Un estudio busca mejorar la calidad del acabado en moldes
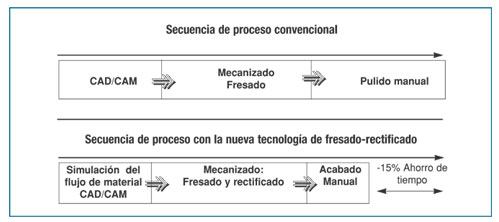
Configuración del sistema
Requerimientos de máquina
- Aspectos de seguridad: La máquina debe de estar equipada con cerramientos que sean capaces de soportar impactos equivalentes a la rotura de una muela de rectificar en operaciones de trabajo. Medio ambiente: en el proceso de rectificado, como es sabido, se generan vapores que deben de ser filtrados antes de dejarlos escapar a la atmósfera. Por lo cual el cierre debe de ser integral además de incluir un aspirador y filtro de vahos.
- Protección de elementos de máquina: los residuos que se generan en el proceso de rectificado pueden ir a parar a guías, husillos etc. de la máquina, por lo todos estos elementos deben de estar convenientemente protegidos.
- Precisión de posicionado y repetibilidad. Al ser una operación que se pretende sustituya a la de pulido manual, la precisión de posicionado de la máquina y la repetibilidad deben de ser lo más altas posibles, ya que el molde no recibe una operación posterior.
Requerimientos del proceso
En cuanto a técnicas de rectificado propiamente dichas, y tras realizar un estudio de las diferentes posibilidades existentes, se seleccionaron dos métodos diferentes:
- Rectificado con banda (similar a una lijadora). Para mecanizar con este sistema se debe de dotar a la máquina de un dispositivo que haga girar a la banda y ésta se desplace en contacto a la superficie a mecanizar. Se empleará en superficies relativamente planas y sin cambios bruscos de dirección (troqueles para capotas de automóviles, etc.)
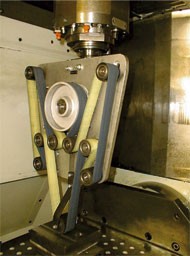
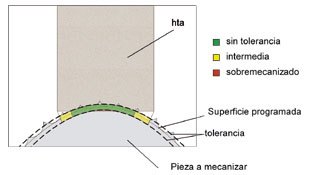
- Rectificado con muela: este caso es el más sencillo de aplicar. Para ello se dispone de una muela esférica en el porta pinzas de la máquina y se trabaja de forma análoga al fresado convencional. Este caso es aplicable a piezas o geometrías más complicadas.
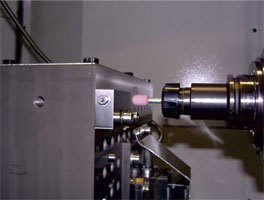
Este trabajo recoge los resultados alcanzados con el primero de los dispositivos, en una serie de ensayos sistemáticos para la evaluación de la aplicabilidad de esta tecnología, realizados sobre probetas en condiciones que tratan de simular las aplicables en una realidad industrial en términos de condiciones de proceso y herramientas utilizadas.
Ensayos con el dispositivo de rectificado por cinta
- Influencia del refrigerante: El rectificado con cinta se realiza en principio en seco, si bien, con el objetivo de analizar el potencial incremento en la vida de la cinta, se han realizado ensayos con refrigeración por aceite y mql (mezcla aire-aceite). El resultado es negativo en ambos casos: en el caso del aceite, provoca el deslizamiento entre la cinta y el rodillo guía, con lo que el mecanizado es inestable, provocando la aparición de marcas. En el caso del mql, tanto las fuerzas de corte como, sobre todo, la rugosidad se ven incrementadas. Esto es debido a que la película de aceite hace que la viruta (polvo) del rectificado se adhiera a la cinta, provocando un comportamiento indeseado.
Por ello el conjunto de ensayos que se describen a continuación se realizaron en seco.
- Influencia de las características de la cinta. Son varios los factores a tener en cuenta respecto a la configuración de la cinta:
- Tamaño de grano. Como se presenta en la figura 5 un menor tamaño de grano permite alcanzar una menor rugosidad. A menor tamaño, un mayor numero de granos actúa simultáneamente con lo que el resultado es más uniforme. Por otra parte, el espacio entre granos es inferior, lo que reduce la capacidad de arranque de material.
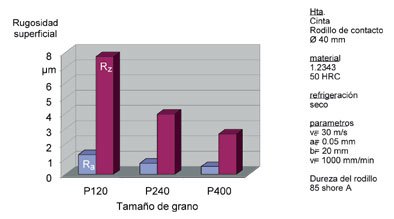
- Tipo de cinta. Se han comparado diferentes composiciones de cintas de CBN y óxido de aluminio. En la figura 6 se presentan los resultados comparativos entre las diferentes cintas. Hay que señalar que una única configuración provoca valores de rugosidad por encima del límite establecido.
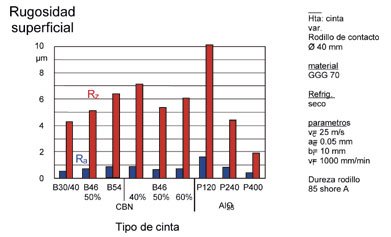
- Material y perfil del rodillo de contacto. Los materiales comparados han sido el aluminio y la goma. Las diferencias entre ambos son poco significativas, pero favorables a la goma. Debido a esta pequeña diferencia se ha seleccionado la goma, y con ella se han ensayado diferentes perfiles del rodillo, así como diferentes durezas de goma. La figura 7 presenta los resultados obtenidos con estas configuraciones.
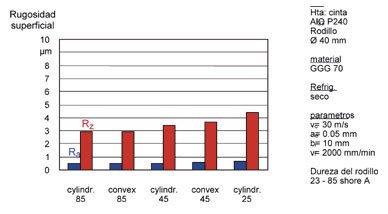
- Velocidad de corte. Si bien las diferencias no son significativas, se han ensayado velocidades entre 20 y 30 m/s, alcanzándose la rugosidad mínima con para 25 m/s. En los tres casos los valores se encuentran en torno a 1 micra Ra, y alrededor de 8 micras Rz.
- Profundidad de pasada. La rugosidad disminuye con el incremento de la profundidad de pasada. Esto es debido a que con una mayor profundidad de pasada el número de granos en contacto con la pieza es mayor, lo que redunda en un mejor acabado.
- Velocidad de avance. Se han ensayado velocidades en el rango entre 1000 y 3000 mm/min. En ese rango, los mejores resultados se han alcanzado con la velocidad más baja. La diferencia con la velocidad más alta es significativa, pero todos los ensayos cumplen holgadamente bajo el límite de 8 micras.
Estrategias de mecanizado conjuntas fresado-rectificado:
La aplicación del pulido por cinta en lugar del pulido manual puede permitir eliminar las últimas pasadas de acabado del fresado, de manera que el proceso total sea más productivo. Con este objetivo, se han estudiado diferentes secuencias de mecanizado, midiendo el resultado final en términos de rugosidad alcanza bajo los mismos límites de validez de este parámetro. En concreto, se han realizado ensayos para determinar la relación entre el paso de herramienta (paso entre pasadas contiguas) y el rectificado bajo diferentes condiciones: avance en la misma dirección que el de fresado, en dirección transversal, rectificado en varias pasadas que sumen la altura de la marca dejada por el fresado, o rectificado en una única pasada que cubra la altura de la marca de fresado. A continuación se presentan los resultados más significativos.
En cada una de las gráficas de las figuras 8 a 11 se presenta la rugosidad superficial alcanzada en las siguientes condiciones:
- La primera columna corresponde a la rugosidad tras el fresado.
- Las columnas segunda y tercera corresponden a la rugosidad alcanzada tras el rectificado en la misma dirección de avance que la de fresado. La columna 2 para el caso en que se realizan pasadas de rectificado de 5 micras hasta completar la altura de la marca dejada por el fresado, y en la columna 3, se elimina el sobrematerial de fresado en una única pasada de rectificado.
- Las columnas 4 y 5 recogen los resultados del rectificado en dirección de avance transversal a la de fresado.
De la misma forma que la pareja anterior, la columna 4 en varias pasadas de 5 micras y la 5 en una única pasada.
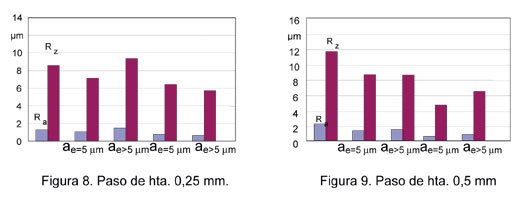
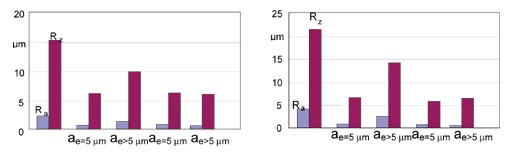
Otro resultado destacable debe obtenerse del análisis de la influencia de la anchura de paso entre pasadas de fresado. Puede apreciarse que la influencia no es excesivamente importante, resultado que también permite pensar en la reducción del número de trayectorias finales de fresado, aspecto que permite también reducir el tiempo de mecanizado total y con ello aumentar la productividad del proceso.
Conclusiones
Para alcanzar estos objetivos el trabajo realizado se ha materializado en los siguientes aspectos:
- El desarrollo a nivel de prototipo de un dispositivo para el rectificado con cinta, que se coloca en el cabezal de fresado sujetado en el propio portaherramientas, con lo que puede ser gestionado en la máquina como una herramienta más.
- El estudio de los parámetros principales de trabajo y su influencia en el resultado final del mecanizado en términos de rugosidad superficial alcanzada. En este sentido se han obtenido algunas interesantes conclusiones:
- La inconveniencia de la aplicación de refrigerante al proceso. Si bien la vida de la cinta se vería incrementada con el uso de refrigerante, se presentan problemas de inestabilidad, deslizamiento y embotamiento de la cinta que desaconsejan la aplicación de refrigerante.
- La influencia de la composición de la cinta. Comparando la cinta de CBN con la de óxido de aluminio, se ha podido apreciar una mayor estabilidad entre las diferentes configuraciones del CBN, si bien los mejores resultados (también los peores) se han alcanzado con cintas de óxido de aluminio. Por otra parte, la cinta de grano fino proporciona los mejores resultados en cuanto a rugosidad, si bien, como es lógico, su capacidad de arranque es inferior.
- La influencia del rodillo de contacto entre cinta y pieza. Se han ensayado diferentes perfiles (radios) del rodillo y diferentes durezas, sin apreciarse una influencia significativa.
- En cuanto a los parámetros de trabajo, la velocidad de corte no tiene una influencia crítica, la profundidad de pasada mejora la rugosidad al aumentar, y la velocidad de avance tiene el efecto contrario, aumenta la rugosidad al incrementarse.
- Finalmente se han analizado diferentes estrategias de fresado y rectificado posterior, debiendo destacar como resultado importante que la aplicación de este nuevo proceso permite reducir de manera significativa el tiempo de acabado con fresa, ya que el acabado final de la pieza no está directamente relacionado con el acabado obtenido en el fresado, sino que el rectificado posterior, en determinadas condiciones (pasada transversal a la de fresado) permite eliminar los errores del fresado de manera eficiente y productiva.