Entrevista a Carlos Atienza, director de Innovación en Tecnología Sanitaria del IBV
Los institutos tecnológicos valencianos Aimme e IBV acaban de concluir su primer año de colaboración en el marco del proyecto Gencor, cuyo objetivo es desarrollar técnicas productivas, materiales y diseños innovadores para restituciones de estructuras corporales en sectores como la Cirugía Ortopédica o Traumatológica, entre otros. A lo largo del desarrollo del proyecto Gencor, que se prevé dure unos dos años, se fabricarán y caracterizarán prototipos físicos plenamente funcionales, lo que garantizará que las estructuras corporales personalizadas desarrolladas cumplan con los exigentes requerimientos de calidad, seguridad, funcionalidad y biocompatibilidad necesarios para su lanzamiento al mercado. El proyecto llevado a cabo por los dos centros supone la investigación en paralelo en diferentes ámbitos de conocimiento, acordes con la especialidad de cada uno. Así, mientras Aimme trabaja en relación con tecnologías de fabricación, el IBV investigará en relación con diseño y desarrollo de estructuras corporales personalizadas. Precisamente Carlos Atienza, director de Innovación en Tecnología Sanitaria del IBV, nos dá más detalles acerca del proyecto.
El proyecto Gencor se basa en tecnologías, materiales y soluciones de diseño que permitan desarrollar estructuras corporales personalizadas. ¿En qué fase se encuentra ahora el proyecto?
En este momento ya hemos acabado la primera anualidad del proyecto, en la misma se han realizado las siguientes tareas:
- Análisis de los productos existentes en el mercado en el sector traumatológico y maxilofacial.
- Definición de pliego de condiciones de los nuevos productos a desarrollar.
- Análisis de tecnologías y materiales de fabricación rápida para adaptarlos a las necesidades del sector sanitario.
- Definición de cuatro demostradores con la nueva metodología de trabajo.
Las tareas para la segunda y última anualidad serán las siguientes.
- Definición en detalle de los demostradores.
- Fabricación de los demostradores.
- Ensayos y validación de los demostradores.
- Difusión y explotación de los resultados
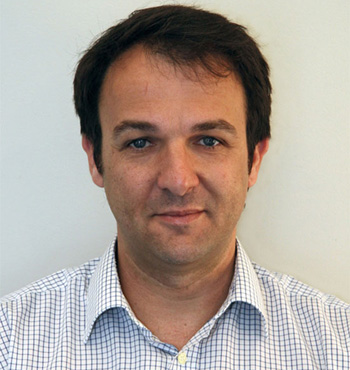
Las restituciones corporales deben cumplir con una serie de requerimientos biocompatibilidad y funcionalidad muy estrictos. ¿Con qué materiales se logra mejores resultados?
Los materiales biocompatibles con los que se va a trabajar son cemento óseo y una combinación de titanio macizo y titanio poroso. Las principales ventajas del cemento óseo son que posee un módulo elástico parecido al hueso, y su bajo coste de fabricación; el principal inconveniente es que no soporta cargas elevadas.
Con la combinación de titanio macizo y titanio poroso, las piezas se fabricarán con una zona central de titanio macizo que aporta rigidez al implante y una zona exterior de titanio poroso para facilitar la osteointegración.
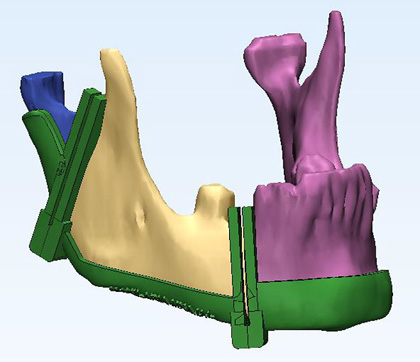
Por otra parte, la tecnología de fabricación aditiva parece ser la más adecuada para este tipo de desarrollos. ¿Qué avances aporta este proyecto? ¿Sería factible un reto de esta envergadura sin impresión 3D?
En este proyecto se está trabajando en el ajuste y mejora de las tecnologías y materiales existentes ya en el mercado para que cumplan con las necesidades de un sector tan exigente como el sanitario.
La impresión 3D es fundamental en el desarrollo de este campo porque permite la fabricación de piezas personalizadas con cualquier geometría y unos costes asumibles. Con las tecnologías convencionales muchas no se podrían fabricar y otras resultarían extremadamente caro fabricarlas teniendo en cuenta las pocas unidades a fabricar de cada pieza, en la mayoría de los casos sólo una.
Para hacernos una idea de qué supone un desarrollo personalizado... ¿podría explicanos cuál sería el proceso?
Los pasos de fabricación de las piezas comienzan con la obtención de las imágenes de la zona que se quiere intervenir: las imágenes se suelen obtener mediante tomografía computerizada (TAC). A continuación se realiza la construcción de un modelo tridimensional en ordenador del defecto óseo a corregir, utilizando el programa Mimics de Materialise. Le sigue la construcción un modelo físico por prototipado rápido del modelo. El cirujano decide la geometría de la pieza de sustitución tras lo cual se diseña la pieza personalizada siguiendo las indicaciones del cirujano, a partir de programas de modelado orgánico tridimensional como el 3-D Matic de Materialise. Posteriormente se procede a la fabricación mediante prototipado rápido. Finalmente, hay que limpiar la pieza, empaquetarla y esterilizarla.
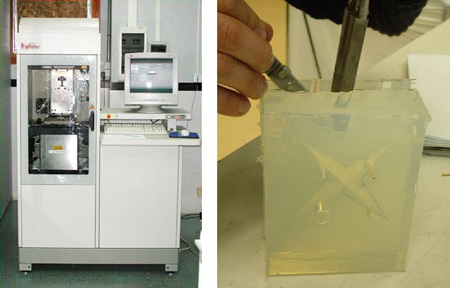
Para Carlos Atienza, “la impresión 3D es fundamental en el desarrollo de este campo porque permite la fabricación de piezas personalizadas con cualquier geometría y con unos costes asumibles”.
En los últimos tiempos se está hablando ya de conferir a los productos realizados mediante Rapid Manufaturing propiedades como textura, rugosidad, entre otras. ¿Qué requisitos demandan las reconstrucciones médicas?
Principalmente la biocompatibilidad. También es necesaria una rigidez suficiente para no romperse frente a las cargas presentes en el cuerpo humano. Por otra parte, y por aspectos estéticos y funcionales se debe reproducir la geometría ósea previa al defecto.
Asimismo, la reconstrucción debe facilitar la osteoinducción y la osteoconducción, debe ser esterilizable y debe cumplir la normativa aplicable a implantes quirúrgicos.
En este sentido, ¿cuáles son los principales escollos con que se encuentran?
Hasta hace poco tiempo la tecnología de fabricación rápida no estaba lo suficiente desarrollada como para ofrecer productos de la calidad requerida.
El principal escollo de los productos personalizados es el coste del diseño y fabricación de los mismos.
En la actualidad los tiempos de diseño se han reducido gracias al desarrollo y mejora de programas de modelado tridimensional muy potentes como el 3-D Matic y el Mimics.
Las tecnologías de fabricación rápida también se han mejorado notablemente en los últimos años obteniéndose una mejor calidad final de los productos y un abaratamiento en su coste de fabricación.
Para finalizar, el proyecto Gencor plantea también la apertura de nueva líneas de producto en empresas ya existentes. ¿De qué productos estaríamos hablando? ¿Y qué nivel de implantación tecnológica deben cumplir las empresas para optar a ello?
Las empresas podrán ofrecer un servicio de diseño y fabricación personalizada de implantes. Nos referimos a productos fabricados a medida de cada paciente y cada patología, por ejemplo plastias craneales, prótesis e instrumental quirúrgico, elementos de osteosíntesis, etc.
Este proyecto está orientado a empresas ya fabricantes de implantes quirúrgicos en el sector maxilofacial, traumatología o veterinaria. Para llevar a cabo el servicio las empresas deben poseer o subcontratar los siguientes recursos tecnológicos:
- Programas de modelado tridimensional (Mimics o 3-D Matic de Materialise).
- Expertos en diseño tridimensional de formas orgánicas.
- Tecnologías de fabricación rápida y materiales requeridos para cada caso.
También es necesario contar con el apoyo del cirujano que va a realizar la operación ya que es el que toma la decisión final sobre las características del implante y para conseguir los las imágenes TAC del paciente.