El sistema UMR aporta mejoras en los envases para lácteos
Para la industria especializada en esta industria, Uniloy Milacron (representada en España por Sebastián Allué, S.L.) ofrece, también para el mercado europeo la serie UMR con husillo reciprocante. Aunque no tan extendida en Europa como en EE. UU., la tecnología de moldeo por soplado mediante husillo reciprocante se utiliza en las principales empresas, también en España. En la pasada edición de la feria NPE de Chicago se pudo ver esta tecnología aplicada a la fabricación de envases de tres capas para el citado sector.
La industria del envase de productos frescos para consumo inmediato tiene exigencias especiales y sus propias características: grandísimos volúmenes de producción, necesidad de envases ligeros y económicos, higiene máxima y una tecnología de moldeo por soplado fácil de usar para los envasadores y productores. Es por todo ello que la serie UMR ha sido diseñada expresamente para la industria de la alimentación, con un énfasis especial en los productos lácteos y frescos.
Hay tres puntos que ponen de manifiesto la eficiencia de la máquina:
- La capacidad de producción por hora. La tecnología de moldeo por soplado UMR alcanza todas sus ventajas cuando se requieren altos volúmenes de envases ligeros y económicos de HDPE. Puede alcanzar las 20.000 piezas hora.
- La segunda ventaja es su bajo consumo energético, debido a un diseño pensado en mover lo menos posible piezas mecánicas, lo cual beneficia mucho al ciclo.
- Muy importante también es el poco tiempo necesario para poner en marcha la máquina.
- El fácil manejo de la máquina la convierte en un equipo muy práctico incluso para operarios no expertos en el proceso del moldeo por soplado.
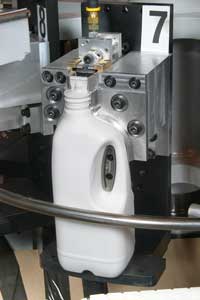
¿Husillo reciprocante o sistema a extrusión continua?
La primera tiene que ver con la mecánica de la máquina. El molde no se traslada con respecto al cabezal de extrusión hacia la estación de calibrado. El ciclo en vacío es generalmente de 1,75 segundos, frente a los 3 segundos del sistema de extrusión continua. La tecnología de husillo reciprocante no requiere corte del parisón, con el lógico ahorro.
La segunda característica técnica a destacar es que la resina se plastifica en una extrusora con husillo reciprocante, que inyecta HDPE por el cabezal intermitente de extrusión durante cada ciclo para crear los parisones. La extrusora puede plastificar 4,6 kg/kW.
El tiempo necesario para crear un parisón es especialmente corto, normalmente de 1,5 segundos, frente a los 8 segundos de un carro sencillo UMS y aproximadamente 4 segundos en doble carro.
Además, el cuello del envase se obtiene mediante soplado (más que mediante calibrado) con un labio interno, normalmente para una tapa de film de aluminio de PE laminado.
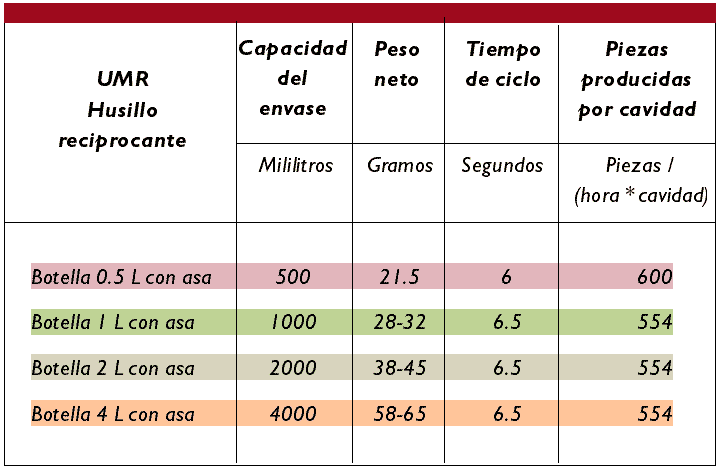