Procesado de materiales por tecnología láser
La tecnología láser permite concentrar altas potencias en áreas muy pequeñas. Utilizando esta característica se pueden conseguir soldaduras y tratamientos superficiales en piezas aportando una menor cantidad de calor al conjunto de la pieza. Esto evita que se produzcan deformaciones, ahorrando así operaciones posteriores a la soldadura o al tratamiento térmico. Los procesos láser son totalmente automáticos, garantizando así su reproducibilidad.
Soldadura por láser (‘Laser Welding’)
La técnica de soldadura láser consiste en la unión de dos piezas fundiendo una zona muy localizada de ambas piezas mediante un haz láser de alta potencia. La soldadura normalmente se realiza sin aporte de material. Esta técnica presenta grandes ventajas respecto a otras técnicas tradicionales de soldadura.
Se consiguen elevadas velocidades de soldadura y cordones muy finos, todo esto hace que las deformaciones y las tensiones creadas en las piezas sean mínimas en comparación con otras técnicas. Además la zona térmicamente afectada es inapreciable. Mediante la combinación de diversos parámetros del láser y el movimiento tridimensional del robot, se pueden realizar soldaduras en todo tipo de geometrías.
Los materiales habituales que se sueldan por láser son los aceros al carbono con bajo contenido en carbono, aceros inoxidables, titanio y varias aleaciones de base níquel.
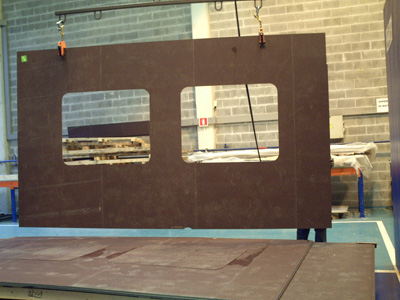
Los campos de aplicación de la soldadura láser son muy amplias, así los sectores como la automoción están incorporando estas técnicas de manera generalizada. La soldadura láser es una técnica realmente competitiva cuando se trata de piezas seriadas, debido a su grado de automatización, aunque es evidente que cualquier pieza de precisión se puede ver beneficiada con esta técnica, ya sean piezas mecanizadas, estampadas o piezas de chapa fina.
Así en los últimos tiempos sectores como el ferroviario están encontrando aplicaciones muy adecuadas para esta técnica. También se está incorporando en el sector naval, la aeronáutica y el alimentario. Se espera un abanico de aplicaciones vayan surgiendo en los próximos años gracias a estos sectores.
Temple por láser (‘Laser Hardening’)
El tratamiento térmico de endurecimiento superficial (temple) por láser es un proceso en el cual se utiliza la energía de un haz láser para producir un calentamiento localizado de la zona a tratar. El aporte de calor se concentra en la capa superficial, permaneciendo frío el interior de la pieza. Debido a la conducción de calor a la masa de la pieza, se alcanzan altas velocidades de enfriamiento al aire (temple), no siendo necesaria la utilización de líquidos refrigerantes.
Esta tecnología permite el tratamiento tanto de grandes piezas unitarias (por ejemplo matrices de estampación), como de largas series de piezas intermedias o pequeñas, en la gran mayoría de los aceros y fundiciones férricas.
El temple por láser es un proceso limpio y ecológico, no se requieren refrigerantes, con lo que se evitan oxidaciones en la pieza. El proceso además se realiza sin contacto de ningún elemento del sistema con la pieza. La profundidad de la capa tratada puede llegar hasta 1,5 milímetros. Esta técnica proporciona también una importante reducción frente a otras técnicas en la cantidad de calor aportada a la pieza, con lo que se minimizan las deformaciones y la posibilidad de aparición de grietas de temple. También se reducen e incluso se eliminan los procesos de mecanizado en duro y ajuste, esto hace que el temple por láser sea una técnica que reduce el coste de fabricación de la pieza. Todo el proceso se controla mediante un sistema pirométrico, lo que hace que sea totalmente reproducible.
El temple por láser se aplica principalmente en matrices y troqueles para conformado de chapa; cortantes de estas; cierres en moldes de inyección de plástico.; Raíles sometidos a desgaste, amarres de sujeción y correderas; engranajes y cremalleras; muelles; casquillos, bulones, tornillos; temples localizados en ejes de rotación, cuchillas y útiles de corte; utillajes de plegadoras; geometrías complejas con radios, cantos, bordes, superficies en relieve etc.; piezas mecanizadas y de gran precisión en general.
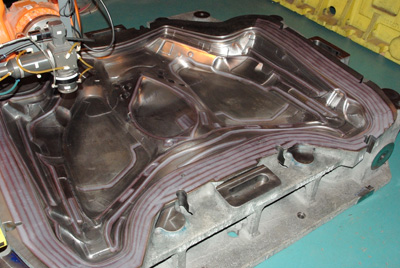
Recargue superficial por láser (‘Laser Cladding’)
La técnica de recargue superficial por láser consiste en la fusión de material, aportado, generalmente, en forma de polvo, mediante la energía suministrada por un haz láser. Este aporte de material puede realizarse sobre toda la superficie de la pieza, o bien sobre zonas concretas, que deban ser modificadas al haber sufrido daños, requieran un cambio de diseño, o bien porque se desee modificar alguna de sus características mejorando las propiedades contra el desgaste, la corrosión etc. El polvo es inyectado mediante una boquilla coaxial donde por el centro pasa el haz láser y dispone de varios puntos de inyección del polvo de aporte en la periferia.
Mediante la combinación de diversos parámetros del láser y el movimiento tridimensional del mismo, se pueden realizar los aportes de material siguiendo la geometría de la pieza o zona concreta a recargar de la misma.
La principal aplicación del ‘láser cladding’ está en la fabricación de piezas de alto valor que trabajan a desgaste. Esta técnica permite utilizar aceros más comunes y baratos en el núcleo de la pieza para luego aplicarle un recubrimiento de características mucho mejores para que aguante los requisitos demandados. Así por ejemplo se pueden aplicar recubrimientos en materiales como aceros de herramientas, aceros inoxidables de alta dureza, aleaciones con distintos porcentajes de carburos de tungsteno, aleaciones de tipo Stellite. Otro campo de aplicación es la reparación de piezas de alto valor añadido como errores en cotas de fabricación, desperfectos producidos en servicio, cambios de plano en prototipos, pieza desgastada etc. También está el aumento de vida en servicio de piezas mediante aporte de materiales de altas prestaciones, como resistentes a desgaste, corrosión, temperatura etc.
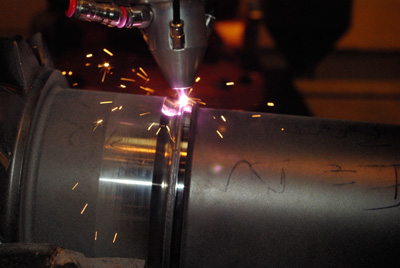
Este proceso proporciona recubrimientos entre 0,1 y varios milímetros de altura; unión metalúrgica entre recubrimiento y pieza con mínima aportación de calor sobre el material base. El material de aporte en polvo es arrastrado mediante gas inerte, con lo que hay ausencia total de corrosión en la zona tratada. El proceso ocasiona el mínimo daño en la estructura original de la pieza y mínima o nula deformación. En gran variedad de materiales de aporte (metálicos, carburos). La capa conseguida tiene una densidad muy elevada, sin poros y con estructuras metalúrgicas finas. Además ocasiona la fusión de solo una pequeña capa de la pieza y baja dilución del material de aporte en la pieza.
La aplicación de este proceso es óptima en campos como el petroquímico y el sector naval, en herramientas sometidas a desgaste, en intercambiadores de calor, husillos de bombas, matrices de forja, pistones; asientos de válvulas; sinfines para extrusión; rodillos de laminación; palas de agitadores; álabes de turbinas; ejes de rotación, cuchillas y útiles de corte; perforadoras; y moldes en la industria del vidrio.