Schneider Electric, nuevo miembro del Packaging Clúster de Catalunya
17 de enero de 2014
Schneider Electric se ha integrado en el Packaging Clúster de Catalunya, un conjunto de empresas relacionadas con el sector del packaging que se constituyó en 2012 con el objetivo de aumentar la competitividad del sector, facilitando el conocimiento y la interacción para lograr objetivos individuales y comunes. De esta manera, más de una trentena de empresas de la cadena de valor del packaging – desde empresas de materia prima, de materiales, de maquinaria de proceso y envasado, hasta fabricantes de automatismos o agentes tecnológicos y usuario final – han creado un espacio de debate y reflexión en torno a los retos y tendencias clave del mercado para alinearse y poner en valor las propias estrategias, activando proyectos de innovación y potenciando el desarrollo de nuevos productos y alianzas.
Como especialista global en gestión de la energía, Schneider Electric ha entrado a formar parte del clúster, donde aportará su experiencia y soluciones en el campo de la productividad, la eficiencia energética y la automatización y control industrial para dotar de una mayor competitividad a la industria. En esta línea, el Clúster de Eficiencia Energética de Catalunya y el Packaging Clúster organizaron el pasado mes de diciembre una jornada sobre Eficiencia Energética en el sector del packaging.
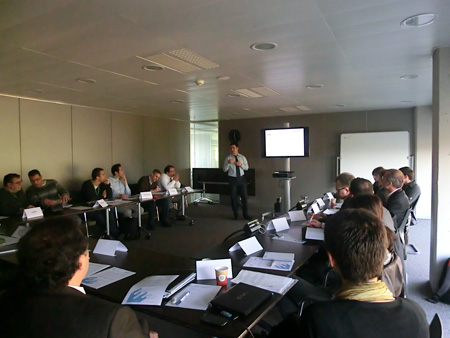
En este contexto, Alberto García, business development OEM Packaging de Schneider Electric, presentó en la jornada el caso de éxito de un proyecto llevado a cabo para lograr una mejora energética en una máquina Flowpack, que se caracteriza por su elevada productividad de hasta 1.200 packs por minuto. Con la solución de Eficiencia Energética de Schneider Electric, se redujo el consumo energético de la máquina un 25% manteniendo el 100% de la productividad (1.200 productos por minuto), con un sobrecoste mínimo de 400 euros.
Para ello, se llevó a cabo una primera fase de análisis en la que se determinó el consumo global de la máquina mediante analizadores de potencia y se estudiaron individualmente los diferentes elementos de consumo del aparato (bombas, motores, calefactores). A continuación se implementó la fase de automatización y se adaptó el software configurándolo y optimizando su consumo según cada uno de los productos a la vez que se optimizaron las levas electrónicas de los servoaccionamientos para evitar paradas y arrancadas con el consiguiente consumo de energía. Cabe destacar, además, que la solución permite disponer de la información de consumo energético ligado a cada unidad producida, facilitando así la toma de decisiones.