Extrusión de hoja espumada
Gneuss Kunststoffechnik01/12/2003
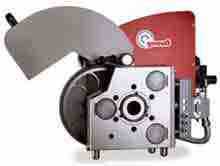
Para un peso dado por m2, la hoja espumada tiene propiedades mecánicas relativamente buenas, y excelentes propiedades de aislamiento, por ello el amplio uso de este material en las siguientes áreas:
- Tablero aislante (con retardantes de la llama) para aislado de edificación y otros usos.
- Envasado de alimentos (aquí, la combinación de buenas propiedades aislantes, peso ligero y resistencia, hacen de la hoja espumada un material de envasado extremadamente atractivo).
- Envasado de piezas frágiles y sensibles.
- Elemento de amortiguación, por ejemplo en la industria del mobiliario.
- Tablero trasero para carteles (gracias a su superficie suave, su resistencia y su peso ligero).
Hay tres procesos básicos empleados en la fabricación de hoja espumada, que presentan diferentes retos para el equipo de filtrado del fundido. Éstos son el agente espumante químico, el agente espumante inyectado en forma de gas-extrusora monohusillo y el agente espumante inyectado en forma de gas-extrusoras en tandem.
Agente espumante químico
En una segunda etapa, tras la extrusión, la hoja pasa por un horno y se calienta. Por encima de cierta temperatura, el agente espumante químico 'reacciona' de manera similar a una levadura en un bizcocho, y se crean muchos poros finos.
La compañía japonesa Sekisui desarrolló un proceso para la fabricación de hoja espumada con un agente espumante químico y varias compañías de todo el mundo hacen este producto con licencia.
La hoja fabricada con este proceso tiene una densidad relativamente alta (por encima de 400 kg/m_). Un ejemplo de aplicación para este producto es una capa de amortiguación dentro de los zapatos, para hacerlos más blandos al caminar, etc.
Una de las características más importantes de este proceso es que el extruido debe procesarse con una temperatura de fundido que es comparativamente cercana al punto de fusión del material, es decir, relativamente baja (alrededor de 120–130ºC). La temperatura de fundido debe mantenerse dentro de una ventana muy estrecha, si sobrepasa un cierto punto, entonces el gante espumante comenzará a reaccionar en la extrusora y será imposible extruir la hoja. Por tanto, no sólo es crítico el calentamiento del equipo de extrusión, sino que también debe tenerse cuidado de que la temperatura del fundido no aumente por un nivel de cizalla innecesario. También cualquier aumento de presión provocado por un sistema de filtrado es claramente un problema al respecto.
Los principales puntos críticos para el filtrado son los siguientes:
- El material es, a estas temperaturas relativamente bajas, altamente viscoso, por lo que hay que tener la seguridad de que la selección del tamaño del cambiador de filtros proporciona un área activa adecuada sin crear ningún espacio muerto en el canal de fluido del fundido.
- El cambiador de filtros no debe crear ningún aumento de presión durante el cambio. Un aumento de presión puede llevar a un aumento de la temperatura del fundido que, a su vez, puede causar que el agente espumante comience a reaccionar.
- El material está relativamente frío, por lo que el fluido del fundido no debería separarse y reunirse como en el caso de cambiadores de filtro de “cavidad dual”, ya que se pueden crear marcas de unión en la hoja.
En consecuencia, el sistema óptimo de filtrado del fundido para hoja espumada con agente espumante químico no debe ser un diseño de cavidad dual, no debe causar aumentos de presión y debe ser capaz de manipular un fundido altamente viscoso.
El cambiador de filtros de cavidad simple KSF de Gneuss, dispuesto para usarse con calentamiento/enfriamiento líquido, es el único sistema de proceso constante que puede usarse para esta aplicación, debido a las siguientes ventajas:
- No hay aumento de presión durante el cambio. Los cambios se inician automáticamente antes de que se alcance un nivel crítico de presión/cizalla.
- El sistema de sellado puede operar con la alta viscosidad.
- No hay áreas muertas en el sistema donde pueda acumularse el material.
Agente espumante inyectado en forma de gas. Extrusora mono-husillo
En la mayoría de los casos, la línea de extrusión se dispone no sólo con un intercambiador de filtros, sino que además incluye una bomba de fundido. En el caso de hoja de PS, se emplea normalmente una boquilla anular, y en el caso de una hoja de poliolefina, también puede emplearse una boquilla ‘coathanger’. Cuando es una plancha de aislamiento de PS para la industria de la construcción, se usa un aditivo retardante de la llama.
La hoja espumada de PS se emplea para el envasado de alimentos, y (con retardantes de llama) para aislamiento. La densidad de la hoja espumada de PS para envasado de alimentos es normalmente de 100 kg/m2. Para la plancha de aislamiento para la industria de la construcción, la densidad puede ser tan baja como 30 kg/m2. La hoja espumada de PS se destina también a aislamiento sonoro y a relleno de mobiliario, etc. En tales casos, la densidad es tan baja como 20 kg/m2. Algunas veces, la hoja espumada de PE se ha llegado a emplear para tapones de sellado para contenedores a vacío o presurizados, con una densidad de 400 kg/m2.
Una de las características más importantes de este proceso es que el extruido debe procesarse a una temperatura de fundido que es comparativamente cercana al punto de fusión del material, es decir, relativamente baja (alrededor de 120-130ºC). Por tanto, no sólo es crítico el calentamiento del equipo de extrusión, sino que también debe tenerse cuidado de que la temperatura del fundido no aumente por un nivel de cizalla innecesario.
Los puntos críticos para el filtrado son:
- El material es, a estas temperaturas relativamente bajas, altamente viscoso, por lo que hay que tener la seguridad de que la selección del tamaño del cambiador de filtros proporciona un área activa adecuada sin crear ningún espacio muerto en el canal de fluido del fundido.
- El cambiador de filtros no debe crear ningún aumento de presión durante el cambio, ya que podría llevar a un incremento de la temperatura del fundido que, a su vez, puede causar que el agente espumante comience a reaccionar.
- El material está relativamente frío, por lo que el fluido del fundido no debería separarse y reunirse como en el caso de cambiadores de filtro de “cavidad dual”, ya que se pueden crear marcas de unión en la hoja.
Hay que tener la seguridad de que la selección del tamaño del cambiador de filtros proporciona un área activa adecuada
El sistema óptimo de filtrado del fundido para hoja espumada es la inyección de gas y la extrusora mono-husillo. El sistema de filtrado no debe tener un diseño de cavidad dual, no debe causar aumentos de presión durante los cambios y debe ser capaz de manipular un fundido altamente viscoso.
El cambiador de filtros de cavidad simple KSF de Gneuss, dispuesto para usarse con calentamiento/enfriamiento líquido es el único sistema de proceso constante que puede usarse para esta aplicación, debido a las siguientes características:
- No hay aumento de presión durante el cambio. Los cambios se inician automáticamente antes de que se alcance un nivel crítico de presión/cizalla.
- El sistema de sellado puede operar con al alta viscosidad.
- No hay áreas muertas en el sistema donde pueda acumularse el material.
Agente espumante inyectado en forma de gas. Extrusoras en tandem
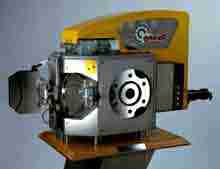
En el caso de hoja de PS, se emplea normalmente una boquilla anular, en una hoja de poliolefina, también puede usarse una boquilla ‘coathanger’, mientras que en planchas de aislamiento de PS para la industria de la construcción, se utiliza un aditivo retardante de la llama.
Para la extrusión de hoja espumada con una línea de extrusión en tandem, las etapas de procesado “plastificación con inyección de gas” y “enfriamiento” están detenidas, lo que da un nivel de flexibilidad mejorado, a cambio sin embargo de un coste de inversión más alto en comparación con una línea de extrusión de una etapa. Si el cambiador de filtros se coloca al final de la extrusora primera, entonces el filtrado se lleva a cabo cuando la viscosidad del fundido es muy baja, lo que significa que se necesita un área de filtrado relativamente pequeña. La temperatura del fundido no es tan crítica en esta etapa, ya que el fundido se enfriará posteriormente en la extrusora secundaria. Como el fundido pasa del filtro a la extrusora secundaria para su enfriamiento y descarga, podría parecer que los requerimientos en la estabilidad del proceso del filtro de fundido en esta posición son menos críticos, pero no es así.
Ésta es la línea de extrusión más ampliamente extendida para hoja espumada, y en este tipo de línea se fabrica hoja espumada con una amplia gama de densidades (de 20 a 400 kg/m2) para envasado de alimentos, plancha de aislamiento, tablero trasero para carteles, etc.
Los puntos críticos para el filtrado
- La viscosidad del material es, con el gas añadido y a esta temperatura relativamente alta, extremadamente baja, con la precisión del fundido a menudo alrededor de 300 bar, por lo que el cambiador de filtros debe ser a prueba de fugas.
- El cambiador de filtros no debe crear ninguna variación de presión durante su operación. El gas se inyecta, controlado a un cierto volumen en el fundido. Si la presión del fundido varía, entonces la estructura de la espuma no puede mantenerse uniforme. Una estructura uniforme de espuma es de una importancia extrema en lo que respecta a hoja espumada para envasado de alimentos.
- En el punto donde el material se filtra, entre la extrusora primera y segunda, el gas ha sido añadido, la viscosidad del fundido es muy baja y la presión del fundido bastante alta. Claramente, si el sistema de filtrado del fundido libera súbitamente la presión del fundido, entonces hay una expansión súbita y violenta del fundido que tiene varios efectos negativos: es un riesgo respecto a la seguridad en tanto que el personal corre el riesgo de quemarse, pero también en cuanto que hay una liberación súbita de gas que en la mayoría de los casos es inflamable, aumentando así el riesgo de un incendio. Si hay una liberación súbita de la presión, esto significa que la presión del fundido se ve afectada y la distribución del gas no es uniforme. Por ello, el uso de un cambiador de filtros discontinuo convencional en este punto puede suponer un gran peligro.
En el caso de planchas aislantes se usan aditivos retardantes de la llama. Éstos son muy corrosivos para el acero y, por tanto, el acero debe tener la mejor protección contra la corrosión. La temperatura del fundido debe mantenerse dentro de un intervalo muy estrecho (alrededor de un máximo de 220ºC) para prevenir que el retardante de la llama “trabaje” el acero. Las propiedades corrosivas del retardante de la llama aumentan drásticamente con cualquier aumento en la temperatura del fundido. Del mismo modo, este retardante es más agresivo cuando está en contacto con el oxígeno del aire. El sistema de filtración del fundido debe estar completamente encapsulado de la llama en una línea de extrusión en tandem.
En cuanto a la importancia de la presión constante en la extrusión de hoja espumada con gas, éste, como ya se ha explicado, se inyecta en el polímero fundido. Esto significa que la bomba de medida está inyectando el gas contra una cierta presión del fundido. Si esta presión del fundido varía, entonces el sistema de control para la bomba de medida lucha por inyectar el gas a un nivel uniforme. Si la presión del fundido es constante, dentro de ± 2 bar, entonces el gas puede inyectarse uniformemente. Si la distribución del gas no es uniforme, entonces la estructura de la espuma es del mismo modo no-uniforme. Esto significa que la estructura de celda no es constante, la densidad de la espuma varía.
La estructura de espuma constante, uniforme, es importante. En la plancha de aislamiento, porque ésta debe cumplir ciertos criterios respecto a las propiedades mecánicas, superficiales y de estabilidad dimensional. Si la estructura de la espuma no es uniforme, la plancha aislante puede mostrar marcas en la superficie, alabearse y distorsionarse, y pueden sufrir las propiedades mecánicas.
En la hoja para termoconformado, si la estructura de la espuma no es uniforme, la hoja no se comportará consistentemente durante el termoconformado. Éste es un problema muy serio, ya que esta hoja espumada se fabrica normalmente en rollos, y estos rollos se almacenan varios días, para permitir que los gases atmosféricos difundan a las celdas abiertas de la hoja. Si la estructura de la espuma cambia mientras está en el rollo, es posible que esto se note durante el termoconformado varios días más tarde y esto conduzca a que todo el rollo se desperdicie. La mayoría de fabricantes de hoja termoconformada fabrican la hoja en varios colores diferentes y mantienen un mínimo absoluto de rollos de cada color en stock. Si durante el termoconformado se establece que uno o dos rollos no pueden termoconformarse debido a cambios en la estructura de la espuma, esto puede causar grandes problemas.
Sistemas de filtrado de fundido de Gneuss para hoja espumada
El cambiador de filtros SF consta básicamente de tres piezas: un bloque de entrada, un bloque de salida y un disco rotatorio. El disco rotatorio contiene un número de cavidades arriñonadas, separadas por costillas finas. Estas cavidades tienen la función de platos rompedores de fluido en cambiadores de filtros convencionales, pero están dispuestas en forma de anillo alrededor del disco rotatorio. Las pantallas de malla tejida de alambre (el medio filtrante real) están ajustadas a estas cavidades. El disco se instala con su eje excéntrico al eje del canal del fundido, y el disco rota en el seno del fundido.
El canal del fluido está optimizado reológicamente, no hay espacios muertos donde el fluido de material pueda estancarse y degradar. La presión del fundido se supervisa antes y después de la unidad e, inmediatamente, cuando tiene lugar el aumento en el diferencial de la presión de sólo 1 bar mayor del punto fijado en el sistema de control, el disco rotatorio se indexa en aproximadamente un ángulo de 1º, movido por medio de un cilindro neumático. Esto significa que una sección extremadamente pequeña (aproximadamente 1%) del área contaminada de la pantalla se mueve, y la reemplaza un área pequeña de área de pantalla limpia. Esto no es suficiente para causar una variación en la presión. Si el diferencial de presión no cae ligeramente, el disco continúa moviéndose un pequeño paso tras otro hasta que el diferencial en la presión cae al punto fijado. Si la presión cae al punto fijado, entonces la unidad esperará por un tiempo fijado, más largo, antes de hacer otro paso indexado, a menos que el diferencial en la presión aumente de nuevo. De este modo, el diferencial en la presión puede mantenerse constante indefinidamente, el prerrequisito crucial para una estructura de espuma consistente.
El movimiento en pasos gradual del disco en intervalos de aproximadamente 1º significa que el gas espumante se libera de una forma segura y controlada. El tamaño relativamente pequeño de las cavidades conduce a una cantidad relativamente pequeña de espumado del material en el disco rotatorio.
El personal operario es avisado por una alarma para cambiar los paquetes de filtros. Normalmente, esto se hace después de que el sistema haya utilizado automáticamente tres paquetes de filtros. Este cambio se lleva a cabo sin ninguna perturbación del proceso, ya que las líneas de hoja espumada con el SF nunca necesitan parar o ajustarse por perturbaciones debidas a cambios de filtros.
El disco rotatorio y las superficies de los bloques están hechos con una superficie extremadamente dura, acero tratado y limado hasta unas tolerancias extremadamente finas. Los dos bloques se mantienen juntos usando pernos pre-cargado. El disco puede rotar suavemente entre los dos bloques, con una capa muy fina de polímero como lubricante, y este sistema de sellado evita fugas tanto de gas como de polímero. Este sistema de sellado tiene la ventaja añadida de no crear espacios muertos, y el sistema es casi a prueba de desgaste. Es normal que las unidades SF en hoja espumada puedan funcionar durante 75.000 horas de operación antes de mostrar signos de desgaste. Gneuss ofrece un servicio de revisión, gracias a su diseño pueden reacondicionarse un número de veces casi infinito. Gneuss oferta, además, la misma garantía contra fugas en unidades reacondicionadas que para unidades nuevas.
Cuando el disco rotatorio original de Gneuss, la gama SF, se introdujo en el mercado al poco de fundarse la compañía en 1983, la industria de hoja espumada fue una de las primeras en sacar partido de las ventajas de este sistema: a prueba de fugas de gas, operación a presión constante. Desde entonces se han suministrado más de 400 cambiadores de filtros SF para hoja espumada.
Área de aplicación para el cambiador de filtros SF
- Las líneas de extrusión de PS en tandem, al final de la extrusora primera.
- Sistema de filtrado de fundido completamente automático de presión y receso constantes y autolimpiables, RSFgenius. El RSFgenius representa un desarrollo posterior del cambiador SF e incluye las siguientes características adicionales:
- El disco rotatorio está completamente encapsulado. Este diseño asegura que todas las piezas en contracto con el fundido están separadas de influencias ambientales (por ejemplo oxígeno).
- Los paquetes de filtros se limpian automáticamente. Poco antes de la re-entrada en el canal del fundido, el área contaminada de la pantalla se limpia. La torta sucia se quita mediante un sistema de retro-lavado segmental de alta presión. Se elimina una cantidad definida de fundido filtrado en el bloque de salida, y se “dispara” a través del área de la pantalla con un diferencial alto de presión (30ª 80 bar), tras lo cual se descarga al exterior. Esta presión de limpieza está preseleccionada y se controla automáticamente. Con cada”disparo”, se limpia sólo un pequeño segmento (aproximadamente un 1% del área de la pantalla), por lo que para cada “disparo” hay disponible un impulso definido alto para la limpieza.
Área de aplicación para el cambiador de filtros RSFgenius
- Las líneas de extrusión de PS, PE y PET en tandem, al final de la extrusión primera.
- Líneas de hoja espumada de PE con agente espumante químico.
- La línea de extrusión de una sola etapa para PS y PE con bomba de engranajes corriente abajo.
Gracias al diseño completamente encapsulado del sistema, se mejora la resistencia a la corrosión respecto al cambiador SF. La característica de auto-limpieza automática es especialmente atractiva en los casos donde el uso del paquete de filtros es alto debido a un nivel de contaminación relativamente alto. Incluso con cargas de contaminación relativamente altas, los paquetes de filtros pueden aguantar uno o dos meses. El recambio de los paquetes de filtros se lleva a cabo sin perturbaciones en el proceso, por lo que las líneas de hoja espumada equipadas con RSFgenius nunca necesitan parar o ajustarse por perturbaciones debidas a cambios de pantallas.
Aunque el RSFgenius se introdujo en 1998, ya se ha posicionado en el área de hoja espumada, con quince unidades ya en operación.
Sistema de filtrado de fundido de proceso constante KSF
El cambiador de filtros KSF representa una versión muy simplificada del cambiador SF, basado en el principio básico del disco rotatorio dentro de dos bloques. Sin embargo, en el caso del cambiador KSF, el disco se monta sobre platos rompedores de fluido redondos desmontables y se mueve automáticamente en pasos de _ cavidad cada vez. No se puede conseguir la estabilidad absoluta de presión de los cambiadores SF y RSFgenius con el KSF, pero su estabilidad de proceso, junto con algunas ventajas especiales hacen de este sistema el único sistema de filtrado de fundido de proceso constante disponible para ciertos casos especiales.
Área aplicación para el cambiador de filtros KSF
Las líneas de extrusión de una etapa de PS y PE, de fundido “frío” (temperatura del fundido <140ºC), sin bomba de fundido montada corriente abajo. Un problema con el filtrado en la espuma “fría” es que si se separa el fluido del fundido, es muy difícil volver a reunirlo.
El KSF se usa en casos especiales donde se emplean sistemas de una etapa. El coste relativamente bajo de las líneas de extrusión de una etapa frente a las líneas en tandem ha visto el crecimiento en el interés y en la demanda para la unidad KSF. Desde que se introdujo en 1995 se han suministrado aproximadamente 50 unidades para estas aplicaciones.
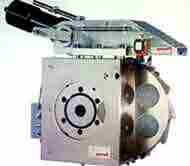
Requerimiento del área de filtrado: filtrado en las fases “caliente” y “fría”
En la fase “fría”, la viscosidad del material no sólo es mucho más alta, sino que no hay normalmente oportunidad de reducir la temperatura del fundido tras el filtrado: debe evitarse un aumento en la temperatura del fundido por cizalla, causada por el cambiador de filtros (80 bar máximo de diferencial en la presión). Por tanto, debe usarse un cambiador de filtros correspondientemente más grande.
En la fase “caliente”, donde el cambiador se monta al final de la extrusora primera, la situación es completamente diferente: la viscosidad es mucho más baja, la temperatura del fundido más alta y la función principal de la extrusora secundaria corriente abajo del cambiador es disminuir la temperatura del fundido. Correspondiente, se puede operar a velocidades de producción relativamente altas con una caída de presión baja. En este punto, recomendamos una caída de presión máxima de alrededor de 50 bar.