente [4]. En consecuencia, la fabricación de estos componentes es muy conservativa y los parámetros de procesos son muy difíciles de modificar: una vez que las condiciones de corte se han validado frente a un ensayo RIG, estas condiciones son congeladas. Bajo estas reglas, el proceso de mecanizado muy difícilmente se puede optimizar. Bajo este contexto, muchos investigadores han estudiado la integridad superficial generada en las aleaciones resistentes a altas temperaturas [5, 6]. Otra evidencia de la importancia del tema es que la prestigiosa academia internacional CIRP (College International pour la Reserche en Productique) ha organizado conferencias específicas sobre integridad superficial en Bremen (2011) y Nottingham (2014). Todos estos esfuerzos han permitido comprender la influencia de las condiciones de mecanizado en la integridad superficial de estas aleaciones. Sin embargo, a pesar de que se presupone que las alteraciones superficiales pueden ser perjudiciales para la vida a fatiga, existen muy pocas investigaciones en este campo, y la relación entre la integridad superficial y el comportamiento a fatiga todavía no está bien establecida [7].
El trabajo que se presenta se ha realizado dentro del marco de colaboración entre la empresa fabricante de componentes de motores aeronáuticos ITP S.A. y Mondragon Unibertsitatea. El objetivo es definir una metodología de trabajo que permita estudiar y comprender la influencia de los parámetros de los procesos de mecanizado en la integridad superficial y vida a fatiga a través de ensayos realizados en laboratorio. El conocimiento adquirido servirá para modificar, optimizar o recomendar las condiciones a emplear en los procesos de mecanizado asegurando la integridad superficial y comportamiento a fatiga de los componentes mecanizados a lo largo de toda su vida en servicio. La figura 1 muestra de forma esquemática la metodología definida.
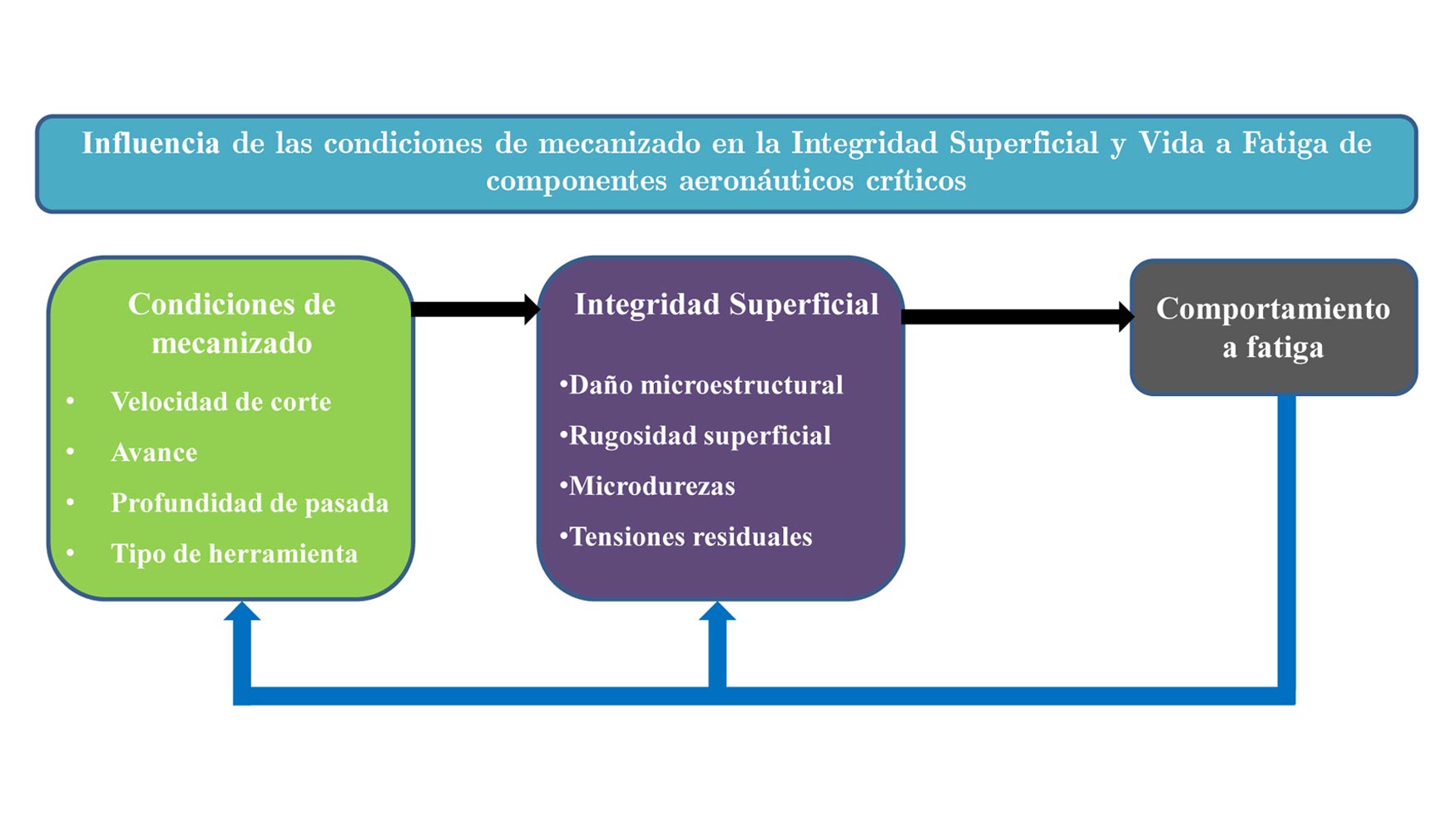
Concretamente en esta comunicación la metodología definida se presenta a través un ejemplo. Se analiza la influencia de la geometría de herramienta en la integridad superficial y vida a fatiga al tornear discos de Inconel 718 bajo condiciones de acabado empleadas en el sector aeronáutico.
2. Metodología
2.1. Material
En este trabajo se han empleado dos discos forjados de Inconel 718 de 7 mm de espesor con un tamaño medio de grano G9 según ASTM. Los discos se obtuvieron a partir de una forja de disco de turbina TP400. Concretamente, los discos se extrajeron mediante electroerosión con hilo de la zona central, tal y como se muestra en la figura 2. La composición química del material se muestra en la tabla 1. La microestructura puede observarse en la figura 3, la cual consiste en una matriz austenítica con estructura cúbica centrada en las caras y precipitados ɣ.
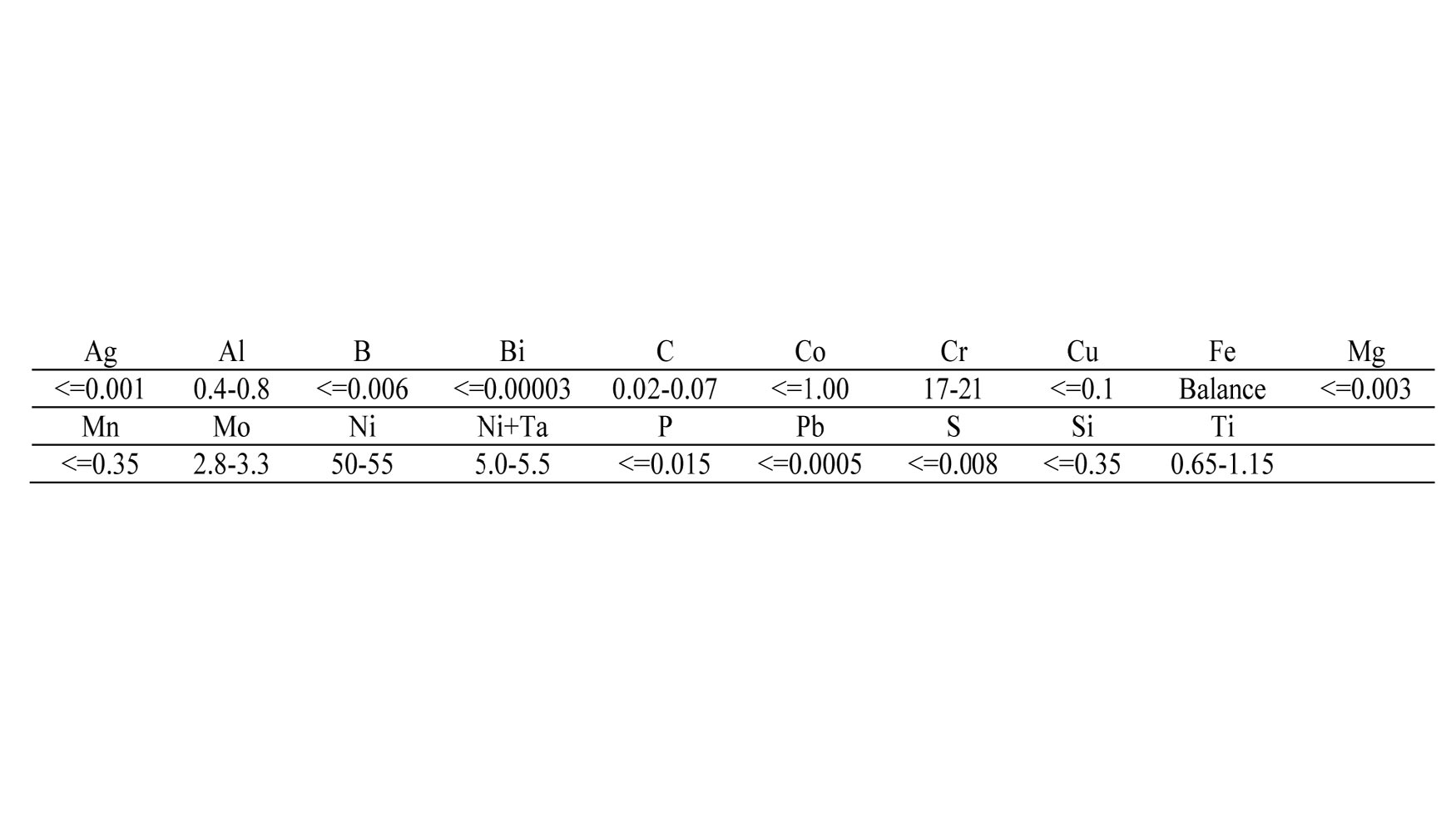
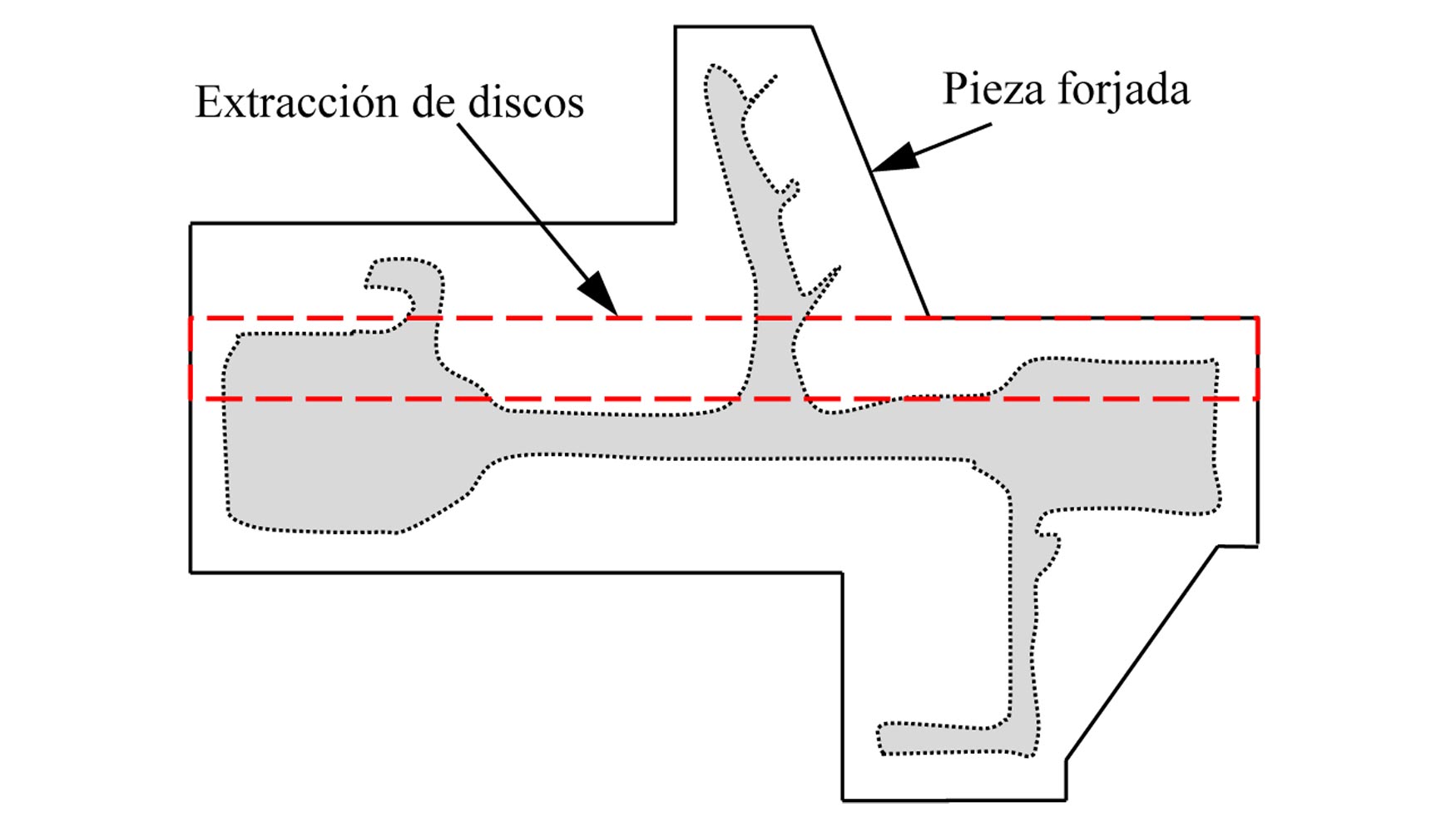
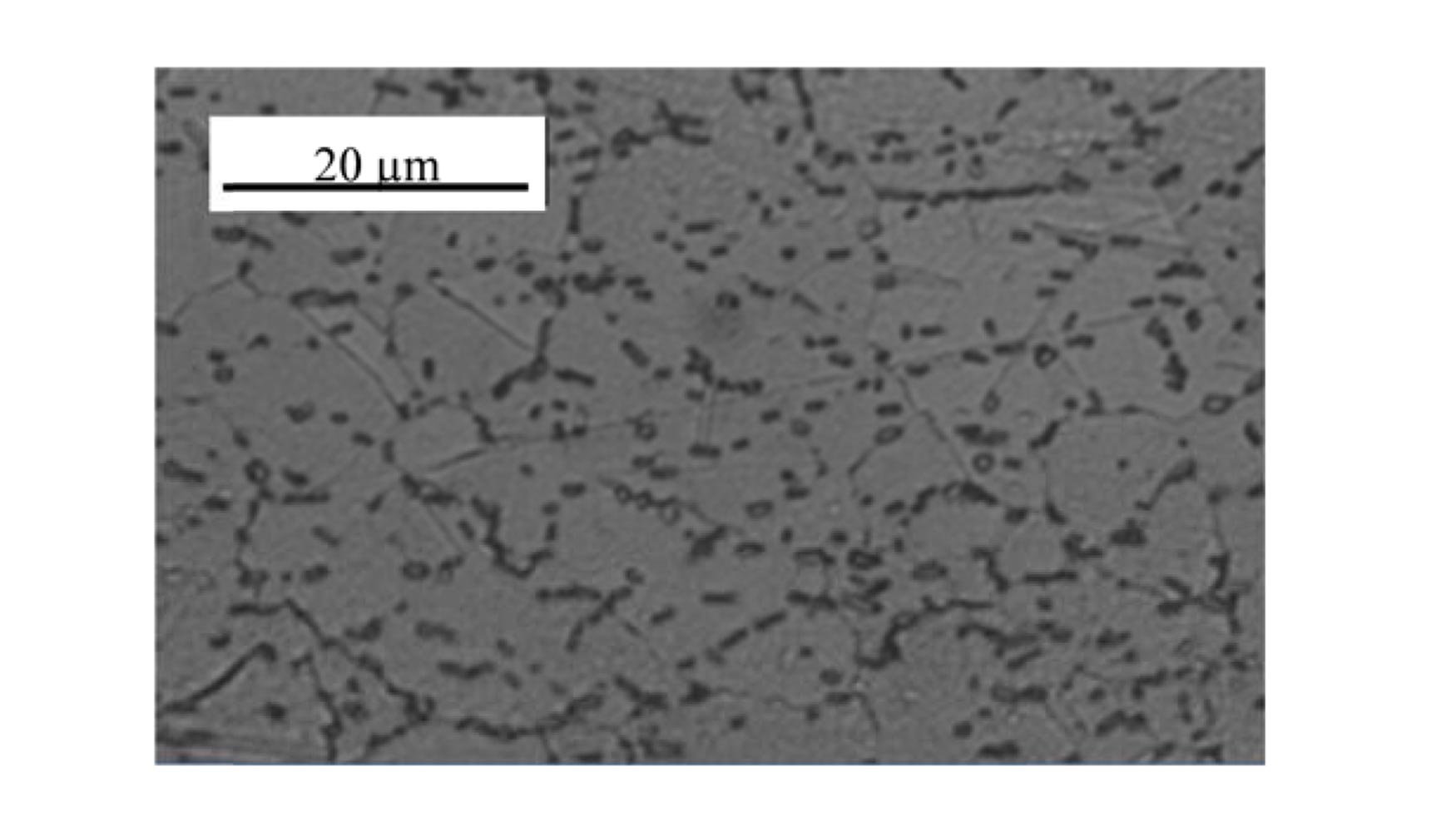
2.2. Ensayos de mecanizado y preparación de probetas
En primer lugar los dos discos forjados e 7 mm de espesor se cortaron para obtener piezas en forma de anillo con un diámetro exterior de 530 mm y diámetro interior de 260 mm. Posteriormente ambos discos con forma de anillo se fjaron en un torno vertical Danobat TV700 (potencia de 71 kW y un par máximo de 1.000 Nm) empleando unos utillajes especiales. Cad uno de los discos se mecanizado empleando herramientas de carburo cementado pero de distinta geometría. Por motivos de confidencialidad la geometría de las herramientas no se indica en este artículo y se denominarán como herramienta tipo A y herramienta tipo B respectivamente.
Tras preparar la superficie de los discos a través de operaciones de desbaste, ambos discos se mecanizaron empleando idénticas condiciones de corte habitualmente utilizadas en las operaciones de acabado de discos de turbina de motores aeronáuticos. La cara superior e inferior del disco se refrentó con una herramienta nueva, llevando a cabo tres pasadas, hasta obtener un espesor final de 4 mm en la región intermedia (ver figura 4). Al mecanizar una nueva pasada los últimos 5 mm de la pasada anterior (medidos en dirección radial) no sé mecanizaron. Consecuentemente, la sección transversal del anillo forjado mostraba un escalón correspondiente a cada pasada, tal y como se ha representado esquemáticamente en la figura 3: S1, S2 y S3 son los escalones correspondientes a la primera, segunda y última pasada de la superficie superior; I1, I2 y I3 son los escalones correspondientes a la primera, segunda y última pasada de la superficie inferior. Estos escalones se utilizaron para medir la rugosidad superficial, tensiones residuales y observaciones de la microestructura como se explicarán más en detalle a lo largo del artículo.
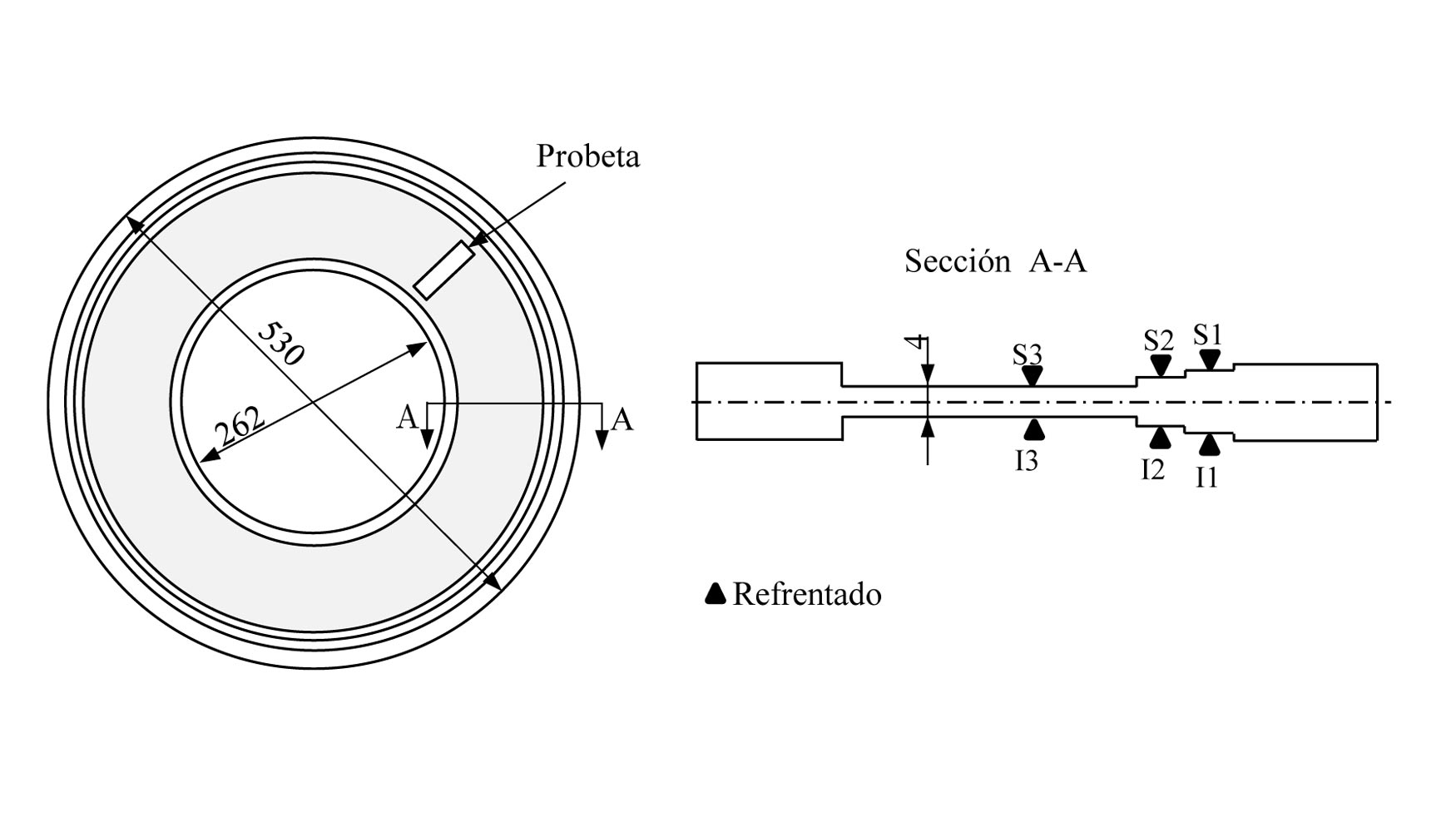
Finalmente, se extrajeron probetas para los ensayos de fatiga de la región intermedia de los discos (superficie representada en gris en la figura 4) mediante electroerosión por hilo. El eje longitudinal de las probetas estaba alineado con la dirección radial de los discos mecanizados. La geometría de las probetas empleadas en los ensayos de fatiga se puede observar en la figura 5. Las aristas de las probetas fueron redondeadas y las superficies laterales fueron rectificadas para quitar la superficie dañada por el proceso de electroerosión.
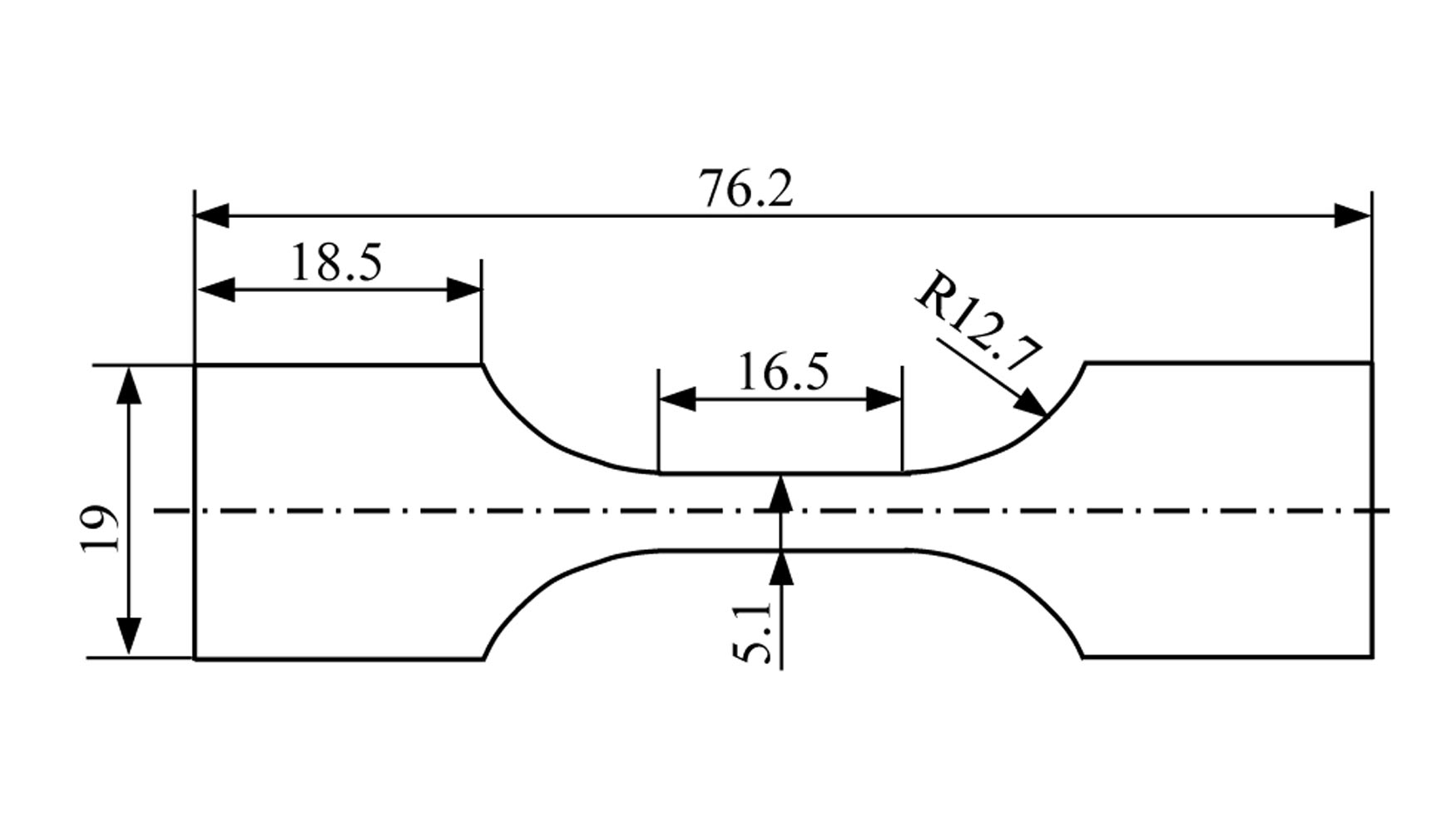
2.3. Mediciones de rugosidad superficial
Para caracterizar la rugosidad superficial de ambos discos se empleó un rugosímetro portátil Mitutoyo SJ-210. Concretamente se midieron los siguientes parámetros: rugosidad media (Ra), distancia máxima pico-valle (Rt), distancia media pico-valle (Rz), la raíz cuadrada de la desviación media del perfil medido (Rq) y el valor del pico más alto medido desde la línea media (Rp). Las mediciones se repitieron cinco veces sobre cada uno de los escalones en diferentes posiciones y se calculó el valor medio para el posterior análisis de integridad superficial.
2.4. Mediciones de tensiones residuales
Las tensiones residuales generadas por el proceso de refrentado se midieron empleando la técnica hole drilling. Para ello se siguieron las recomendaciones indicadas en la guía técnica The measurement of residual stresses by the hole drilling technique [8]. A pesar de que existe la normativa ASTM E357 para la medición de tensiones residuales empleando la técnica hole drilling, en este trabajo se utilizó el procedimiento fine increment hole drilling desarrollado por Grant et al. [9]. Las tensiones residuales originadas por los procesos de mecanizado se concentran en una región muy superficial, mostrando un alto gradiente de tensiones residuales en las primeras 50 μm de profundidad. La metodología descrita en la normativa ASTM E357 está muy limitada para esas aplicaciones y se puede perder información crítica en las mediciones de tensiones residuales. Por ello, el empleo de incrementos de taladrado pequeños, tal y como proponen Grant et al. [9], resultan interesantes para medir tensiones residuales generadas por los procesos de mecanizado obteniendo resultados semejantes a los obtenidos por la técnica de difracción por rayos X. En primer lugar las superficies de los puntos de medición de tensiones residuales fueron preparadas para poder pegar las rosetas extensométricas siguiendo los pasos que se describen:
a) limpieza de la superficie con acetona, b) lijado de la superficie con liga de grado 1000, c) acondicionado de la superficie con un ácido de base agua para limpiar superficies y d) neutralización de la superficie empleando un alcalino de base agua para medir superficies.
A continuación se pegaron las rosetas modelo EA-06-031RE-120 del grupo Vishay. Los discos se fijaron en el interior de una microfresadora Kern Evo (ver Figura 6a). Antes de realizar el agujero la herramienta de corte se alineó con el centro de la galga. A continuación se realizó el agujero realizando un total de 16 incrementos: 4x16 μm, 4x32 μm y 8x64 μm. Las deformaciones experimentadas por las rosetas se grabaron en un equipo de adquisición de datos National Instrument después de cada incremento. Finalmente, los perfiles de tensiones residuales se calcularon utilizando el método integral propuesto por Schajer [10]. Concretamente, las tensiones residuales se midieron en la superficie de la primera pasada y en la mitad de la región intermedia (coincidente con la zona calibrada de las probetas de fatiga) de ambos discos mecanizados. La Figura 6b representa esquemáticamente la posición de los puntos de medida: A1, B1 y C1 están localizados en la superficie de la primera pasada; A2, B2 y C2 están localizados en la superficie de la pasada final.
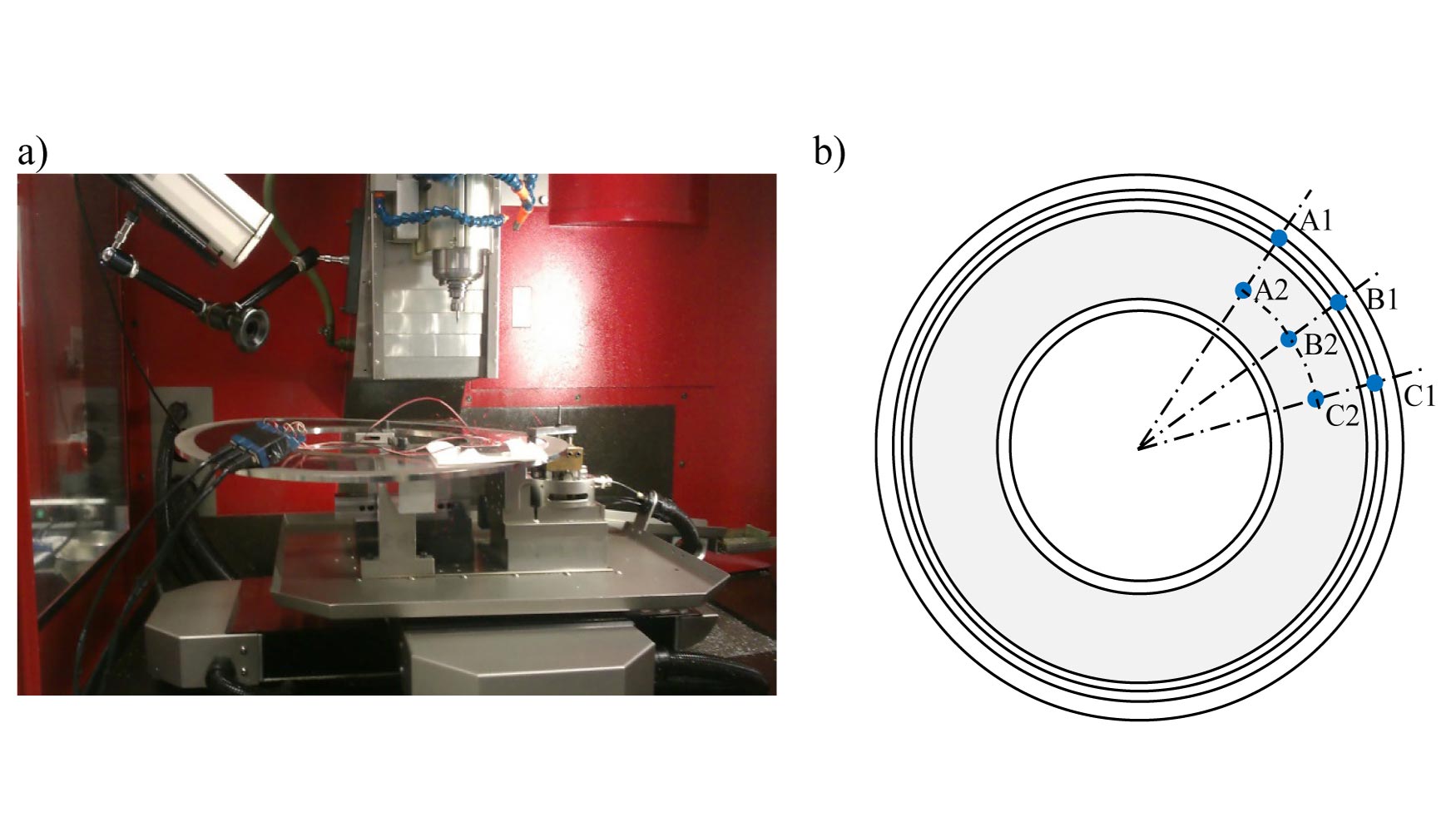
2.5. Observaciones de la microestructura en la capa superficial
Se extrajeron muestras de ambos discos mecanizados mediante corte por electroerosión por hilo para observaciones microestructurales. Concretamente, las muestras se obtuvieron de los escalones correspondientes a la primera pasada, segunda pasada y de la región intermedia de los discos (ver figura 4). Las muestras se engastaron en una resina fenólica, a continuación se lijaron empleando lijas de carburo de silicio y finalmente se pulieron hasta obtener la calidad superficial deseada. A continuación las muestras se atacaron químicamente empleando la solución Grandy. La microestructura de las muestras se observó en un microscopio óptico Leica DM IRM.
2.6. Mediciones de microdurezas
Las muestras para mediciones de microdurezas de obtuvieron de la región intermedia de los discos mecanizados (región coincidente con la zona calibrada de las probetas de fatiga) mediante corte por electroerosión por hilo. Antes de realizar los ensayos de microdurezas las muestras se engastaron en una resina fenólica y se pulieron. Finalmente, los ensayos de microdurezas se realizarón en un microdurómetro Zwick empleando un indentador Vickers con una carga de 100 g y aplicándolo durante 15 s. Concretamente se realizarón 10 mediciones de microdurezas a 20, 40, 80, 150 y 250 μm de profundidad.
2.7. Ensayos de fatiga isoterma a bajos ciclos
Las probetas obtenidas de ambos discos mecanizados con diferentes herramientas de corte se ensayaron a fatiga bajo condiciones de bajos ciclos a 450 °C en control por fuerza según la norma ASTM E466 07. Para ello se empleó un equipo servohidráulico MTS, con capacidad de carga de 100 kN y equipado con un horno de inducción. Las probetas se ensayaron en tres niveles de carga, con tensión máxima aplicada por encima del límite elástico del material para garantizar condiciones de fatiga a bajos ciclos. Los ensayos se realizaron empleando una onda trapezoidal (1-1-1-1) y ratio de carga R=0. El criterio de fallo establecido fue la rotura de la probeta.
3. Resultados y discusión
3.1. Rugosidad superficial
La tabla 2 muestra los resultados de las mediciones de rugosidad sobre la superficie de las distintas pasadas realizadas en el disco mecanizado con la herramienta tipo A y en el disco mecanizado con la herramienta tipo B. Los resultados se presentan normalizados, tomando como referencia el menor valor de cada uno de los parámetros empleados para caracterizar la rugosidad superficial. Tal y como se observa en la tabla 2 los parámetros de rugosidad superficial (Ra), distancia máxima pico-valle (Rt), distancia media pico-valle (Rz), la raíz cuadrada de la desviación media del perfil medido (Rq) y el valor del pico más alto medido desde la línea media (Rp) en general mostraron valores similares en las tres pasadas realizadas con cada una de las herramientas. Estos resultados son los esperados ya que las condiciones de corte fueron idénticas en las tres pasadas y el desgaste de la herramienta no fue severo (desgaste de flanco VB < 0,12 mm en la herramienta tipo A y VB < 0,22 mm en la herramienta tipo B). Sin embargo, la rugosidad superficial obtenida con la herramienta tipo B mostro valores aproximadamente 4 veces superiores que al mecanizar con la herramienta tipo A. Por lo tanto, estos resultados evidencian la influencia de la geometría de la herramienta en la rugosidad superficial de la pieza mecanizada.
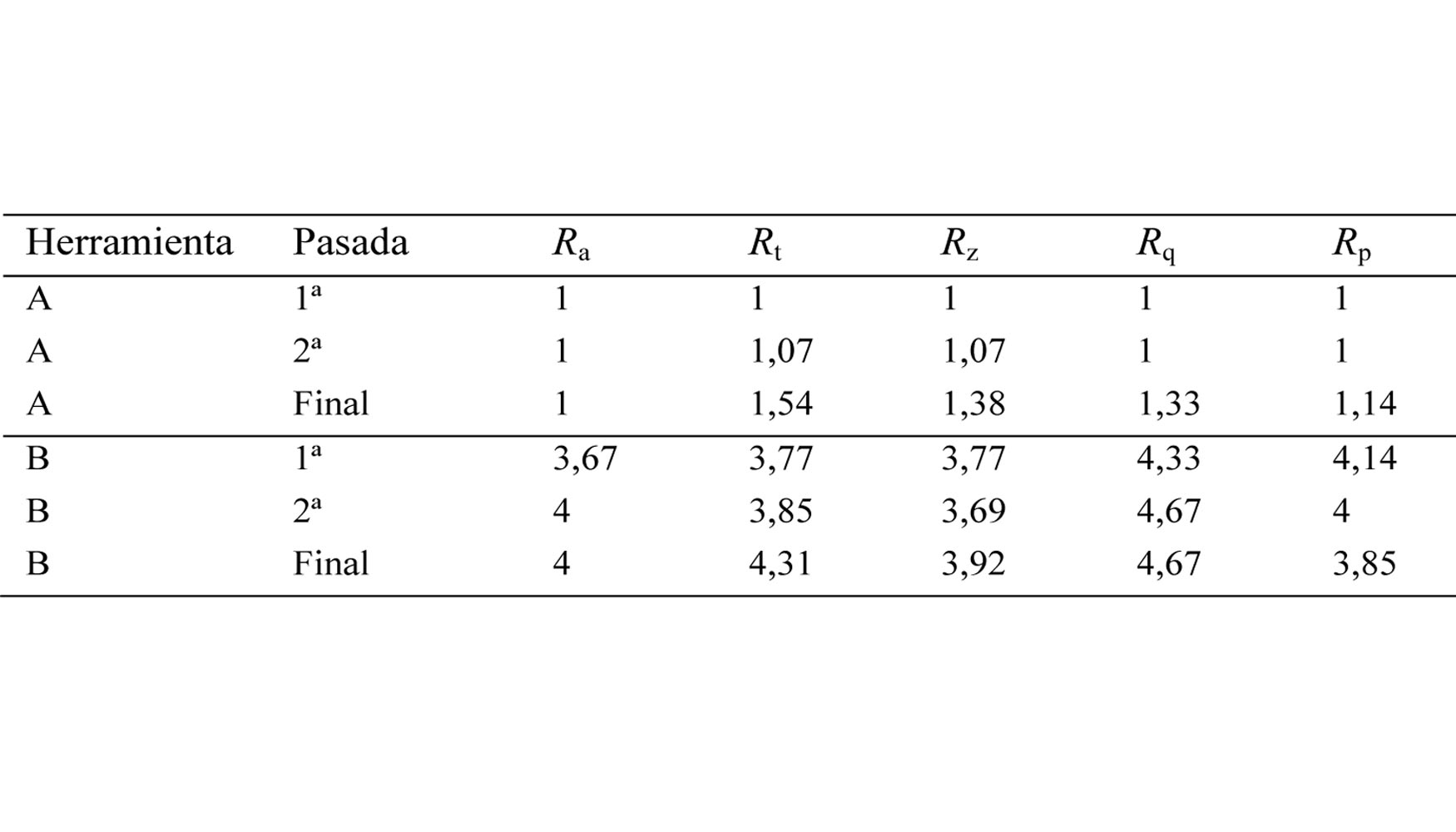
3.2. Tensiones residuales
La figura 7 compara los perfiles de tensiones residuales medidos en la superficie de los dos discos mecanizados. Hay que señalar que los valores de tensiones residuales se muestran normalizados frente al valor de tensión residual superficial máximo obtenido en las mediciones. El perfil de tensiones residuales mostró una forma similar en todos los casos (ver figura 7): en general las tensiones residuales son tractivas en la superficie y rápidamente pasan a ser compresivas. A continuación alcanzan un pico de compresión máximo a una profundidad aproximada de 70-75 μm y finalmente se relajan hasta estabilizarse en torno valores nulos a una profundidad de ≈ 200 μm. Los perfiles de tensiones residuales obtenidos en este trabajo muestran una forma y magnitud similar a la obtenida por otros autores al tornear Inconel 718 en similares condiciones [11-13]. Las tensiones residuales superficiales generadas por la herramienta tipo B fueron más tractivas tanto en la dirección de corte (Figura 7a) como en la dirección de avance (Figura 7b). Esta tendencia se cumplió tanto en la superficie de la primera pasada (señalado como t1 en las figuras) como en la superficie final (señalado como t2 en las figuras). Las tensiones residuales superficiales suelen ser más tractivas si predomina el efecto térmico generado por el proceso de corte y suelen ser más compresivas si predomina el efecto mecánico asociado a las fuerzas de corte [13]. Por lo tanto, se puede concluir que en las condiciones de corte empleadas en este estudio el efecto térmico fue predominante y éste fue más significativo con las herramientas tipo B.
En general el pico de tensión residual de compresión también fue mayor al emplear herramientas tipo B tal y como se puede observar en la figura 7. Cabe destacar que tanto el valor del pico máximo de compresión como la profundidad del pico máximo de compresión aumentaron considerablemente en la pasada final al emplear herramientas tipo B. Posiblemente este aumento puede estar asociado al mayor desgaste presentado por las herramientas tipo B. Al aumentar el desgaste las fuerzas de mecanizado, y sobre todo las de penetración, dando lugar a una mayor deformación en la capa afectada por el mecanizado.
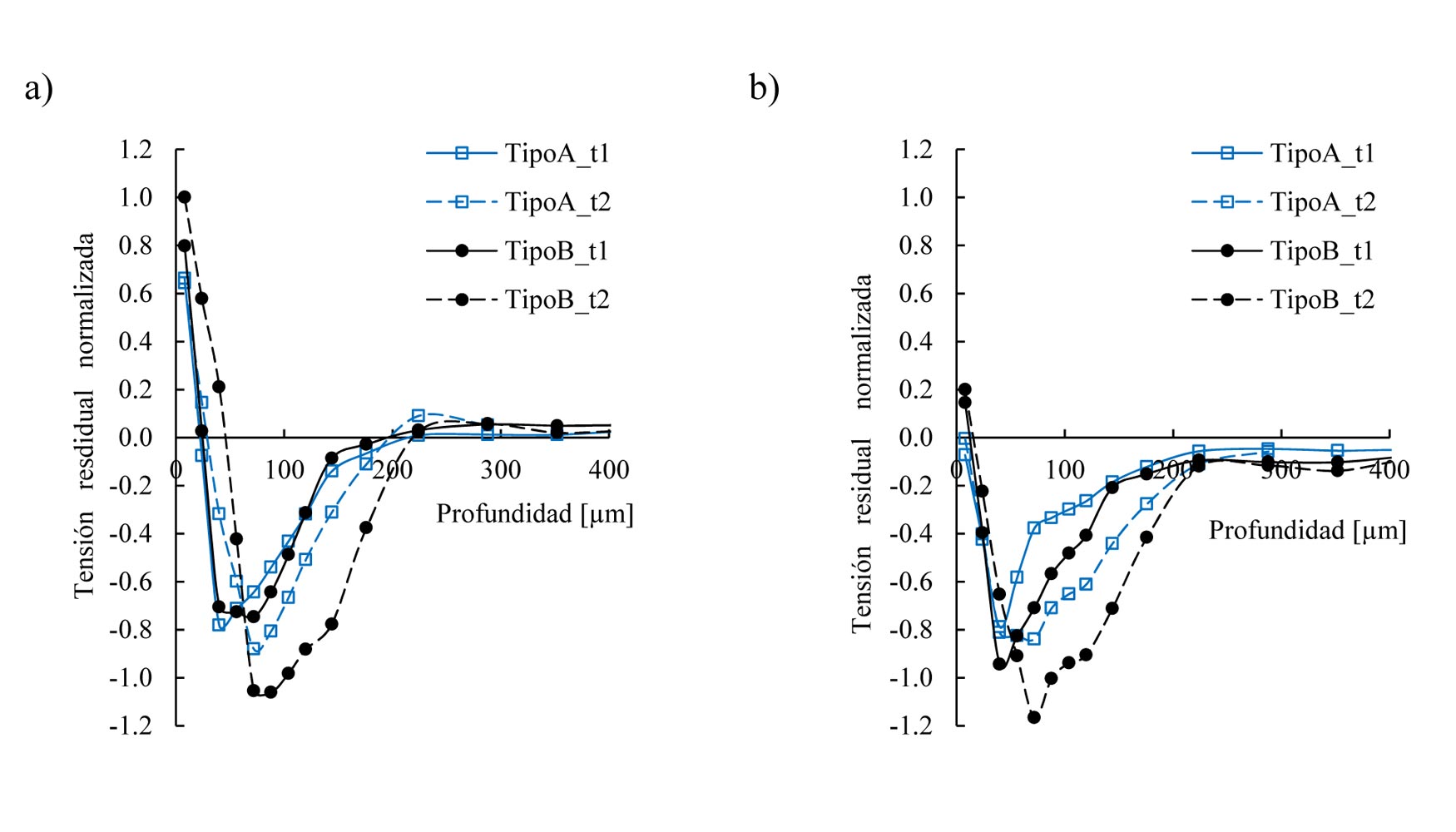
3.3. Daño microestructural
Tal y como se ha expuesto en el procedimiento experimental se observaron en un microscopio óptico las muestras obtenidas en los diferentes escalones de ambos discos mecanizados con la herramienta tipo A y tipo B. En general ambos discos presentaron muy pocos defectos o alteraciones superficiales, lo cual indica que las condiciones de corte seleccionadas en este estudio (incluso para tiempos prolongados). Las alteraciones más relevantes fueron la presencia de capas distorsionadas (granos muy deformados) o la presencia de una alta densidad de dislocaciones indicadora de endurecimiento por acritud. De todos modos estas alteraciones fueron muy localizadas y superficiales; es decir, no se observaron a lo loargo de toda la superficie mecanizada y no sobrepasaron profundidades de 10 µm (muy por debajo ed los valores aceptados en la industria aeronáutica). La figura 8 muestra ejemplos de capas distorsionadas observadas en las superficies mecanizadas con la herramietna tipo A y tipo B.

3.4. Microdurezas
El perfil de microdurezas únicamente se midió en la superficie de la última pasada (superficie coincidente con la zona calibrada de las probetas de fatiga). La figura 9 muestra los perfiles de microdurezas (valores normalizados respecto a la microdureza del núcleo del material HVsup/HVnuc). Tal y como se puede observar en la figura las dos herramietnas generaron superficies ligeramente más duras que el núcleo lo cual es coherente con las observaciones de alteraciones microestructurales. Por otro lado, se puede observar que las dos herrmientas produjeron cambios similares en los valores de microdurezas, por lo que la influencia de la geometría de la herramienta no es tan evidente para las condiciones de corte estudiadas.
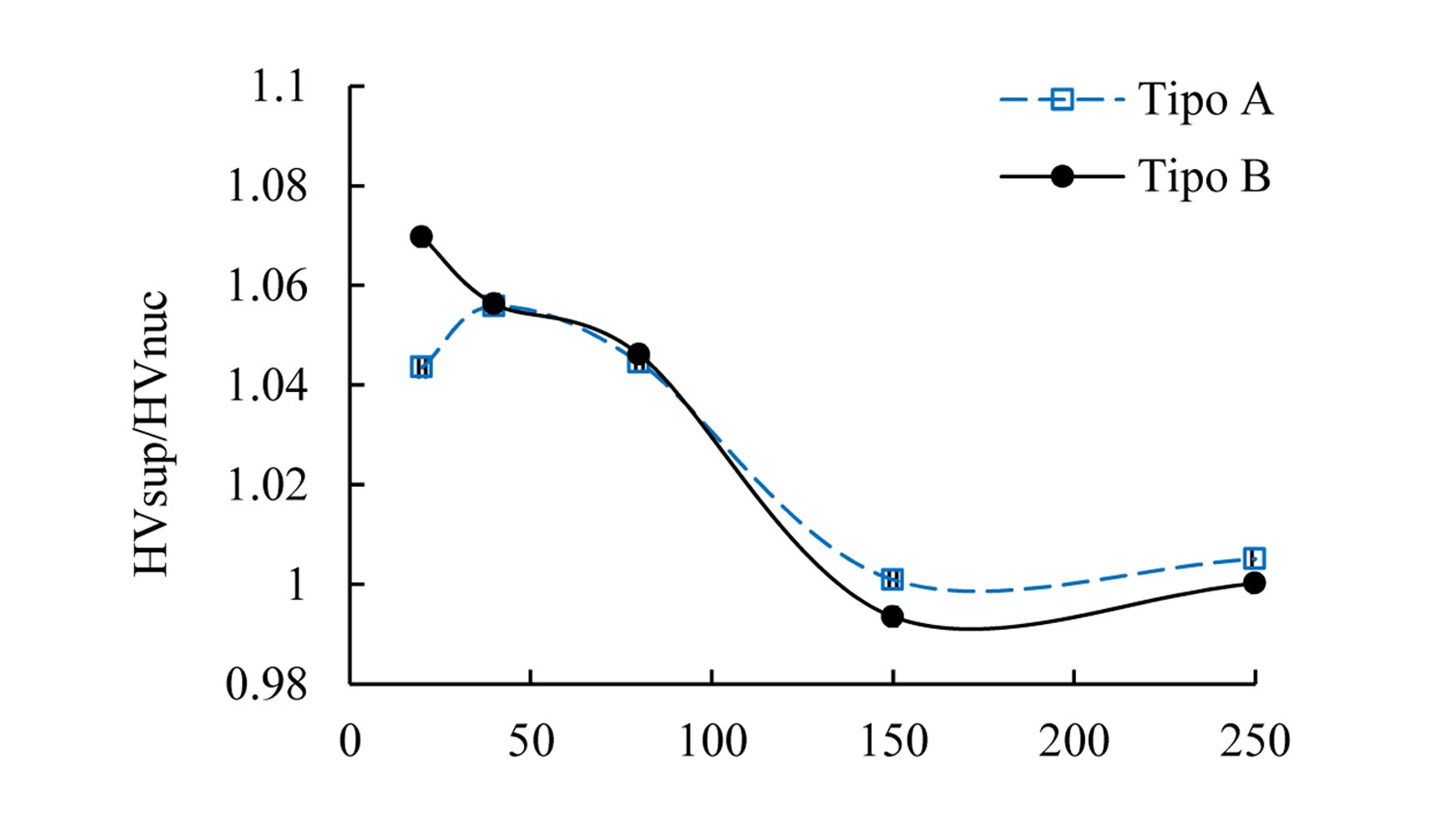
Figura 9. Perfil normalizado de microdurezas (HVsup/HVnuc) en la superficie final de los discos mecanizados con la herramienta tipo A y tipo B.
3.5. Fatiga de bajos ciclos
Los resultados de los ensayos de fatiga isoterma a bajos ciclos se muestran en la figura 10. Los resultados de las vida obtenidas por las probetas (N) se han normalizado respecto a la vida más corta obtenida en todos los ensayos (Nmin). Por otro lado, el eje de ordenadas representa el valor de la tensión máxima (σmax) aplicada normalizada respecto del límite elástico de la aleación Inconel 718 a 450 °C (σy). Las probetas extraídas del disco mecanizado con la herramienta tipo A obtuvieron en general vidas significativamente más largas (entre un 30 a 50% más largas si se comparan los peores resultados de cada lote). Estos resultados están en concordancia con el análisis de integridad superficial. A pesar de que los discos mecanizados con ambas herramientas mostraron daños superficiales muy localizados y perfiles de microdurezas muy similares, la superficie final del disco mecanizado con la herramienta tipo B fue considerablemente más rugosa y con tensiones residuales superficiales más tractivas. Efectivamente, las superficies más rugosas, actuando como microentallas, y la presencia de tensiones residuales tractivas aceleran el inicio de grietas reduciendo la vida a fatiga de la pieza.
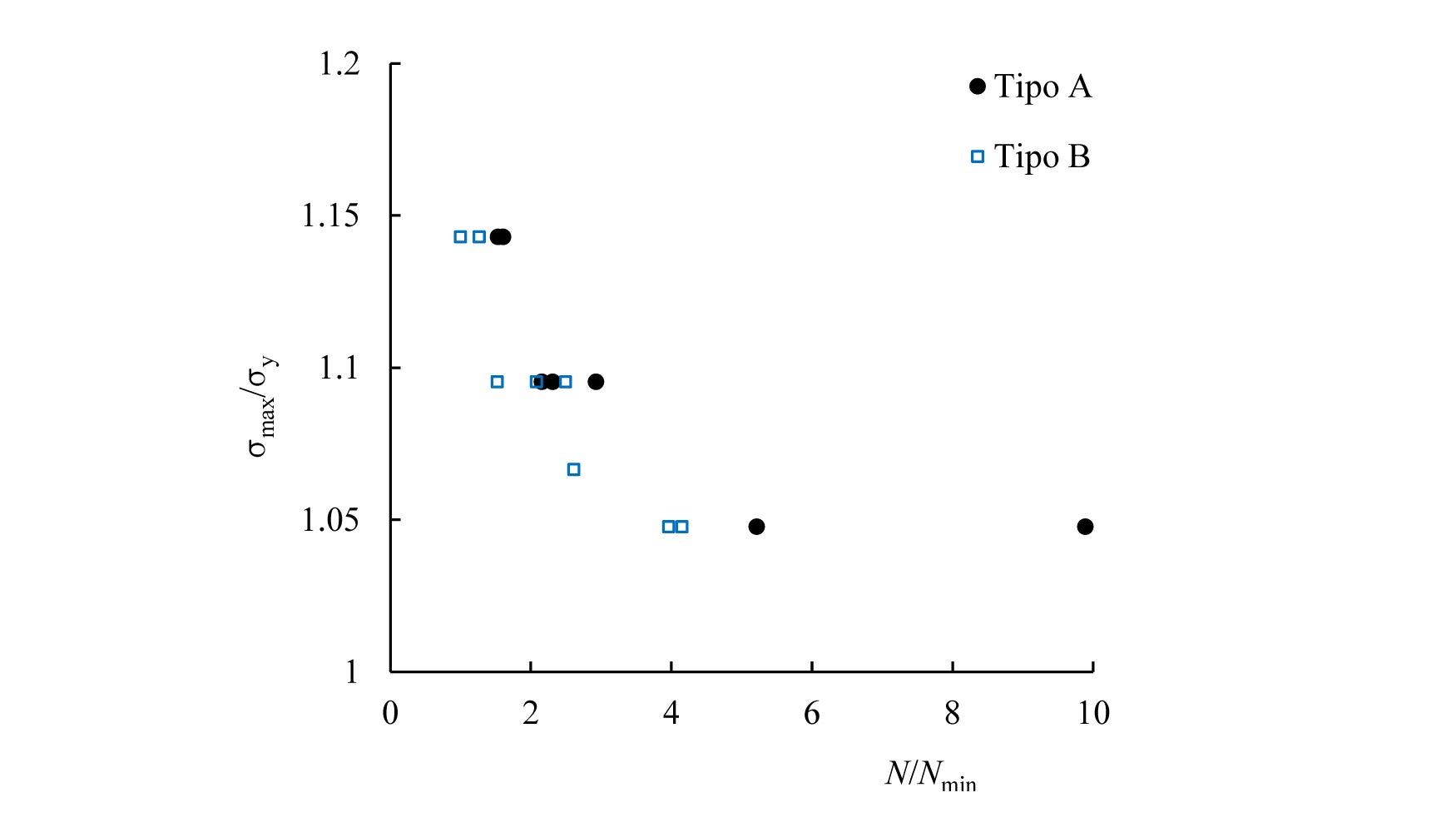
Figura 10. Vida a fatiga normalizada (N/Nmin) en función de la tensión máxima aplicada.
4. Conclusiones
Las principales conclusiones que se extraen del trabajo realizado son las siguientes:
- Se ha definido una metodología de trabajo que permite estudiar la influencia de los condiciones de procesos de mecanizado en la integridad superficial y vida a fatiga de componentes críticos aeronáuticos.
- Los discos mecanizados que tienen una integridad superficial más deficiente (mayor rugosidad y mayores tensiones residuales superficiales tractivas) presentan vidas a fatiga menores.
- Para las condiciones de mecanizado analizadas en este trabajo la geometría de la herramienta tiene una mayor influencia sobre la rugosidad superficial y perfil de tensiones residuales que sobre el daño microestructural prácticamente nulo) y perfil de microdurezas.
- Bajo las condiciones de mecanizado empleadas en este trabajo se seleccionan las herramientas tipo A ya que permiten fabricar discos con mejor integridad superficial y vida a fatiga. Por otro lado, se recomienda analizar unas condiciones de trabajo menos severas para las herramientas tipo B con el fin de asegurar una adecuada integridad superficial y vida a fatiga del componente mecanizado.
Agradecimientos
Los autores quieren agradecer al Gobierno Vasco por la financiación de los proyectos Estrateus (IE14-396), Micromaquinte (PC2014-01) y Crincoplus (UE2013-08), y al Gobierno de España por financiar el proyecto Desafío II (RTC-2014-1861-4), los cuales han servido para llevar a cabo el trabajo presentado.
Referencias
[1] Winstone, M. R., Brooks, J.W. ‘Advanced high temperature materials: Aeroengine fatigue’. Cienc Tecnol Mater 20.1 (2008): 15-24.
[2] Ezugwu, E. O. ‘High speed machining of aero-engine alloys’. Journal of the Brazilian society of mechanical sciences and engineering 26.1 (2004): 1-11.
[3] Posavljak, S, Maksimović, K. ‘Initial fatigue life estimation in aero engine discs’. Scientific Technical Review, ISSN 206 (1820): 2011.
[4] Teti, R., Jemielniak, K., O’Donnell, G., Dornfeld, D. ‘Advanced monitoring of machining operations’. CIRP Annals-Manufacturing Technology 59.2 (2010): 717-739.
[5] M'Saoubi, R., Outeiro, J. C., Chandrasekaran, H., Dillon Jr, O. W. ‘A review of surface integrity in machining and its impact on functional performance and life of machined products’. International Journal of Sustainable Manufacturing 1.1 (2008): 203-236.
[6] Ulutan, Durul, and Tugrul Ozel. ‘Machining induced surface integrity in titanium and nickel alloys: A review’. International Journal of Machine Tools and Manufacture 51.3 (2011): 250-280.
[7] Herbert, C., Axinte, D. A., Hardy, M., Withers, P. ‘Influence of surface anomalies following hole making operations on the fatigue performance for a Nickel-based superalloy’. Journal of Manufacturing Science and Engineering 136.5 (2014): 051016.
[8] Grant, P. V., J. D. Lord, P. S. Whitehead. The measurement of residual stresses by the incremental hole drilling technique. National Physical Laboratory, 2002.
[9] Grant, P., Lord, J., Whitehead, P., Fry, A.T. ‘The application of fine increment hole drilling for measuring machining-induced residual stresses’. Applied Mechanics and Materials 3 (2005): 105-110.
[10] Schajer, G. S. ‘Measurement of non-uniform residual stresses using the hole-drilling method. part II—practical application of the integral method’. Journal of Engineering Materials and Technology 110.4 (1988): 344-349.
[11] Sharman, A. R. C., J. I. Hughes, K. Ridgway. ‘An analysis of the residual stresses generated in Inconel 718 when turning’. Journal of Materials Processing Technology 173.3 (2006): 359-367.
[12] Sharman, A. R. C., J. I. Hughes, K. Ridgway. ‘The effect of tool nose radius on surface integrity and residual stresses when turning Inconel 718’. Journal of Materials Processing Technology 216 (2015): 123-132.
[13] Berruti, T., Lavella, M., Gola M.M. ‘Residual stresses on Inconel 718 turbine shaft samples after turning’. Machining Science and Technology, 13-4 (2009): 543-560.