Rompiendo moldes
Con un máximo de 36 estaciones de moldeo por soplado, la innovadora máquina de moldeo por soplado y estirado giratoria Contiform 336 puede alcanzar una producción de 81.000 envases PET por hora. Las preformas de botellas se calientan a una temperatura de 100 a 120 °C en un horno lineal de infrarrojos y luego son guiadas por una rueda dentada hasta el molde de soplado de aluminio. Justo cuando se cierra el molde, una varilla de estirado se inserta en el cuello de la preforma para estirarla axialmente, aplicando hasta 40 bar de presión de soplado. Esto presiona los lados de la preforma contra la pared interior del molde para dar forma a la botella, que posteriormente recoge la rueda dentada de salida.
Este método se utiliza para producir alrededor de 300 billones de botellas al año, y con este número en rápido crecimiento, las plantas embotelladoras exigen un rendimiento cada vez más elevado de las máquinas. Aún así, a medida que aumentan las tarifas energéticas, así como la conciencia medioambiental, todos estos resultados no pueden ir en detrimento de la sostenibilidad.
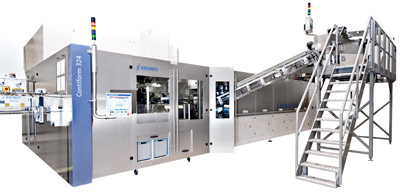
Cada estación gestiona 2250 botellas/hora
Con esta última renovación de la serie Contiform, introducida por primera vez en 1997, el principal desafío era equilibrar las prioridades de máxima producción y mínimo consumo de energía. Krones ha conseguido controlar este desafío con calidad de experto. Han sido capaces de elevar aún más la marca establecida por la generación anterior, aumentando la producción de cada estación de moldeo por soplado de la ya impresionante cifra de 2.000 botellas, a un volumen récord de 2.250 botellas por hora.
Para lograr este salto, el equipo de ingenieros dirigido por Dieter Finger, jefe de desarrollo Eléctrico en la división de Tecnología Plástica de Krones, necesitó introducir algunas importantes innovaciones. “Hasta ahora, las transmisiones por correa eran suficientes para accionar las distintas ruedas”, afirma. “Con la nueva Contiform, sin embargo, estamos tratando con velocidades donde el estirado de la correa inherente a esta solución nos impide alcanzar la precisión necesaria para una transición fluida entre la rueda de soplado y la rueda de transferencia”.
Los ingenieros han solucionado este problema reemplazando las transmisiones por correa por servoaccionamientos directos. La tercera generación de máquinas Contiform ahora utiliza motores de par que proporcionan hasta 2.300 Nm de par motor. “No sólo son mucho más precisos que las transmisiones por correa”, explica Finger, “su sofisticado sistema de gestión de potencia les permite compartir energía en caso de fallo de alimentación o parada de emergencia, lo que significa que pueden llevar la máquina rápidamente a una parada sin perder la sincronización”.
Estos motores se controlan mediante la solución SDC (Servo Drive Control) de Krones basada en la tecnología de B&R, que la compañía ha utilizado en muchas de sus divisiones durante más de cinco años. La solución SDC permite acoplar un número ilimitado de ejes a través de Powerlink en una amplia variedad de topologías. Los variadores proceden de la serie ACOPOSmulti de B&R, con una CPU X20 que actúa como controlador.
Los servoaccionamientos eléctricos sustituyen a los neumáticos
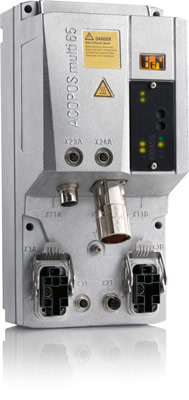
“A diferencia de los motores lineales de canal en U o planos convencionales, este diseño dispone de una varilla de desplazamiento de imán permanente que se mueve dentro de un tubo del estátor, que sostiene las bobinas del servoaccionamiento y un sensor de Hall“explica el experto electrónico de Krones.”El motor lineal tubular elimina las correas y el juego asociado con las soluciones estándar de accionamientos con varilla de estirado. Puesto que la fuerza se traduce directamente en la extensión de la varilla de estirado, también es posible utilizar rodamientos más pequeños, obteniendo como resultado un motor que no necesita engrase ni mantenimiento”.
Este motor realizado a medida fue desarrollado por NTI (LinMot) de acuerdo con las especificaciones de Krones. “Las especificaciones incluían que el motor proporcionara una fuerza máxima de 2 kN y lograra una velocidad máxima de 2 m/s”, añade Finger. “También necesitábamos una precisión de posicionamiento de 0,2 mm y, al mismo tiempo, la capacidad de integrar el motor sin problemas en el resto de nuestra solución de servoaccionamiento”.
Motor lineal tubular con encoder Hall en un servoaccionamiento ACOPOS estándar
A fin de satisfacer estas especificaciones, el motor fue diseñado para funcionar en un servoaccionamiento ACOPOS trifásico estándar de B&R con una tensión del bus de continua de 800 V. El servoaccionamiento ACOPOS de B&R también evalúa y linealiza la señal del sensor Hall. “La programación implicada aquí también es un factor a tener en cuenta”, explica Finger. “Una vez más, B&R ha demostrado su flexibilidad y compromiso modificando el firmware estándar de ACOPOS. Como resultado, ahora disponemos de motores lineales tubulares como estándar de la compañía que combinan movimientos muy homogéneos con un consumo de energía mínimo”.
Para los variadores que controlan los motores lineales, Krones seleccionó ACOPOSremote de B&R con protección IP65, junto con una CPU X20 de B&R que se encarga del control del módulo de expansión. Para proporcionar el control de la válvula y supervisar la presión de soplado, los módulos de E/S IP67 están conectados al segundo interface POWERLINK del controlador. Finger es muy consciente de las claras ventajas que esto conlleva para los fabricantes de maquinaria. “La instalación de este variador directamente en cada estación de estirado nos permite producir por adelantado toda la estación, verificarla y parametrizarla. Además, sólo necesitamos una línea de alimentación para cada estación. Esto no sólo encaja perfectamente con nuestro enfoque modular, también es totalmente compatible con la estrategia de producción en línea de montaje que estamos utilizando, por primera vez, en estas máquinas”.
Proceso de estirado eléctrico: mayor rendimiento, cambio de formato más rápido, procesamiento más flexible
Los operarios de la máquina también se benefician del nuevo proceso de estirado eléctrico, que no sólo aumenta la producción, sino que también les ofrece total libertad para adaptar todo el proceso. Finger ilustra lo que esto significa en la práctica: “En primer lugar, el tipo de botella se puede seleccionar con sólo pulsar un botón, sin tener que perder tiempo cambiando los cabezales manualmente. Para modificar el perfil de movimiento del accionamiento de estirado, también basta con pulsar un botón. Como resultado, al cambiar de una botella de pequeño volumen a una botella de gran volumen, ya no es necesario modificar la curva”.
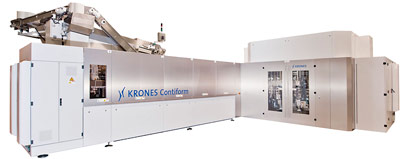
Pero esto es sólo el principio. La curva puede incluso configurarse libremente para dividir el proceso de estirado en fases con distintas velocidades. El operario puede aprovechar esta nueva flexibilidad de control para producir una botella de la misma calidad con una preforma de material más asequible, o para crear botellas de diseño más complejo, que antes eran imposibles de crear con la calidad necesaria.
ACOPOS de B&R: alimentación del bus de continua hasta en 70 metros
Con la misma importancia, cabe destacar que esta nueva generación consume mucha menos energía. Esto se consigue, en parte, eliminando la transmisión neumática de las estaciones de estirado. Otra contribución proviene de la capacidad de la solución de B&R para ampliar el alcance de la alimentación del bus de continua hasta los 70 metros. Krones ha aprovechado esta función para acoplar las alimentaciones del bus de continua de los módulos de estirado de la máquina con los módulos de servoaccionamiento. En caso de fallo de alimentación, la energía puede ser desviada de la rueda de soplado para llevar el sistema a una parada controlada y mover las varillas de estirado a una posición segura. “Si nuestro sistema de servoaccionamiento no fuera de un único proveedor, tendríamos que trabajar con distintas tensiones del bus de continua. Para ello serían necesarios convertidores DC/DC, que en el pasado ya nos habían dado problemas”, recuerda Finger.
La energía se devuelve al bus de continua incluso durante el funcionamiento normal. La energía generada por el frenado de las varillas de estirado (el aire comprimido en las botellas las devuelve a su posición inicial a hasta 650 N) puede utilizarse en otras estaciones, permitiendo que cada estación utilice un promedio de sólo 250 vatios.
Otras medidas implementadas por Krones para poder optimizar aún más el consumo incluyen la innovadora etapa de soplado intermedio y un perfeccionado sistema de reciclaje de aire comprimido interno, así como una importante reducción en el volumen de espacio muerto. En conjunto, la cantidad de aire comprimido requerido por la máquina se reduce en un tercio.
Las ventajas de la nueva serie de máquinas de moldeo por soplado de Krones son claramente evidentes. Por todo ello, no es de extrañar que la nueva generación de máquinas Contiform haya percibido una fuerte demanda incluso antes de su lanzamiento oficial, y tampoco que tuviera un exitoso impacto en el Día del Cliente de Krones 2011.
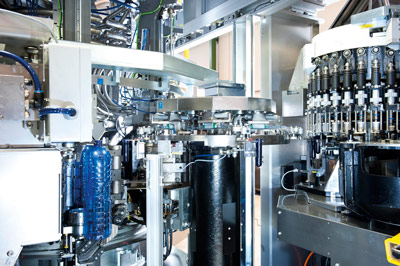