Optimización del concepto de embutición de un refuerzo capó
5 de junio de 2012
AutoForm es un software que ofrece soluciones para matricerías y troquelerías que permite simular, mediante el método de elementos finitos, toda la cadena de proceso. Con más de 200 empleados, AutoForm es el proveedor líder mundial de software de simulación de embutición de chapa metálica, cálculo de costes de herramienta y material, diseño de las herramientas y mejora y optimización del proceso. Los 20 principales fabricantes de automóviles y la mayoría de sus proveedores eligen AutoForm.
Matrici S.Coop es un referente en el desarrollo producto-proceso de todo tipo de piezas BIW (‘body in white’) en el sector del automóvil, con especial mención al ámbito de las piezas de piel (piezas exteriores). Dentro de éstas, Matrici colabora con los principales constructores automovilísticos para el desarrollo tanto del producto, como del proceso de obtención de la pieza que entraña más dificultad dentro de la carrocería, el lateral, siendo actualmente un referente mundial de calidad.
El objetivo principal de Matrici S.Coop ha sido reducir el adelgazamiento en zonas críticas a rotura mostradas de color naranja en la Figura 1 y aumentar el estiramiento en las zonas grises de dentro de pieza de la misma imagen. Para ello escogió algunos parámetros de geometría del embutidor, el coeficiente de fricción, las propiedades del material y los factores de restricción de los frenos definidos como variables que, según su larga experiencia en el conformado de este tipo de piezas, podían influir notablemente en el estiramiento de la chapa.
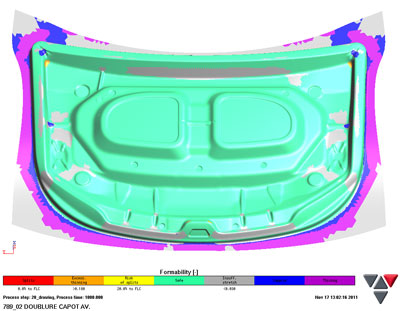
Figura 1. Resultados Formability de la simulación inicial.
Se realizó un primer análisis utilizando AutoForm Sigma en el que se calcularon varias simulaciones y se estudió la influencia de los parámetros del proceso: factores de restricción de los frenos, coeficiente de fricción y material. Se obtuvieron unos primeros resultados donde se detectaba una influencia importante del coeficiente de fricción en muchas zonas. Además los factores de restricción de los frenos también jugaban un papel importante. Por el contrario las propiedades del material no influían de forma significativa. La combinación de estas variables no consiguió mejorar el resultado de factibilidad de la pieza por lo que se definió un segundo cálculo incluyendo la geometría del embutidor y desestimando las propiedades del material.
En este segundo cálculo se observó que los factores de restricción de los frenos tenían una gran influencia sobre el resultado. Por el contrario el coeficiente de fricción y la geometría del embutidor no provocaban cambio alguno. Además se detectó que era importante optimizar los distintos tramos de frenos variables definidos en la simulación inicial. En este cálculo los resultados de factibilidad mejoraron notablemente. Aun así se decidió realizar un tercer y último cálculo para optimizar al máximo la calidad final de la pieza.
En este tercer cálculo se tuvieron en cuenta solamente los factores de restricción de los distintos tramos de freno variable. Mediante el análisis de las zonas críticas por falta o exceso de estiramiento se detectó una gran influencia de los factores de restricción de los distintos tramos del freno variable y se pudo cuantificar gracias a los diagramas de Pareto y tarta que muestra AutoForm Sigma.
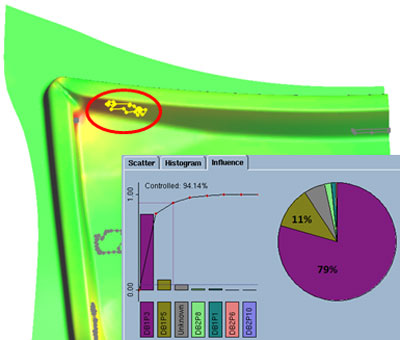
Finalmente se consiguió un resultado óptimo mediante la definición adecuada del concepto de frenos. Haciendo una comparativa entre la figura 1 y la figura 3 se pueden ver claramente las mejoras conseguidas.
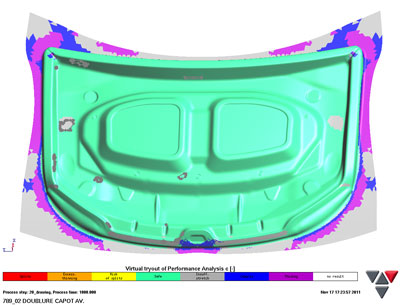
Recientemente esta pieza ha sido llevada a producción y se han comparado los resultados con los de AutoForm Sigma, verificando que los frenos ejercen una influencia importante en el estiramiento. Por el contrario, la modificación de otros parámetros como el radio de entrada de matriz y radio punzón de la geometría del embutidor no han ayudado a mejorar el resultado del mismo. Según el departamento de I+D de Matrici S.Coop: “El análisis estadístico de las variables diseño-proceso-material con AutoForm Sigma, que influyen en el conformado de chapa, es hoy en día, una herramienta fundamental en la resolución de piezas complejas y una ventaja añadida en el ciclo de vida del producto. Esta herramienta nos permite acortar el número de ciclos cálculo-error-modificación, en el inicio de desarrollo del producto, con la repercusión directa en el recorte de tiempos en las fases siguientes de diseño y fabricación”.