Estudio del desgaste de muelas de CBN empleadas en el rectificado de superaleaciones
En las turbinas existen numerosos componentes fabricados con materiales de especial resistencia a elevadas temperaturas (temperatura de trabajo superiores a 1.050 °C). Entre estos materiales, destacan las aleaciones base Ni, Ti, Co, entre otras, con composiciones de multitud de elementos metálicos y no metálicos que aportan resistencia a la corrosión, al desgaste e incremento de propiedades mecánicas a elevadas temperaturas. El abanico de materiales es muy amplio y su comportamiento ante diferentes procesos de mecanizado, diverso.
Existe gran variedad de componentes, si bien aquellos que presentan formas más intrincadas y con tolerancias más estrechas (álabes, blisk/impellers o NGVs, por ejemplo) se acaban mediante procesos como el rectificado y/o electroerosión. Estos procesos presentan aún problemas no resueltos que limitan su potencial y pueden llegar a suponer hasta el 75% del coste de fabricación en algunos componentes.
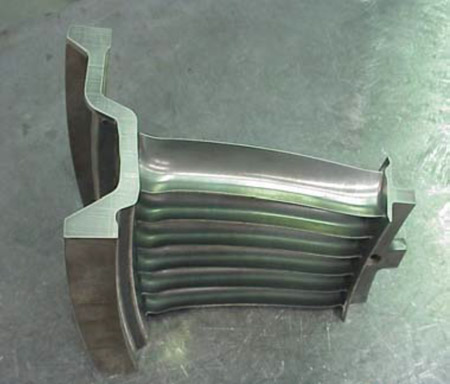
De estos procesos de acabado, el rectificado es el proceso que supone un mayor desembolso, por lo que las tendencias actuales en investigación están centradas en la búsqueda de soluciones que incrementen la productividad. Esto supone que el proceso en su forma clásica no es capaz de llevar a cabo de manera satisfactoria el mecanizado de este tipo de materiales y es necesario recurrir a variante como el Creep-Feed Grinding o el High Efficiency Deep Grinding.
Se trata de procesos que aumentan de manera siginificativa la profundidad de pasada del proceso a costa de disminuir la velocidad de avance (caso del Creep-Feed Grinding). Uno de los objetivos que se persigue con este tipo de procesos es intentar aumentar el caudal de viruta para que sea ésta la que evacúe la mayor parte del calor generado en la zona de contacto. Así mismo, en el caso del Creep Feed Grinding, al aumentar el tiempo de contacto entre muela y pieza, y gracias al empleo de muelas de CBN (material de elevada conducción térmica), la fracción de calor que se evacúa hacia la pieza se reduce hasta el 3-8% de todo el calor generado durante el proceso (mientras que con Al2O3 los porcentajes alcanzan el 80%).
Como consecuencia, se consiguen reducir considerablemente la temperatura a pesar de haber aumentado de manera significativa el caudal de viruta. Al mismo tiempo, el fluido de corte es capaz de evacuar mucho más calor que en el caso del rectificado convencional (90% frente al 5-10%). Además, el aumento del tamaño de la viruta, posibilita que el mecanismo predominante de arranque de material sea la cizalladura frente a la deformación lateral (ploughing) o el rozamiento (rubbing). Esta reducción de la temperatura en la pieza con un arranque de material basado en la cizalladura permite un proceso eficiente y altamente productivo.
Sin embargo, el Creep Feed Grinding trae consigo otros fenómenos no deseables como son un desgaste excesivo de las muelas y la necesidad de máquinas muy rígidas y de gran potencia. Es por ello que, a pesar de que hay estudios en los que se lleva a cabo el proceso de Creep-Feed Grinding con muelas convencionales, en la mayoría de los casos el mantenimiento de las geometría de la pieza en series largas obliga al empleo de muelas de CBN o incluso de diamante. La principal ventaja de este tipo de muelas es la mayor dureza del material abrasivo que minimiza el desgaste de la muela llegando a obtenerse ratios de desgaste volumétrico (Volumen de material rectificado/Volumen de muela desgastado) de 15.000 muy por encima de los ratios de desgaste del rectificado convencional (50-100).
Estudio del desgaste de la muela de CBN
Los mecanismos de desgaste existentes en las herramientas son: abrasión, adhesión, afinidad química, agrietamiento de la superficie y difusión. La superposición de estos mecanismos de desgaste en muelas electrodepositadas de CBN conduce a los desgastes del tipo ‘wear flat’ (generación de grano plano) y caida de grano (ver Figura 2).
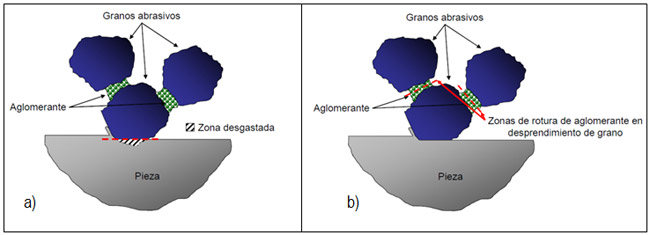
En este tipo de muelas, el desgaste predominante es del tipo ‘wear flat’ (grano plano). Se trata de la desaparición de las aristas de corte del grano por fenómenos de difusión, elevadas temperaturas y presiones en la zona de contacto grano-pieza. La aparición de este plano en el grano, incluso en un porcentage ínfimo del 3% en área total de la muela, introduce fuertes incrementos de la fricción en el proceso y, por ende, de las fuerzas, la potencia consumida (calor generado) y la aparicición de vibraciones con consecuencias negativas para la calidad de la pieza.
En ciertas ocasiones, por el contrario, cuando la carga sobre el grano es muy elevada (rectificado con grandes tasas de arranque sobre radios de acuerdo), aparece la fractura de grano y, en casos severos, la caida de grano. Esta última que puede ser peligrosa por dar lugar a desconchamientos de la capa abrasiva y el dañado irreversible de la pieza. Por último, cabe destacar la posibilidad de que el material de pieza, de naturaleza plástica, quede adherido a la muela con consecuencias como una disminución de la capacidad de arranuqe, de la capacidad de refrigeración, así como un aumento del rozamiento (y potencia consumida). Estamos, en cualquier caso, ante fenómenos a evitar cuya aparición debe ser cuidadosamente estudiada.
El Departamento de Ingeniería Mecánica de la UPV/EHU, junto con ITP S.A., está desarrollando un estudio para minimizar el desgaste de las muelas de CBN empleadas en el rectificado de NGVs. Para ello, se está caracterizando el desgaste de las muelas mediante parámetros estándar de rugosidad a lo largo del tiempo y su influencia en el consumo de potencia. El estudio del desgaste de forma cuantitativa requiere la digitalización de la superficie con la máxima precisión. Para ello, se ha empleado un microscopio confocal Leica DCM 3D. Al mismo tiempo, se ha procedido a la obtención de imágenes reales que permiten diferenciar los bordes de grano del aglomerante.
En la Figura 3, aparecen las superficies de una muela nueva y una desgastada que ha rectificado más de 8x106mm3 de Inconel 718. Se observa claramente el desgaste predomientante de ‘wear flat’, así como el embotamiento de la muela.
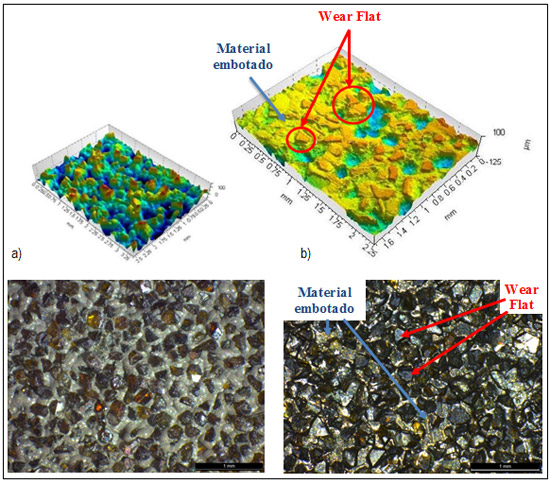
El análisis cuantitativo de la superficie se ha llevado a cabo empleando parámetros de rugosidad superficial 3D contemplados en la norma ISO-25178. En concreto, se han estudiado los parámetros de altura Sq, Ssk, Sk, Sp, Sv, Sz y Sa, los parámetros funcionales Sm, Smc y Sxp, así como los obtenidos de la curva de Abott-Firestone en 3D, Spk y Svk.
Resultados obtenidos
En la Figura 4 se observan las diferencias en los resultados obtenidos aplicando una lc=0,8 mm. De los parámetros estudiados, los parámetros de altura son lo que presentan mayor variación con el desgaste encontrado en este tipo de muelas. Entre ellos, cabe destacar el Sz, Sp, Sk, Spk y Svk como los que presentan mayor sensibilidad.
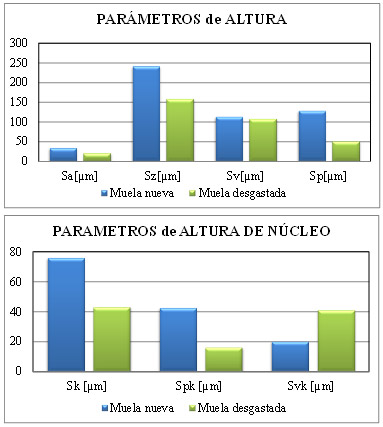
Como se ha comentado anteriormente, esta diferencia implica pérdida de capacidad de corte, incremento del rozamiento y, por ende, la potencia consumida. En la Figura 5, se puede observar la variación de la potencia por unidad de área debida al desgaste de la muela. En este caso, además, los datos de la muela desgastada no corresponden a una muela en el final de su vida útil como en el caso anterior, si no, aproximadamente a mitad de ésta. La gráfica muestra claramente cómo la monitorización de la potencia es esencial para incrementar al máximo la vida de la muela y la eficiencia del proceso.
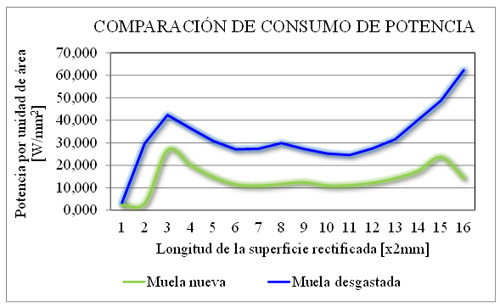
Conclusiones
El rectificado de materiales aeronáuticos implica un elevado coste que debe ser minimizado. Una de las acciones correctoras para por minimizar el desgaste de las muelas de CBN mediante el control de la potencia de la máquina. Para ello, deben relacionarse los parámetros de rugosidad de la norma ISO-25178 (parámetros cuantitativos de desgaste) con los consumos monitorizados en máquina.
Los resultados obtenidos muestran que los parámetros de rugosidad que mayor sensibilidad presentan a la variación de la superficie de la muela con el desgaste de la misma son Sz, Sp, Sk, Spk y Svk.