"E-Manufacturing" mitjançant sinteritzat per làser per a la producció de sèries
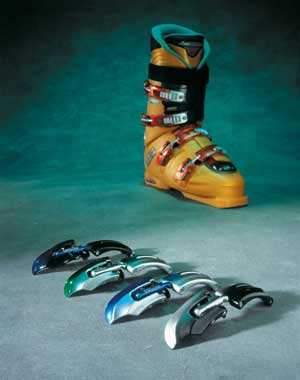
- Producció directa de prototips funcionals en diversos materials plàstics.
- Producció directa d'útils en metall per a motlles d'injecció de plàstic i altres aplicacions.
- Producció directa de patrons i motlles per a diverses tècniques de fusió.
- Producció directa de peces d'ús final en quantitats el nombre varia d'una sola peça (peces úniques) fins a desenes de milers.
Per cobrir aquest ampli rang d'aplicacions, s'ha triat el terme e-Manufacturing, que es refereix a la producció ràpida, flexible, i rendible de peces directament des d'un fitxer electrònic. Pot incloure els termes "rapid prototyping", prototipatge ràpid, "rapid tooling", "(spare) Parts on demand", fabricació de peces o recanvis sota comanda, etc. Les recents innovacions relatives a les màquines de sinteritzat per làser, materials, accessoris i mètodes de postprocés han augmentat el rang d'aplicacions, gràcies a la millora en les propietats de les peces. Al mateix temps els aspectes econòmics de la tecnologia han estat millorats considerablement
Aquest article presenta i lustra casos reals recents mostrant projectes d'èxit amb "e-Manufacturing". Els exemples inclouen la producció de lots de petites sèries, i la producció de sèries personalitzades, per a diversos sectors industrials.
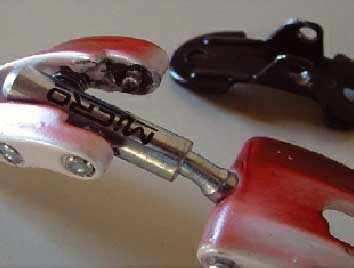
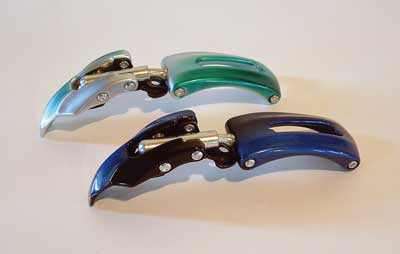
Un projecte dut a terme per Tecnologia & Design lustra bé com el "i-Manufacturing" a través de sinteritzat per làser, pot ser aplicat de forma beneficiosa per a la producció de petites sèries d'aquests productes, en aquest cas del tancament d'una bota d'esquí (Fig.1). El tancament el componen dues peces principals de plàstic unides per una barra metàl·lica i muntades sobre un suport metàl·lic, en forma de fulla (Fig. 2). Tant l'aspecte com la funcionalitat del tancament vénen determinats fonamentalment per les peces de plàstic, les quals tenen acabats i formes lliures complexes. Les reduïdes dimensions, l'escassa quantitat a produir i la complexitat de la geometria constitueixen una coincidència ideal per aprofitar els avantatges que ofereix el "i-Manufacturing. Però en aquest producte dos importants requeriments han de ser coberts. Primer, el producte ha de suportar pes i impactes de manera repetida. Segon, en ser una part visible ha d'assolir els més elevats estàndards estètics.
Les peces en plàstic van ser produïdes directament per sinterització per làser amb poliamida 2200 (niló 12) com a material de sèrie. Les peces van ser després polides i revestides. L'article acabat (Fig. 3) és impossible de distingir respecte dels tancaments produïts a través de mètodes convencionals. Tant el test de fatiga, com el test d'impacte van ser efectuats amb resultat satisfactori.
En Tecnologia & Design també van analitzar la rendibilitat de produir les dues peces de plàstic i comparar els resultats amb el model tradicional, via motlle d'injecció. L'anàlisi econòmica va mostrar que per a una mida de lot de fins a 600 peces, la via del sinteritzat per làser és més barata que l'opció de motlle d'injecció. Una anàlisi de temps va mostrar que, utilitzant un sistema EOSINT P380, un lot complet de 600 tancaments podia ser produït en 27 dies, mentre que mitjançant motlle d'injecció eren necessaris 65 dies.
Evidentment la via del "e-Manufacturing" ofereix més beneficis addicionals tals com flexibilitat en la producció, possibilitat de modificar el disseny sense costos addicionals, etc.
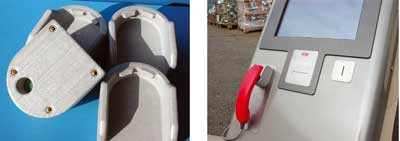
Suports d'auriculars telefònics per a les cabines públiques
Els suports van ser realitzats a través de sinterització per làser en una EOSINT P 380 utilitzant com a material Alumide, una poliamida 12 barrejada amb alumini. Després del procés de construcció, la superfície va ser suavitzada completament amb el mètode AutoFinish. La plataforma de treball de l'EOSINT P 380 va ser prou gran per produir 120 suports en un sol procés de construcció (Fig. 5). Cadascun dels suports va aconseguir les exigències de producte final especialment atenent a l'aspecte metàl·lic, qualitat de superfície, rigidesa, resistència i precisió quant a les seves dimensions.
D'aquesta forma, els suports van ser instal·lats a les cabines de telèfon públiques amb molt bons resultats. A causa de l'enorme èxit que va obtenir el projecte, Telekom Àustria va decidir produir més suports d'auricular telefònic mitjançant sinteritzat làser. En aquest moment està planificat construir una quantitat de 300 a 500 peces any. Això significa realitzar només 4 processos de construcció a la EOSINT P 380. Les modificacions sobre el disseny són possibles en qualsevol moment, sense costos.
Aquest exemple mostra com és possible realitzar una producció de petites sèries a través de sinterització per làser de forma reeixida, sense inversions inicials en utillatge o motlle. Les propietats del producte arriben als requeriments en tots els aspectes. Més encara, les superen fins i tot.
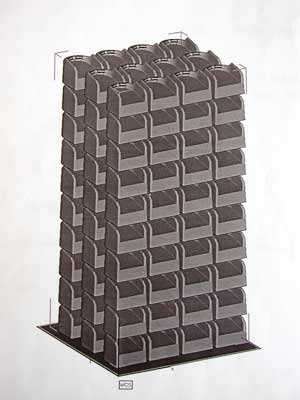
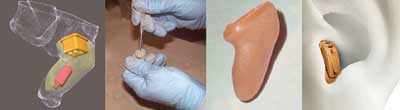
Producció massiva de productes a mida
- Alta precisió i enfocament en el detall per assentar bé a l'oïda.
- Parets fines que deixin espai per a l'electrònica.
- Biocompatibilitat, és a dir, permetre el contacte amb la pell sense alteracions lèrgiques.
- Ha de superar l'entorn vital del cos (greix, suor, etc.) Durant anys sense degradar-se.
Tradicionalment aquestes carcasses han estat fabricades prenent una impressió de cera de la cavitat de l'oïda del pacient, formant un motlle flexible voltant d'ell i colant dins d'ell una resina acrílica curable per UV. Això consumeix molt de temps en treball manual i si la carcassa no encaixa perfectament en el sentit tot el procés ha de començar de nou.
Per això existia, una necessitat, i un alt potencial de millora. Phonak va identificar la possibilitat d'optimitzar aquest procés mitjançant el sinteritzat per làser directe de les carcasses, i va desenvolupar la cadena de processos corresponent. Avui en dia les impressions en cera se sotmeten al escàner, les dades digitalitzats són convertits en carcasses virtuals que s'adapten tant a cau d'orella del pacient com a l'electrònica, i després són sinteritzades per làser (Fig. 6).
Phonak ara construeix fins a tres nivells de carcasses per treball, cada nivell contenint 60-120 carcasses, amb mesures que van des de 10 x 10 x 15 mm a 30 x 30 x 25 mm.
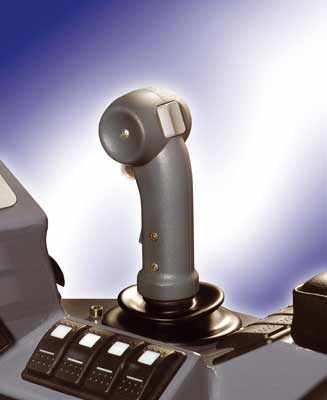
Producció de sèries rendibles mitjançant la fabricació de motlles o estris
Per a la producció d'una de les peces plàstiques FIT utilitzar el sinteritzat per làser directe sobre plàstic, de manera similar als projectes descrits abans. Per als altres 14 components es requeria injecció en motlle de PA 06/06 GF 30 (poliamida amb fibra de vidre). FIT va construir l'utillatge utilitzant el sinteritzat per làser directe sobre metall. Per poder produir l'utillatge complet per als 14 components en el termini de poques setmanes va ser necessari optimitzar tant el concepte del motlle com el del procés. El concepte utilitzat es lustra mitjançant la injecció de motlle mostrada a la Fig 8. Aquesta mostra un motlle de quatre cavitats contenint els costats dret i esquerre de les cavitats per a dues de les parts. Cada cavitat ha estat dissenyada de tal manera que hagi de ser sinteritzat per làser el mínim volum de material. L'utillatge sencer va poder ser produït en una única màquina EOSINT M 250 Xtend en només 290 hores.
De fet el client va fer diverses modificacions en les peces després que el projecte hagués ja iniciat, el que va provocar 3 setmanes de retard en el projecte. Però amb l'ajuda dels seus tecnologies de sinteritzat per làser, FIT va mantenir la seva disponibilitat en el lliurament, a Hamm, de totes les peces necessàries per al llançament del producte a la fira. El lot complet de producció va seguir servint-se en temps rècord i amb la màxima qualitat.
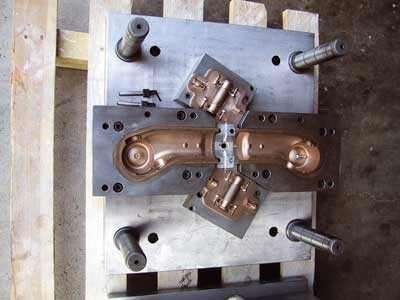
Resum i comentari
Una força important que empeny aquesta tendència és el factor "cost per peça". Hi ha una tendència general al mercat, cap a l'increment de les variants de producte i també cap a cicles de vida dels productes més curts. Aquestes tendències donen com a resultat un menor nombre de peces requerides per variant, és a dir, menors quantitats de producció. El "e-Manufacturing" té un avantatge natural en aquesta situació. També les millores que van incorporant, quant a la productivitat dels sistemes de sinteritzat làser ia la cadena de processos, signifiquen que els punts d'equilibri milloren de forma continuada. És a dir, les quantitats per les que l'ús del "e-Manufacturing", d'una geometria donada, és més econòmic que la producció convencional, estan augmentant.
I en darrer lloc, però no per això menys important: El sinteritzat per làser és i serà la tecnologia clau per al "e-Manufacturing" gràcies, de manera particular, a les propietats dels materials disponibles. També hi ha d'haver més mètodes de postprocés, i més automatitzats, per exemple per al polit o revestiment de peces sinteritzades per làser, de manera que es podran arribar a aconseguir textures i patrons específics.