Control preciso del proceso de cocción
Poner la masa en agua caliente, dejarla hervir, escurrir y listo. Como en casa, lo mismo hace la instalación de cocción de spaetzle de Staedler, pero en dimensiones industriales y con un control preciso gracias a los sensores de Ifm para garantizar una constante y elevada calidad del producto
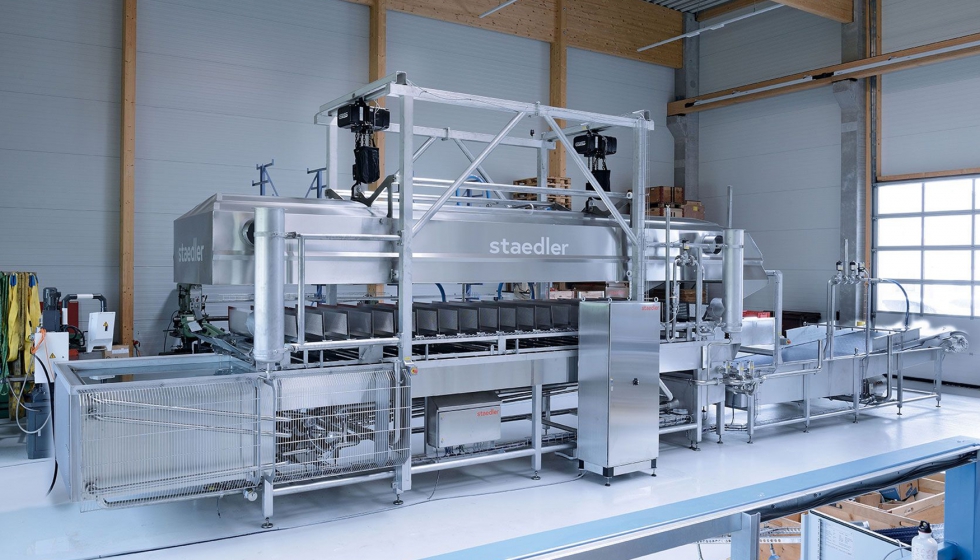
La empresa Staedler Automation AG, con sede en Henau (Suiza), lleva más de 10 años fabricando sistemas de automatización de proceso. Entre otros productos, Staedler Automation fabrica sistemas de cocción totalmente automáticos para la industria alimentaria. El sistema que se muestra aquí se destinará a un fabricante de spaetzle, una pasta típica alemana.
Lukas Staedler, director general de Staedler Automation AG, explica cómo funciona: “Imagínese una olla que está en funcionamiento constantemente. Es decir, la masa cruda se introduce en la parte inicial del sistema, pasa por el mismo en un tiempo determinado, de modo que al final sale el producto cocinado al punto. Durante este tiempo de cocción definido, se consigue una calidad constante del producto”.
Los alimentos a cocinar se transportan mediante palas en el baño de agua caliente. Ya que el proceso de cocción no requiere prácticamente de ningún contacto mecánico entre la máquina y el producto, se minimizan los daños en el producto. Al final, los alimentos cocinados se transfieren rápidamente a la zona de enfriamiento.
“En principio, estos sistemas pueden cocinar cualquier cosa que flote”, subraya Lukas Staedler. “En este sistema en concreto, pasta fresca como ravioli, tortellini o spaetzle. Pero también podría ser embutido o verduras. En total, esta planta alcanza una producción de 2,5 toneladas por hora.
Mantenimiento de temperaturas exactas
Mientras que en casa las burbujas de agua hirviendo en la olla podrían servir para indicar la temperatura aproximada, la temperatura en un proceso de cocción industrial debe mantenerse con máxima precisión. Solo así se consigue una calidad constante del producto tal y como exige el cliente.
Así, en este sistema, la medición de la temperatura proporciona los valores del proceso más importantes en dos puntos, lo que también se denomina Punto Crítico de Control o, abreviado, PCC. La primera es la temperatura del agua casi en ebullición, que en este caso debe controlarse exactamente a 95 °C, y la segunda es la temperatura en el baño de enfriamiento para detener inmediatamente el proceso de ebullición. Dos sensores de temperatura garantizan temperaturas exactas regulando el intercambiador de calor.
Staedler apuesta por los sensores de temperatura de Ifm del tipo TA2502 en estos Puntos Críticos de Control, que cuentan con un elemento de medición Pt1000 de alta precisión y rápida respuesta para un amplio rango de temperaturas de -50 a 200 °C. Además, estos sensores se caracterizan por su elevada repetibilidad y estabilidad duradera, un requisito esencial para una calidad óptima y constante del producto.
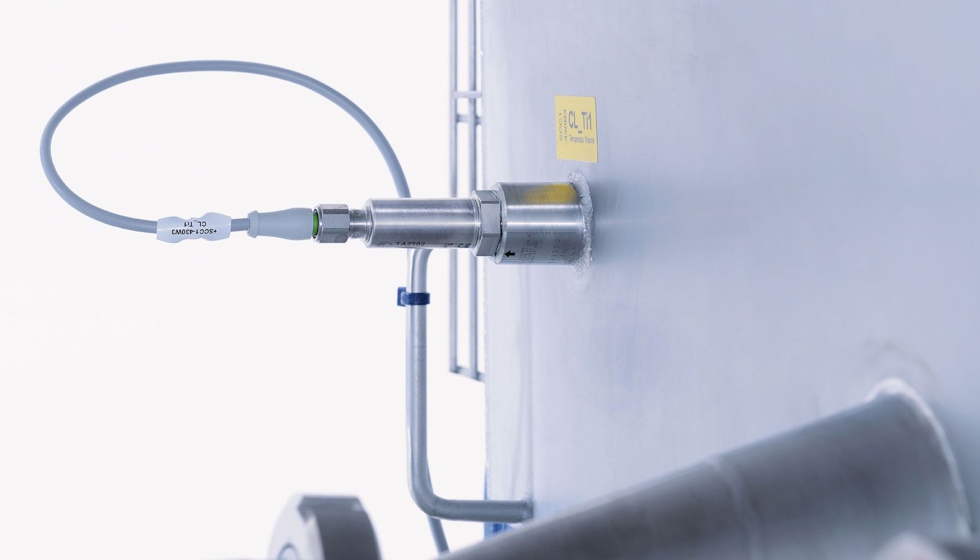
En el futuro, Staedler tiene previsto utilizar en estos puntos sensores de temperatura autocontrolados de Ifm del tipo TCC. La particularidad de este equipo es que dispone de dos elementos de medición de tecnologías distintas. Esto significa que las variaciones de precisión se detectan inmediatamente y se indican mediante una señal de conmutación de alarma y a través de un LED en el equipo, claramente visible a distancia. Esto simplifica enormemente el asegurarse la calidad del producto, ya que la fiabilidad de la temperatura está garantizada en todo momento entre los intervalos de calibración siempre que el sensor no detecte ninguna deriva y emita una señal de advertencia. En cambio, con los sensores convencionales puede producirse una desviación o deriva de la temperatura al día siguiente de la calibración, la cual no se detectaría hasta la siguiente calibración. En el peor de los casos, esto obligaría a retirar grandes lotes de producto, con la consecuente pérdida de reputación del fabricante.
Control de la limpieza CIP mediante el valor de conductividad
Tras cada producción, el sistema se limpia mediante un proceso CIP. Para ello, una bomba independiente enjuaga los conductos con productos de limpieza alcalinos y ácidos. A continuación, se aclara con agua limpia antes de reanudar la producción. El sensor de conductividad LDL200 de Ifm desempeña un papel decisivo en este proceso: midiendo de forma precisa la conductividad puede determinar inequívocamente si existe producto de limpieza en la tubería y en qué concentración. En función del valor medido, el controlador sabe, por ejemplo, si es necesario añadir producto de limpieza o si se ha completado el proceso previo de enjuague, el enjuague intermedio o el final. Al final del proceso de limpieza, la tubería se enjuaga con agua limpia. Hasta que no se haya alcanzado el valor exacto de conductividad del agua de lavado no se desbloquea el sistema para reiniciar la producción. Así, se garantiza una perfecta separación de fases en el proceso CIP.
Además de la conductividad, el LDL200 mide la temperatura del fluido y la transmite al controlador a través del protocolo de comunicación IO-Link. De esta manera también se controla el intercambiador de calor, de modo que siempre tenga suficiente energía para mantener la temperatura de ebullición del agua.
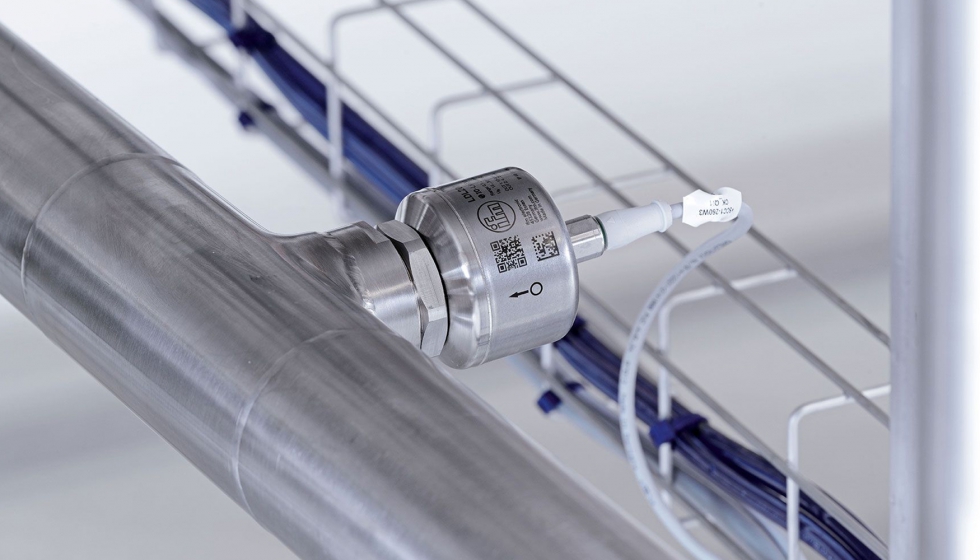
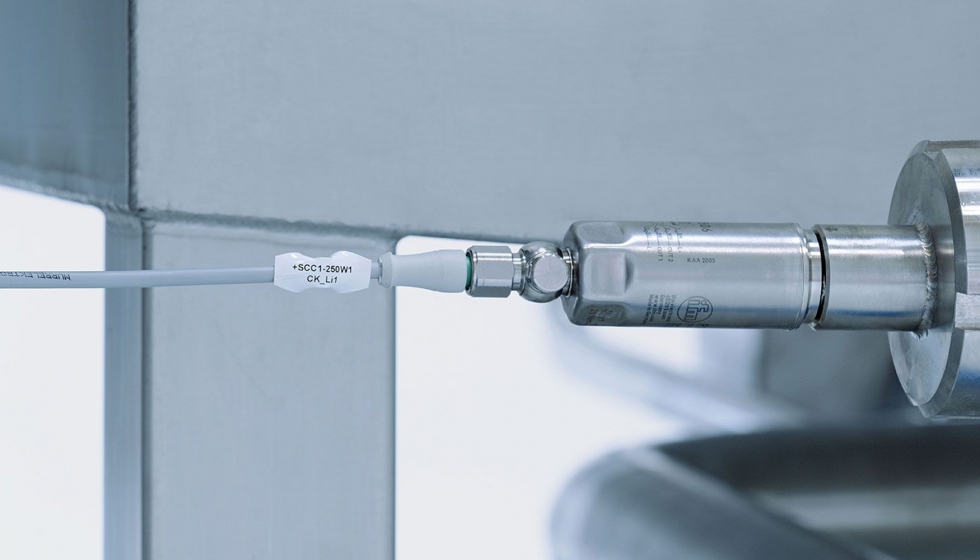
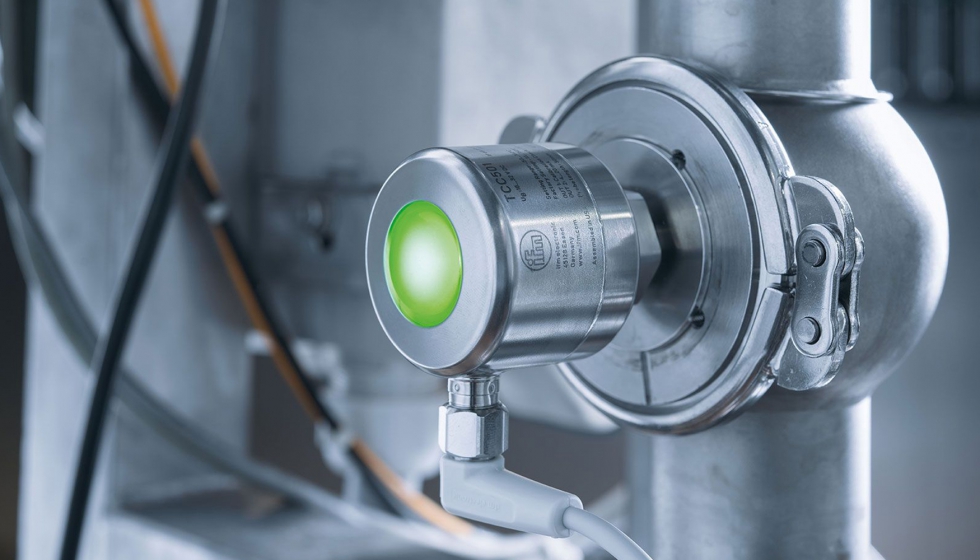
Supervisión de posición con detectores inductivos
Además, el sistema cuenta con detectores inductivos para supervisar la posición. Aunque estos no participen directamente en el proceso de cocción, cumplen una importante función de control. La cinta de refrigeración, sobre la que se deposita el producto que entra y sale del baño de enfriamiento, puede levantarse del baño utilizando un polipasto para su limpieza manual. Dos detectores inductivos registran sin contacto la posición final superior o inferior y también garantiza que el sistema solo pueda ponerse en marcha cuando la cinta está en la posición inferior correcta.
Un tercer detector inductivo está montado en el filtro ranurado, que también puede extraerse para su limpieza manual. El detector comprueba que el filtro se ha insertado correctamente antes de iniciar la producción.
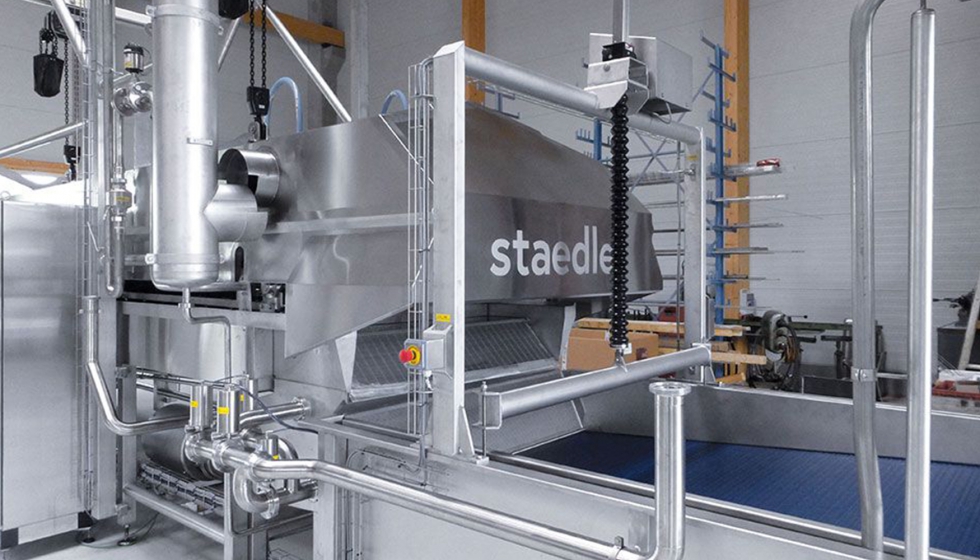
Comunicación de sensores con IO-Link
Todos los sensores se conectan al controlador a través de IO-Link. Este protocolo de comunicación transmite al controlador los valores de medición de forma digital. Así, se evitan con eficacia los errores de medición debidos a las pérdidas de conversión. Pero con IO-Link se puede hacer aún mucho más.
Lukas Staedler comenta lo siguiente: “Todo sensor de un PCC debe revisarse anual o semestralmente. Para calibrarlos, los sensores de temperatura se colocan en un líquido de referencia a una temperatura definida. Realizamos la calibración de los sensores de temperatura través de IO-Link.
Con el sensor de conductividad LDL, se transmiten ambos valores del proceso, temperatura y conductividad, en una sola línea. El caudalímetro SM transmite al controlador tanto el valor del contador como también la cantidad de caudal actual a través de una salida mediante IO-Link”.
En cuanto a la automatización con IO-Link, Lukas Staedler tiene una opinión clara: “En principio, la automatización puede parecer más compleja, pero IO-Link también ofrece un claro valor añadido. Por un lado, puede transmitir varios valores de medición de un sensor en un solo cable, lo que reduce el coste de montaje. Por otro lado, los sensores de temperatura se calibran directamente y no a través de valores de corrección en el controlador, como sucedía anteriormente. Esto simplifica el programa de control. Es decir que, en general, las ventajas de IO-Link son muy amplias.
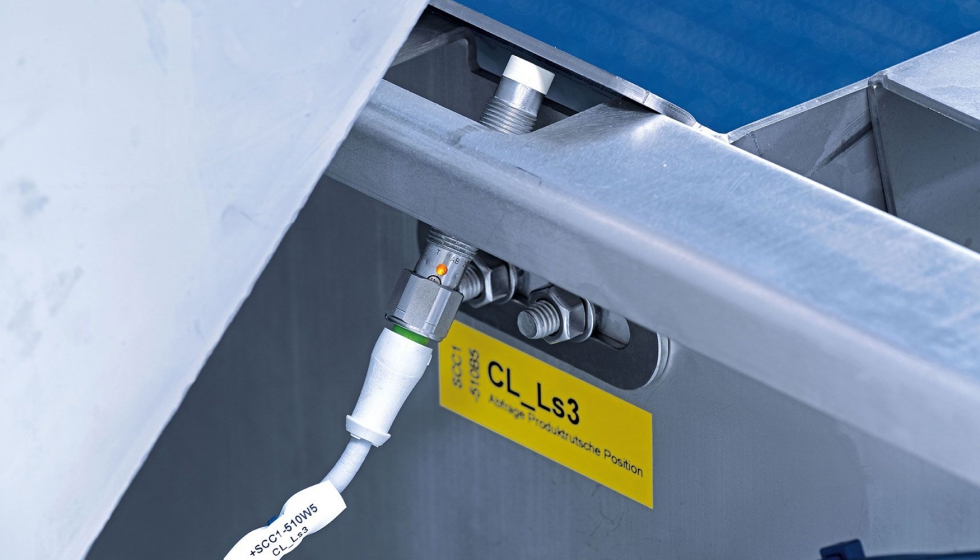
Las soluciones de automatización de Ifm convencen a Staedler
En palabras de Lukas Staedler: “Estamos muy satisfechos con Ifm. Ya habíamos recurrido a Ifm varias veces en proyectos anteriores. Esto se debe a que Ifm ofrece una solución integral, es decir, desde el detector inductivo hasta el caudalímetro electromagnético, pasando por medición de temperatura, sensores de presión y medición de conductividad. En resumen: los sensores de Ifm cubren todas nuestras necesidades aquí en la planta. Otro motivo de nuestra decisión es la buena relación calidad / precio. Los sensores tienen grandes ventajas para plantas de este tipo y, al mismo tiempo, son asequibles. No cabe duda de que también confiaremos en Ifm para futuros proyectos”.