La fabricación ligereza es una tecnología clave en el camino hacia un mundo neutro en emisiones de CO2
Engel celebra su jornada dedicada a la fabricación ligera 'Lightweight Future Day'
La fabricación ligera desempeña un papel fundamental en la obtención de los objetivos de protección del clima. El Lightweight Future Day 2021, organizado por el fabricante de maquinaria y proveedor de soluciones de sistemas Engel en mayo, dejó claro una vez más que la ligereza es una tecnología clave en el camino hacia un mundo neutro en emisiones de CO2, y que los termoplásticos desempeñarán un papel importante en este sentido.
Expertos de todas las industrias usuarias importantes, como la automoción, la fabricación de bicicletas y motocicletas, la aeronáutica y la industria del deporte y el ocio, así como representantes de importantes institutos de investigación presentaron soluciones de vanguardia en el Lightweight Future Day 2021. Más de 500 asistentes obtuvieron conocimientos de un total de 15 ponencias que presentaban todas las facetas de los desarrollos y tendencias actuales de la ligereza, y participaron en los debates. A cada ponencia le siguió una sesión de preguntas y respuestas moderada por Norbert Müller, jefe de desarrollo de maquinaria inteligente en Engel, y Bastian Brenken, director general de Composites United.
Debido a la actual pandemia del coronavirus, el Lightweight Future Day se celebró este año de forma virtual. Los participantes procedían principalmente de Europa, con especial atención a Alemania, el Reino Unido y los países del Benelux, pero “hubo incluso algunos expertos en materiales ligeros de Estados Unidos que no se desanimaron por la hora de la conferencia, que para ellos era temprano”, como señala Christian Wolfsberger, Director de Desarrollo Comercial de Materiales Ligeros de Engel y organizador del Lightweight Future Day.
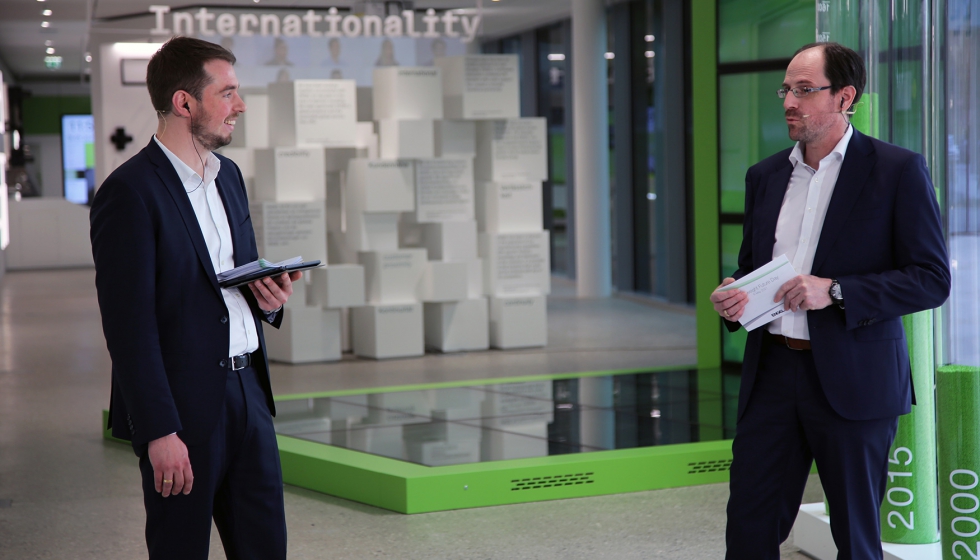
Norbert Müller, jefe de Desarrollo de máquinas inteligentes en Engel (derecha) y Bastian Brenken, director general de Composites United e.V. (izquierda) guiaron a los participantes a través del programa y moderaron las sesiones de preguntas y respuestas.
Los compuestos termoplásticos aceleran la producción en serie
Los termoplásticos y la tecnología de producción correspondiente facilitan la producción en serie de grandes volúmenes, como explicó Michael Thienel, experto en el desarrollo de soluciones de puertas del proveedor de la industria automovilística Brose, en la primera ponencia: “Con una mezcla inteligente de materiales, hemos conseguido desarrollar un innovador sistema de puertas que establece nuevos estándares en cuanto a ligereza, funcionalidad y diseño flexible. En comparación con los productos heredados a base de acero, ahorramos hasta cinco kilogramos, es decir, un 40% del peso, manteniendo la misma seguridad en caso de colisión. Además, hemos conseguido un grosor de pared de sólo 0,6 milímetros”. Su empresa ha suministrado anualmente a Ford un millón de módulos de puerta fabricados con termoplásticos reforzados con fibra (lámina termoplástica) desde 2018. En la actualidad, Brose ya está en el umbral de la producción en serie con la siguiente generación de módulos de puerta: el nuevo elemento estructural sustituye a otros elementos de puerta basados en el acero. En total, esto ahorra un kilo más de peso por puerta de coche, y el sistema es también más rentable como el elemento de acero.
Muchas de las ponencias del Lightweight Future Day demuestran que el camino hacia la ligereza más avanzada suele pasar por la transformación de termoplásticos. FACC, especialista en componentes ligeros para la fabricación de aviones, también apuesta por los termoplásticos. La empresa se centra especialmente en el futuro mercado de la 'Movilidad Aérea Urbana' las cabinas aéreas tripuladas y los drones no tripulados en el tráfico aéreo urbano, como explicó René Adam, director de Investigación y Tecnología de la empresa. Se esperan volúmenes de producción de entre 5.000 y 30.000 componentes al año. Se trata de cifras muy superiores a las de la producción de piezas para aviones de mayor tamaño, que ronda las 1.000 unidades al año. Debido a sus largos tiempos de curado, los termoestables utilizados principalmente en la fabricación de aviones hasta la fecha no podrían cumplir los cortos tiempos de ciclo requeridos aquí.
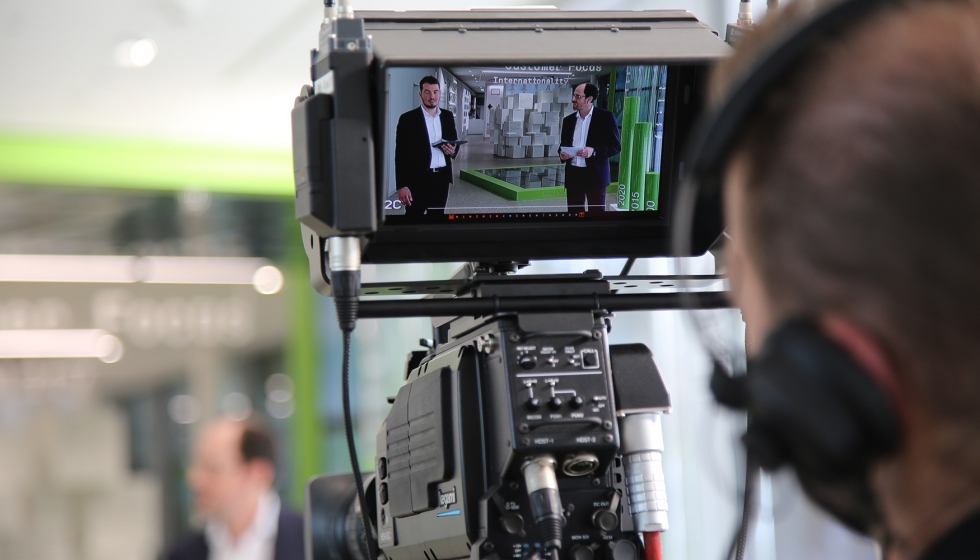
En 2022, se espera que el evento tenga lugar como una solución híbrida que permita la participación tanto presencial como virtual.
La capacidad de reciclaje hace que el peso ligero sea más sostenible
Sin embargo, es probable que los termoplásticos también desempeñen un papel más importante en la fabricación tradicional de aviones en el futuro, ya que la industria de la aviación se ha fijado el objetivo de lograr la neutralidad climática para 2050. René Adam: “Los procesos de producción de la industria aeronáutica cambiarán totalmente. La fundición híbrida, la unión en frío y el conformado rápido aún no se han convertido en procesos estándar. Tenemos que mejorar considerablemente las estructuras de costes y los ciclos de producción. Estas son las razones que nos llevan a la FACC a creer que los termoplásticos serán el material clave para los plásticos compuestos de fibra en la industria de la aviación de cara al futuro”.
Otro tema fue común en muchas de las presentaciones: la excelente reciclabilidad de los termoplásticos en comparación con la reciclabilidad más limitada de los materiales compuestos de fibra termoestables. Georg Käsmeier, socio director de Forward Engineering, señaló que la UE está tratando de convertir la economía circular en la norma como parte del Green Deal. “Ahora es el momento de pasar del pensamiento lineal al circular en el desarrollo de productos y de tener en cuenta el proceso de reciclaje ya en la fase de diseño del producto”, instó a los participantes en la conferencia. Como parte de un estudio, su empresa comparó la huella de CO2 en la producción de un pedal de freno basado en termoplásticos primarios, materiales de base biológica y termoplásticos reciclados. El potencial de ahorro de CO2 del uso de termoplásticos con contenido reciclado resultó ser significativo. “Creemos que los materiales termoplásticos tienen un gran potencial en términos de sostenibilidad. Para aprovecharlo, es necesario establecer procesos de reciclaje a escala industrial. Pero vemos que la industria está abordando este reto”, dijo Käsmeier.
Piezas ligeras termoplásticas de una sola vez
Debido a la creciente importancia de los termoplásticos en la fabricación ligera, Engel –firma representada por Roegele– ha invertido mucho en tecnologías y sistemas para la transformación de termoplásticos en los últimos años. “Somos la primera empresa del mundo que puede ofrecer un proceso totalmente integrado que comienza con una célula de colocación de cinta UD y termina con un componente ligero termoplástico totalmente consolidado y sobremoldeado”, indicó Paul Zwicklhuber, ingeniero de desarrollo de Composite Processing en Engel, en su presentación. La célula de colocación de cintas se basa en el principio de pick-and-place. Esto significa que las cintas pueden depositarse y soldarse por puntos a intervalos de tres a cuatro segundos. Dado que la calidad de la pila depende en gran medida de la precisión del posicionamiento de la cinta, Engel ha equipado la célula de colocación con un sistema de medición con tecnología de cámaras de alta resolución. A continuación hay una unidad de consolidación que consolida los tejidos de cinta termoplástica en el ciclo de moldeo por inyección. La consolidación puede integrarse perfectamente en el proceso global, lo que aumenta considerablemente la eficiencia en la producción de soluciones de cinta a medida.
Engel Organomelt es el núcleo del proceso integrado. Aquí se forman y funcionalizan preimpregnados compuestos de fibra termoplástica como cintas UD y láminas orgánicas. Los elementos funcionales, como las nervaduras de refuerzo o los elementos de ensamblaje, pueden sobremoldearse inmediatamente después del termoformado utilizando un termoplástico del grupo de materiales de la matriz. Esto permite un proceso de producción altamente integrado y totalmente automatizado, al tiempo que el proceso simplifica el reciclaje de las piezas al final de su vida útil. El proceso Organomelt también se utiliza en la producción de módulos de puertas de Brose.
El caso de uso de la empresa suiza Svismold demostró que los materiales ligeros también pueden ofrecer ventajas aunque el peso no sea un problema. La empresa consiguió convencer a un fabricante de tablas de surf para que sustituyera las anteriores aletas termoestables por una aleta fabricada con compuestos de fibra termoplástica basados en cintas UD. Resultó que la nueva aleta ofrecía unas características de precisión de la dirección inigualables. Una de las razones es que los flujos de fuerza calculados con precisión en la pieza pueden reproducirse exactamente en ella, ya que el uso de UD-tape garantiza la alineación de las fibras, al tiempo que se reducen los costes de producción. La tabla de surf con la nueva aleta recibió una entusiasta acogida por parte de la comunidad de surfistas.