Diseños de automóviles cada vez más complejos se hacen realidad gracias al avance de las tecnologías de soldadura de plásticos
Craig Birrittella, gerente de desarrollo de negocios del mercado automotriz para la línea de productos de soldadura y montaje de Branson en Emerson
24/05/2023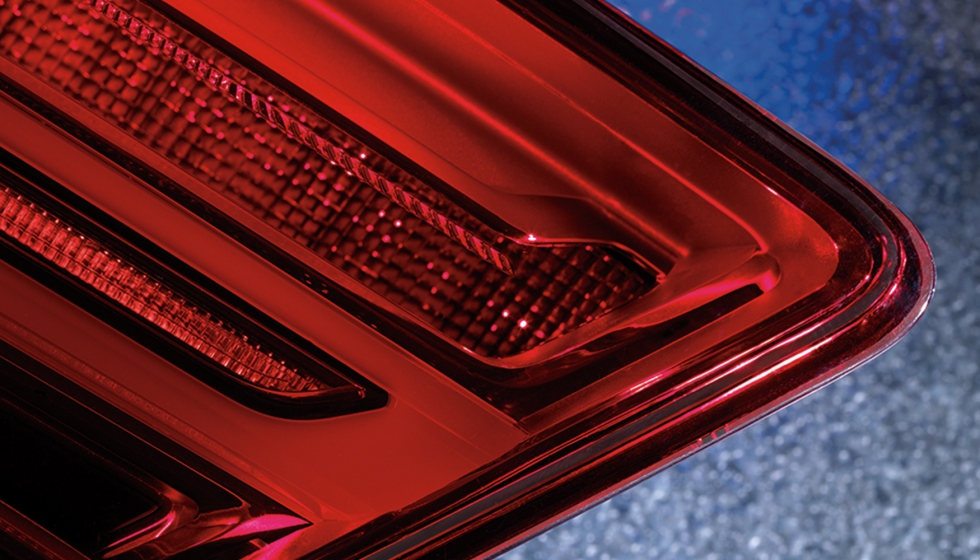
Los plásticos revolucionaron el diseño y la fabricación de automóviles, desde componentes interiores y exteriores hasta paneles de carrocería completos y piezas debajo del capó. Para lograrlo, hizo falta desarrollar una amplia gama de nuevas técnicas de ensamblaje que sustituyeron a las fijaciones mecánicas, así como a los adhesivos, y que sirvieron para reducir costos, mejorar la productividad y aumentar la seguridad en el trabajo. Hoy en día, esa revolución sigue adelante a muy buen ritmo, ya que los fabricantes de automóviles van sacando partido de las continuas mejoras en la tecnología de procesamiento y ensamblaje de plásticos, especialmente en el ámbito de la electrónica.
Un buen ejemplo de este fenómeno son los nuevos diseños de luces traseras centrales que se pueden ver en los automóviles actuales. Los módulos de luces traseras pequeños y relativamente sencillos están dando paso a conjuntos de una sola pieza, donde el estilo es más importante, y que pueden medir hasta 1.400 mm de lado a lado con complejos contornos multidimensionales. Y eso si hablamos solo de las carcasas exteriores. Si nos centramos en el interior, la sofisticación lograda en la electrónica impresiona, con conjuntos de luces orgánicas LED (diodos emisores de luz) que sirven para indicar los cambios de dirección y de frenado e iluminar las trayectorias de los coches cuando van marcha atrás. También pueden incluir sensores, dispositivos de radar y cámaras, junto con las placas de circuitos y el cableado correspondientes. Este tipo de ensamblajes han sido posibles gracias a las nuevas tecnologías de soldadura de plásticos y a su vez han dado lugar a otras nuevas que no solo sirven para unir las formas complejas que haya, sino que además lo hacen sin dañar los delicados componentes electrónicos de su interior.
Hace tan solo 10 años, un coche normal y corriente tenía un número relativamente pequeño de sensores, que se encargaban principalmente de monitorizar los componentes del motor de combustión y de la transmisión. Hoy en día, la cantidad de dispositivos electrónicos que hay en un coche puede superar de media los 200 si contamos sensores, radares y cámaras. Todos ellos se encargan de darle al conductor, que puede ser humano o automatizado, información sobre el propio vehículo y también sobre su entorno, como la ubicación de las líneas de los carriles, de otros automóviles, de objetos peligrosos e incluso de seres humanos o animales. Al igual que ocurre con la aplicación del piloto trasero central, estos componentes electrónicos están alojados, fijados y protegidos por estructuras de plástico y su fragilidad supone un reto a la hora de ensamblar estos módulos.
Los vehículos eléctricos y autónomos plantean nuevos retos
La situación va dando lugar a cada vez más retos a medida que aumenta el número de vehículos eléctricos y autónomos. Los automóviles a gasolina actuales están muy conectados e incluyen tecnología que será esencial en los automóviles autónomos. Por este motivo, la actual escasez de chips semiconductores está causando tantos problemas en la producción de vehículos y disparando los precios de los coches tanto nuevos como de segunda mano.
Al mismo tiempo, los diseñadores intentan crear un entorno más personalizado y cómodo para los conductores y para sus pasajeros. Se puede ver esta tendencia en la iluminación interior, en la que unas pocas lámparas individuales, empleadas para facilitar la entrada y la salida del vehículo o para iluminar mapas, están dando paso a la iluminación ambiental e incluso a la inteligente. Cuando un conductor se acerca a su coche, su llavero se comunica con los sensores y enciende la iluminación interna para darle la bienvenida. En las juntas herméticas de estos llaveros también se usan muchos plásticos. Las pantallas de información al conductor son hoy en día un elemento de diseño clave en el interior de los automóviles. Estas pantallas, desde las de los instrumentos del salpicadero hasta las de los mapas interactivos y las selecciones de radio por satélite, están conectadas de forma directa o indirecta a casi todos los sensores y cámaras posibles del coche. Tanto para las carcasas de plástico exteriores de ensamblaje como para todas las placas de circuitos y el cableado del interior de la consola es necesario llevar a cabo un proceso de ensamblaje.
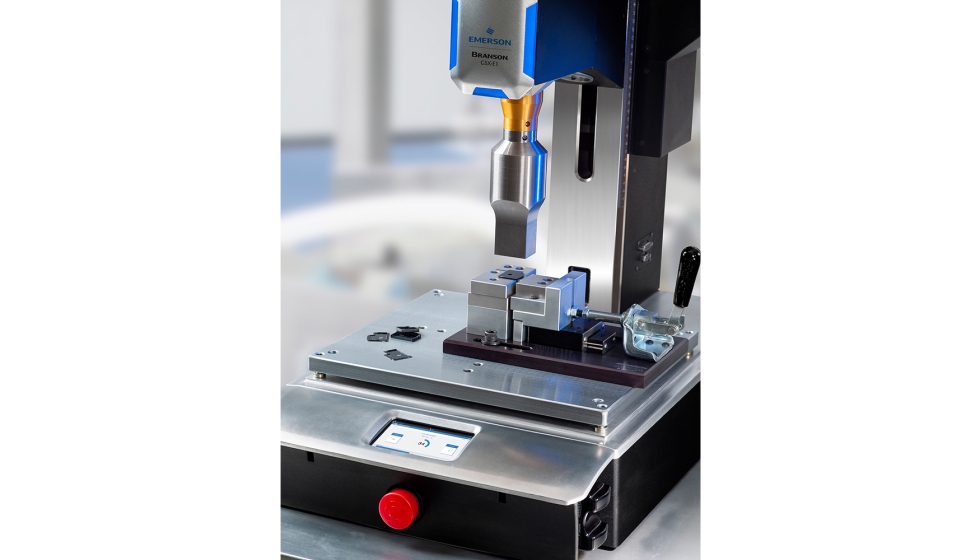
Las tecnologías de soldadura de plásticos se lanzan a superar los retos
La soldadura de plásticos no es tan solo una tecnología, sino que este término de por sí engloba una serie de tecnologías de ensamblaje que van evolucionando para satisfacer la amplia gama de necesidades relacionadas que se dan en el ámbito de la industria automotriz.
La soldadura por ultrasonidos es la técnica más común y probablemente siga siendo la que se lleva con más frecuencia en la unión de componentes plásticos de automoción. Este proceso, que crea un movimiento generador de calor de alta frecuencia entre los componentes que se pretende unir, lleva empleándose desde hace 75 años para unir piezas termoplásticas pero en los casos en que se moldea hasta conseguir una sola pieza resulta demasiado complejo o tiene un costo elevado. En la industria automotriz muchos componentes ya se unen por ultrasonido. Sin embargo, la complejidad, fragilidad y precisión que requieren los sensores, cámaras y componentes de iluminación han llevado a Emerson a desarrollar un nuevo “modo dinámico”, pendiente de patente, que puede ajustarse automáticamente a las particularidades de cada pieza y a materiales únicos. Por ejemplo, esta técnica puede soldar de forma segura piezas de plástico pequeñas, finas o complejas a estructuras de plástico que haya directamente encima de sensores o componentes electrónicos delicados sin dañarlos. También puede soldar piezas que haya encima de ensamblajes de plástico que contengan elementos internos compresibles, como las juntas o los núcleos elastoméricos, y puede manipular materiales que tengan una dureza o una consistencia estructural variable, como los materiales compuestos.
Una nueva tecnología láser, patentada para la soldadura clara sobre clara, conlleva el uso de múltiples haces posicionados en muchos ejes para que la energía pueda aplicarse por toda la superficie de la soldadura, incluso cuando el ensamblaje es de gran tamaño y multidimensional. A diferencia de la soldadura por puntos, que va realizando la soldadura poco a poco, en esta un dispositivo móvil une las piezas aplicándoles presión y permite pre ensamblarlas. Una superficie transmite libremente la energía láser (sin verse afectada) a través de la segunda superficie (que absorbe el láser), donde la energía láser se convierte en calor que se conduce a través de la interfaz, haciendo posible la soldadura.
Los láseres son extraordinariamente versátiles. Pueden soldar docenas de polímeros diferentes, incluidos algunos de los materiales de ingeniería más avanzados. A veces pueden utilizarse incluso con resinas que de otra manera serían imposibles de soldar, como las resinas cristalinas y amorfas o los plásticos reforzados. Normalmente, la superficie pasante es más o menos clara y la capa absorbente es más oscura, pero no siempre tiene por qué ser así. Utilizando diversos revestimientos y aditivos, se puede conseguir que un material que de otro modo sería transparente al láser absorba su radiación, lo que permite crear ensamblajes de capas clara sobre clara.
La tecnología de vibración limpia ofrece a los fabricantes otra opción para las exigentes aplicaciones de la industria automotriz. En la soldadura por vibración convencional, el calor necesario para crear la soldadura se va formando por la fricción de las dos superficies que se van a unir al moverse una contra otra. En cambio, la vibración limpia es un proceso de dos pasos. En primer lugar, los componentes que se pretenden soldar se colocan por encima y por debajo de un emisor de infrarrojos de lámina metálica que se ajusta exactamente a las líneas de la unión. En segundo lugar, el emisor precalienta los plásticos y, una vez que las líneas de soldadura han empezado a fundirse, se retira el emisor, se juntan las dos piezas bajo presión y empiezan a vibrar suavemente. El resultado es una soldadura sin partículas ni otros efectos secundarios indeseables y, además, sin daños en componentes electrónicos sensibles.
La estaca de calor y el estampado son otras dos tecnologías de soldadura probadas que han demostrado ser especialmente eficaces para capturar y asegurar componentes que pueden estar hechos de muchos materiales: plásticos, polímeros reforzados con vidrio, metales, cerámica, telas y medios de filtro, incluso placas de circuito impreso (PCB), interruptores y electrónica. En el proceso de estaca convencional, los componentes se colocan en pequeños postes en una pieza de plástico, mientras que los postes expuestos se moldean usando calor y fuerza para crear discos aplanados, similares a remaches, que fijan los componentes en su sitio.
Uno de los avances más recientes de esta tecnología se denomina estaca por pulsos. Su principal ventaja en el ámbito de la automoción radica en que el calentamiento y el enfriamiento precisos se aplican de forma muy controlada y localizada. Este método es una mejora significativa respecto a las herramientas de estaca térmica anteriores, que irradiaban continuamente calor elevado en todas direcciones antes, durante y después del proceso. La estaca por pulsos se puede aplicar perfectamente para fijar varios componentes muy próximos entre sí que haya en piezas 3D geométricamente complejas. Una sola herramienta puede contener varias boquillas para la estaca por pulsos, lo que les permite realizar al mismo tiempo varias estacas en piezas o conjuntos (empleando diferentes temperaturas y velocidades de enfriamiento, si es necesario). En una única máquina PulseStaking pueden operar hasta 60 boquillas diferentes.
Conclusión
Según un informe de la Agencia Internacional de la Energía (AIE), Global EV Outlook 2021, publicado a finales de abril, el crecimiento del número de vehículos eléctricos vendidos seguirá aumentando a lo largo de esta década, por lo que el número de vehículos eléctricos matriculados en todo el mundo pasará de los 10 millones actuales a los 145 millones en 2030. Al mismo tiempo, según las estimaciones recién publicadas de la consultora Wood Mackenzie, el peso de las ventas de vehículos con motor de combustión interna irá reduciéndose hasta suponer menos del 50% sobre las ventas totales de vehículos en 2050.
Debido a la creciente popularidad de los vehículos eléctricos y autónomos, la industria de la automoción se está redefiniendo. Estos fabricantes están determinando, mediante ajustes, controles y estrategias, cuál es el enfoque que deben tomar para adaptarse de forma óptima a estas nuevas grandes tendencias. Al comprender las posibles aplicaciones de ensamblaje que hay disponibles en estos segmentos, los proveedores de primer y segundo nivel pueden posicionarse para ofrecer soluciones específicas que satisfagan la demanda de aplicaciones complejas, multidimensionales y cada vez más centradas en la estética.
Sobre el autor
Craig Birrittella es el gerente de desarrollo de negocios del mercado de la automoción para la línea de productos de soldadura y montaje de Branson en Emerson. Durante los más de 25 años que lleva trabajando en Emerson, Craig ha recibido una patente estadounidense por la adaptación de lentes para mejorar la energía láser y se ha centrado en diversas áreas técnicas adicionales, como la vibración, la vibración limpia y la soldadura por infrarrojos. Craig es licenciado en Ingeniería Mecánica por la Universidad Estatal de Nueva York, situada en Búfalo.