El CNC asegura el ritmo de producción
Si el número de unidades que se produce es del orden de cientos de miles, la disponibilidad de la máquina y cada segundo de tiempo productivo son fundamentales desde el punto de vista económico. GE Fanuc optimiza la producción de grandes series por medio de rápidos y fiables sistemas de control de CNC, que proporcionan funciones especiales integradas.
Contribuyendo a optimizar la producción en serie se encuentran, por ejemplo, los sistemas de control de gama alta de las Series 30i/31i/32i de GE Fanuc. Están equipados con los más avanzados procesadores de alta velocidad, un bus interno de alta velocidad y un potente sistema de control de servos. Además de rápidos ciclos de control servo y de cabezal, la alta resolución de los encoders de posición, que ofrecen hasta 16 millones de pulsos por revolución, es muy ventajosa. Especialmente práctico es asimismo el PLC integrado con su propio procesador de alta velocidad, que alcanza velocidades de ejecución de hasta 25 ns/paso para programas de contactos, pudiendo ejecutar hasta tres de ellos simultáneamente. Los dispositivos periféricos que forman parte del proceso completo, como cambiadores de herramientas, alimentadores de piezas, etc., pueden así manejarse rápida y fluidamente.
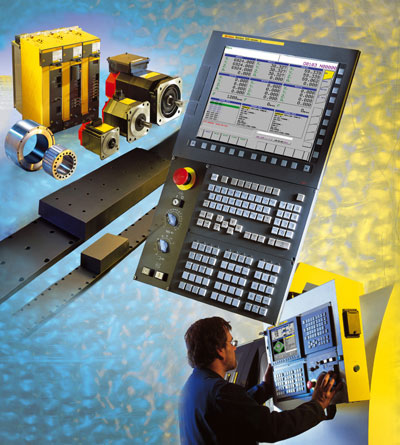
Los procesos automatizados ejercen generalmente una importante función en la producción en masa. El requisito básico para ello es la disposición de una estructura de comunicación, a la que las máquinas se encuentren conectadas a través de sus controles de CNC. Los sistemas de red, como Ethernet, y la transferencia de datos vía FL-net, Profibus y otros sistemas de bus permiten disponer de toda la información necesaria cuando se requiera.
Como Edgar Weiter, experto en aplicaciones de máquinas complejas de GE Fanuc Automation CNC Europe, sabe por experiencia: "Cargar los datos, ponerla en marcha y dejar que trabaje por sí sola - así es como ven los directores de producción la fabricación automatizada ideal. La carga de las piezas, la comprobación de los componentes, el re-mecanizado y la retirada de las piezas han experimentado un enorme cambio en los últimos años. Con frecuencia son sistemas de robots, que han evolucionado para hacerse más eficaces y asequibles, los responsables de estos cambios." Sensores y sistemas de visión aseguran que los robots actúen con gran rapidez y precisión. Pueden, por ejemplo, tomar piezas brutas no clasificadas, clasificarlas, suministrárselas a la máquina e incluso separar las piezas incorrectas.
Para todas estas soluciones de automatización, la comunicación con el CNC es esencial. GE Fanuc posee una prolongada experiencia en este campo. Por un lado, la producción de Fanuc en Japón, a los pies de Mount Fuji, está altamente automatizada; por otro, Fanuc es también uno de los principales fabricantes de robots. Si bien los robots tienen sus propios sistemas de control, pueden comunicarse con el CNC de la máquina herramienta a través de un simple enlace de bus de campo. Conectando un cable y cargando el software, el usuario crea un enlace directo, que incluso puede establecerse tras la puesta en marcha de la máquina herramienta. Además, para ello no es necesario efectuar grandes cambios ni en el software de la máquina ni en el de los robots.
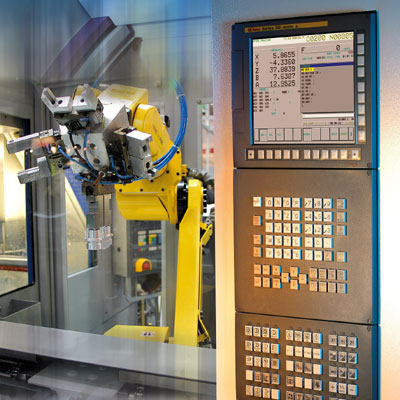
Pero no sólo es el entorno de las máquinas el que debe diseñarse para la producción a gran escala, ya que también las propias máquinas contribuyen en gran medida al éxito de la producción. El sistema de control de CNC, de hecho el cerebro de la máquina, es responsable de que la máquina se mueva de forma que, incluso cientos de miles de veces, un componente igual y de alto valor cualitativo sea producido en el menor tiempo posible. Con este fin, GE Fanuc, líder del mercado mundial en tecnología de CNC, ha desarrollado funciones especiales que el usuario final puede aplicar según lo requiera.
Una de dichas funciones se encuentra integrada en el sistema de control de CNC de la Serie 30i. El "Aprendizaje de la Pieza" permite al sistema de control aprender de los errores. Edgar Weiter describe esta función del siguiente modo: "Con el Aprendizaje de la Pieza se pueden optimizar los movimientos axiales para cada componente durante el fresado o el torneado y, con cierta dependencia de la velocidad, aumentar la precisión. El contorno de la pieza y los movimientos axiales son captados por el sistema de medición y transmitidos al CNC, que optimiza sus ajustes consecuentemente para generar en la siguiente pieza movimientos optimizados, con menores errores de vibración y mayor precisión.“
El Aprendizaje de la Pieza no puede, por supuesto, transgredir las leyes de la física, como por ejemplo la relación de interdependencia entre velocidad y precisión. Pero tan solo compensando los errores de origen térmico y las imprecisiones causadas mecánicamente, la función puede lograr en la mayoría de los casos un claro aumento de la velocidad con la misma precisión. Y, como ya se ha mencionado: durante la producción en masa, cada segundo cuenta.
Para iniciar el aprendizaje, el usuario debe primeramente hacer funcionar la máquina con dos o tres piezas para obtener los datos necesarios para la comparación. El sistema de control de CNC optimiza la totalidad del proceso automáticamente y corrige los valores incorrectos ocasionados por el desgaste, la elevación de la temperatura y otros factores que habitualmente se dan durante la producción de grandes series.
Los límites de esta función dependen en cierta medida de la memoria principal del sistema de control de CNC, ya que el sistema de control debe ser capaz de almacenar todos los valores medidos y compararlos con los que ya se habían recogido. Por esta razón, para poder utilizar el Aprendizaje de la Pieza, un programa codificado no puede ser ilimitadamente largo y complejo. Actualmente es posible una longitud de programa de dos minutos, y este valor irá aumentando gradualmente gracias a las constantes mejoras en el hardware y a la cada vez mayor capacidad de almacenamiento.
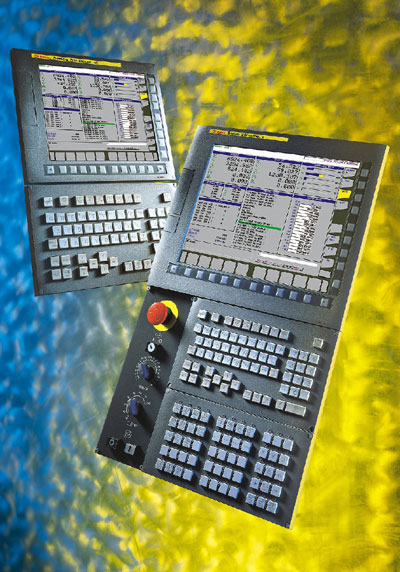
La función denominada Selección de las Condiciones de Mecanizado se utiliza también para optimizar la relación entre la velocidad de mecanizado y la precisión, aunque no a través de los valores medidos del componente, ni tampoco automáticamente. En este caso, se trata principalmente de un simple sistema con diez niveles seleccionables, que van desde el de más alta precisión (a baja velocidad) al de más alta velocidad (con menor precisión). Dependiendo del tipo de mecanizado, desde el pre-desbaste al acabado fino, el usuario puede seleccionar el nivel apropiado y rectificarlo en cualquier momento pulsando una tecla. Incluso durante la producción en serie, vale la pena invertir algo de tiempo y ejecutar varios ciclos a modo de prueba. Los ajustes óptimos determinados de este modo recompensan tanto más cuanto mayor es el número de piezas de la serie.
Procesamiento de datos binarios: el camino más corto
En la fabricación de pistones de motores y componentes similares, durante la que se repiten frecuentemente subprogramas, los sistemas de control de CNC de GE Fanuc pueden también programarse directamente utilizando datos binarios. Esto tiene la ventaja de que no es necesario trasladar los datos al sistema de control, pudiendo ser directamente canalizados a los ejes. De este modo se pueden lograr tiempos de interpolación muy reducidos y altas velocidades de mecanizado. Edgar Weiter pone un ejemplo: "En Francia equipamos una máquina para el fresado de cigüeñales con este procesamiento de datos binarios. En esta aplicación, tanto los muñones centrales, como los muñones excéntricos son fresados durante una revolución. Esto se realiza mediante una cuchilla de fresado que se mueve hacia atrás y hacia adelante, dependiendo del contorno. Los datos para el proceso de fresado se guardan en formato binario, ya que el procedimiento se repite para cada cigüeñal. Esto representa un claro ahorro del tiempo con respecto al uso del subprograma, para el que los datos ASCII deben ser leídos y compilados." El usuario tiene todavía posibilidad de introducir algunos datos de corrección, aunque el programa en sí es procesado en formato binario.
`Hasta ahora, un inconveniente del procesamiento de datos binarios era el gran volumen de datos de los programas de máquina, debido a que cada segmento de interpolación debe ser descrito. Sin embargo, gracias a la cada vez mayor capacidad de almacenamiento disponible, el área de aplicación de este tipo de programación se está extendiendo.

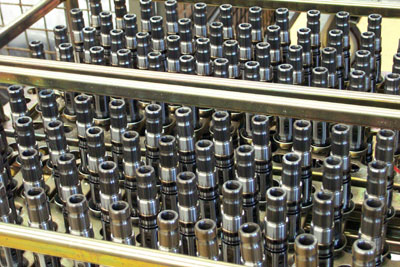
El empleo de datos binarios es también interesante con relación a la función Operación con Tabla de Trayectoria, que facilita la interpolación y sincronización de diferentes ejes y simplifica la programación de operaciones de múltiples canales. Los subprogramas convencionales para tales aplicaciones consisten en varios bloques, en los que el tiempo y la velocidad a la que se debe interpolar una determinada posición está definida para todos los ejes. Con la Operación con Tabla de Trayectoria, por el contrario, para cada eje individual se dispone un subprograma que es función de una magnitud o variable de control. Edgar Weiter explica: "En principio, es como una tabla en la que la primera columna contiene la variable de control, en función de la cual vienen dadas todas las demás. Esta variable de control es normalmente un tiempo, pero también puede ser una posición del cabezal o del eje. El programador instruye entonces las posiciones de los ejes secuencialmente para cada eje individual en función de esa variable de control."
Estos subprogramas individuales se almacenan en el sistema de control o, posteriormente, pueden ser procesados directamente desde un PC, en el que se compilan como datos binarios. Edgar Weiter señala su relación con la producción en serie: "La Operación con Tabla de Trayectoria se utiliza con máquinas complejas para aplicaciones donde se utilizan varios ejes, normalmente distribuidos en diferentes canales. La función opera a través de los diferentes canales, ya que éstos pueden disponerse de acuerdo a una línea de tiempo común. Estas máquinas se usan principalmente en la producción en masa, ya que conllevan un extenso trabajo de programación. Mediante la Operación con Tabla de Trayectoria, este esfuerzo se reduce considerablemente."
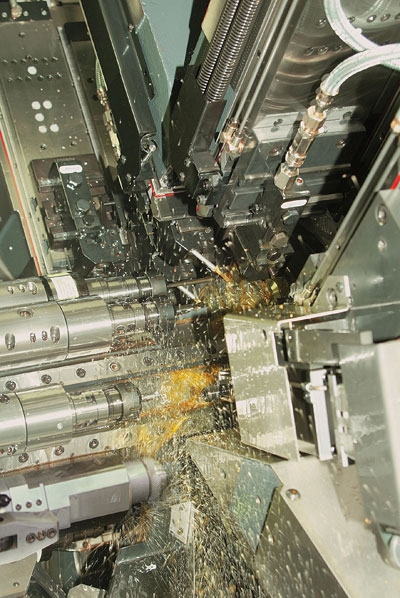
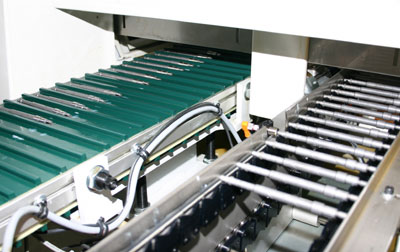