Aplicación de la forja rotativa de Inconel 718 a una geometría del sector aeronáutico: análisis microestructural
Introducción
La forja rotativa es un proceso incremental y nace como una alternativa a la forja convencional. Debido a dicha naturaleza incremental, la forja rotativa es capaz de reducir las fuerzas de conformado y obtener grandes ratios de deformación sin grietas en un solo golpe. Los movimientos de los utillajes son dos básicamente, una rotación y una traslación axial. El útil inferior y superior rotan sincrónicamente mientras el utillaje superior se traslada verticalmente para realizar la carrera necesaria para formar la pieza. Lo que concede el carácter incremental a este proceso es la inclinación del utillaje superior sobre el eje vertical, llamado ángulo de nutación. Este puede variar entre 2º y 8º en función de la geometría y material a conformar. A continuación se muestra un esquema de la comparativa entre forja rotativa y convencional así como de los movimientos de este primero.
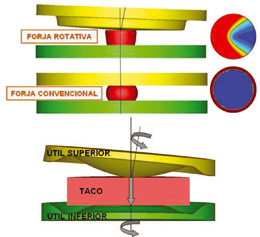
Una de las características importantes de la forja rotativa es la geometría de champiñón que adquiere el taco según se va deformando, a diferencia del barrilete característico de la forja convencional [1]. Este proceso incremental deforma al taco según un nuevo camino de deformación mejorando así el ratio de deformación por golpe, lo que conlleva llegar a geometrías ‘near-net-shape’ en un solo golpe. Una consecuencia directa es la reducción de costes de utillaje por la reducción de preformas necesarias para lograr la geometría final.
Tecnalia, en trabajos previos, desarrolló un modelo de simulación capaz de reproducir geometría y fuerzas implicadas en un proceso de forja rotativa [2,3]. Posteriormente se ha mejorado este modelo incluyendo el cálculo microestructural durante el propio proceso [4,5].
Los requerimientos de los componentes del sector aeronáutico son muy restrictivos, tanto desde el punto de vista geométrico como microestructural. En función de la microestructura de un componente este presenta uno u otro comportamiento mecánico durante su vida útil, pudiendo ser este resistencia a fatiga o a creep. Por ello el estudio de la evolución microestructural incluso durante el proceso de conformado cada vez adquiere mayor importancia.
Los cálculos microestructurales se basan en la implementación de las ecuaciones que rigen esa evolución basadas en la temperatura, deformación, velocidad de deformación y tamaño inicial del grano [6]. Los parámetros que definen las ecuaciones anteriores son determinados en ensayos de compresión de simple y doble golpe [7].
El material utilizado en este estudio, Inconel 718, es uno de los más utilizados en el sector aeronáutico por resistencia a la corrosión, creep y fatiga a altas temperaturas durante la vida útil del componente. Estas ventajas se ven contrarestadas por la estrecha ventana de conformado que posee. Estando ésta limitada entre 900 y 1.120 °C [8]. El control de esta temperatura así como de los valores de deformación y de velocidad de deformación durante el proceso de conformado conllevan un control de la microestructura final del componente.
Obtener una microestructura de tamaño de grano fino implica un control preciso de la temperatura durante el proceso de forja. Una de las fases del Inconel 718 es la fase δ, siendo su característica principal la limitación del crecimiento del tamaño de grano. Por ello si el objetivo es una microestructura con grano fino es necesario asegurarse que no se supera la temperatura de disolución de esta fase, rondando los 1.020 °C. Este fenómeno se estudia en profundidad en varias publicaciones [9,10].
Durante el conformado a estas temperaturas tiene lugar la recristalización cuya consecuencia es una caída del nivel tensional en la gráfica tensión —deformación y nucleación de nuevos granos—. Lo primero implica menores fuerzas requeridas para la deformación y lo segundo implica afinamiento del tamaño de grano. En trabajos previos se han analizado estudios del proceso de recristalización en la forja rotativa [4].
Forja rotativa: geometría
Tras los primeros resultados de la aplicación del proceso de conformado mediante la forja rotativa al Inconel 718 [4,5] para la obtención de una geometría sencilla de recalcado, en el presente trabajo se expone el análisis realizado en una pieza industrial del sector aeronáutico. La geometría de dicha pieza, expuesta en la siguiente figura, fue suministrada por la empresa Industria de Turbo Propulsores, S.A. (ITP).
![Figura 2. [Geometría pieza real después del mecanizado] Figura 2. [Geometría pieza real después del mecanizado]](https://img.interempresas.net/fotos/908118.jpeg)
El objetivo ha sido obtener la geometría previa al mecanizado mediante forja rotativa dentro de las especificaciones de máquina disponibles. Dadas las dimensiones de los componentes del sector aeronáutico, dichas especificaciones son un requisito complejo siendo necesarios equipos que requieran grandes inversiones.
De este modo se ha obtenido la definición de la preforma y los parámetros de fabricación que cumplían los requisitos iniciales de fuerzas de manera numérica. La preforma se muestra en la siguiente figura.
![Figura 3. [Preforma de forja rotativa] Figura 3. [Preforma de forja rotativa]](https://img.interempresas.net/fotos/908119.jpeg)
Los parámetros de proceso usados han sido:
- Velocidades del proceso: 70 rpm y 0,8 mm/s
- Temperatura de utillajes: 500 °C
La relación de velocidades es relativamente lenta en comparación con la usada para piezas de otros sectores, como la automoción. La definición de la temperatura de los utillajes proviene del trabajo previo realizado sobre una geometría sencilla de recalcado.
Con los parámetros mencionados la fuerza necesaria para la fabricación de dicha preforma alcanza valores hasta 1.700 toneladas en función de la temperatura inicial del taco. Como se muestra en la siguiente gráfica, la fuerza necesaria se reduce aumentando la temperatura del taco, de 970 a 1.000 °C. Sin embargo, este aumento de temperatura se encuentra limitado por las condiciones finales de microestructura requeridas. Estas fuerzas son relativamente pequeñas comparables con los procesos convencionales de forja.
![Figura 4. [Comparativa de fuerzas para la preforma a diferentes temperaturas iniciales en forja rotativa] Figura 4. [Comparativa de fuerzas para la preforma a diferentes temperaturas iniciales en forja rotativa]](https://img.interempresas.net/fotos/908123.jpeg)
Optimización de la temperatura inicial del taco
El aumento sistemático de la temperatura inicial del taco se traduce en una reducción de fuerzas. Sin embargo, la microestructura final (afinamiento de grano y homogeneidad) puede verse dañada considerablemente aún forjando dentro de la ventana de trabajo definida para el Inconel 718, entre 900 y 1.120 °C. El objetivo de esta sección es la obtención de la geometría con tamaño de grano fino (mayor que 6ASTM) y homogéneo en toda la sección de la misma.
Los resultados numéricos microestructurales tomando como temperatura inicial del taco 970 y 1.000 °C se muestran en la siguiente figura. Las condiciones iniciales de proceso son las velocidades marcadas en la sección anterior, 70 rpm y 0,8 mm/s, así como temperatura de utillajes de 500 °C. El tamaño de grano inicial al comienzo de la forja rotativa ha sido 9ASTM.
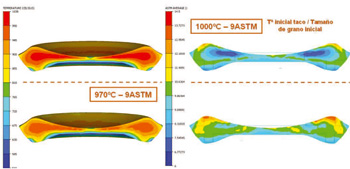
Para el caso de temperatura inicial igual a 1.000 °C, en la zona central de la sección la temperatura aumenta por encima de la inicial debido al calentamiento por deformación plástica. Este incremento de temperatura para el caso del Inconel 718 puede llegar a alcanzar los 60 °C [11]. Debido a este efecto, la temperatura en esa zona central supera la temperatura de disolución de fase δ, mencionado con anterioridad, lo que implica un crecimiento del tamaño de grano en esa zona. Así se refleja en la imagen de la microestructura donde el tamaño de grano ha aumentado de 9ASTM inicial a valores entre 6.7 y 7.5ASTM.
En la siguiente gráfica se muestran los valores máximo y mínimo del tamaño de grano para cada uno de los dos casos anteriores.
![Figura 6. [Tamaño de grano máximo y mínimo. Optimización de la temperatura inicial del taco] Figura 6. [Tamaño de grano máximo y mínimo. Optimización de la temperatura inicial del taco]](https://img.interempresas.net/fotos/908125.jpeg)
Se aprecia como el caso de 1.000 °C posee una microestructura más heterogénea que el caso de 970°C debido al crecimiento de grano mencionado con anterioridad. De este modo queda reflejada la temperatura de 970 °C iniciales como la más idónea para esta geometría en la forja rotativa.
Forja rotativa: geometría escalada
Tras los resultados obtenidos previamente surge la necesidad de la realización de una pieza experimental. Para ello se utilizará la máquina experimental de forja rotativa que dispone Tecnalia en sus instalaciones desarrollada conjuntamente con la empresa Industrias Puigjaner, S.A. (DENN), mostrada en la siguiente imagen.
![Figura 7. [Máquina de forja rotativa desarrollada conjuntamente entre DENN y Tecnalia] Figura 7. [Máquina de forja rotativa desarrollada conjuntamente entre DENN y Tecnalia]](https://img.interempresas.net/fotos/908126.jpeg)
Debido a las dimensiones de la pieza es necesario escalar dicha geometría a valores de fuerzas y geometría aptas para la máquina experimental. Por ello, el escalado elegido es 1/3. Esto implica una reducción geométrica tal y como se muestra en la tabla siguiente, tanto para el taco inicial como para la preforma tras la forja rotativa:
![Tabla 1. [Comparativa geométrica del taco inicial y preforma tras la forja rotativa a escala real y escalada 1/3] Tabla 1. [Comparativa geométrica del taco inicial y preforma tras la forja rotativa a escala real y escalada 1/3]](https://img.interempresas.net/fotos/908127.jpeg)
Comparativa geometría a escala real y escalada 1/3
En el presente apartado se realiza la comparativa entre preforma escalada a tamaño real y la escalada 1/3. En la comparativa se estudia tanto las fuerzas como la distribución de temperaturas y tamaño de grano en la sección transversal de la preforma.
1.1 Fuerza
La misma reducción vista en geometría puede verse en rangos de fuerzas, como se aprecia en la siguiente gráfica.
![Figura 8. [Comparativa de fuerzas entre preforma a escala real y escalada 1/3] Figura 8. [Comparativa de fuerzas entre preforma a escala real y escalada 1/3]](https://img.interempresas.net/fotos/908128.jpeg)
1.2 Temperatura y tamaño de grano
En las siguientes figuras se presenta la comparativa en temperaturas y tamaño de grano referente a la preforma de forja rotativa a escala real y escalada 1/3. Ambas geometrías fueron obtenidas por forja rotativa con los siguiente parámetros de proceso: 70 rpm y 0,8 mm/s, temperatura de utillajes igual a 500 °C, tamaño de grano inicial de la forja rotativa 9ASTM y temperatura inicial de taco igual a 970 °C.
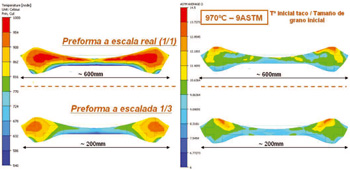
Tal y como se aprecia en las imágenes, la preforma a escala real posee temperaturas superiores en el centro de la sección transversal. Esto es debido fundamentalmente al tamaño de la pieza, es decir, a mayor tamaño mayor es la deformación y como consecuencia mayor es el incremento de temperatura por deformación plástica. A pesar de este incremento de temperatura, al partir de una temperatura de 970 °C al final del proceso no se sobrepasa los 1.020 °C, temperatura de disolución de la fase δ, a partir de la cual el tamaño de grano empieza a crecer. Por este motivo, para ambos casos la microestructura obtenida es similar en cuanto a homogeneidad y tamaño de grano.
En la siguiente gráfica se muestran los valores máximo y mínimo del tamaño de grano para cada uno de los dos casos anteriores.
![Figura 10. [Tamaño de grano máximo y mínimo. Comparativa del escalado] Figura 10. [Tamaño de grano máximo y mínimo. Comparativa del escalado]](https://img.interempresas.net/fotos/908130.jpeg)
Como conclusión se obtiene la verificación de la similitud en ambos casos, escalado 1/3 y real, de la homogeneidad y el afinamiento de grano.
2. Influencia de parámetros del proceso sobre la preforma escalada 1/3
Tras la comparativa realizada en la sección anterior, en el presente apartado se estudia la influencia de diferentes parámetros sobre la microestructura final. Los parámetros seleccionados han sido el tamaño de grano inicial, la velocidad del proceso y el ángulo de nutación.
2.1 Tamaño de grano inicial
Para poder ver la influencia de este parámetro se han analizado dos casos, uno partiendo de 4ASTM y otro de 9ASTM como tamaño de grano inicial. Los parámetros iniciales de proceso son iguales para ambos casos: velocidades de 70 rpm y 0,8 mm/s, temperatura de utillajes igual a 500 °C y temperatura inicial del taco previo a la forja rotativa igual a 970 °C.
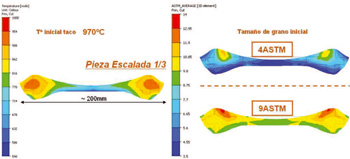
Como conclusión de las imágenes anteriores, la distribución obtenida es homogénea cuando el tamaño de grano inicial fino es 9ASTM. En el caso de tamaño de grano inicial igual a 4ASTM se necesita incrementar la temperatura para garantizar la recristalización en toda o al menos gran parte de la geometría y obtener una microestructura final fina y homogénea.
En la siguiente gráfica se muestran los valores máximo y mínimo del tamaño de grano para cada uno de los dos casos anteriores.
![Figura 12. [Tamaño de grano máximo y mínimo. Influencia del tamaño de grano inicial] Figura 12. [Tamaño de grano máximo y mínimo. Influencia del tamaño de grano inicial]](https://img.interempresas.net/fotos/908133.jpeg)
En la gráfica previa queda patente de nuevo la homogeneidad de la microestructura partiendo de un tamaño de grano fino. De este modo se establecen las dos variantes de trabajo en función del tamaño de grano inicial para el caso cuya meta sea la obtención de una microestructura fina y homogénea. Partiendo de tamaño de grano fino el objetivo a conseguir durante el proceso de conformado es no aumentar la temperatura por encima de la temperatura de disolución de la fase δ con objeto de no empeorar la microestructura ya fina inicial. Sin embargo, partiendo de tamaño de grano grosero el objetivo del proceso de conformado es recristalizar la mayor sección de la geometría posible para afinar el tamaño de grano inicial.
2.2 Velocidad de conformado
El estudio de la influencia de la velocidad de conformado nace de la necesidad de adaptar los parámetros de la geometría escalada a los parámetros de la máquina experimental disponible en Tecnalia. Las velocidades de proceso utilizadas en el caso de la geometría real estaban condicionadas por el tamaño de la pieza. La reducción de la velocidad de trabajo es directamente proporcional a la reducción de pares y esfuerzos. Sin embargo, en el caso de la pieza escalada a 1/3 es posible incrementar esta velocidad permitiendo realizar un análisis de la sensibilidad de este parámetro.
Como primera consecuencia de la variación de la velocidad del proceso surge la variación de las fuerzas en el mismo. En la siguiente gráfica se visualiza la evolución de la fuerza durante el proceso de forja rotativa para tres velocidades diferentes de proceso, una correspondiente a las velocidades de la geometría a escala real, 70 rpm y 0,8 mm/s, y dos correspondientes a las velocidades adaptadas a la máquina experimental situada en Tecnalia, 300 rpm con la variación entre 15 y 5 mm/s.
![Figura 13. [Comparativa de fuerzas para diferentes velocidades de proceso de foja rotativa] Figura 13. [Comparativa de fuerzas para diferentes velocidades de proceso de foja rotativa]](https://img.interempresas.net/fotos/908153.jpeg)
La fuerza máxima obtenida para la velocidad de conformado de 70 rpm y 0,8 mm/s se encuentra entre las resultantes de las otras dos velocidades más rápidas.
A continuación se muestran las figuras correspondientes a la comparativa temperatura - microestructura para las diferentes velocidades de proceso, como en secciones anteriores. Los parámetros iniciales para todos los casos han sido temperatura inicial del taco 970 °C, tamaño de grano inicial 9ASTM y temperatura de utillajes igual a 500 °C.
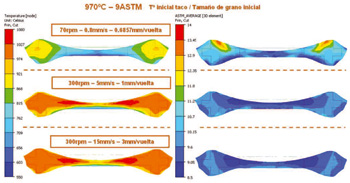
Las velocidades más rápidas de proceso originan una distribución más homogénea de la microestructura. Por el contrario, son estas las que ocasionan mayor temperatura en las zonas interiores de la geometría ocasionando crecimiento del tamaño de grano en estas zonas. Sin embargo, este fenómeno quedará controlado tomando una temperatura inicial adecuada a los parámetros del proceso.
En la siguiente gráfica se muestran los valores máximo y mínimo del tamaño de grano para cada uno de los tres casos anteriores.
![Figura 15. [Tamaño de grano máximo y mínimo. Influencia de la velocidad del proceso] Figura 15. [Tamaño de grano máximo y mínimo. Influencia de la velocidad del proceso]](https://img.interempresas.net/fotos/908156.jpeg)
En la figura 15 se han representado los valores máximos y mínimos de tamaño de grano para los distintos casos cinemáticos estudiados, quedando reflejada la tendencia a la homogeneidad de grano a medida que incrementamos la velocidad de conformado.
2.3 Ángulo de nutación
El ángulo de nutación es el ángulo que forma el eje del utillaje superior con la vertical. El aumento de este ángulo origina el aumento del carácter incremental del proceso. Es decir, al aumentar el ángulo, la sección del utillaje superior en contacto con el taco, responsable del conformado, se reduce lo que conlleva a la reducción de las fuerzas necesarias para el conformado.
En la siguiente figura se representa dicho utillaje inclinado con dos ángulos de nutación diferentes, 5º y 2º. Todos los casos expuestos hasta este apartado han sido realizados con un ángulo de nutación de 5º.
![Figura 16. [Utillaje superior con diferentes ángulos de nutación] Figura 16. [Utillaje superior con diferentes ángulos de nutación]](https://img.interempresas.net/fotos/908157.jpeg)
Las fuerzas requeridas para ambos procesos se exponen a continuación. Es apreciable la reducción del tonelaje necesario para deformar la misma geometría aumentando el ángulo de nutación de 2º a 5º.
![Figura 17. [Comparativa de fuerzas para ángulos de nutación de foja rotativa] Figura 17. [Comparativa de fuerzas para ángulos de nutación de foja rotativa]](https://img.interempresas.net/fotos/908158.jpeg)
A continuación se muestran las figuras correspondientes a la comparativa temperatura – microestructura para los diferentes ángulos de nutación. Los parámetros iniciales para todos los casos han sido temperatura inicial del taco 970 °C, tamaño de grano inicial 9ASTM, temperatura de utillajes igual a 500 °C y velocidades de 300 rpm y 5 mm/s.

Las diferencias más acusadas se ven en la temperatura alcanzada en la zona central, siendo el caso del ángulo de 5º superiores al de 2º. Por el contrario, el efecto en la microestructura es prácticamente nulo.
En la siguiente gráfica se muestran los valores máximo y mínimo del tamaño de grano para cada uno de los dos casos anteriores.
![Figura 19. [Tamaño de grano máximo y mínimo. Influencia del ángulo de nutación] Figura 19. [Tamaño de grano máximo y mínimo. Influencia del ángulo de nutación]](https://img.interempresas.net/fotos/908160.jpeg)
Conclusiones
En el presente artículo se expone el estudio de los parámetros obtenidos de una pieza del sector aeronáutico con objeto de fabricarla mediante el proceso incremental de conformado denominado forja rotativa aplicado a uno de los materiales más utilizados en dicho sector, el Inconel 718.
El primer paso fue definir la preforma y los parámetros de proceso necesarios para la fabricación del componente a estudio dentro de las especificaciones de máquinas disponibles en el mercado.
Con objeto de poder realizar una validación experimental, se escaló la geometría a 1/3 de las dimensiones reales para poder adaptar el proceso a la máquina experimental de forja rotativa disponible en Tecnalia.
Como conclusión del análisis de las variables de proceso es posible afirmar:
- Para la obtención de microestructuras de tamaño de grano fino y homogéneo, se distinguen dos estrategias de conformado en función del tamaño de grano inicial del taco:
- Para tamaños de grano iniciales finos (~ 9ASTM): el objetivo del proceso de conformado es no incrementar la temperatura por encima de la temperatura de disolución de la fase δ del Inconel 718 para evitar el crecimiento del tamaño de grano, manteniendo de este modo la microestructura fina y homogénea inicial.
- Para tamaños de grano iniciales groseros (~ 4ASTM): el objetivo del proceso de conformado es recristalizar el grano. Esto se ve favorecido al incrementar la temperatura inicial del taco.
- La microestructura final de una pieza es independiente del ángulo de nutación utilizado para la forja rotativa.
- Las claves para la obtención de una microestructura homogénea y fina son, por tanto:
- Partir de tamaño de grano fino.
- Partir de una temperatura inicial de taco lo suficientemente pequeña (~ 970 °C) para no superar la temperatura de disolución de la fase δ durante el proceso de conformado.
- Velocidades de conformado rápidas, a partir de 1mm/s, implicando mayores velocidades de deformación.
Trabajo futuro
El trabajo inmediato a desarrollar a lo largo del presente año es la ejecución de los ensayos responsables de la validación experimental del trabajo numérico presentado en este artículo y para lo cual ya se ha diseñado la hoja de ruta de fabricación.
Agradecimientos
Este trabajo está financiado por el programa Etortek del Gobierno Vasco, en concreto por el proyecto de referencia ProFUTURE (IE10-271). Para la ejecución de este trabajo han sido imprescindibles la colaboración de las empresas Industrias Puigjaner, S.A. (DENN) e Industria de Turbo Propulsores, S.A. (ITP). Tecnalia en colaboración con DENN desarrolló una máquina de forja rotativa que será utilizada para realizar la validación experimental del presente trabajo en un futuro próximo. Este trabajo no hubiera sido posible sin los datos geométricos proporcionados por ITP.
Referencias
[1] G. Liu, S.J. Yuan, Z.R. Wang, D.C. Zhou. “Explanation of the mushroom effect in the rotary forging of a cylinder”: submitted to Journal of Materials Processing Technology (2004)
[2] X. Mateu, J.F. Puigjaner, M. Albea, J. San José, M. T. Santos, S. Varela. “Process design and simulation of aluminium wheel disk manufactured by rotary forge and flowforming”: submitted to 3rd ASIAFORGE Meeting (2010)
[3] J. San José, M. T. Santos, S. Varela, M. Albea, X. Medan, J. F. Puigjaner. “Material reduction costs by new rotary processes: rotary forging and flowforming”: submitted to 30rd SENAFOR Congress 2010 (2010)
[4] A, Mangas, M. Santos, J. San Jose, G. Atxaga, O. Adarraga, Microstructural behaviour in Rotary Forging of Inconel 718, submitted to ESAFORM 2012 Congress (2012).
[5] A, Mangas, M. Santos, J.I. Zarazua, J. San Jose, G. Atxaga, O. Adarraga, Sensitivity Analysis to optimise the microstructural properties of an Inconel 718 component manufactured by Rotary Forging, submitted to ESAFORM 2013 Congress (2013).
[6] T. ALtan, G. Ngaile, G. Shen. Cod and Hot Forging, Fundamentals and Applications. First edition, ASTM International, 2005
[7] J.R. Cho, H.S. Jeong, D. J. Cha, W. B. Bae, J. W. Lee. “Prediction of microstructural evolution and recrystallization behaviours of a hot working die steel by FEM”: submitted to Journal of materials processing technology (2004)
[8] C.A. Dandre, C.A. Walsh, R.W. Evans, R.C. Reed and S.M. Roberts. “Microstructural evolution of nickel-base superalloy forgings during ingot-to-billet conversion: process modelling and validation”. Superalloys 2000, Edited by T.M. Pollock, R.D. Kissinger, R.R. Bowman, K.A. Green, M. McLean, S. Olson, and J.J. Schirra. TMS me Minerals, Metals & Materials Society), 2000
[9] C. Ruiz, A. Obabueki, K. Gillespie, Evaluation of the microstructure and mechanical properties of delta processed alloy 718. The Minerals, Metals & Materials Society (1992) 33-42.
[10] C.A. Dandre, C.A. Walsh, R.W. Evans, R.C. Reed and S.M. Roberts. “Microstructural evolution of nickel-base superalloy forgings during ingot-to-billet conversion: process modelling and validation”. Minerals, Metals & Materials Society (2000) 85-94.
[11] M. C. Mataya, Simulating microstructural evolution during the hot working of Alloy 718, JOM (1999) 18-26.