Insertos para moldes fabricados con tecnologías de ‘additive manufacturing’
Actualmente la fabricación de utillajes sigue siendo lenta y costosa, causando problemas a las empresas a la hora de generar series cortas de producción que son cada vez más demandadas por los clientes. También resultan poco productivos para realizar prototipos hechos para simulación de materiales, y finalmente requieren de un proceso largo de diseño, lo que aumenta el tiempo de lanzamiento al mercado.
Hoy en día se pueden fabricar insertos metálicos mediante tecnologías de Fabricación Aditiva (‘additive manufacturing’, AM). Estos insertos suelen requerir, en algunos casos, operaciones posteriores de posprocesado, para alcanzar un nivel de precisión y acabado superficial óptimos.
Sin embargo, diferentes fabricantes de tecnologías de AM generan insertos para moldes que permiten reducir los tiempos, los costes de producción, así como la variación de diseño de la pieza. Las tecnologías AM requieren de algunas condiciones a la hora de optar para un inserto de inyección de plástico. En primer lugar debemos pensar en el número de piezas finales que queremos fabricar, en segundo lugar debemos rediseñar la pieza para que se aprovechen las ventajas de diseño que permite el AM, como paredes finas, bisagras, inserto de logos, etc., logrando una calidad de pieza final muy alta tanto en precisión dimensional como en el aspecto superficial y acabado.
Otra de las facetas que hay destacar es la duración del inserto y otras consideraciones que detallamos a continuación. Serán factores claves en la vida útil del molde, la elección del material y su temperatura de trabajo, así como el tiempo de ciclo de inyección y su proceso de refrigeración. Por esta razón, cabe destacar la importancia de disponer de buenas guías de diseño para insertos y aplicar geometrías que no sometan el molde a presiones y temperaturas demasiado elevadas que pueden causar fallos dentro del molde o bien provocar que el inserto tenga una vida útil limitada.
Existen algunas tecnologías AM que posibilita insertar canales de refrigeración en el contorno del molde, disminuyendo el ciclo de inyección de las piezas plásticas, para mejorar la productividad. Este es el caso de la tecnología Laser Cusing que permite fabricar canales de refrigeración en el contorno del molde y en las partes que necesitan refrigeración específica, optimizando de esta manera el ciclo de inyección.
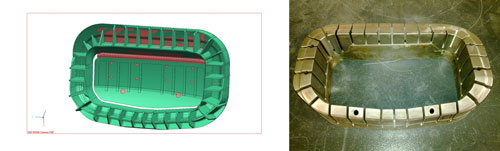
Caso práctico realizado por Fundación AITIIP con la tecnología Laser Cusing
Objetivo
En este caso el objetivo era dar solución al siguiente problema: en la fabricación de la pieza plástica de abajo se observaban deformaciones en la fase de expulsión, lo que provocaba rechazos en la producción. Tras análisis se definió la causa como una acumulación de material por diseño de pieza y espesores no uniformes.
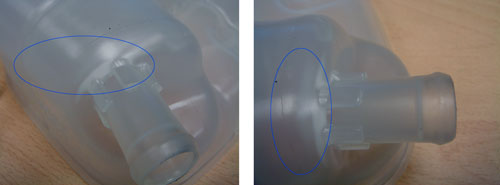
El molde con el que se fabricaba esta pieza tenía una refrigeración insuficiente en la zona que se muestra en la imagen. Esta refrigeración era escasa debido a la compleja forma geométrica de la pieza en esa zona. Como consecuencia se incorporó un inserto de Cu-Be, que mejoró la extracción de calor durante el enfriamiento; era de dimensiones considerables con lo cual su coste era importante. En estas condiciones, la pieza necesita más tiempo para alcanzar una temperatura lo suficientemente baja como para la extracción, aumentando el ciclo de fabricación, y presentando incluso ‘marcas blancas’ que evidencian la deformación irrecuperable en la pieza y casi la rotura. Se decidió implementar el uso de una tecnología avanzada de fabricación de moldes de inyección, que permitiera una mejor refrigeración en esta zona de detalle complejo, difícil accesibilidad y escaso espacio físico para ubicar un sistema eficaz de enfriamiento.
Solución
Tras la realización de un análisis térmico de la pieza se constató que la zona crítica se desmoldeaba a temperatura muy alta, estando el núcleo de la pieza a 120°C, es decir, por encima de la temperatura HDT del PP. La razón de tan alta temperatura era debido al diseño de la pieza, que no era adecuado por tener un mayor espesor en esta zona. El sistema de refrigeración no resultaba eficiente, incluso contando con la ayuda del material con el que estaba fabricada la corredera, Cu-Be (conductividad térmica elevada). Se descartó aumentar el caudal y reducir la temperatura del refrigerante al aparecer problemas de llenado en el resto de la pieza.
La solución pasó por optimizar el sistema de refrigeración construyendo un circuito exclusivo para la zona problemática, que ayudara a extraer de manera eficiente el calor

1) En primer lugar se diseñó un inserto para el molde que incorporara detalles complejos de la geometría de la pieza, sistema de refrigeración adaptado a la forma de la pieza, entrada y salida para el refrigerante y sujeción al molde.
A continuación se muestra el inserto por capas para que se pueda apreciar claramente cómo se diseñaron los canales.
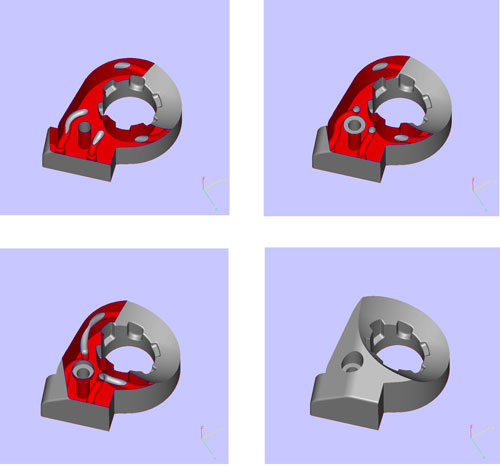
2) En segundo lugar se realizó la fabricación directa del inserto con la tecnología Laser Cusing, en material acero CL 50 (DIN 2709), para herramientas respetando así todos los detalles geométricos. Las características del material empleado fueron las siguientes:
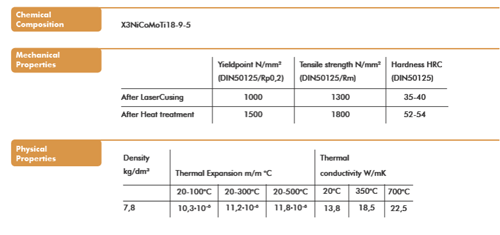
A continuación se muestran una secuencia de imágenes del proceso de fabricación:
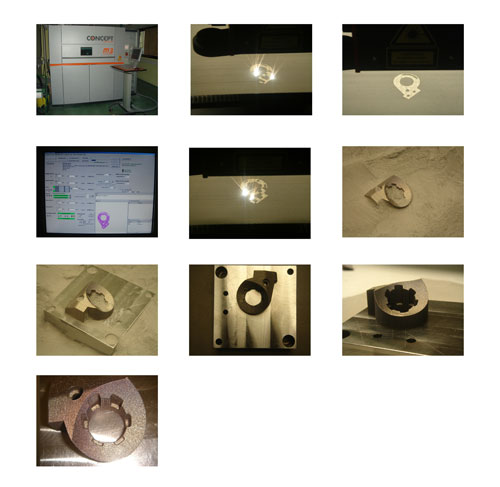
3) En tercer lugar se separó el inserto de la base (necesaria para su fabricación con esta tecnología, mediante corte por hilo) y posteriormente se realizó el acabado del inserto, puliendo las superficies que así lo necesitaban.
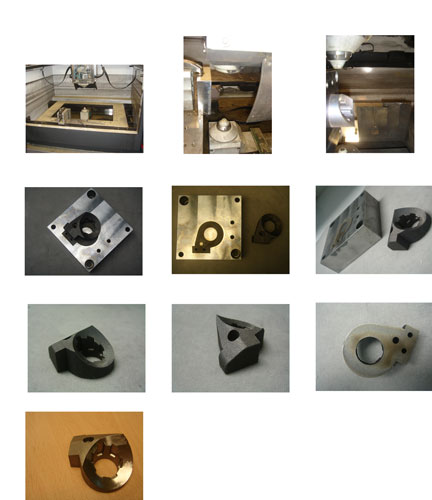
4) Por último se llevó a cabo el montaje, ajuste y ensayo del inserto constatándose su correcto funcionamiento sin fugas de agua, sin poros en el material, con la dureza suficiente para soportar largas series de fabricación, con el máximo detalle de definición de la pieza inyectada y permitiendo suprimir las deformaciones al tiempo que se reducía considerablemente el tiempo de ciclo.
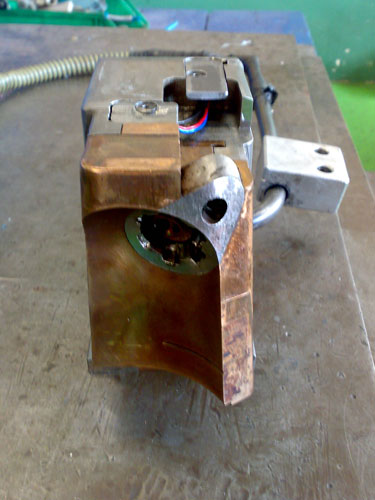
Resultados
- Piezas sin deformaciones.
- Mejora de la productividad un 25%, de 55 piezas/h a 70 piezas/h
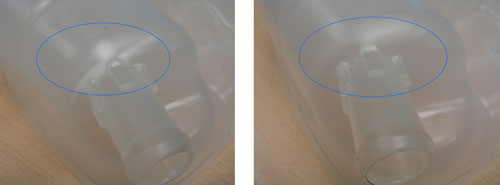
Como conclusión se puede comprobar que la tecnología Laser Cusing resulta ser la tecnología ideal para la fabricación de insertos de molde que incluyen canales de refrigeración optimizados.
Las tecnologías de ‘construcción generativas’ están especialmente indicadas para fabricar cualquier canal de refrigeración en el interior de un postizo, aunque su trayectoria no sea recta, de secciones variables, tamaño reducido y muy próximos a la superficie sin riesgo de filtraciones o fugas.
La tecnología Laser Cusing dispone de un sistema de centrado y referencias que permite que los insertos fabricados puedan ser montados en el conjunto del molde sin problemas.
El material empleado es un acero para herramientas de alta dureza superficial, resistencia y densidad iguales o superiores a los aceros estándar para moldes.
La inclusión de un inserto de estas características conlleva ventajas económicas como una cadencia de producción un 25% mejorada y un ahorro considerable en materiales al sustituir el inserto de Cu-Be por uno de acero refrigerado.