Readaptación fácil y escalable basada en IoT
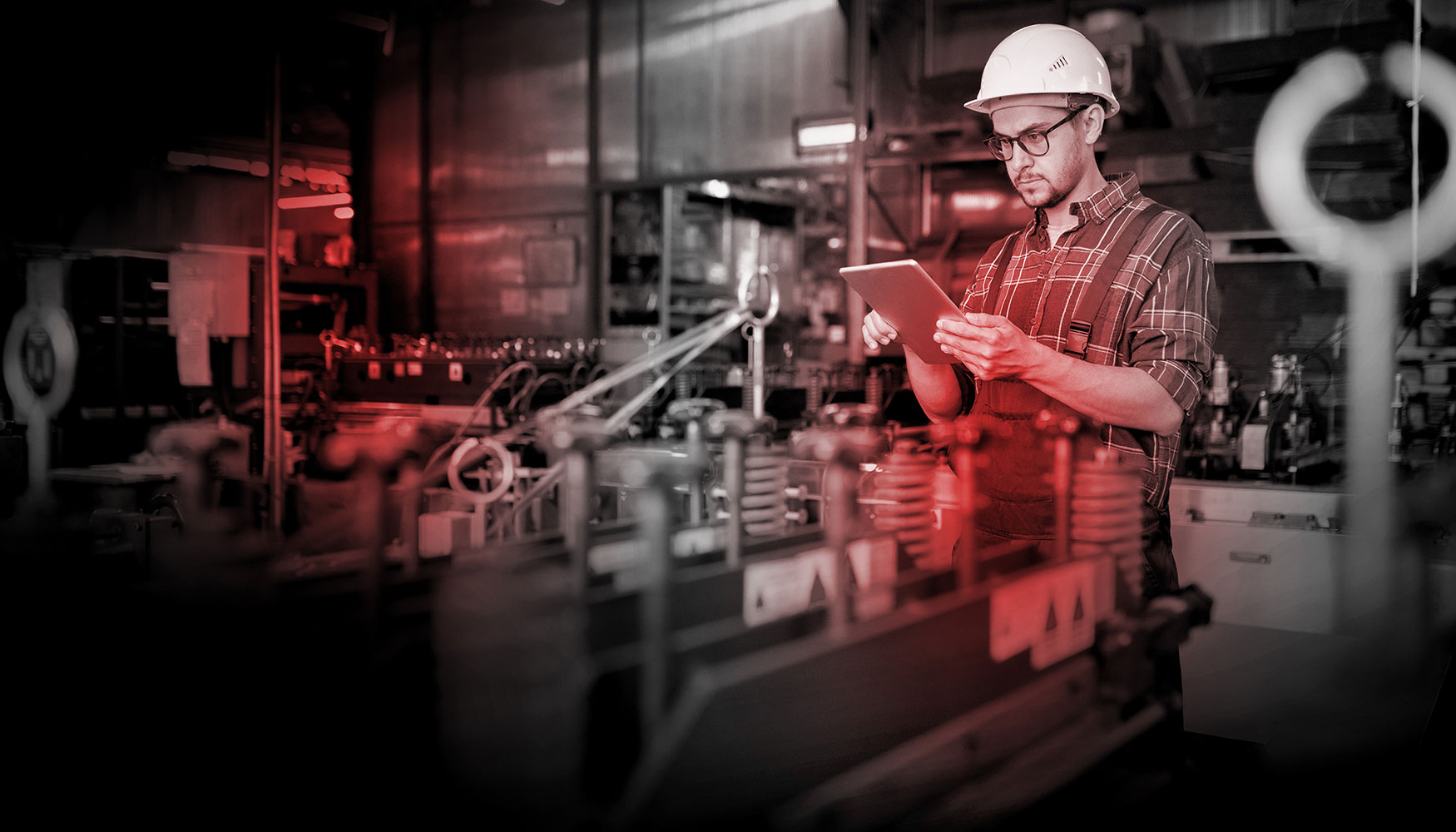
Fuente: pressmaster.
Se tiende a creer que la tecnología más reciente y avanzada es superior. A veces, sin embargo, es mejor utilizar tecnologías probadas de hace décadas, actuales o incluso heredadas. Por supuesto, los equipos antiguos plantean otros retos, tales como la eficiencia, la calidad irregular, el mantenimiento costoso y el trabajo manual.
La sustitución de equipos de fabricación antiguos conlleva una serie de distintas consideraciones para los propietarios de empresas. No es poco frecuente que los equipos heredados representen inversiones de capital de millones de dólares y años de planificación. Por consiguiente, el enfoque de la readaptación resulta más rentable.
Los entornos de producción pueden experimentar mejoras sustanciales con la incorporación de la automatización inteligente. Los sistemas existentes pueden crear valor adicional mediante una mayor automatización. Dado que las máquinas más antiguas suelen estar ya amortizadas, el impacto económico de una mayor productividad, sin necesidad de grandes inversiones nuevas, resulta especialmente ventajoso para sobrevivir en un mercado internacional. Para que la modernización tenga éxito, las máquinas automatizadas deben registrar y analizar con precisión los datos operativos. Además, es esencial que las conclusiones extraídas de estas evaluaciones puedan hacerse extensivas a otros centros de fabricación.
La dificultad planteada con las máquinas heredadas es que carecemos de los conocimientos necesarios para formular las preguntas adecuadas. ¿Cómo puede resolverse este planteamiento? La readaptación de las máquinas constituye la mejor estrategia.
La readaptación es el proceso de actualizar o añadir nuevas funciones a equipos existentes mediante una solución de IoT de forma no invasiva. La transformación de una máquina en su gemela digital permite examinar y optimizar la producción con mayor detalle y eficacia.
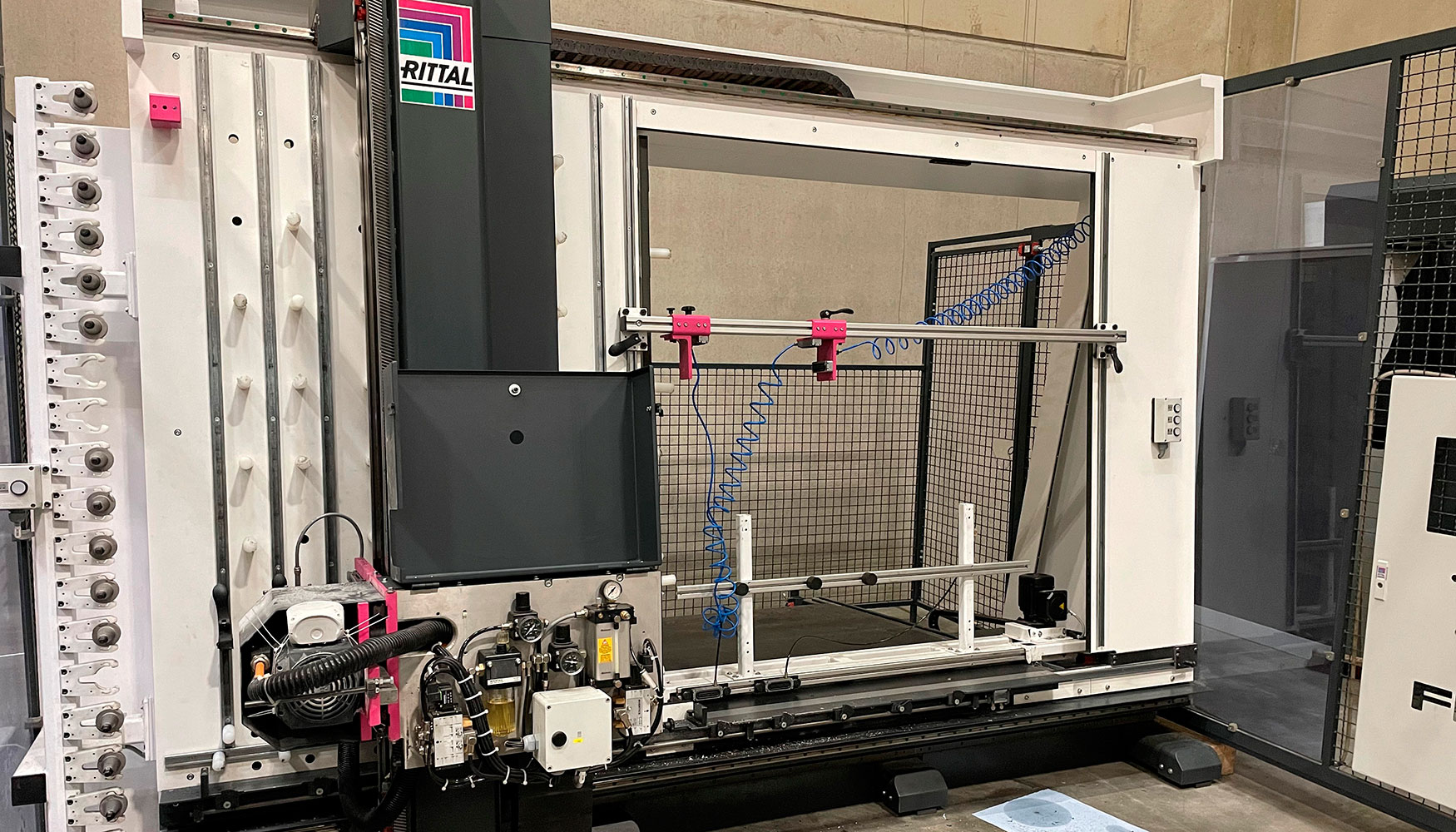
Figura 1. Máquina de corte industrial de FEGA & Schmitt con monitorización. (Fuente: Würth Elektronik eiSos).
Prueba de concepto en asociación
Würth Elektronik es un ferviente partidario del concepto de código abierto y, junto con FEGA & Schmitt e IAV, ha realizado esta prueba de concepto para la supervisión de máquinas de corte industriales (Figura 1). FEGA & Schmitt conceptualizó este proyecto, Würth Elektronik suministró componentes de conectividad y detección y, junto con IAV, proporcionó soluciones de infraestructura en la nube (Figura 2). IAV también ofreció análisis de datos y servicios completos de integración de sistemas.
El objetivo era desarrollar un producto fácil de instalar para los clientes de FEGA & Schmitt, con el fin de supervisar máquinas de corte industriales y detectar su utilización basándose en mediciones de corriente, así como detectar posibles problemas con las herramientas de corte antes de que se produzcan.
A veces, una determinada combinación de movimientos de la herramienta puede provocar su rotura. Al identificar este conjunto de movimientos, se puede realizar una predicción de fallos. En consecuencia, habrá mucho menos tiempo de inactividad en la producción. Por otro lado, la medición de corriente permite determinar la utilización de la máquina y simplifica el proceso de planificación.
Durante la prueba de concepto, uno de los requisitos estrictos de la instalación era no interferir en la infraestructura del cliente ni causar periodos de inactividad en los procesos.
Los clientes reciben información completa sobre la disponibilidad del sistema a partir del producto acabado. El mantenimiento predictivo es una característica clave y diferenciadora de los productos de FEGA & Schmitt mediante el uso de sensores y la evaluación de datos asistida por IA.
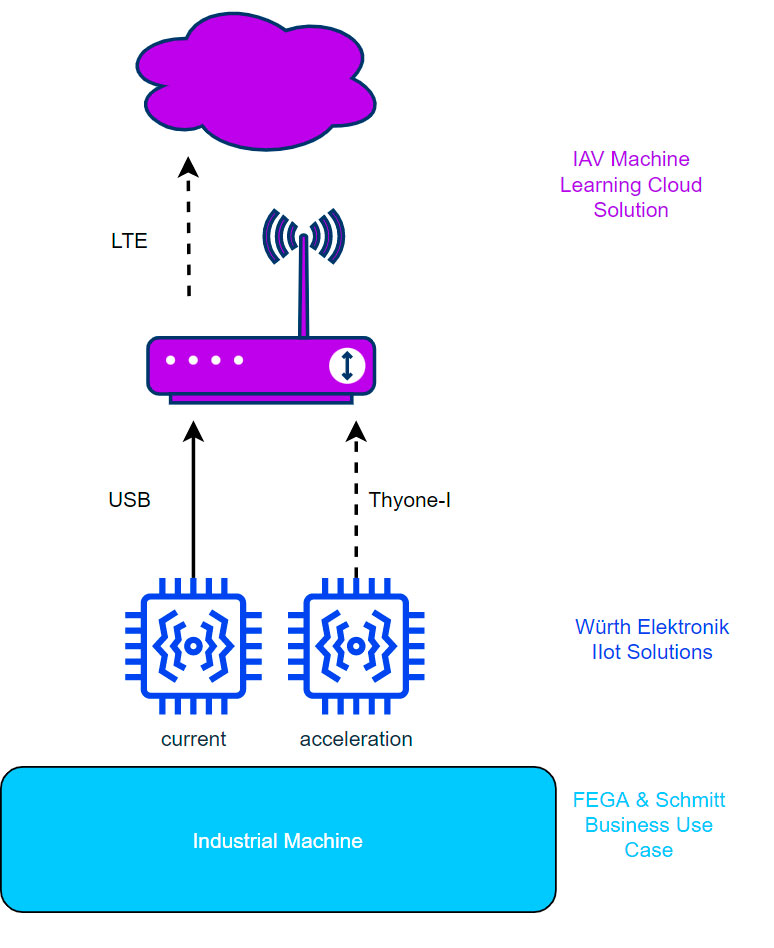
Figura 2. El concepto de readaptación basada en IoT y las funciones de las empresas asociadas. (Fuente: IAV).
Prototipos con placas FeatherWing
FeatherWings es un conjunto de placas de prototipado apilables con distintas funcionalidades. Würth Elektronik ha creado una gama de placas de desarrollo FeatherWing de código abierto y totalmente compatibles con el factor de forma Feather. Esto incluye Sensor Featherwings, conectividad inalámbrica WE Pro-Ware, Wi-Fi y varias fuentes de alimentación. Existe un repositorio GitHub [1] para todas las placas de código abierto, incluidos sus esquemas, lista de materiales/componentes, software y descripciones de conectividad a la nube para Azure y AWS.
Detección por aceleración
Las Sensor FeatherWings (Figura 3) se utilizan para crear los puntos de datos iniciales. Dado que la aceleración está estrechamente relacionada con el movimiento de la mano de corte, el uso de un sensor de aceleración es un buen punto de partida para supervisar los movimientos.
WE Sensor FeatherWing es una placa de desarrollo con cuatro sensores. Además del factor de forma Feather de Adafruit, también es compatible con QWIIC-connect de Sparkfun, que proporciona una interfaz I2C estándar que también es compatible con STEMMA QT y Grove/Gravity. Esto ofrece infinitas posibilidades para la creación de prototipos.
Todo lo anterior facilita el plug-and-play de varios sensores y dispositivos de diferentes fabricantes sin mucho cableado y lo hace extremadamente útil para la creación de prototipos.
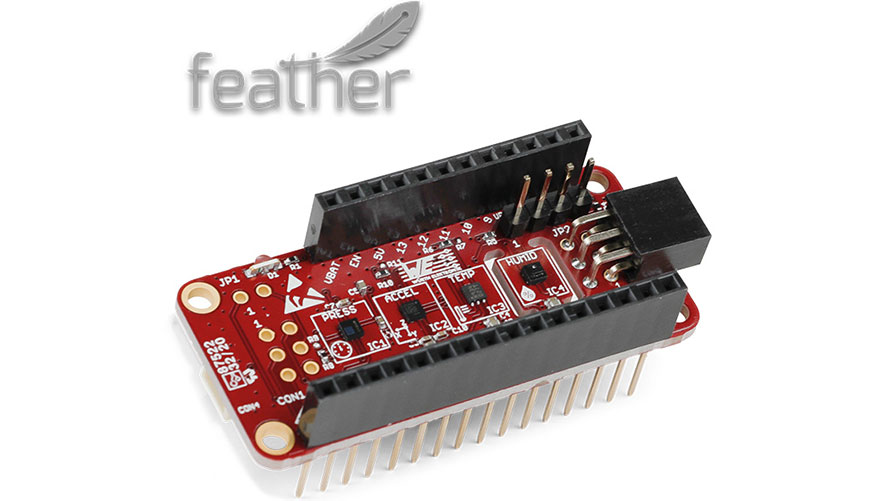
Figura 3. WE-Sensor FeatherWing. (Fuente: Würth Elektronik eiSos).
Conectividad por LTE-M/NB-IoT
La conectividad de nodos y pasarelas se resuelve de diferentes maneras. La conectividad de pasarela/nube puede establecerse mediante dos métodos distintos. Utilizando una Raspberry Pi industrial con conectividad LTE, se envían grandes cantidades de datos a la nube para el análisis espectral durante toda la fase de generación del modelo. Una vez creado el modelo, la conectividad pasa al módulo Adrastea-I LTE-M/NB-IoT de Würth Elektronik. Esto reduce enormemente el tráfico de red y, por consiguiente, los costes. Ambos métodos se han probado en entornos de producción conectados a la nube.
El nodo se conecta a la nube mediante una pasarela que utiliza el módulo de radio propietario Thyone-I Wireless de 2,4 GHz. No hay que subestimar la seguridad, por lo que la pasarela de conectividad a la nube utiliza el protocolo TLS y el nodo emplea un enfoque similar con el elemento seguro (ATECC608A-TNGTLS de Microchip Technologies) por un lado y la bóveda de claves de la nube por el otro. Toda la conexión está protegida y cifrada entre todos los participantes en la comunicación: nodos, pasarelas y la nube.

Figura 4. Medición de vibraciones mediante un acelerómetro. (Fuente: Würth Elektronik eiSos).
Implementación en detalle
Medición de vibraciones
Para seleccionar el acelerómetro adecuado, es esencial comprender claramente la aplicación y sus tareas de medición. En este caso, se utilizó un sensor MEMS de aceleración de 3 ejes para detectar los movimientos del brazo de corte. Los desarrolladores llevan mucho tiempo esperando aprovechar las ventajas que ofrecen los sensores MEMS en cuanto a tamaño, coste y fiabilidad y todo ello se aprovechó al máximo con el empleo de un sensor de aceleración de 3 ejes WSEN-ITDS (Figura 4).
Medición de corriente
Las mediciones de corriente deben ser no invasivas, ya que no se puede interferir en los dispositivos que se van a monitorizar. La solución debería ser fácilmente aplicable a cualquier máquina similar. Para ello, se utilizó el transformador de corriente de núcleo partido 855-4101/400-001 de WAGO y la placa SparkFun Current Sensor Breakout ACS723 con sensor de efecto Hall (Figura 5). La ventaja de utilizar un sensor de efecto Hall es que el circuito que se detecta y el circuito que lee el sensor están aislados eléctricamente; por lo tanto, el circuito que se detecta puede funcionar a tensiones CC o CA más altas que la placa principal.
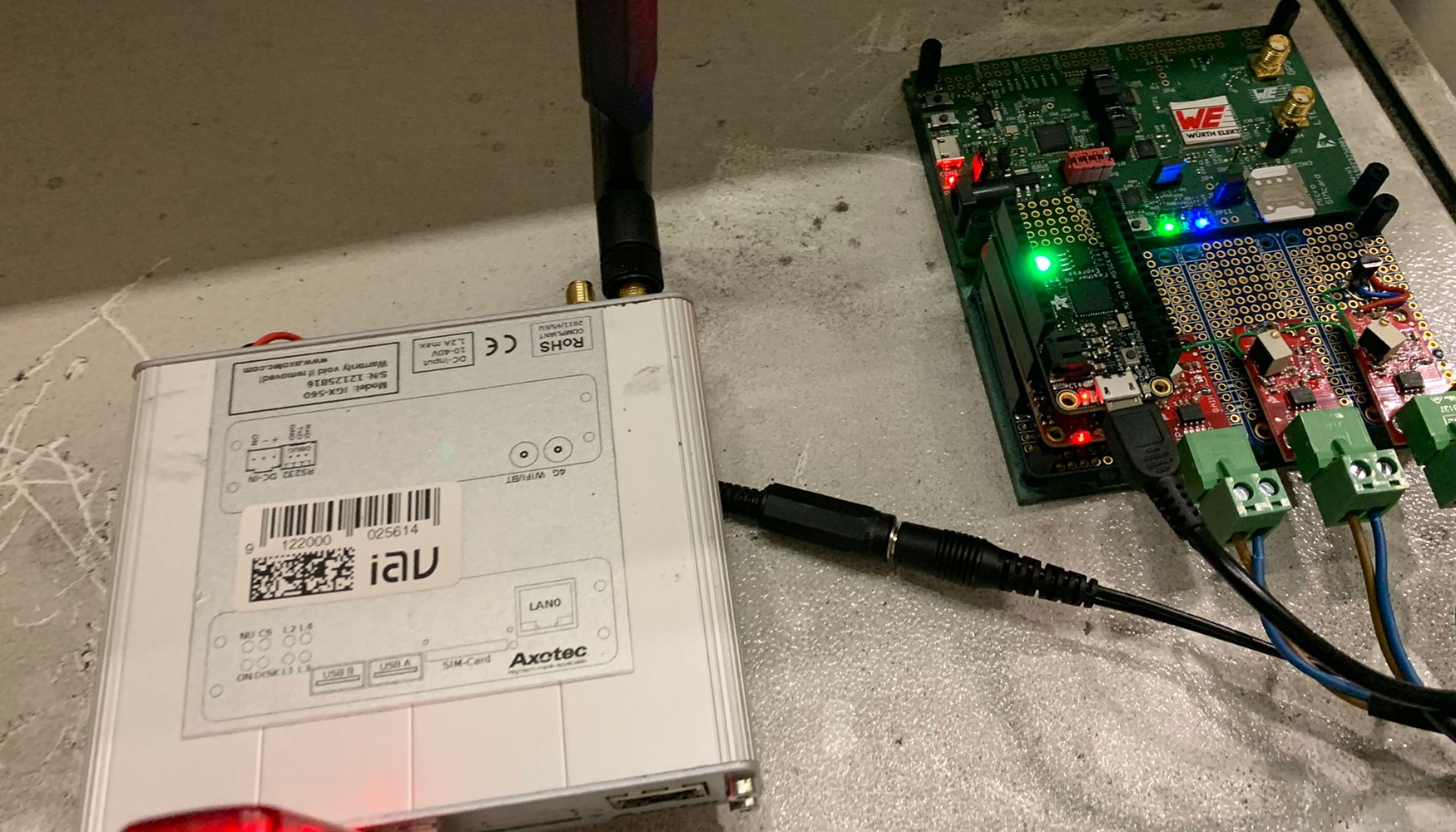
Figura 5. Medición de corriente mediante un sensor de efecto Hall. (Fuente: Würth Elektronik eiSos).
Soluciones de conectividad
Para la prueba de concepto, se utilizaron dos versiones de las soluciones de conectividad. La versión uno de la conectividad, utilizada en la fase inicial de recopilación de datos, era una pasarela compatible con Raspberry Pi de IoT de uso industrial. Se utilizó un sistema basado en Linux para generar el código C y optimizar la recopilación y transferencia de datos, ya que se necesita un gran volumen de datos para validar el comportamiento de la máquina. Para la nube, se creó un panel de control para la monitorización en tiempo real de los datos utilizando Node-Red y Grafana. Además, se analizaron los datos de flujo temporal a fin de identificar tendencias y patrones con aprendizaje automático. Los patrones de procesos similares se reconocen y etiquetan automáticamente (Figura 6). El resto de patrones se marcan como desconocidos. Estos datos sirven de base para las estadísticas de procesos que pueden utilizarse para diversos casos de uso empresarial, como la supervisión de procesos, el control de calidad y el mantenimiento predictivo.
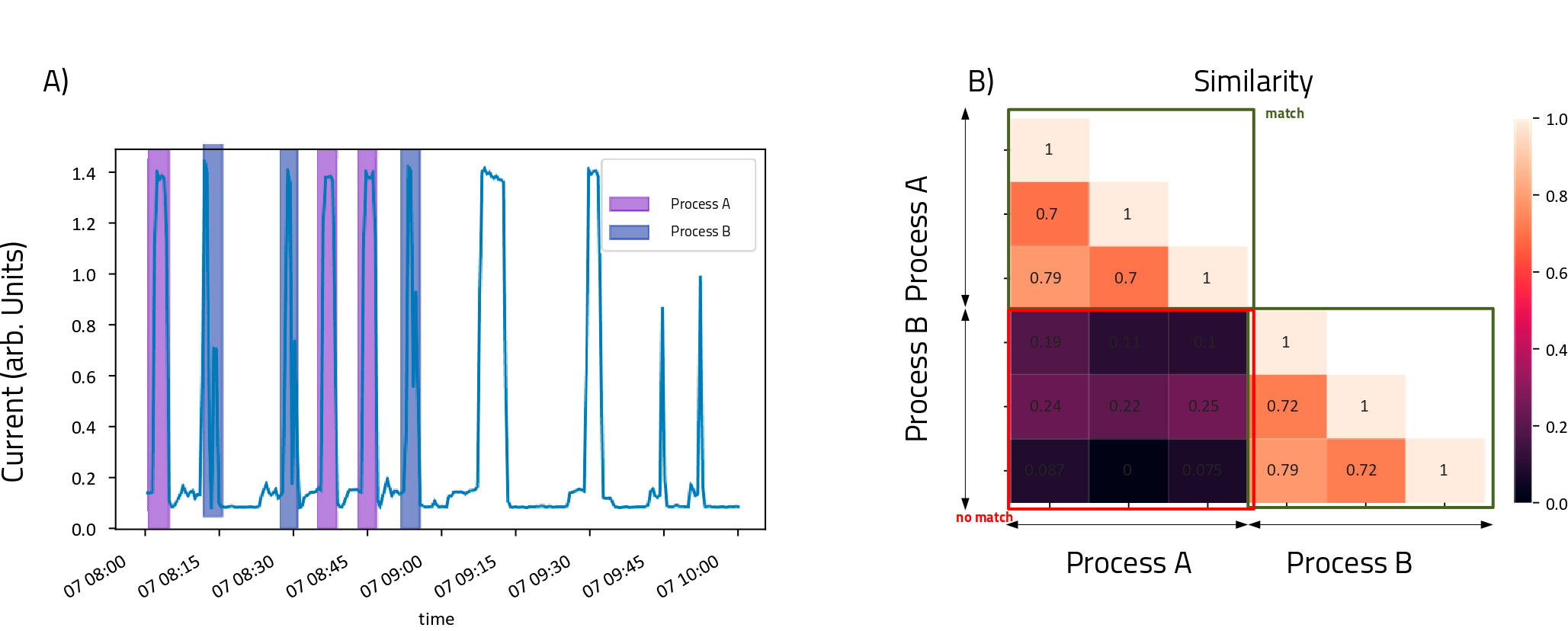
Pruebas en un entorno real
Durante las pruebas reales se plantearon numerosos retos: pérdida de datos a causa de la distancia y de las diversas fuentes de radio de la nave de fabricación, movimiento constante de las placas apilables y de la fuente de alimentación, o falta de ella.
Los sensores de aceleración se montaron en el brazo de corte sin ninguna fuente de alimentación cercana. Este obstáculo se superó con la ayuda de una batería LiPo. A pesar del bajo consumo de corriente en espera, la transmisión constante de datos durante la fase inicial agotó la batería. A diario se transmitían grandes cantidades de información, lo que provocaba que la batería se agotara cada dos o tres días. La solución fue utilizar un panel solar para cargar la batería. Para ello, se utilizó una solución de código abierto de Adafruit.
El segundo problema era la ubicación de los sensores y los módulos de radio. El sensor debe estar situado en el mango de la herramienta, que es una pieza móvil. En la máquina, todas las piezas móviles están protegidas por carcasas metálicas, que actúan como una jaula de Faraday. A pesar de ser pequeña y eficaz, la antena integrada no servía para nada. Este problema se resolvió colocando una antena externa en el exterior de la carcasa.
La parte de detección de corriente consta de transformadores de corriente de núcleo dividido y sensores de efecto Hall para cada fase. La combinación de dos sensores requirió una calibración que fue realizada por Würth Elektronik.
Acelerar la creación de prototipos
Hacer una prueba de concepto con componentes de código abierto puede reducir drásticamente el tiempo de creación de prototipos. La combinación de placas preexistentes con contactos estándar y sensores con conectores estándar, facilita las pruebas y la experimentación con la configuración.
La utilización de dos etapas en la creación de prototipos de prueba de concepto permitió crear un modelo eficaz en la primera etapa, que luego pudo aplicarse en la segunda. La segunda etapa utilizará modelos locales en el microcontrolador y solo enviará la cantidad mínima de datos. Los datos necesarios se enviarán a la nube mediante el módulo celular Adrastea-I.
Würth Elektronik ofrece SDK gratuitos de estilo Arduino para diferentes procesadores y vende las placas. Estas placas pueden adaptarse fácilmente con los datos (PCB y BoM) de Würth Elektronik o Awesome Feather GitHub de Adafruit [2].
Este caso práctico demostró que el uso de estándares de código abierto para la creación de prototipos ofrece flexibilidad, lo que se traduce en una enorme velocidad de implementación.
Referencias
Sobre los autores
Adithya Madanahalli se licenció en Ingeniería de Comunicaciones por la Universidad Técnica de Múnich. Después trabajó varios años como ingeniero de software en el campo de la conectividad inalámbrica y los sensores. Desde 2022, Adithya es ingeniero de IoT en Würth Elektronik eiSos en la división 'Wireless Connectivity and Sensors'. Se especializa en el diseño y desarrollo de soluciones de IoT centradas en hardware, software integrado y seguridad integral.
El Dr. Jan Gieseler es diplomado en física por la Universidad de Karlsruhe y licenciado en optoelectrónica y láseres por la Universidad Heriot Watt (Escocia), tras lo cual se doctoró en fotónica por el ICFO de Barcelona (España). Después, siguió trabajando como científico postdoctoral en investigación fundamental en la ETH de Zúrich, la Universidad de Harvard y el ICFO. En 2020, Jan se incorporó al DigitalLab de IAV en Berlín. Allí trabaja como científico de datos centrado principalmente en ingeniería de datos, análisis de series temporales y soluciones de IoT y sensores inteligentes.
Bernd Grimm es licenciado en Economía de la Empresa y Tecnologías de la Información. Desde que empezó a trabajar en el sector mayorista de la electricidad en 2008, él y sus equipos han trabajado en numerosos proyectos con un marcado enfoque en el servicio al cliente. Lleva en el cargo de jefe de gestión de proyectos en el ámbito de la industria y las instalaciones en FEGA & Schmitt desde 2019. Como tal, colabora con su equipo en el proyecto 'Be.Linked', cuyo objetivo es establecer el tema de la “distribución de servicios emparejada con la digitalización y la IA” para FEGA & Schmitt.
Miroslav Adamov estudió Física e Informática en la Universidad de Belgrado (Serbia). Posteriormente, prosiguió su labor científica en TU-Berlin, WIAS Berlín, FAU Erlangen/Núremberg y el Center of Private Equity Research de Múnich. Tras un par de años en finanzas cuantitativas, en 2015 se incorporó a Würth Elektronik como Senior Business Analyst. En 2017 asumió el cargo de Senior IoT Solution Architect con un enfoque principal en la conceptualización e implementación de soluciones de IoT industriales.
Eduard Richter completó su formación como técnico electricista titulado y licenciado en Administración de Empresas. Desde 2017 trabaja en el comercio mayorista eléctrico como gestor técnico de cuentas clave. Su tarea consiste en posicionar los servicios de FEGA & Schmitt entre los clientes existentes y los nuevos. Gracias a su experiencia en ventas, contribuye al desarrollo y la mejora de los servicios.