El concepto ECO2 (ecológico y económico) es uno de los objetivos de la fabricación por mecanizado
Refrigeración criogénica para operaciones de mecanizado de alto valor añadido
En este artículo se presenta la tecnología de mecanizado criogénico con CO2, los sistemas de regulación e inyección desarrollados y algunos casos de aplicación con resultados exitosos.
El concepto ECO2 (ecológico y económico) es una realidad a perseguir hoy en día en muchos sectores industriales, entre ellos el de la fabricación por mecanizado. El empleo de técnicas avanzadas de refrigeración criogénica durante las operaciones de mecanizado es una alternativa interesante a la hora de avanzar hacia el denominado ‘green manufacturing’. El empleo de fluidos criogénicos, como el nitrógeno líquido o el dióxido de carbono líquido, se traduce en una menor temperatura en la zona de corte, un aumento del rendimiento productivo y una mayor limpieza en la zona de trabajo. En el caso del dióxido de carbono, las ventajas se multiplican, siendo éste un producto que puede ser almacenado a temperatura ambiente y tiene un precio relativamente bajo, lo que industrialmente lo hace atractivo. Además, el dióxido de carbono de uso industrial se obtiene de un proceso primario al cual se le da un segundo uso, reutilizándolo en lugar de eliminarlo como residuo. En sectores y aplicaciones donde el coste de la herramienta es elevado, su vida útil es reducida y la integridad superficial es crítica, el uso de esta tecnología se presenta como alternativa de gran interés.
1. Introducción
De cara a aumentar la productividad del mecanizado y teniendo en cuenta la necesidad de mantener y/o mejorar la integridad superficial tras el proceso, es habitual el empleo de lubricantes y refrigerantes durante el proceso de mecanizado. Estos lubricantes/refrigerantes, conocidos como fluidos de corte, generalmente son emulsiones derivadas del petróleo. Una de las apuestas de la Unión Europea en cuanto a sus objetivos ‘20-20-20’ es reducir los gases de efecto invernadero en un 20%, conseguir que el consumo de energía proveniente de fuentes renovables sea del 20% y aumentar un 20% la eficiencia energética [1]. De ahí que la fabricación limpia o ‘green manufacturing’ sea cada vez más importante en el sector del mecanizado.
Consecuentemente, dentro del ámbito de la refrigeración de los procesos de mecanizado, han surgido diferentes alternativas a la taladrina como puede ser el mecanizado con lubricantes sólidos, taladrina a alta presión, mínima cantidad de lubricante (MQL), cold- gun o la refrigeración criogénica. La problemática de algunas de estas alternativas es que son para casos y operaciones concretas; por lo general pueden aumentar los gastos de producción o requerir una alta inversión inicial; y finalmente siguen teniendo cierto impacto ambiental. En cambio con la refrigeración criogénica se utiliza una tecnología limpia, segura y medioambientalmente respetuosa y se consigue un aumento del ratio de material eliminado (MRR) sin provocar mayor desgaste en la herramienta [2].
Los fluidos criogénicos que normalmente se utilizan para inyectar en la zona de corte son el nitrógeno líquido (LN2) o dióxido de carbono líquido (CO2). Estos fluidos son utilizados desde hace años en otros sectores por otras compañías. Concretamente Articube, cuya matriz es una empresa vitoriana de matricería, utiliza el CO2 para refrigeración de platos y copas, Cool-Clean (Minnneapolis) utiliza hielo seco de CO2 para la limpieza de fachadas o el Grupo Horeca (Málaga) ofrece utensilios para cocinar con LN2.
En cuanto al mecanizado, las razones por las cuales se utiliza el LN2 como fluido de corte es debido a que es un gas inerte que se encuentra en grandes cantidades en la atmósfera, tiene una alta capacidad refrigerante (-196 °C es la temperatura en estado líquido) y no se necesitan sistemas de aspiración adicionales a los comúnmente utilizados en máquinas herramienta. Los ensayos realizados por diversos autores muestran que el LN2 posee propiedades lubricantes. Esta propiedad fue intuida en Hong et al. 2002 donde se asoció a la presión estática de inyección, pero no fue hasta cinco años más tarde, en Hong et al. 2007, donde se demostró que dicha presión producía una película hidrodinámica entre la herramienta-viruta-pieza que se traducía en coeficientes de fricción más bajos [3] [4]. Siguiendo estos pasos, en Klocke et al. 2012 y Krammer et al. 2013, se vio que en comparación con la taladrina a presión se consiguen mecanizar hasta 900 metros más en el caso del fresado de titanio debido a dicha película lubricante. Su aparición se justificó mediante la teoría del ‘Vapour bubble’ por la cual la presión del vapor en la zona de corte se opone a la presión estática de inyección formando una burbuja que actuaba como film protector [5] [6]. Hoy en día son varios los grandes fabricantes internacionales de máquina herramienta que tratan de incorporar esta tecnología en su cartera de productos, como por ejemplo Okuma America Corporation en colaboración con 5ME, que introduce el LN2 por el interior del husillo de la máquina para refrigerar una herramienta de alto avance, tal y como se muestra en la figura 1.
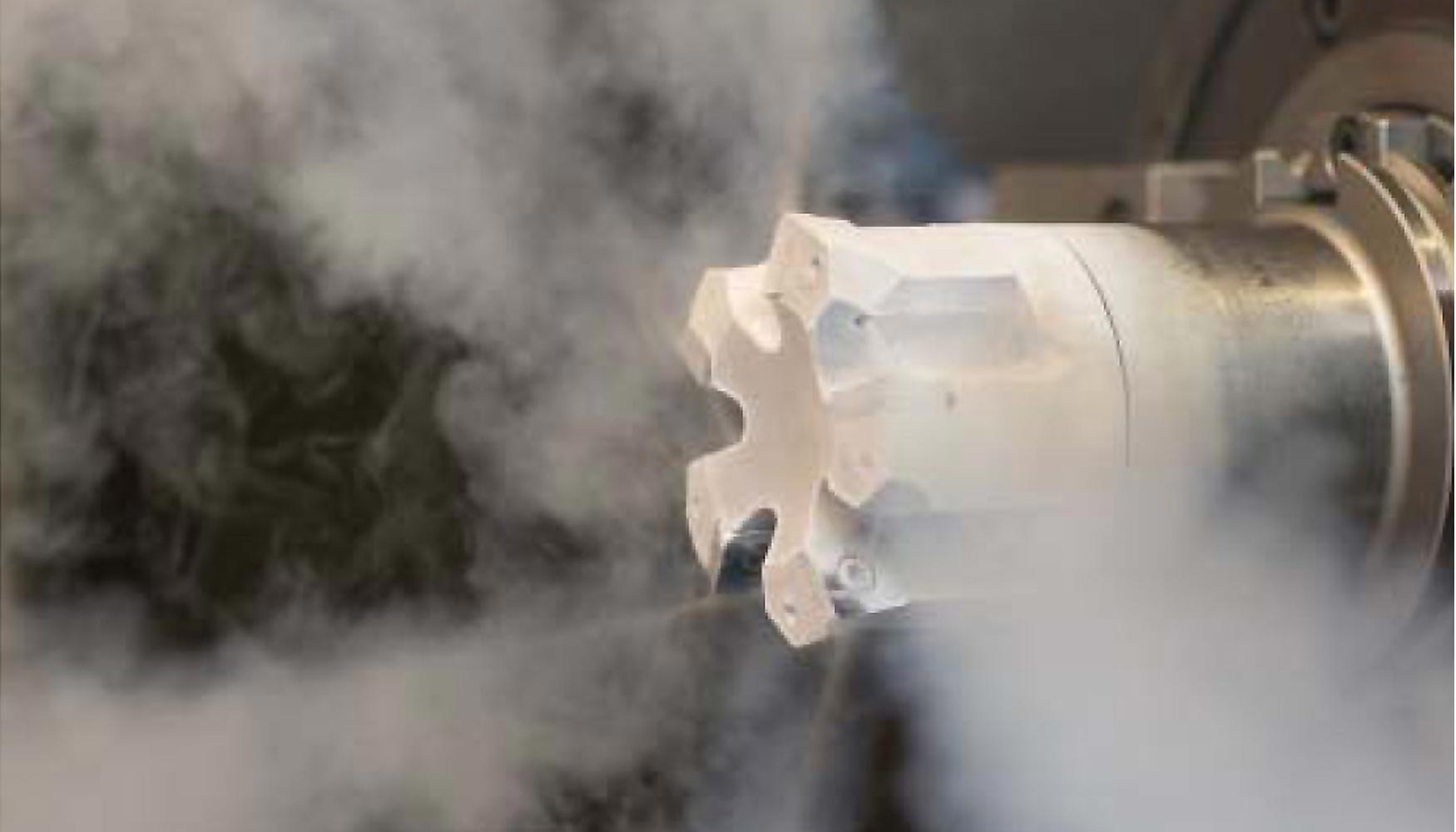
Figura 1. Refrigeración criogénica por el interior de una herramienta (5ME y Okuma).
Por otra parte, un aspecto a considerar es que el LN2 es de difícil almacenamiento debido a que está en continua ebullición, por lo que en los recipientes y tanques se genera una sobrepresión que una vez alcanza un determinado valor acciona una válvula de seguridad que permite evacuar nitrógeno en forma de escape para evitar cualquier riesgo por sobrepresión. En cambio el CO2, aunque tiene una capacidad refrigerante menor (-78 °C en estado líquido), puede ser almacenado a temperatura ambiente en recipientes presurizados a 55-60 bares y además se puede disolver en aceites cuando está en estado supercrítico. En esta línea, en Supekar et al. 2012 se demuestra la efectividad del CO2 en estado supercrítico (scCO2) y su combinación con micropartículas de aceite de soja para el torneado de Ti- 6Al-4V [7]. Otro estudio similar fue el realizado en Stephenson et al. 2014 [8] donde se obtuvo que al tornear con dicha técnica Ti-6Al-4V se obtenían también mayores ratios de MRR o tasas de arranque. Cabe destacar que el CO2 que se utiliza para la refrigeración criogénica es obtenido de un proceso primario, es decir, se le da un segundo uso en lugar de ser expulsado a la atmósfera directamente como residuo. De este modo se conserva el escaso impacto medioambiental inherente a los sistemas criogénicos basados en LN2.
En el sector industrial, las tecnologías limpias de mecanizado han incrementado su valor y presencia en torno a un 10% anual desde 2007, hasta alcanzar un valor total de 2 trillones de euros en la actualidad [1]. Sin embargo, no es hasta la EMO de 2011 cuando se da un paso real al frente y el grupo alemán MAG decide lanzar una línea completa de máquinas-herramienta con refrigeración criogénica mediante LN2, con las cuales mostraba su posible aplicación en el fresado de los bloques de los motores en el sector automovilístico. Además de sus máquinas ‘All in one’ y con el fin de ampliar su abanico de clientes, MAG también lanzó un portaherramientas capaz de soportar las temperaturas criogénicas producidas por el LN2 en su interior y así lograr una adaptación de las máquinas ya existentes a su tecnología.
Después de esa demostración de MAG, la realidad es que los derroteros de la refrigeración criogénica desde un punto de vista industrial y práctico han ido por otros caminos, en concreto con el uso de CO2 como gas refrigerante. Incluso MAG que en 2011 presentaba en la EMO su línea criogénica de LN2 ese mismo año ya trabajaba en el desarrollo de husillos para adaptar sus máquinas a la utilización de CO2 . Prueba de ello es su patente US2011/0166692 A1 en la que registra un método para refrigeración y lubricación de la zona de corte mediante un husillo en el que por su interior se combina CO2 y MQL en un mismo conducto para su posterior pulverización en los orificios de fresas con refrigeración interna [9].
Uno de los primeros en apostar por el CO2 como fluido de corte fue la empresa norteamericana Cool-Clean, la cual fue fundada en 2001 y cuya actividad principal era la limpieza de superficies mediante chorros con micropartículas de hielo seco. En 2008 patenta una boquilla en la que se combina micropartículas de aceite con CO2 , consiguiendo así un ‘cryoMQL’ para aplicación externa en procesos de corte. La característica principal de esta boquilla es que las micropartículas de aceite formadas en el interior de la boquilla recorren las paredes externas de ésta por efecto coanda hasta alcanzar su extremo donde por electrospraying se combinan con el CO2 [10]. Cool-Clean, a la vista de la línea marcada por MAG, dos meses después de la EMO 2011 patenta su propio sistema de inyección regulable de CO2 para máquinas-herramienta [11]. A raíz de este hito, Cool-Clean lanza su línea de refrigeración criogénica ‘Chil Aire’ en la cual se ofrecen tres gamas diferentes del sistema patentado.
Otra de las empresas que ha apostado por la refrigeración criogénica es la alemana Rother technologies. Esta empresa, con más de treinta años especializada en ofrecer soluciones adaptadas al cliente en cuanto a lubricantes, ensamblajes de máquinas, herramientas, etc., ha centrado el eje de su estrategia comercial en la refrigeración criogénica con CO2. En junio 2011 patenta su primer sistema de inyección ‘cryoMQL’ [12], es decir, cuatro meses antes que Cool-Clean lo hiciera. Este sistema diseñado por Rother principalmente se basa en hacer independiente la producción del aerosol del sistema de inyección de éste. Así se pueden tener con un mismo sistema varias líneas de ‘cryoMQL’ independientes. En el caso de Rother, la línea de refrigeración criogénica se denomina ‘Aerosol Master’ y consta al igual que Cool-Clean de tres gamas.
En el caso de multinacionales, como Starrag y Walter, en lugar de ofrecer una solución integral al igual que Rother, lo que hacen es aunar esfuerzos para lograr ofrecer al consumidor un servicio completo de refrigeración criogénica con el fin de no quedarse fuera del mercado. Como resultado de esta unión, en la EMO 2013 presentaron una fresadora con refrigeración criogénica mediante CO2 con la que obtuvieron el premio ‘MM Award for Innovation’ al mecanizar palas de turbina con dicha fresadora. Actualmente, Walter se encuentra en fase de lanzamiento de su línea ‘Walter Cryo-tec’. Con esta línea es posible utilizar el CO2, aire o MQL en modo ‘stand alone’ o combinar el CO2 con cualquiera de las otras dos opciones.
En este trabajo se recogen los avances realizados por la UPV/EHU y Tecnalia, en colaboración con la Universidad de León, en lo referente a mecanizado criogénico. Se presentan los sistemas de regulación e inyección utilizados en la puesta a punto de la tecnología y se presentan tres casos de éxito para aplicaciones en operaciones de mecanizado comunes como fresado, taladrado y torneado.
2. Mecanizado criogénico: sistemas de inyección
En los últimos años desde la UPV/EHU y Tecnalia se lleva trabajando en el desarrollo de una tecnología de refrigeración criogénica propia con el fin de ser capaces de aplicarla a operaciones habituales de mecanizado como el fresado, taladrado y torneado. Para ello, a la vista del análisis realizado y con el objetivo claro de reducir al máximo la inversión inicial a la hora de aplicarlo en el entorno industrial, principalmente se ha apostado por la refrigeración criogénica con CO2 frente al LN2. La idea ha sido acercar esta tecnología a las empresas del entorno, tanto a fabricantes de máquina-herramienta como a usuarios mecanizadores.
En primer lugar, para la inyección del CO2 en la zona de corte se necesita de un sistema regulador que evite la formación de hielo seco y consecuentemente el taponamiento del circuito. Esta formación de hielo seco se debe a que el CO2 se encuentra almacenado a una presión de 55-60 bares y si se expande a presión atmosférica sin ningún tipo de regulación, como se puede observar en el diagrama de fases de la figura 2, en el proceso de expansión pasaría por la ‘zona de sólido’ provocando la formación de hielo seco. Es decir, el CO2 en estado líquido antes de evaporarse se solidifica si su presión no es regulada en el interior del circuito.
En el marco de este trabajo se ha adaptado un sistema de regulación propio de CO2 para poder trabajar con fluidos criogénicos, en concreto con CO2, en operaciones de mecanizado. Este sistema mantiene en todo el circuito una presión de 8-12 bares para evitar que la presión del CO2 esté por debajo del punto triple (5,11 bares y -56,4 °C). Consecuentemente, la expansión final se produce en la salida del sistema de inyección, donde el CO2 líquido ya sí pasa a CO2 gas y partículas sólidas, alcanzando su temperatura más baja (- 78 °C). Este sistema es común a cualquier aplicación en la que se desee refrigerar la zona de corte con CO2 durante el mecanizado.
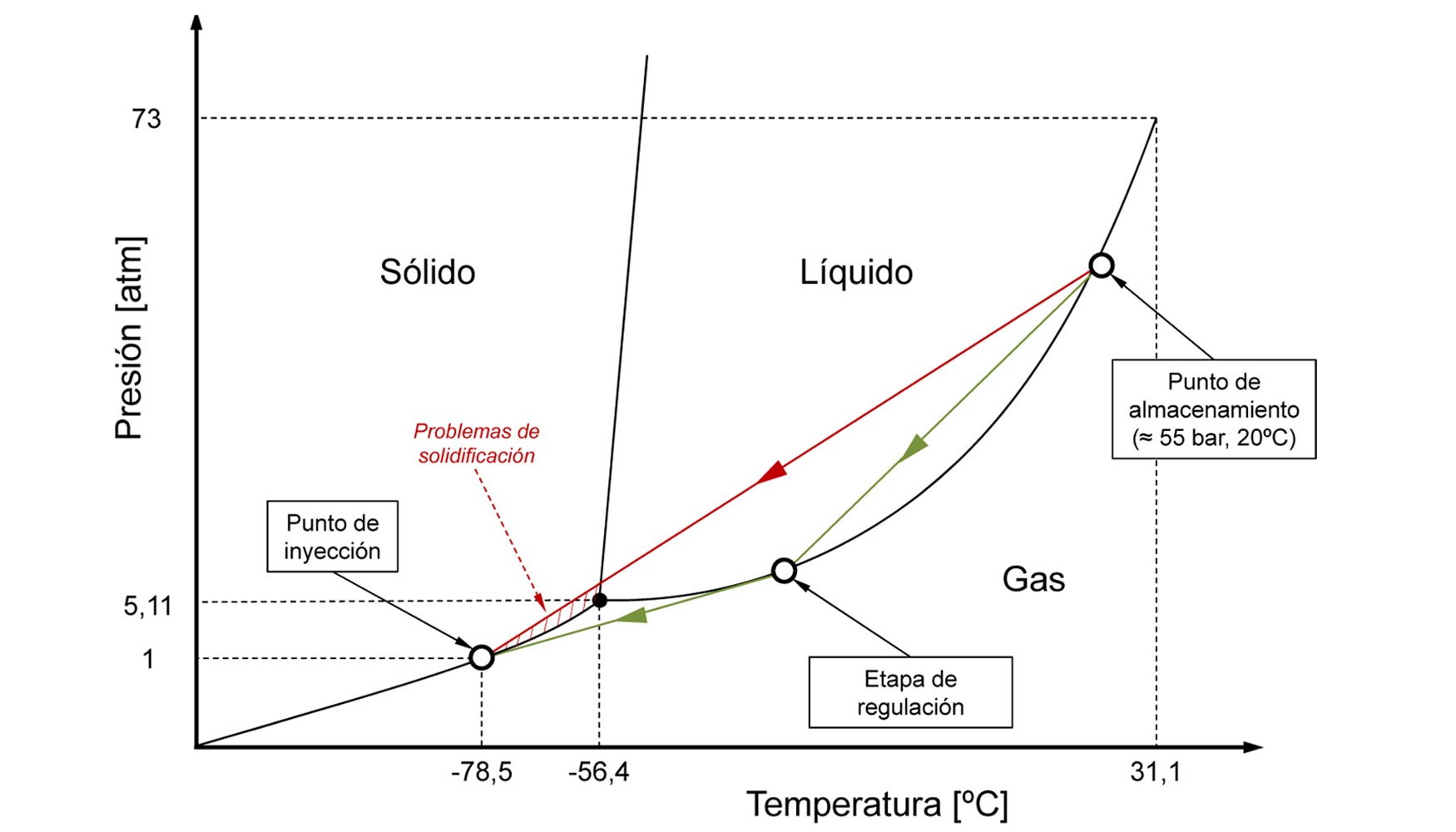
Figura 2. Diagrama de fases CO2.
Por otra parte, dependiendo del tipo de operación de mecanizado en la que se vaya a realizar se han desarrollado diferentes métodos para la correcta inyección del CO2. En el caso de fresado, éste puede ser aplicado de forma interna a la herramienta o externa mediante la utilización de una tobera similar a las utilizas con la taladrina. En caso de utilizar el CO2 interiormente, se hacen necesarios la modificación de la junta rotativa de la fresadora mediante un adaptador que permita la entrada del CO2 sin dañarla ni dañar los rodamientos del husillo; hermetizar los portaherramientas a utilizar para evitar despresurizaciones que provoquen descensos drásticos de temperatura en el interior del husillo; y por último utilizar herramientas comerciales de refrigeración interna convencionales.
Para las operaciones de taladrado, además de las técnicas expuestas en el apartado anterior existe una tercera opción para poder aplicar el CO2 internamente en caso de no tener un conducto en el interior del husillo por el cual conducirlo. Para ello simplemente es necesario adecuar un adaptador coaxial utilizado generalmente para aplicar taladrina o MQL. En este adaptador el CO2 entra de forma radial a una cámara presurizada en su interior que está provista de unos orificios que permiten su entrada al interior de la herramienta.
Por último, para su aplicación en operaciones de torneado, el CO2 puede ser utilizado externamente como se utiliza habitualmente la taladrina, o en caso de desear una aplicación más precisa y eficiente, utilizar portaherramientas con refrigeración interna para taladrina a alta presión. Este tipo de portaherramientas por lo general poseen dos salidas dirigidas hacia la cara de desprendimiento e incidencia, respectivamente. Gracias a este tipo de portaherramientas y la inyección del CO2 por ambas caras se consiguen principalmente tres efectos. El primero es que se reduce la temperatura de corte por la inyección del CO2 de la cara de incidencia; el segundo que se consigue controlar la dirección de la viruta además de volverla más frágil al inyectar CO2 en la cara de desprendimiento; y por último se logra convertir la plaquita en un intercambiador de calor lo que se traduce en un menor desgaste por efectos térmicos.
En la figura 3 se muestra la aplicación del sistema de refrigeración criogénico en una operación de fresado de acabado utilizando refrigeración por el interior del husillo de la máquina. Se trata de una máquina Kondia a la que se le han realizado las modificaciones necesarias para su uso en aplicaciones criogénicas.
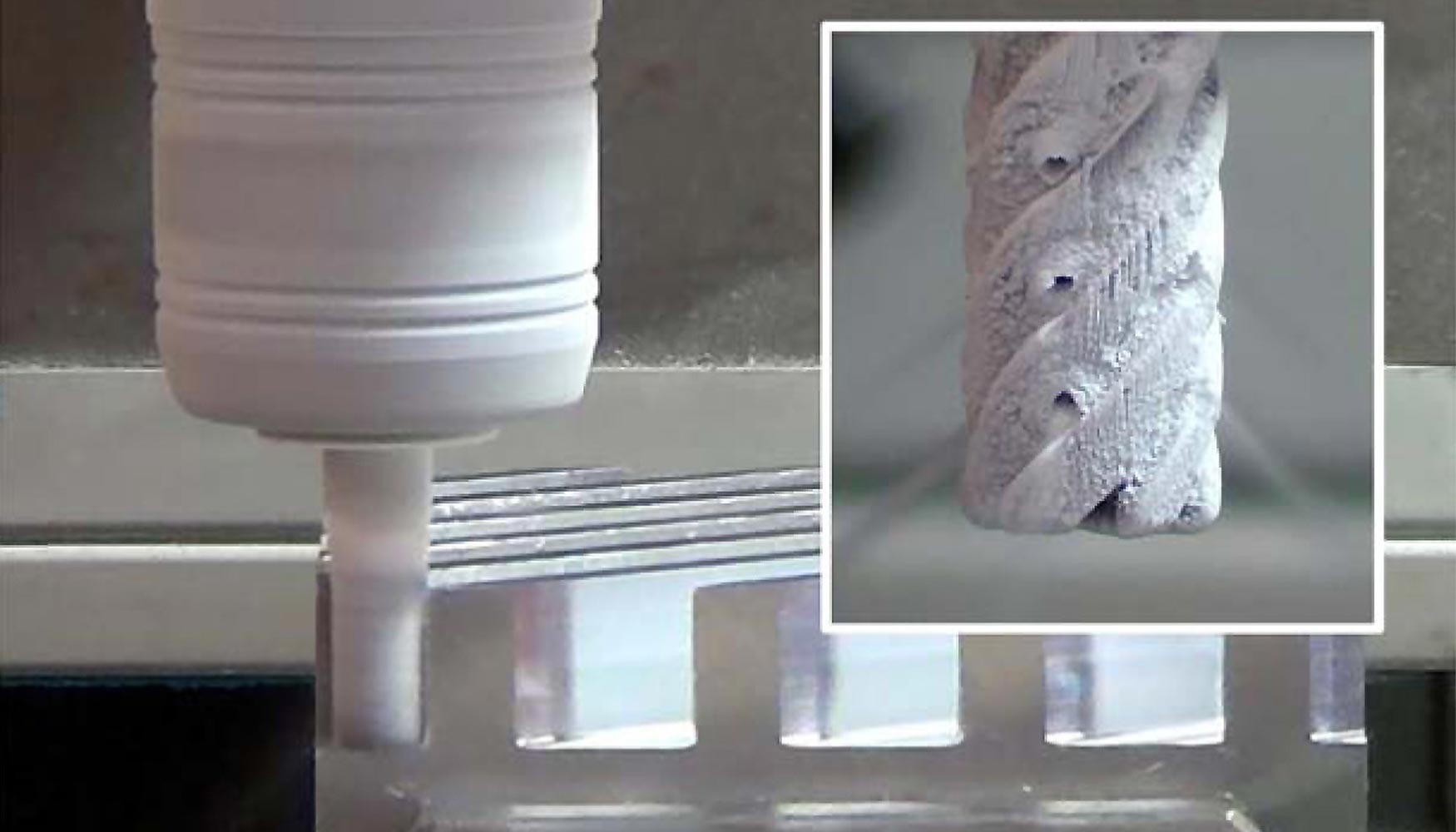
3. Casos de aplicación
La UPV/ EHU y Tecnalia, como agentes de la RVC I, y acordes con su rol de agentes tecnológicos y hacedores de la trasferencia de tecnología, han colaborado con empresas del entorno en la consecución de los objetivos propuestos y bajo el marco del proyecto BeCool. La idea es acercar la tecnología de mecanizado criogénico a las empresas del entorno, principalmente alentados por los éxitos demostrados por otras compañías tanto en Europa como en EE UU. Algunos de los casos de éxito en cuanto a aplicación se presentan a continuación. Se han seleccionado únicamente tres, los cuales hacen referencia a las operaciones de fresado, taladrado y torneado.
En el caso del fresado se presentan los resultados al mecanizar un acero templado con una dureza de 45HRc donde se compararon por un lado el mecanizado en seco, por otro la lubricación MQL y finalmente la combinación de este último con CO2. El objetivo principal de este ensayo fue reducir la carga térmica a la que está sometida la herramienta. La razón por la que se opta por combinar el CO2 con micropartículas de aceite es debido a la fuerte carga mecánica a la que se somete a la herramienta durante el mecanizado en este tipo de aceros de alta fuerza específica de corte. Las condiciones de corte fueron de 90 m/min para la velocidad de corte, 0,075 mm/diente para el avance, una profundidad de pasada de 1 y 18 mm de ancho de pasada. La herramienta utilizada fue una fresa frontal de 3 insertos de diámetro 20 mm, la presión del CO2 fue de 10 bares y 100 ml/h el caudal de aceite utilizado para pulverizar en la zona de corte.
Los resultados muestran que gracias a la disminución de temperatura aportada por la utilización de CO2, el desgaste de la herramienta se reduc a la mitad, como muestran los desgastes de los insertos en la figura 4. Este avance es de gran interés en sectores como el de la fabricación de moldes para estampación y matricería debido a que por lo general se mecanizan en seco o MQL debido a que por la dureza del material la temperatura generada es muy alta y las herramientas utilizadas no aguantan la fatiga térmica producida por la utilización de taladrinas.
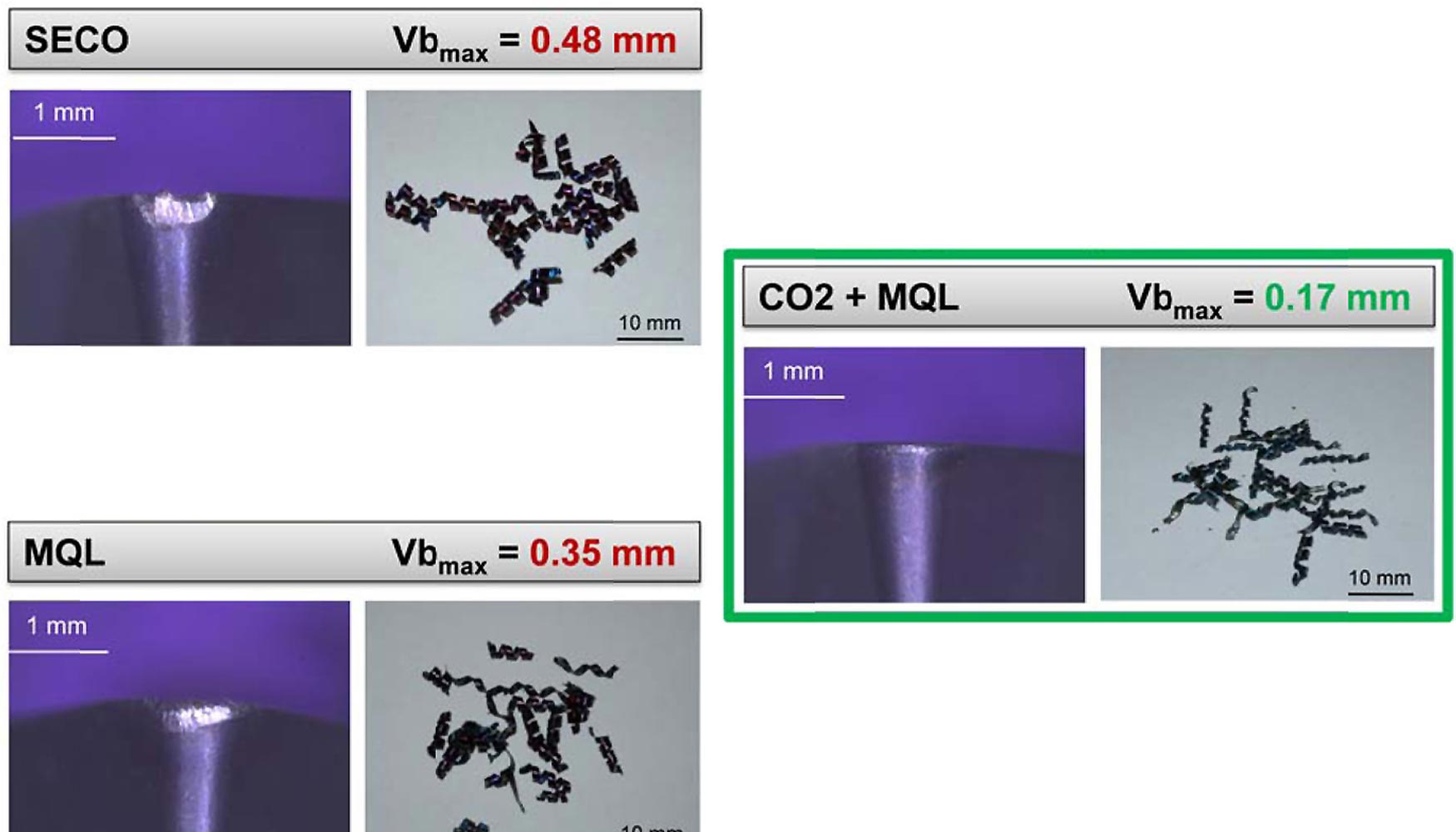
En cuanto a taladrado, se presentan los resulta dos obtenidos tras el mecanizado de stacks de titanio (Ti-6Al-4 V) y fibra de carbono. Este tipo de materiales combinados son cada vez más utilizados en el sector aeronáutico. Las planchas de titanio tenían 10 mm de espesor mientras que las de fibra de carbono tenían 8 mm. La problemática del mecanizado de stacks viene dada por la combinación de dos defectos contraproducentes. El primero radica en la necesidad de mecanizar en seco la fibra de carbono. El segundo efecto es consecuencia del primero, al no poder utilizar ningún fluido de corte se alcanzan temperaturas de corte considerables que llevan a producir adhesiones del titanio en el filo de la herramienta debido a su gran afinidad con el material de ésta a elevadas temperaturas. Por ello, en este caso se ha aplicado el CO2 con una broca de diámetro 7,5 y refrigeración interna comparándolo con el mecanizado en seco.
A tenor de los resultados obtenidos, se consiguió minimizar la adhesión de titanio provocada por el mecanizado en seco, además de eliminar el daño térmico en la fibra de carbono. En cuanto a la vida de herramienta, en la figura 5 se muestra la herramienta utilizada taladrando en seco y taladrando con CO2, para un mismo número de agujeros.
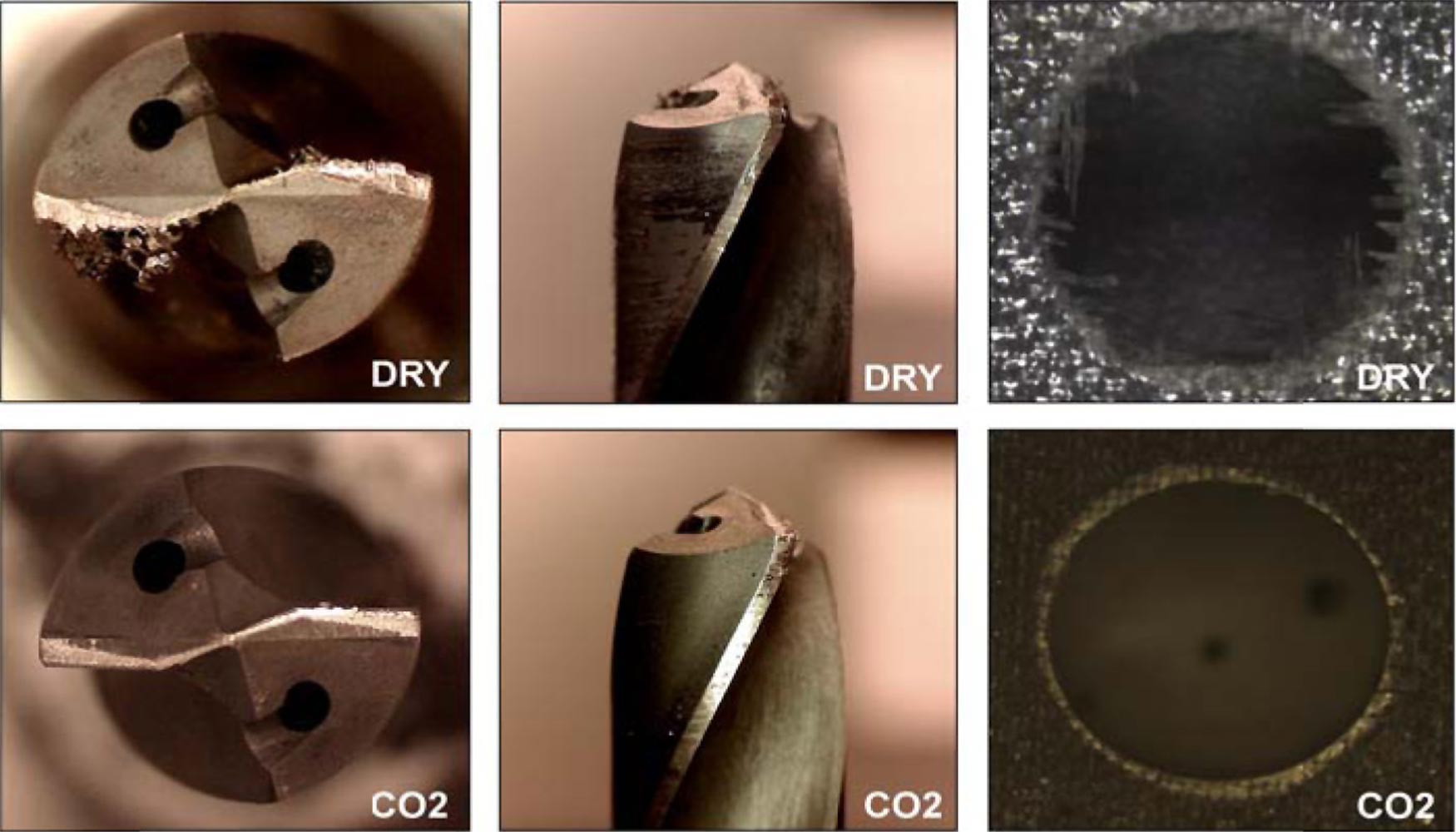
En cuanto al torneado se seleccionó un material comúnmente utilizado en la industria del entorno, como son los aceros inoxidables. Concretamente se cilindraron barras de AISI 304L con una velocida de de corte de 225 m/min, 0,25 mm/rev de avance y un a profundidad de pasada de 1,5 mm. En esto ensayos se comparó el mecanizado en seco frente al mecanizado criogénico tanto con LN2 como con CO2, la utilización de MQL (80 ml/h) y finalmente mecanizado con taladrina. El objetivo de este ensayo se centró principalmente en tener una noción real de las alternativas propuestas a la taladrina en relación a la vida de herramienta.
En la figura 6 se muestran los resultados de vida de la herramienta con diferentes técnicas de lubricación-refrigeración. Se asigna un valor de 100% al mejor de los casos, el uso de taladrina convencional. Se aprecia como el mecanizado en seco únicamente alcanza un valor de 46% en cuanto a vida de herramienta. El empleo de LN2 en solitario y MQL en solitario reporta valores de vida útil entorno al 50%. Estos resultados demuestran como en esta aplicación es necesario combinar capacidades lubricantes con capacidades refrigerantes, ya que por separado no dan buen resultado. En el caso del CO2 se aprecia que la vida de la herramienta alcanza hasta un 70%, en parte debido a la capacidad refrigerante y lubricante ya demostrada en otros trabajos. Finalmente, la combinación de LN2 y MQL, en este caso la tecnología ‘Green’ que mejores resultados reporta, con valores hasta el 92%. Esto resalta de nuevo la importancia de lubricar y refrigerar en aplicaciones de torneado de acero inoxidable. Si bien, en ninguno de los casos se llega a alcanzar la vid a útil que se consigue con el uso de taladrina, alcanzar un 92% de este valor con tecnologías de refrigeración ECO2 es un gran avance en este campo. La escasa pérdida de vida útil se compensa fácilmente con las notables ventajas de estas tecnologías, como por ejemplo el poder mecanizar en condiciones de semi-seco, el obtener la viruta seca, eliminar los gastos derivados del uso de taladrinas y sobre todo el impacto ambiental.
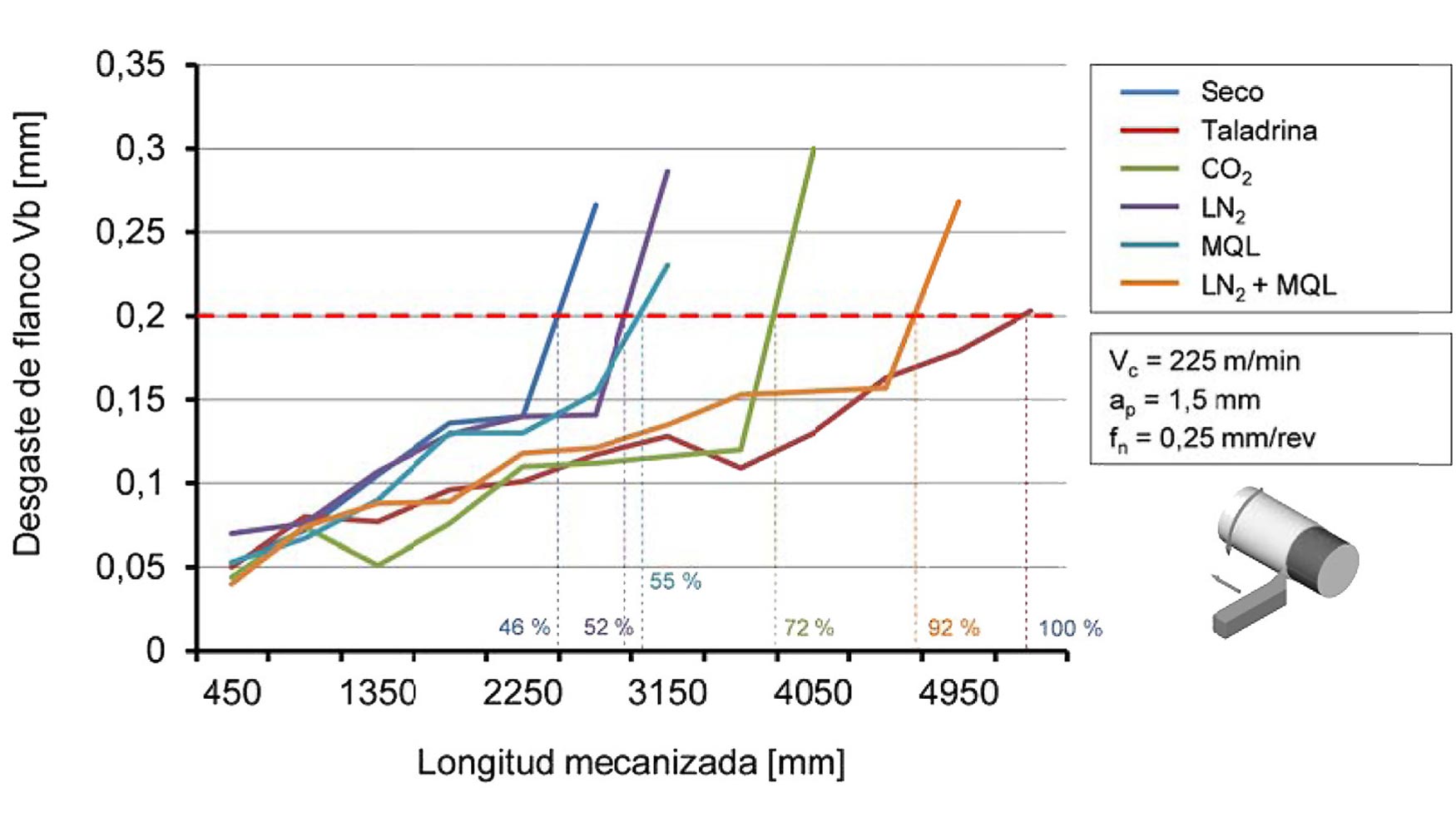
4. Conclusiones
Como se ha podido apreciar en el trabajo realizado el objetivo principal ha sido satisfacer las necesidades industriales en los diferentes campos que el mecanizado abarca desde un punto de vista tanto económico como ecológico (rendimiento ECO2).
Para ello se han desarrollado diferentes técnicas de refrigeración criogénica con CO2 para su posible aplicación en las operaciones de fresado, taladrado y torneado, tanto de forma externa como interna la herramienta.
Esta tecnología es de gran interés para los procesos de mecanizado realizados principalmente en sectores como el aeronáutico de matricería y moldes. Los ensayos muestran que en el fresado de materiales de alta dureza, como el caso de los aceros templados, la refrigeración criogénica es una alternativa real debido a que se reduce el desgaste de la herramienta de forma notable. También en el taladrado de materiales como el titanio donde existen problemas de adhesión, al aplicar la refrigeración criogénica con CO2 se logra estabilizar el proceso de forma significativa a la vez que se alarga la vida de la herramienta. Además, en el taladrado de compuestos de carbono se aprecia como, gracias a la refrigeración criogénica, se elimina el daño térmico que pueda sufrir la pieza por las temperaturas de corte alcanzadas. Por otra parte, al mecanizar materiales donde el desgaste por influencia mecánica tiene prevalencia sobre el desgaste por influencia térmica, el uso de CO2 ha sido la alternativa más prometedora al mecanizado tradicional con taladrina.
No todos los resultados han sido exitosos durante el desarrollo de esta tecnología. Hay aplicaciones en donde el gasto de fluido criogénico y la inversión inicial no compensa las mejoras obtenidas por su aplicación. En esta línea, será de gran importancia la identificación correcta de aquellas aplicaciones donde el mecanizado asistido por fluidos criogénicos puede tener cabida.
Agradecimientos
Se agradece el soporte recibido del programa Manunet, Grupo SPRI y Gobierno Vasco por el Proyecto de acrónimo BeCool, liderado por HRE Hidraulic, y en el que han participado las empresas Mecanifran, Neco, Susensa, MetalEstalki y Kondia, así como Tecnalia y UPV/EHU como agentes tecnológicos. Se agradece la ayuda recibida con cargo al presupuesto de gastos del Departamento de Desarrollo Económico y Competitividad y al Fondo Europeo de Desarrollo Regional (Feder), así como a la UPV/EHU bajo el programa UFI 11/29 y al proyecto DPI2012-36166 del Mineco.
Referencias
[1] Pusavec, F.; Deshpande, A.; Yang, S.; M'Saoubi, R.; Kopac, J.; Jr., O. W. D. & Jawahir, I. Sustainable machining of high temperature Nickel alloy – Inconel 718: part 1 – predictive performance models Journal of Cleaner Production, 2014, 81, 255 - 269
[2] Kopac, J. Achivievements of sustainable manufacturing by Machining Journal of achievements in materials and manufacturing engineering, 2009, 34 (2), 180-187
[3] Hong, S. Y.; Ding, Y. & Jeong, J. Experimental Evaluation of friction coefficient and liquid nitrogen Lubrication effect in cryogenic machining Machining Science and Technology, 2002, 6, 235-250.
[4] Hong, S. Y. Lubrication Mechanism of LN2 in Ecological Cryogenic machining Machining Science and Technology, 2007, 10, 133-155.
[5] Klocke, F.; Krämer, A.; Sangermann, H. & Lung, D. Thermo-Mechanical Tool Load during High Performance Cutting of Hard-to-Cut Materials Procedia CIRP, 2012, 1, 295 – 300.
[6] Kramer, A.; Klocke, F.; Sangermann, H. & Lung, D. Influence of the lubricoolant strategy on thermo-mechanical tool load CIRP Journal of Manufacturing Science and Technology, 2013, 7, 40-47.
[7] Supekar, S.; Clarens, A.; Stephenson, D. & Skerlos, S. Performance of supercritical carbon dioxide sprays as coolants and lubricants in representative metalworking operations Journal of Materials Processing Technology, 2012, 212, 2652 – 2658.
[8] Stephenson, D.; Skerlos, S.; King, A. & Supekar, S. Rough Turning Inconel 750 with Supercritical CO2-based Minimum Quantity Lubrication Journal of Materials Processing Technology, 2014, 214, 673-680.
[9] Horn, W.; Haus, W. & Shmalzried, S. Method for cooling and lubricanting a tool and for cleaning the machined Surface, US-2011/0166692. 2011.
[10] Jackson, D.P. Nozzle device and method for forming cryogenic composite fluid spray, US-7,389,941 B2. 2008.
[11] Jackson, D.P. Method of forming and using carbonated machining fluid, US-8,048,830 B1. 2011.
[12] Schmid, K. Vorrichtung zur aerosolerzeugung, EP 2.338.587 A1. 2011.