El moldeo por inyección de tapones, vasos o cubos...
Ferromatik Milacron16/06/2007
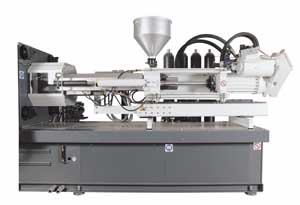
Actualmente, las aplicaciones de envase son a menudo moldes multicavidades, como, por ejemplo, tapones de cierre con 96 cavidades e incluso más. Para lograrlo, los platos de sujeción han de tener las dimensiones adecuadas, unas guías perfectamente paralelas y una buena rigidez para asegurar, de esta forma, la distribución regular de la fuerza. Hay que tener presente que las dimensiones de los platos de sujeción no reflejan necesariamente la fuerza de cierre requerida.
A la necesidad de una buena dinámica de la máquina que permita conseguir una elevada velocidad y tiempos de ciclo más cortos se une el importante factor del seguro de moldes, que garantiza una larga vida útil de la máquina y pocos paros por mantenimiento.
Por regla general las máquinas para envases funcionan las 24 horas del día con tiempos de ciclo lo más cortos posible, siendo la expulsión de los tapones de cierre un factor tiempo importante.
A veces se necesita en esta fase un intervalo adicional a fin de comprobar que todas las piezas han sido desmoldeadas y retiradas de la zona del molde.
Para evitar este tiempo muerto adicional se requiere un seguro de molde eficiente y preciso, que permita reconocer con certeza las piezas que hayan podido quedar enganchadas.
Molde de pisos
En las piezas más grandes, como, por ejemplo, envases, el número de cavidades es menor, pero en cambio se requiere un alto rendimiento de la unidad de cierre y, además, unos grupos de inyección de elevada potencia, ya que debido a la reducida ratio entre el grosor de la pared y las condiciones de flujo se necesitan elevadas presiones de inyección y también un alto rendimiento de plastificación para disponer rápidamente de la cantidad de masa necesaria, dado que por la delgadez de la pared los tiempos de enfriamiento son bastante cortos.
En aplicaciones todavía mayores, como en el caso de los cubos, los principales retos son los reducidos tiempos de apertura y cierre del molde, las altas velocidades de inyección, las elevadas presiones y la gran potencia de plastificación.
Todas estas exigencias juntas determinan las especificaciones requeridas por la máquina, por lo cual repasaremos a continuación las diferentes versiones de equipamiento que ofrecemos.
Unidad de cierre
En aplicaciones de envases se utiliza preferentemente un sistema de fuerza de cierre central, ya que garantizan una distribución de la fuerza de cierre más equilibrada y un cierre y bloqueo regulares que aseguran, por tanto, un menor desgaste y una vida útil del molde más larga. Además, este sistema ofrece una máxima protección del molde. El cilindro de cierre, de actuación directa, permite la monitorización de un posible aumento de presión debido a piezas moldeadas no expulsadas, ya que la mayor presión se produce al iniciarse el movimiento de cierre, cuando se trata de acelerar grandes masas, mientras que hacia el final del proceso de cierre disminuyen la velocidad y, por tanto, la fuerza requerida. En este sentido la rodillera presenta un inconveniente, puesto que al final del movimiento aumenta la fuerza de cierre, lo que dificulta reconocer posibles piezas encalladas y reaccionar ante su presencia.
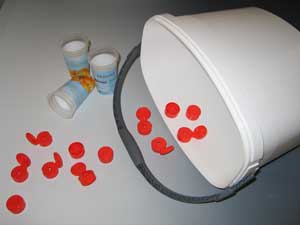
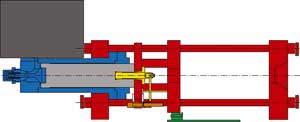
Unidad de inyección
El accionamiento eléctrico del husillo de plastificación utilizado habitualmente permite realizar funciones en paralelo y, lo que es todavía más importante, conseguir una buena calidad de la masa. Preferentemente se utilizan grupos de inyección mayores, dado que para una dosificación lo más exacta posible se necesita una carrera de inyección no superior a 1,5D. Existen muchos motivos para ello. En una carrera de inyección de más de 1,5D se reduce la longitud del husillo disponible, lo que disminuye la calidad de la masa. Con un husillo de largo insuficiente puede ocurrir, sobre todo en cargas más altas, que el granulado no fundido bloquee la válvula de retención, lo que incidiría negativamente en el peso exacto de cada embolada. Definitivamente, el rendimiento será tanto mayor cuanto mayor sea también la longitud disponible del husillo.
Últimas tendencias en los nuevos diseños de las máquinas de inyección
Bien mirado, las máquinas de inyección para envases ya son actualmente máquinas altamente especializadas, con una clara tendencia a convertirse en máquinas para una sola función.