La tecnología de servoaccionamiento distribuido y EtherCAT P facilitan la revisión del proceso de producción
Dirk Hansen, director de productos de Drive Technology de Beckhoff Automation
15/06/2023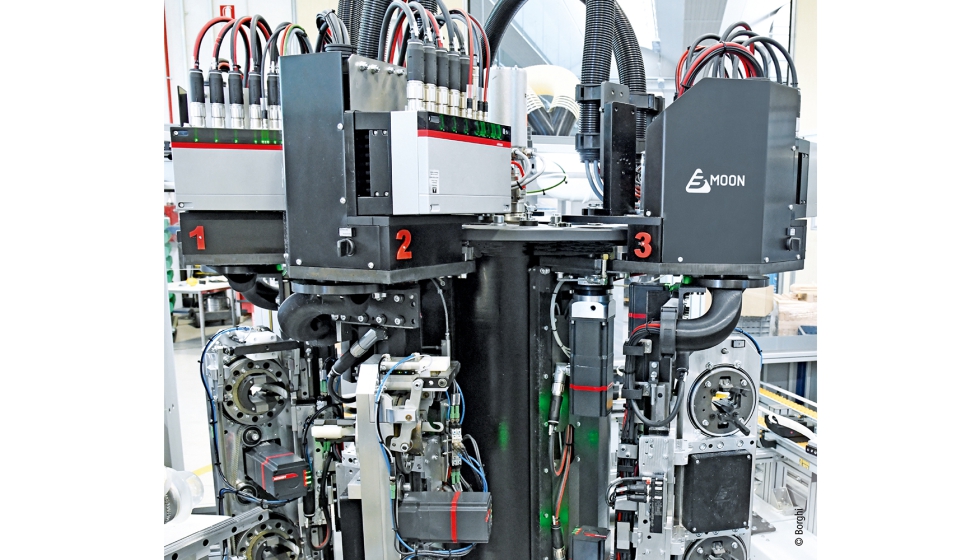
A primera vista, no son más que objetos cotidianos: escobas y cepillos de formas, materiales y colores muy diversos para uso doméstico e industrial. La gama de materiales y dimensiones es igual de amplia: desde pequeños cepillos de acero, polipropileno, crin de caballo o fibra de Tampico hasta grandes rodillos para vehículos de limpieza viaria. Esto hace necesaria una tecnología de producción de vanguardia para fabricar escobas, cepillos y fregonas al estilo de Borghi: de forma económica, en grandes volúmenes y con precisión y calidad.
Con sede en la localidad italiana de Castelfranco Emilia (Módena), las raíces de Borghi se remontan a 1948, lo que confiere a la empresa cerca de 75 años de experiencia en este segmento específico. En la actualidad, Borghi produce en varias filiales, entre ellas las de Brasil, China, India, Polonia y España. También tiene oficinas de venta en varias regiones de importancia estratégica, como Asia, Europa y EE. UU. “Ahora Borghi es un grupo internacional”, explica su presidente, Paolo Roversi. “Tenemos más de 250 empleados dedicados no solo a la producción de máquinas, sino también al montaje de armarios de control, a la fabricación de moldes y a otras muchas cosas. Detrás de los productos comercializados por una gran cantidad de grandes marcas de cepillos y escobas es frecuente encontrar el trabajo de una de nuestras máquinas”, continúa.
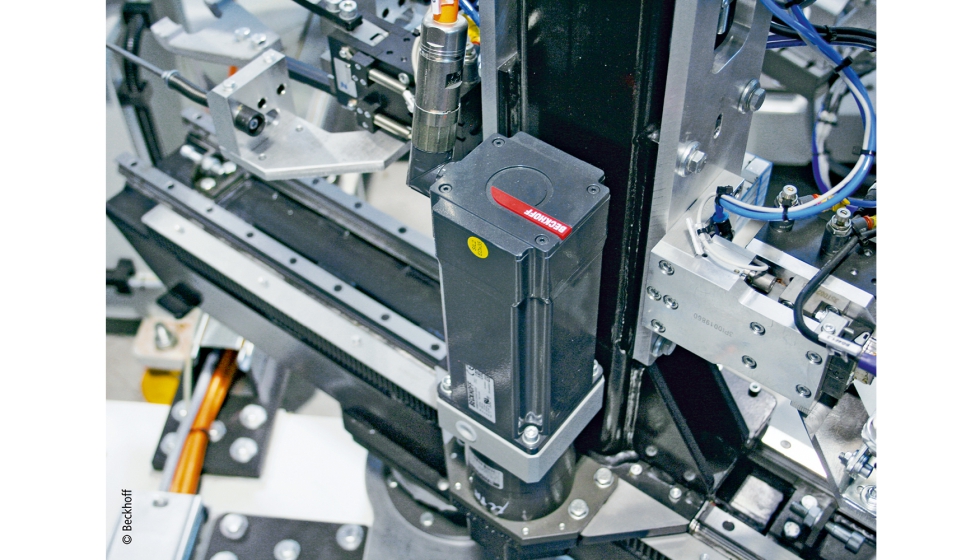
Producción de escobas con requisitos estrictos
A la hora de fabricar una escoba, el cepillo es el elemento más importante. Los cepillos están formados por varias hileras de fibras enhebradas en lo que se conoce como ‘listón’. No solo pueden tener geometrías completamente distintas, sino que también pueden estar hechos de materiales diferentes. “Por ejemplo, para procesar fibras sintéticas, naturales y metálicas en un solo sistema se necesita una enorme flexibilidad”, señala Paolo Roversi.
El ciclo clásico de producción de cepillos comienza con la alimentación de las placas base, que se envían a la estación de taladrado una vez insertadas. En la siguiente fase, los mechones se insertan en las placas perforadas antes de cortarlos a medida. El último paso consiste en apartar el producto acabado. Este último paso de mecanizado coincide casi siempre con la inserción de la siguiente placa base lista para un nuevo ciclo. “Durante la transición entre las distintas fases de procesamiento, los ejes de movimiento de las estaciones de trabajo tienen que detenerse brevemente para dejar que el producto semiacabado pase a la siguiente estación”, explica Paolo Roversi, señalando un importante cuello de botella en la productividad. Esta breve parada suele durar de 2 a 3 segundos, lo que puede no parecer mucho, pero aun así representa una pérdida de productividad de alrededor del 20% para un ciclo completo de unos 15 segundos. Al mismo tiempo, estas pausas forzadas encierran un enorme potencial de aumento de la productividad.
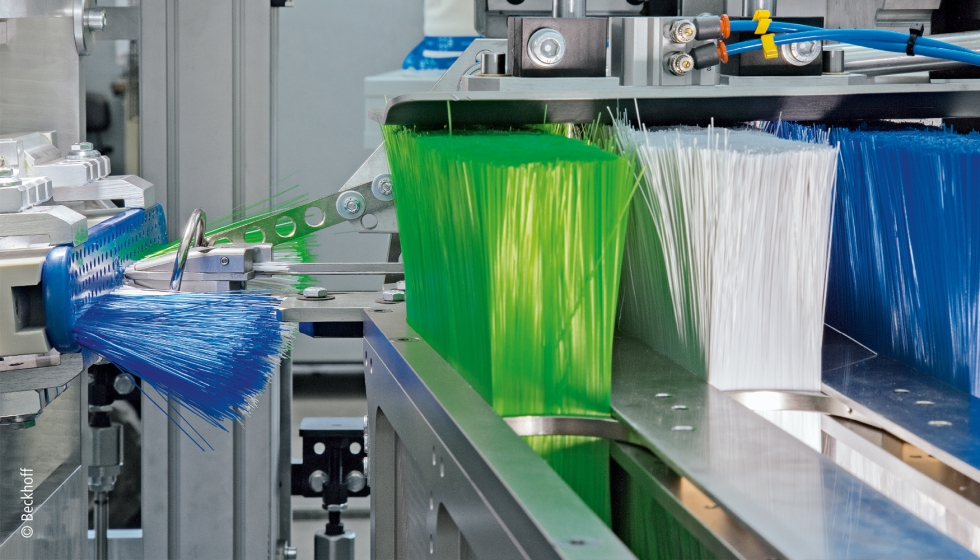
Eliminación de los tiempos de pausa mediante control de movimiento
Aquí es exactamente donde entró en juego el proyecto Moon de Borghi para optimizar el rendimiento y la eficacia de las máquinas. “Con nuestra nueva generación de máquinas, hemos querido romper con el esquema clásico de los ciclos de cambio de fase y desarrollar un concepto de máquina capaz de funcionar de forma continua”, señala Paolo Roversi, destacando el enfoque optimizado de la producción de cepillos. Esto requiere un diseño de máquina completamente diferente y un proveedor de automatización capaz de gestionar este alto nivel de complejidad con un enfoque seguro, fiable y determinista. Tras evaluar varios sistemas de automatización, se optó por Beckhoff. Fueron sus soluciones de automatización, como el servoaccionamiento distribuido AMP8000 y EtherCAT P, las que hicieron posible la implantación del concepto, recuerda Paolo Roversi.
Fue necesario rediseñar la mecánica a fondo para hacer posible el funcionamiento continuo de la máquina, con un elemento central compuesto por cuatro pequeñas torretas de mecanizado independientes que transfieren las placas de una fase de mecanizado a la siguiente de manera fluida. Cada torreta de mecanizado puede posicionarse de forma flexible mediante cinco servoaccionamientos para adaptarse a los formatos de las placas que se están procesando. Este enfoque requiere una tecnología de accionamiento compacta y potente en forma de servoaccionamientos distribuidos AMP8000 con electrónica de potencia integrada. Para conectar la alimentación y las comunicaciones, incluida la seguridad, se utiliza una sola línea EtherCAT P, lo cual no solo ahorra espacio en las torretas, sino que también reduce el peso.
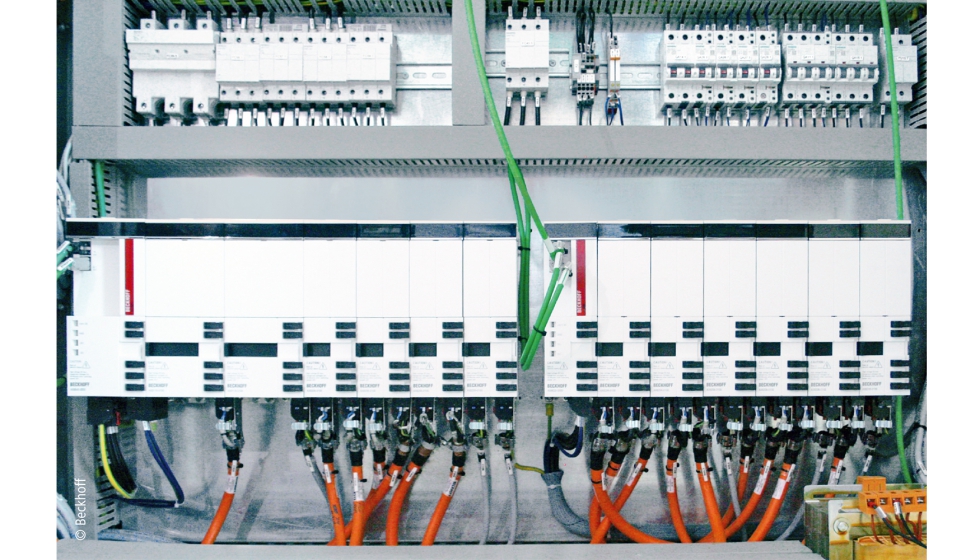
Optimización del espacio necesario en la máquina y el armario de control
El módulo de alimentación AMP8600 desempeña un papel clave en la alimentación distribuida: una fuente de alimentación con protección IP65 por torreta es suficiente para suministrar a sus cinco accionamientos energía y comunicación a través de EtherCAT P. El pequeño tamaño de los servoaccionamientos AMP8000, las reducidas dimensiones y la flexibilidad del módulo de alimentación distribuida, así como el mínimo trabajo de cableado necesario para EtherCAT P fueron esenciales para cumplir los requisitos de compacidad, rendimiento y fiabilidad de la máquina.
“Nunca estuvimos solos a la hora de implantar este innovador concepto de automatización”, recuerda Paolo Roversi. “El apoyo in situ de los expertos de Beckhoff lo hizo todo más fácil. Además, al gestionar con un único socio de proyecto todos los elementos de automatización, desde el panel de control hasta el accionamiento, nos ahorramos los problemas de compatibilidad habituales al trabajar con varios proveedores”.
El enfoque distribuido de manera coherente, con casi el 50 % de la electrónica de potencia ubicada directamente en la máquina, también tiene un efecto positivo en el espacio ocupado: a pesar de contener un total de 45 ejes, el armario de control de la máquina es muy compacto y ofrece espacio suficiente para el CX2040, los terminales EtherCAT y los servoaccionamientos adicionales de la serie AX8000. Paolo Roversi afirma entusiasmado: “Este enfoque ha supuesto un importante ahorro en costes, materiales, espacio y trabajo de instalación”.
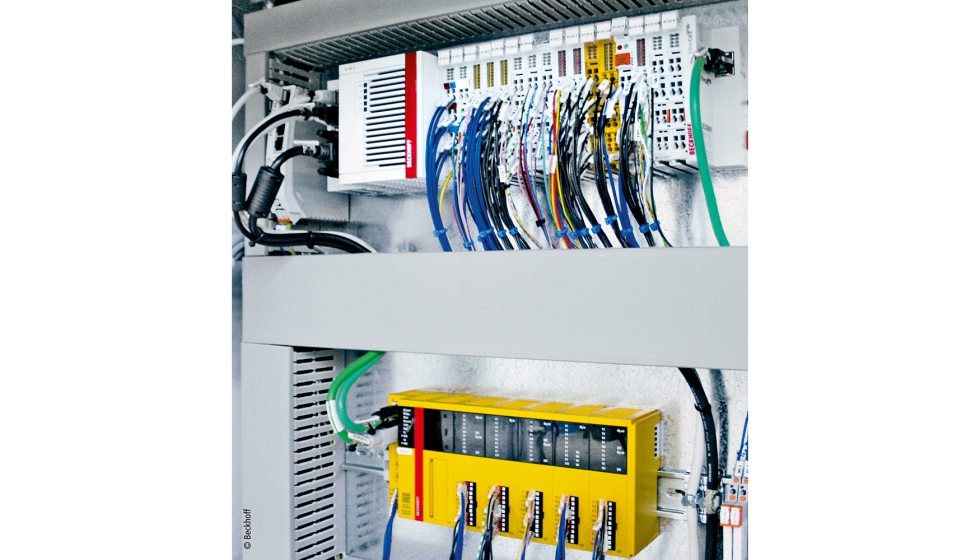
Preparados para la Industria 4.0 y el futuro
Hoy en día, todas las máquinas se desarrollan con Industria 4.0 de serie, con la correspondiente conectividad y tecnología de sensores. Según Paolo Roversi, Beckhoff también ha simplificado la programación en este sentido, ya que TwinCAT 3 utiliza de manera uniforme la nueva arquitectura estandarizada de Borghi: “Al mismo tiempo, queda mucho espacio para futuras ampliaciones, para el desarrollo de nuevos modelos y para la integración OT/IT. La tecnología de control basada en PC de Beckhoff ofrece la máxima escalabilidad para ello y permite una integración sencilla de varios sistemas de control y la HMI en un único hardware estándar”.